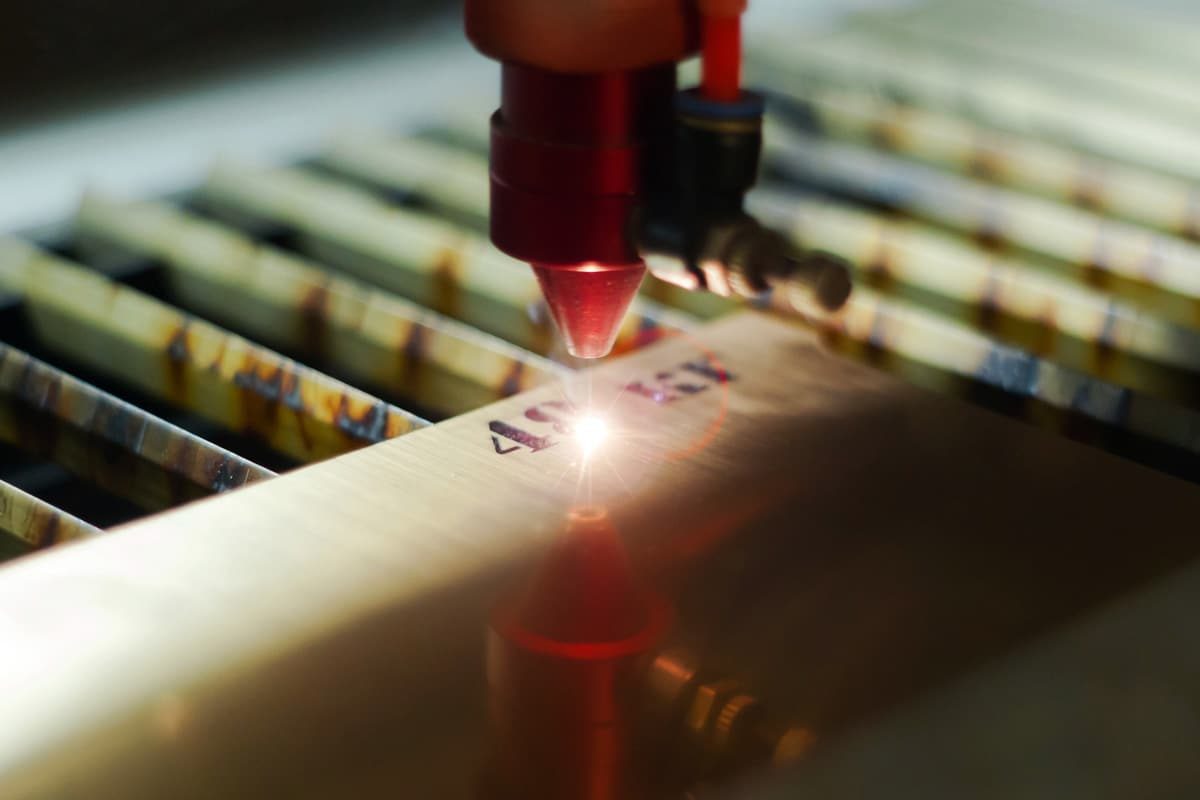
Lazer Markalamada Yüksek Kontrast Nasıl Elde Edilir
Verimli ve doğru bir markalama yöntemi olarak lazer markalama, özellikle elektronik üretim, tıbbi cihazlar, otomotiv parçaları, havacılık, mücevher, paketleme ve diğer alanlar olmak üzere birçok sektörde yaygın olarak kullanılmaktadır. Ürün seri numaralarından, QR kodlarından, marka logolarından karmaşık grafiklere kadar, lazer markalama teknolojisi çeşitli malzemeler üzerinde kalıcı markalama sağlayabilir. Bu teknoloji, temassız, yüksek hız, düşük maliyet ve yüksek hassasiyet ile modern üretim endüstrisinin vazgeçilmez bir parçası haline gelmiştir. Kontrast, lazer markalamanın kalitesini etkileyen önemli bir faktördür. Yüksek kontrast, yalnızca markanın okunabilirliğini iyileştirmekle kalmaz, aynı zamanda ürünün ve markanın görsel etkisini doğrudan etkiler. Otomatik barkod okuma, marka logolarının netliği veya karmaşık endüstriyel markalamalar olsun, markanın kalitesini sağlamak için iyi kontrast şarttır. Peki, lazer markalamada yüksek kontrast nasıl elde edilir? Bu makale, çeşitli uygulama senaryolarında mükemmel lazer markalama efektleri elde etmenize yardımcı olmak için ilgili teknolojileri ve en iyi uygulamaları ayrıntılı olarak inceleyecektir.
İçindekiler
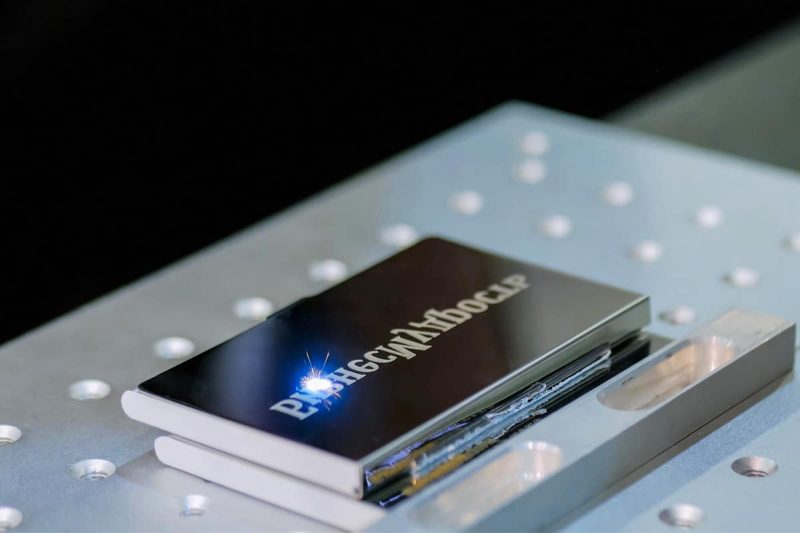
Lazer Markalama Teknolojisi Hakkında Bilgi Edinin
Lazer markalama teknolojisi, temas gerektirmeyen, yüksek hassasiyetli ve çeşitli markalama yöntemleri nedeniyle endüstride yaygın olarak kullanılmaktadır. Markalama malzemesine ve markalama gereksinimlerine bağlı olarak, lazer markalama, gravür, tavlama, köpürtme, ablasyon ve karbon göçü gibi çeşitli yollarla gerçekleştirilebilir. Her teknolojinin farklı çalışma prensipleri ve markalama etkileri vardır ve farklı uygulama senaryolarına uygundur. Aşağıda, avantajlarını ve uygulama alanlarını anlamanıza yardımcı olmak için her markalama teknolojisini derinlemesine inceleyeceğiz.
Oymak
Gravür, bir işaret oluşturmak için bir malzemenin yüzey katmanını çıkarmak için yüksek enerjili lazerler kullanan bir tekniktir. Lazerin yüksek sıcaklığı, malzemenin buharlaşmasına veya erimesine neden olarak kalıcı bir girintili işaret bırakır. Bu teknik genellikle malzemeleri derin veya kalıcı olarak işaretlemek için kullanılır ve uzun süreli dayanıklılık ve aşınmaya karşı direnç gerektiren uygulamalar için uygundur.
- Uygulanabilir malzemeler: metal, plastik, seramik, ahşap, vb.
- Avantajları: Kazıma derinliği kontrol edilebilir, markalama aşınmaya karşı çok dayanıklıdır ve otomotiv parçaları ve takımlar gibi zorlu ortamlarda çalışan parçalar için uygundur.
- Uygulama endüstrileri: otomotiv üretimi, elektronik ekipman, metal işleme, mücevher, alet tanımlama vb.
Gravür teknolojisi özellikle paslanmaz çelik ve alüminyum alaşımları gibi sert malzemeleri işaretlemek için uygundur. Dayanıklı ve net işaretler oluşturabilir, işaretlerin zorlu koşullar altında bile okunabilir olmasını sağlar.
tavlama
Tavlama teknolojisi esas olarak metal malzemeler için kullanılır. Lazer, malzemenin yüzeyini ısıtır ve yüzeyde farklı renklerde izler oluşturmak için bir oksidasyon reaksiyonuna neden olur. Malzemenin yüzey tabakası herhangi bir malzemeyi çıkarmadan yalnızca renk değiştirdiğinden, tavlama izinin pürüzsüz yüzeyi, malzeme yüzeyinde yüksek gereksinimleri olan uygulamalar için uygundur.
- Uygulanabilir malzemeler: paslanmaz çelik, titanyum alaşımı, krom ve diğer metal malzemeler.
- Avantajları: Malzemenin yüzeyinde mekanik hasar oluşmaz, pürüzsüz yüzey, tıbbi ekipman ve yüksek talep gören parçalar için uygundur.
- Uygulama endüstrileri: tıbbi ekipman, cerrahi aletler, havacılık parçaları, vb.
Tavlama markalama teknolojisinin en önemli avantajı, malzeme yüzeyinin bütünlüğünü korurken yüksek kontrastlı markalamalar sağlama yeteneğidir ve bu da onu malzeme performansı konusunda yüksek gereksinimleri olan endüstriler için ilk tercih haline getirir.
köpürme
Köpükleme teknolojisi genellikle plastik işaretleme için kullanılır. Lazer, malzemenin yüzeyini ısıtır ve bunun sonucunda yerel olarak buharlaşır ve küçük kabarcıklar oluşur. Bu kabarcıklar malzemenin yansıtıcı özelliklerini değiştirerek fark edilir bir renk farkı yaratır. Köpükleme genellikle malzemenin yüzeyini hafifçe yükseltir ve işarete üç boyutlu bir etki katar.
- Uygulanabilir malzemeler: Plastik ve kauçuk gibi metal olmayan malzemeler.
- Avantajları: Köpürme izi nettir ve yüksek kontrasta sahiptir, özellikle koyu plastik malzemeler için uygundur.
- Uygulama endüstrileri: elektronik bileşenler, plastik ürünler, tüketici ürünleri ambalajları, vb.
Köpük işaretleme, plastiğin genel yapısını değiştirmeden belirgin bir işaretleme elde edebilir. Genellikle elektronik ürünler, paketleme malzemeleri ve tüketim malları alanlarında kullanılır.
Ablasyon
Ablasyon teknolojisi, malzemelerin yüzeyinden kaplamaları veya filmleri hassas bir şekilde çıkarmak için yüksek enerjili lazerler kullanır. Gravürün aksine, ablasyon yalnızca yüzey katmanını kaldırır ve alttaki malzemeyi etkilemez. Bu teknoloji genellikle kaplanmış malzemelerin yüksek hassasiyetli işaretlenmesi için kullanılır, yüzey kaplamasını kaldırarak alttaki malzemeyi açığa çıkarır ve böylece bir kontrast oluşturur.
- Uygulanabilir malzemeler: kaplamalı metaller, plastikler, cam, vb.
- Avantajları: Yüksek hassasiyetli markalama, yüksek görünüm gereksinimleri olan uygulamalar ve ince markalama için uygundur.
- Uygulama endüstrileri: elektronik bileşenler, ev aletleri gövdeleri, enstrümanlar, vb.
Ablasyon markalama, özellikle elektronik ürün muhafazaları, otomotiv bileşenleri ve hassas aletlerin işaretlenmesi gibi alttaki malzemenin ortaya çıkarılması gereken uygulamalarda, çok katmanlı malzemeler için uygundur.
Karbon göçü
Karbon göçü, lazerler aracılığıyla bir malzemenin karbon içeriğini değiştirir ve malzemenin yüzeyinin renginin değişmesine ve kalıcı bir iz oluşmasına neden olur. Karbon göçü, özellikle karbon içeren metal malzemelerde kullanılır. Malzemedeki karbon elementini yeniden dağıtmak veya süblimleştirmek için lazer enerjisini hassas bir şekilde kontrol eder ve bir renk değişimi oluşturur.
- Uygulanabilir malzemeler: karbon çeliği, paslanmaz çelik, titanyum ve diğer karbon içeren metal malzemeler.
- Avantajları: Yüzey kalitesine zarar vermeden son derece yüksek kontrast elde edilebilir ve özellikle görünüm açısından yüksek beklentileri olan ürünler için uygundur.
- Uygulama endüstrileri: tıbbi cihazlar, mücevher, tüketici ürünleri, vb.
Karbon göçü işaretleme teknolojisi, malzemenin yüzeyine zarar vermediği için cerrahi aletler ve lüks eşyalar gibi paslanmaz çelik ve titanyum alaşımlarının işaretlenmesinde yaygın olarak kullanılmaktadır.
Farklı lazer markalama teknolojileri, çeşitli uygulamalar için geniş bir yelpazede seçenekler sunar. Gravür teknolojisi derin ve dayanıklı markalamalar sağlar, tavlama teknolojisi renk değişimleri elde ederken pürüzsüz bir metal yüzey sağlar; köpürtme plastik malzemeler için uygundur, ablasyon kaplamalı malzemelerin işlenmesinde iyidir ve karbon göçü yüksek kontrastlı metal markalama için eşsiz sonuçlar sağlayabilir. Malzeme türüne ve markalama gereksinimlerine bağlı olarak, uygun markalama yöntemini seçmek ürün markalamalarının kalitesini ve okunabilirliğini büyük ölçüde artırabilir. Endüstriyel üretimde, bu teknolojileri anlamak ve belirli uygulama senaryolarına göre seçim yapmak çok önemlidir.

Lazer Markalamada Kontrastı Anlamak
Lazer markalama sürecinde, kontrast, markanın kalitesini belirleyen önemli faktörlerden biridir. Yüksek kontrastlı markalar, özellikle kontrast kalitesinin üretim verimliliğini ve ürün performansını doğrudan etkilediği endüstriyel uygulamalarda, bilgilerin tanımlanmasını ve okunmasını kolaylaştırır. Aşağıda, lazer markalamada kontrastın tanımı ve çeşitli endüstrilerdeki önemi ayrıntılı olarak açıklanacaktır.
Kontrastın Tanımı
Lazer işaretlemede kontrast, işaretli kısım ile çevresindeki işaretsiz alan arasındaki ışık ve karanlık farkına atıfta bulunur. Özellikle, işaretli alanın rengi, parlaklığı veya yansıtıcılığı, işaretsiz alanla keskin bir kontrast oluşturarak net bir görsel etki yaratır. Kontrast ne kadar yüksekse, işaret o kadar net olur ve bu, işaretli bilgileri okumak veya taramak için çok önemlidir.
Kontrastın oluşumu temel olarak aşağıdaki hususlara bağlıdır:
- Malzeme yüzeyinin özellikleri: Farklı malzemelerin emiciliği ve yansıtıcılığı, lazerin malzemeyle etkileşimini etkiler ve böylece işaretin rengini ve netliğini etkiler. Örneğin, siyah plastik üzerine lazer markalama, beyaz plastik üzerine yapılandan önemli ölçüde farklı olacaktır.
- Lazer parametreleri: Güç, darbe frekansı, tarama hızı ve diğer parametreler lazer markalama derinliğini, renk değişimini ve malzeme üzerindeki parlaklığı etkileyecek ve dolayısıyla markanın kontrastını doğrudan etkileyecektir.
- Çevresel koşullar: Sıcaklık, nem ve diğer faktörler de malzemenin fiziksel özelliklerini ve lazer markalamanın etkisini etkileyebilir.
İster barkod, ister QR kodu, ister metin veya desen olsun, net işaretleme yeterli kontrasta bağlıdır. Özellikle endüstriyel üretimde, işaretlemenin net olup olmadığı doğrudan ürünün izlenebilirliği ve okunabilirliği ile ilgilidir.
Yüksek Kontrastın Önemi
Yüksek kontrastlı lazer işaretleme yalnızca görsel olarak daha belirgin olmakla kalmaz, aynı zamanda endüstriyel otomasyon ve manuel tanımlamanın verimliliğini de önemli ölçüde artırır. Bu, özellikle aşağıdaki açılardan kritik öneme sahiptir:
- Gelişmiş okunabilirlik ve tanıma: Yüksek kontrastlı işaretlemeler, bilgileri farklı ışıklarda, açılarda ve mesafelerde görünür hale getirir. Özellikle karmaşık endüstriyel ortamlarda, güçlü ışık, yansımalar veya toz gibi faktörler düşük kontrastlı işaretlemelerin görünürlüğünü etkileyebilirken, yüksek kontrast zorlu koşullarda bile kolay tanıma sağlar.
- Otomatik ekipmanın okuma verimliliği: Otomobil üretimi, elektronik ürünler, lojistik ve tıbbi ekipman gibi birçok sektörde barkodlar ve QR kodları gibi bilgi işaretleri genellikle otomatik kod okuma ekipmanı tarafından tanınır. İşaretin kontrastı yetersizse, kod okuma cihazının tanıma hataları yapma veya birden fazla tarama gerektirme olasılığı daha yüksek olur ve bu da üretim verimliliğini azaltır. Yüksek kontrastlı işaretlemeler tanıma hatalarını ve okuma hatalarını azaltarak otomatik ekipmanın verimliliğini önemli ölçüde iyileştirebilir.
- Ürün izlenebilirliğini ve uyumluluğunu sağlayın: Elektronik, otomobil ve tıbbi ekipman gibi yüksek standartlı endüstrilerde ürün izlenebilirliği, güvenlik ve kaliteyi sağlamanın önemli bir parçasıdır. Lazer işaretleme, bu endüstrilerde parçaları işaretlemek için yaygın olarak kullanılır. Yüksek kontrastlı işaretlemeler, yalnızca üretim, nakliye ve kullanım sırasında ürünleri izlemeye yardımcı olmakla kalmaz, aynı zamanda endüstri düzenlemelerinin gereksinimlerinin karşılanmasını da sağlar.
- Marka ve görsel efektleri geliştirin: Mücevher, lüks ürünler, cep telefonu kılıfları vb. gibi bazı tüketim malları alanlarında, lazer işaretleme genellikle marka tanımlaması için kullanılır. Yüksek kontrastlı işaretlemeler yalnızca ürünün estetiğini artırmakla kalmaz, aynı zamanda marka tanınırlığını da artırır. Net ve dayanıklı işaretlemeler yalnızca marka imajını vurgulamakla kalmaz, aynı zamanda tüketicilere iyi bir görsel deneyim sağlar.
Sektördeki Uygulama Örnekleri
- Otomotiv endüstrisi: Üretim hattında izlenebilirliği ve otomatik kod okumanın doğruluğunu sağlamak amacıyla seri numaraları, üretim tarihleri ve parçaların parti numaraları için yüksek kontrastlı işaretleme kullanılır.
- Elektronik endüstrisi: Çipler ve baskılı devre kartları gibi bileşenlerin lazerle işaretlenmesi, yüksek hızlı üretim hatlarındaki ekipmanların doğru okunmasını sağlamak için genellikle incelik ve yüksek kontrast gerektirir.
- Tıbbi cihaz sektörü: Cerrahi aletler ve tıbbi cihazlar için yüksek kontrastlı lazer markalama, ürünlerin benzersizliğini ve izlenebilirliğini garanti altına alarak ürünlerin sıkı hijyen ve kalite gereksinimlerini karşılamasını sağlar.
- Havacılık ve Uzay: Özel malzemeler ve zorlu ortamlar nedeniyle, yüksek kontrastlı işaretleme, üretim, montaj ve bakım sırasında parçaların net bir şekilde okunabilirliğini sağlayabilir.
Yüksek kontrast yalnızca lazer markalama kalitesinin bir sembolü değil, aynı zamanda endüstriyel üretim verimliliğini ve ürün izlenebilirliğini sağlamada önemli bir faktördür. Markalama netliği konusunda katı gereksinimleri olan endüstrilerde, yüksek kontrastlı markalama elde etmek, otomatik kod okuma ekipmanının performansını iyileştirmede, hataları azaltmada ve ürün uyumluluğunu sağlamada yeri doldurulamaz bir rol oynar. Bu nedenle, uygun lazer parametrelerini ve malzemelerini seçmek ve markalama sürecini optimize etmek, yüksek kontrast elde etmek için önemli adımlardır.
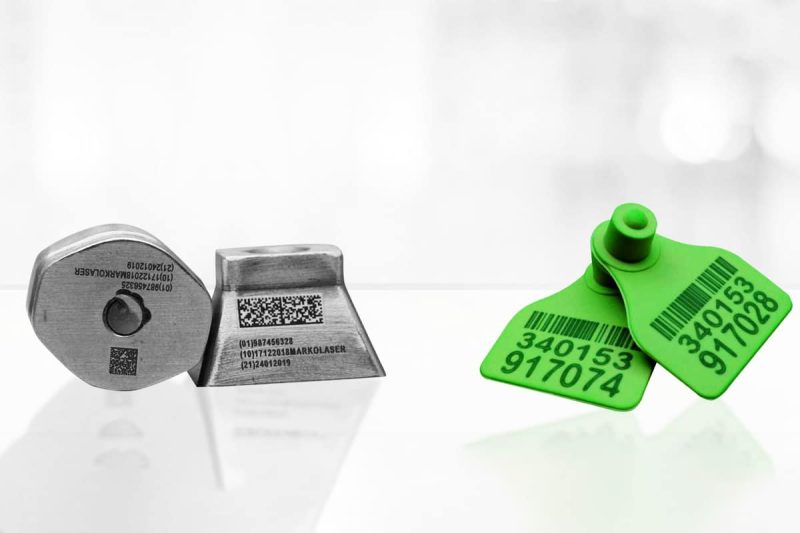
Lazer İşaretleme Kontrastını Etkileyen Faktörler
Lazer markalamanın kontrastı, malzemenin özellikleri, lazer parametreleri, çevre koşulları ve yüzey hazırlığı gibi birden fazla faktörden etkilenir. Bu faktörleri anlamak ve buna göre optimizasyon ayarlamaları yapmak, markalarınızın netliğini ve kalitesini önemli ölçüde iyileştirebilir. Aşağıda, bu faktörleri çeşitli yönlerden kontrol ederek yüksek kontrastlı lazer markalamanın nasıl elde edileceğini ayrıntılı olarak tartışacağız.
Malzeme özellikleri
Lazer markalamanın etkisinde, özellikle yüksek kontrastlı markalamalarda malzemenin fiziksel ve kimyasal özelliklerinin doğrudan etkisi vardır; malzemenin emilim oranı, yansıtma özelliği, yüzey rengi ve yüzey durumu gibi faktörler önemli faktörlerdir.
- Emilim oranı: Bir malzeme tarafından lazer enerjisinin emilim oranı, işaretleme etkisini belirleyen ana faktörlerden biridir. Yüksek emilim oranına sahip malzemeler, lazer enerjisini daha verimli bir şekilde ısı enerjisine dönüştürebilir ve bu da malzeme yüzeyinde daha belirgin değişikliklere neden olur. Örneğin, plastikler, ahşap ve kaplamalı metaller gibi malzemeler genellikle yüksek lazer emilim oranlarına sahiptir ve bu nedenle daha keskin işaretler üretir. Cam ve bazı metaller daha düşük emilim oranlarına sahiptir ve istenen etkiyi elde etmek için daha yüksek güç veya özel lazer dalga boyları gerektirebilir.
- Yansıtma: Alüminyum, gümüş ve bakır gibi yüksek yansıtma özelliğine sahip malzemeler, lazer enerjisinin çoğunu yansıtma eğilimindedir ve bu da işaretleme etkisinin önemsiz olmasına neden olur. Bu tür malzemeleri işaretlerken, yeterli enerji emilimini sağlamak ve işaretleme kontrastını iyileştirmek için genellikle belirli bir dalga boyuna sahip bir lazer (fiber lazer veya yeşil lazer gibi) kullanmak gerekir. Uygun yüzey işlemi veya ön kaplama, yansıtma özelliğini azaltmaya ve işaretlemeyi iyileştirmeye de yardımcı olabilir.
- Yüzey rengi ve bileşimi: Malzemenin rengi de lazer işaretlemenin kontrastı üzerinde önemli bir etkiye sahiptir. Koyu renkli malzemeler (siyah plastikler ve siyah metal kaplamalar gibi) önemli kontrast üretme olasılığı daha yüksektir çünkü koyu renkli malzemeler genellikle lazer enerjisini daha verimli bir şekilde emer. Tersine, beyaz plastik veya gümüş metal gibi açık renkli malzemeler, ideal kontrastı elde etmek için daha yüksek lazer gücü veya daha ince parametre ayarlamaları gerektirebilir.
- Yüzey durumu: Malzeme yüzeyinin pürüzsüzlüğü veya pürüzlülüğü, lazer ile malzeme arasındaki etkileşimi doğrudan etkiler. Pürüzsüz yüzeyler genellikle lazer ışığını daha eşit şekilde yansıtır ve bu da daha yüksek kontrastla sonuçlanırken, çok pürüzlü yüzeyler lazer enerjisinin dağılmasına neden olarak işaretleme etkisini azaltabilir. Ancak, orta derecede pürüzlü bir yüzey lazer enerjisinin emilmesini kolaylaştırabilir ve böylece işaretleme etkinliğini artırabilir. Bu, malzemeye ve uygulama gereksinimlerine bağlı olarak doğru yüzey pürüzlülüğünü seçmenin kontrastı iyileştirmede olumlu bir etkiye sahip olabileceği anlamına gelir.
Lazer Parametreleri
Lazer markalama sırasında, lazer ekipmanının parametre ayarları markanın kalitesi, doğruluğu ve kontrastı üzerinde önemli bir rol oynar. Lazer gücü, hızı, darbe frekansı ve odak optimize edilerek, markalama etkisi iyileştirilebilir ve işaretlenen kontrast artırılabilir.
- Güç: Lazerin gücü, malzemenin yüzeyine ilettiği enerji miktarını belirler. Çok düşük bir güç, belirsiz işaretlemeye ve yetersiz kontrasta neden olabilirken, çok yüksek bir güç, malzemenin aşırı yanmasına veya erimesine veya hatta malzemenin yüzeyine zarar vermesine neden olabilir. Yüksek kontrastlı işaretleme elde etmek için, lazer enerjisinin malzeme özelliklerine uymasını ve malzemeye zarar vermeden net işaretleme elde edilmesini sağlamak için güç seçiminin hassas bir şekilde ayarlanması gerekir.
- Hız: Lazer kafasının hareket ettiği hız, lazerin malzeme yüzeyinde etki ettiği süreyi etkiler. Daha düşük hızlar, lazerin malzeme yüzeyinde daha uzun süre kalmasını sağlayarak ısı enerjisi birikimini artırır ve böylece işaretlemenin derinliğini ve kontrastını iyileştirir. Ancak, çok düşük bir hız aynı zamanda malzemenin aşırı ısınmasına ve işaretin netliğini etkilemesine neden olabilir. Bu nedenle, en iyi işaretleme etkisini elde etmek için hız ayarı güçle birlikte düşünülmelidir.
- Darbe frekansı: Lazer darbe frekansı, lazer tekrarlama oranını, yani birim zaman başına düşen lazer darbesi sayısını belirler. Yüksek frekanslı lazer darbeleri, kısa sürede daha fazla alanı kaplayabildikleri için hassas ve karmaşık desen işaretlemeleri için daha uygundur; düşük frekanslı lazer darbeleri ise derin işaretlemeler için uygundur. Yüksek kontrastlı işaretleme elde etmek için uygun darbe frekansını seçmek, malzeme yüzeyinde daha düzgün ve net işaretler üretmeye yardımcı olabilir.
- Odaklanma: Doğru lazer odaklama, lazer enerjisinin malzeme yüzeyindeki belirli bir alana yoğunlaşmasını sağlayarak en verimli enerji transferini sağlar. Yanlış odaklama, lazer enerjisinin dağılmasına neden olarak işaretin netliğini ve kontrastını etkileyebilir. Lazer odağını ayarlayarak, işaretlenen alanın maksimum lazer enerjisi elde etmesini ve kontrastı iyileştirmesini sağlayabilirsiniz.
Çevre koşulları
Lazer markalama sırasında çevresel koşullar da markalama etkisini etkiler. Sıcaklık, nem ve çalışma ortamının temizliği, malzemenin fiziksel özelliklerini ve lazer enerjisi iletiminin verimliliğini değiştirecek ve böylece kontrastı etkileyecektir.
- Sıcaklık: Ortam sıcaklığının malzemelerin fiziksel özellikleri ve lazer enerjisinin iletimi üzerinde belirli bir etkisi vardır. Yüksek sıcaklık ortamları, özellikle plastikler gibi ısıya duyarlı malzemelerde malzemelerin emilim oranını azaltabilir. Yüksek sıcaklıklar, malzemelerin önceden yumuşamasına veya deforme olmasına neden olarak işaretleme etkisini etkileyebilir. Bu nedenle, lazer işaretleme yüksek sıcaklık ortamında yapıldığında, lazer gücünü azaltmak veya diğer parametreleri optimize etmek gerekebilir.
- Nem: Nem, özellikle plastikler ve ahşap olmak üzere belirli malzemelerin lazer markalama etkisi üzerinde önemli bir etkiye sahiptir. Yüksek nemli bir ortam, su buharının malzeme yüzeyinde yoğunlaşmasına neden olarak lazer enerjisinin iletimini etkileyebilir ve markanın netliğini azaltabilir. Marka kontrastını sağlamak için, yüksek nemli ortamlarda, malzemenin yüzeyinin kuru olduğundan emin olmak en iyisidir.
- Temizlik: Malzemenin yüzeyindeki toz, gres, oksitler ve diğer kirleticiler lazer enerjisinin iletimini engelleyecek, enerjinin dağılmasına ve dolayısıyla işaretleme etkisinin etkilenmesine neden olacaktır. Özellikle yüksek hassasiyet gereksinimleri olan lazer işaretleme için malzeme yüzeyinin temiz olduğundan emin olmak çok önemlidir. Lazer işaretlemeden önce malzeme yüzeyini temizlemek, işaretin kontrastını önemli ölçüde iyileştirebilir.
Yüzey Hazırlığı
Lazer markalamadan önce, malzemenin yüzey hazırlığı doğrudan nihai markalama kalitesini ve kontrastını etkileyecektir. Makul yüzey temizliği, pürüzlülük ayarlaması ve gerekli ön işlem, lazer enerjisinin malzeme yüzeyine etkili bir şekilde aktarılmasını ve net markalamalar üretmesini sağlamaya yardımcı olur.
- Temizlik: Malzeme yüzeyi, lazer işaretleme etkisini etkileyebilecek toz, gres, oksit tabakaları veya diğer kirleticileri gidermek için işaretlemeden önce iyice temizlenmelidir. Çözücüler, fırçalar veya ultrasonik temizleme ekipmanı kullanmak, yüzeyin herhangi bir kalıntıdan arındırılmasını sağlayarak lazer işaretlemenin kontrastını iyileştirebilir.
- Yüzey pürüzlülüğü: Uygun yüzey pürüzlülüğü, özellikle yüksek yansıtıcı malzemelerde, malzemenin lazer enerjisini daha iyi emmesine yardımcı olabilir. Yüzey pürüzlülüğünü artırmak, yansıtıcılığı azaltabilir ve böylece işaretleme etkisini iyileştirebilir. Ancak, yüksek hassasiyetli tıbbi cihazlar veya elektronik bileşenler gibi pürüzsüz yüzeyler gerektiren uygulamalar için, daha iyi işaretleme sonuçları için yüzey pürüzsüzlüğünün sağlanması gerekir.
- Ön işlem: Bazı malzemeler, lazer işaretleme etkisinin en iyi performansını sağlamak için ön işlem gerektirebilir. Örneğin, metal malzemeler cilalanabilir veya kaplanabilir ve plastik malzemeler yüzey kimyasal işlemiyle işlenebilir. Bu adımlar, malzeme yüzeyi tarafından lazer enerjisinin emilimini iyileştirmeye yardımcı olur ve böylece daha yüksek kontrast elde edilir.
Lazer markalamanın kontrastını etkileyen faktörler karmaşık ve çeşitlidir ve bunlar arasında malzemenin özellikleri, lazer ekipmanının parametreleri, çevre koşulları ve yüzey hazırlığı yer alır. Bu faktörleri hedefli bir şekilde ayarlayarak, lazer markalamanın kontrastı etkili bir şekilde iyileştirilebilir ve markalama etkisinin net ve dayanıklı olmasını sağlayabilir. Bu, yalnızca endüstriyel üretimdeki izlenebilirlik ve tanımlama gereksinimlerini karşılamakla kalmaz, aynı zamanda marka tanımlama gibi uygulamalarda daha iyi görsel efektler de elde edebilir.
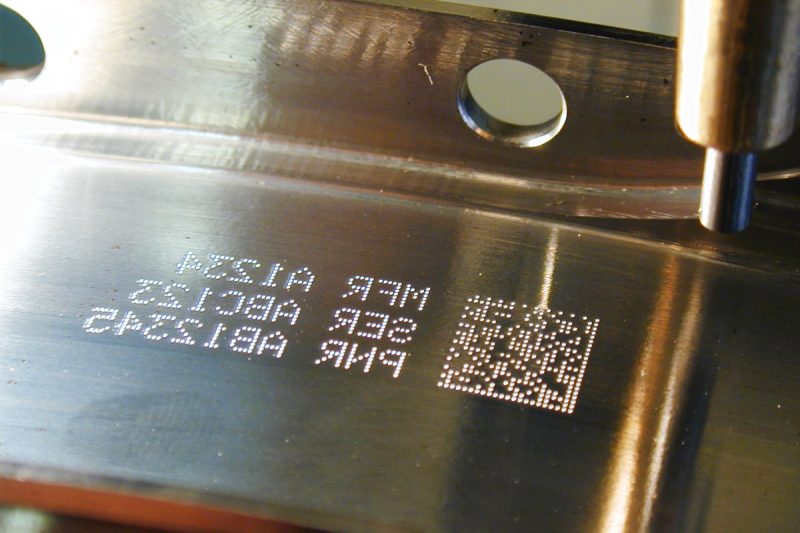
Yüksek Kontrast Elde Etmek İçin Yedi Temel Uygulama
Lazer markalamada yüksek kontrast elde etmek için, lazer tipinin seçiminden çevresel kontrole ve son işlem teknolojisinin uygulanmasına kadar bir dizi en iyi uygulamanın benimsenmesi gerekir. Makul çalışma ve ayarlama yoluyla, farklı malzemeler üzerinde net ve dayanıklı markalama efektleri elde edilebilir.
Doğru Lazer Tipini Seçin
Lazerin dalga boyu farklı malzemeler için farklı emilim oranlarına sahiptir, bu nedenle doğru lazer türünü seçmek çok önemlidir. Fiber lazer jeneratörleri paslanmaz çelik, alüminyum ve bakır gibi metal malzemeler için uygundur ve net işaretler üretebilir. CO2 lazerleri plastikler, organik malzemeler ve ahşap, deri vb. gibi bazı metal olmayan malzemeler için daha uygundur. Malzeme özelliklerine uyan bir lazer jeneratörü seçmek daha yüksek enerji emilimi sağlayabilir ve böylece işaretleme kontrastını iyileştirebilir.
Malzeme hazırlama
Malzeme yüzeyinin hazırlanması, işaretleme sonuçları üzerinde doğrudan bir etkiye sahiptir. Lazer enerjisinin eşit şekilde dağıtılması ve emilmesi için yüzey temiz ve düz olmalıdır. Malzemeye bağlı olarak, işaretlemeye müdahale edebilecek tüm kirleri gidermek için parlatma, kumlama, kimyasal temizleme vb. gibi ön işlemler gerekebilir. Bu tür bir hazırlık, lazerin iletim etkisini optimize etmeye ve işaretin kontrastını ve netliğini iyileştirmeye yardımcı olur.
Lazer Parametre Optimizasyonu
Yüksek kontrast elde etmek için lazer parametrelerinin ayarlanması çok önemlidir. Güç, hız, darbe frekansı vb. gibi parametreler, malzemenin özelliklerine göre ayarlanmalıdır. Genellikle, daha yüksek güç, işaretin derinliğini artırır, ancak çok yüksek güç, malzemenin yanmasına veya aşırı işlenmesine neden olabilir. Daha yavaş bir işaretleme hızı, lazer ile malzeme arasındaki etkileşimi artırmaya yardımcı olur ve böylece kontrastı iyileştirir. Bir dizi deneysel test yoluyla, en iyi işaretleme etkisini sağlamak için farklı malzemeler için en uygun lazer ayarları bulunabilir.
Kontrollü Çevre Koşulları
Ortamın sıcaklığı, nemi ve temizliği lazer markalamanın kararlılığını etkileyecektir. Aşırı sıcaklık veya nem, malzemenin fiziksel özelliklerini değiştirebilir ve bu da lazerin emilim ve iletim verimliliğini etkiler. Özellikle neme duyarlı malzemeler üzerinde lazer markalama yaparken sabit çevre koşullarının korunması tutarlı markalama sonuçları sağlayabilir. Yüksek kontrastlı markalama kalitesini sağlamak için markalama sürecine müdahale eden toz veya kirleticilerden kaçınmak için çalışma alanını düzenli olarak temizleyin.
Tesisat ve Malzeme Taşıma
Markalama işlemi sırasında, malzeme sabit ve hareketsiz kalmalıdır. Herhangi bir ufak hareket, belirsiz markalamalara veya hatalara yol açacaktır. Yüksek hassasiyetli fikstürler ve malzeme fikstürleri kullanmak, markalama pozisyonunun sabitliğini ve tutarlılığını sağlayarak, tekrarlanan işleme veya bulanık markalamalardan kaçınılmasını sağlayabilir. Özellikle geniş alanları veya karmaşık desenleri işaretlerken, sabit bir fikstür genel markalama kalitesini iyileştirebilir.
Yazılım ve Kontrol Sistemleri
Modern lazer markalama sistemleri, lazerin çıkış gücünü, yolunu ve markalama hızını doğru bir şekilde yönetmeye yardımcı olabilen son derece akıllı kontrol yazılımlarıyla donatılmıştır. Bu işlevlerin doğru kullanımı, otomatik parametre ayarlaması sağlayabilir ve operasyonel verimliliği artırabilir. Ayrıca, yazılım, sonraki işlemleri kolaylaştırmak ve her markalamanın ideal kontrastı elde edebilmesini sağlamak için farklı malzemeler için en iyi parametre ayarlarını da kaydedebilir.
Son İşleme Teknolojisi
Bazı durumlarda, lazer markalamadan sonra yapılan son işlem kontrastı daha da iyileştirebilir. Örneğin, metal yüzeyler işaretleme etkisini artırmak için oksitlenebilir veya koruyucu bir tabaka ile püskürtülebilir. Bazen, işaretleme sonrası bir temizleme adımı, işaretleme işleminden kalan kalıntıların temizlenmesine yardımcı olarak işareti daha net ve daha dayanıklı hale getirebilir. Bu son işlem teknikleri, lazer markalamanın genel kalitesini iyileştirmek için farklı malzemelere ve uygulama senaryolarına göre esnek bir şekilde kullanılabilir.
Yüksek kontrastlı lazer işaretleme, doğru lazer tipini seçerek, parametreleri ince ayarlayarak, çevre koşullarını kontrol ederek ve son işlem tekniklerini kullanarak elde edilebilir. Bu en iyi uygulamalar, işaretin netliğini ve dayanıklılığını iyileştirmeye yardımcı olacak ve işaretin çeşitli malzemeler üzerinde iyi performans göstermesini sağlayacaktır.
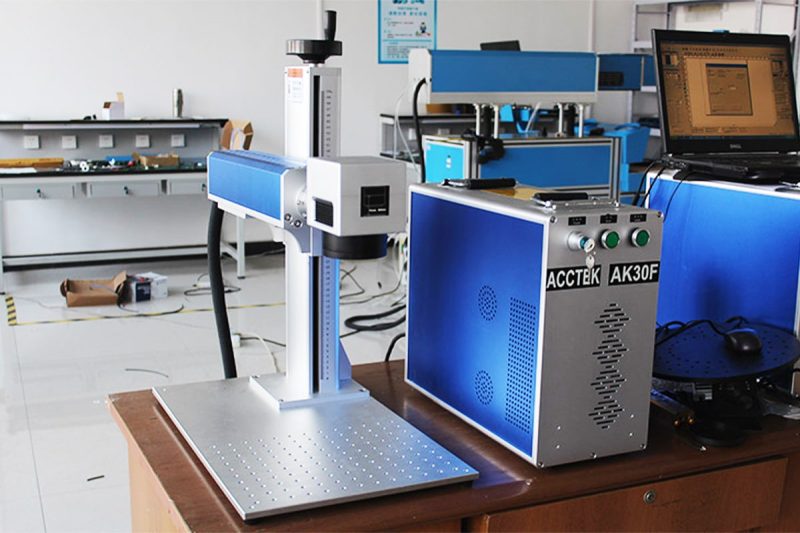
özetle
Yüksek kontrastlı lazer markalama elde etmek için malzemeler, lazer parametreleri ve çevre gibi çeşitli faktörleri göz önünde bulundurmak gerekir. Lazer türünü doğru seçerek, markalama ayarlarını optimize ederek ve malzemenin temizliğini koruyarak şirketler markalama kalitesini büyük ölçüde iyileştirebilir ve daha güzel ve pratik markalama efektleri elde edebilir.
Malzeme hazırlama açısından, farklı malzemeler farklı emilim ve yansıtma özelliğine sahiptir, bu nedenle doğru lazer jeneratörünü seçmek önemlidir. fiber lazer markalama makinesi AccTek tarafından sağlanan, paslanmaz çelik ve alüminyum gibi metal malzemeler için özellikle uygundur, CO2 lazer markalama makinesi ise plastikler ve organik malzemeler için daha uygundur. Cilalama ve temizleme gibi malzeme özelliklerine göre uygun ön işlem, lazer enerjisinin eşit şekilde emilmesini ve markalama kontrastının daha net olmasını sağlayabilir.
Lazer parametrelerini ayarlamak da aynı derecede önemlidir. Lazer ekipmanımız markalama yaparken esnek parametre ayarlamasını destekler ve güç, hız ve frekansa göre en uygun ayarları bulabilir. İster metal üzerinde derin bir markalama ister plastik üzerinde sığ bir markalama olsun, yüksek kontrastlı efektler garanti edilebilir. AccTek'in fiber lazer markalama makinesi, yüksek yansıtıcı malzemeler için bile bunu kolayca halledebilir.
Çevresel koşulları kontrol etmek de göz ardı edilemeyecek bir adımdır. Markalama ortamını kuru ve temiz tutmak, tozun veya nemin markalama etkisini etkilemesini etkili bir şekilde önleyebilir. Ekipmanlarımız çeşitli endüstriyel ortamlarda iyi performans gösterir ve güçlü bir stabiliteye sahiptir, şirketlerin farklı koşullar altında tutarlı markalama sonuçları elde etmesine yardımcı olur. Günlük operasyonlarda, lazer markalama makinelerimiz tasarım olarak basittir ve bakımı kolaydır. Lazer markalama makinelerimizi makul bir şekilde kullanarak, müşteriler hızlı ve doğru markalama elde edebilir ve ürünün genel kalitesini ve marka imajını iyileştirebilir. Bu çabalar sayesinde, ürün yalnızca daha güzel hale getirilmekle kalmaz, aynı zamanda müşteriler lazer markalama çözümlerimizle ilgilenebilir ve böylece sipariş büyümesi teşvik edilebilir.
Lazer markalama makinelerimizle ilgileniyorsanız, işletmenize uygun özelleştirilmiş çözümler hakkında daha fazla bilgi edinmek için lütfen bizimle iletişime geçmekten çekinmeyin.
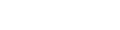
İletişim bilgileri
- [email protected]
- [email protected]
- +86-19963414011
- 3 Bölge A, Lunzhen Sanayi Bölgesi, Yucheng Şehri, Shandong Eyaleti.
Lazer Çözümleri Alın