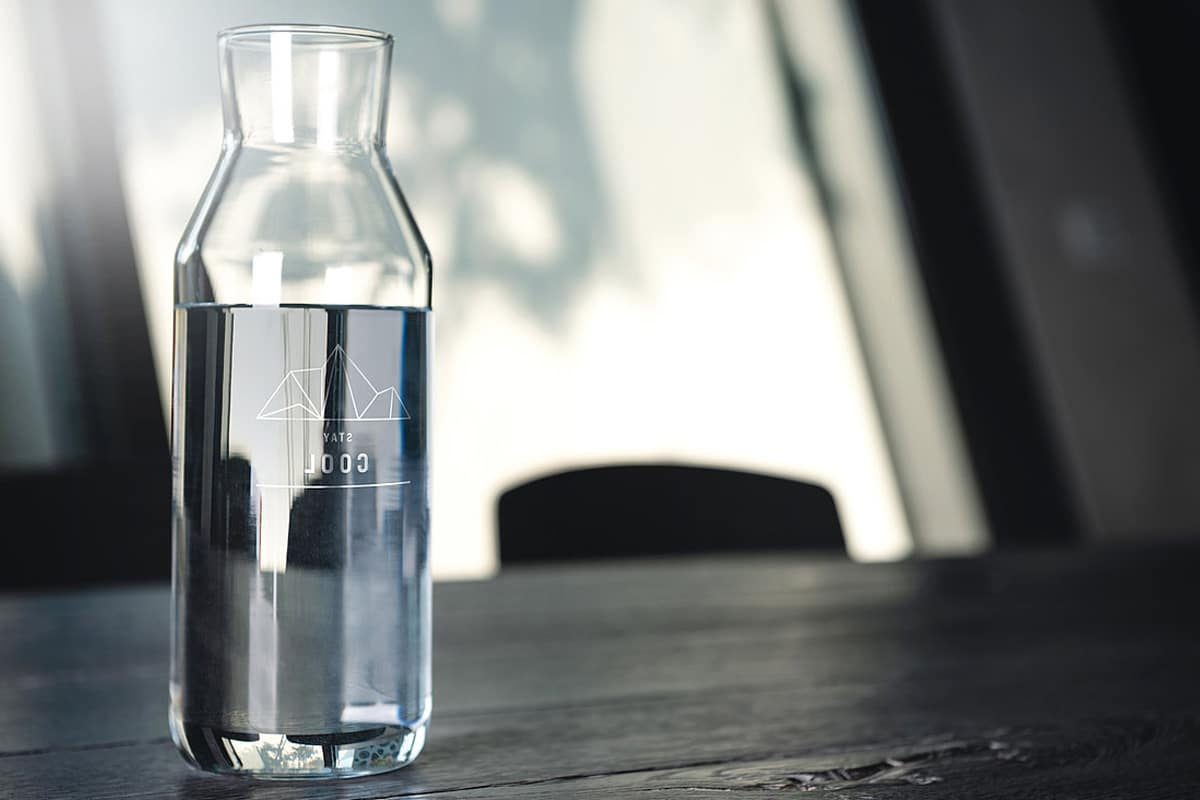
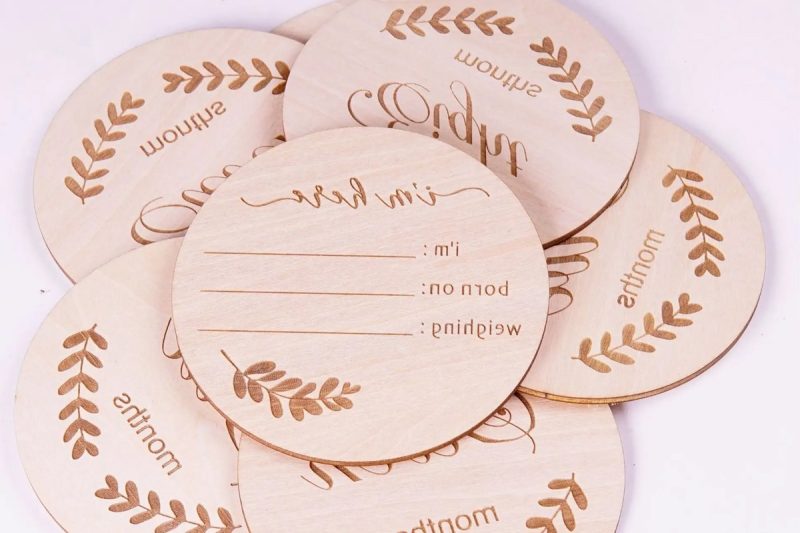
Lazer Türü ve Kaynağı
- Fiber Lazer: Yüksek enerji yoğunluğu ve mükemmel odaklama özellikleriyle fiber lazer jeneratörleri, özellikle çelik, alüminyum ve bakır gibi metal malzemelerin markalanması için oldukça uygundur. Fiber lazer markalama son derece yüksek hassasiyet elde edebilir ve elektronik bileşenler, tıbbi cihazlar ve otomotiv parçaları gibi son derece ince desenler ve metinler gerektiren yüksek hassasiyetli uygulamalarda sıklıkla kullanılır. Ayrıca, fiber lazerler düşük enerji tüketimine ve uzun hizmet ömrüne sahiptir ve bu da onları metal işaretleme için ilk tercih haline getirir.
- CO2 lazer: CO2 lazerler esas olarak metal olmayan malzemeleri işaretlemek için kullanılır, özellikle ahşap, plastik, deri ve kağıt gibi malzemeler için. 10,6 mikron dalga boyuyla metal olmayan malzemelerin enerjisini verimli bir şekilde emebilir, bu nedenle paketleme, giyim ve el sanatları gibi endüstrilerde yaygın olarak kullanılmıştır. Kesme ve kazıma işlevleri CO2 lazer markalama Ayrıca reklam prodüksiyonu, mobilya dekorasyonu ve model imalatında da öne çıkmaktadır.
- Ultraviyole (UV) lazer: UV lazerler, kısa dalga boyları (genellikle 355 nm) nedeniyle soğuk ışık kaynakları olarak adlandırılır. Diğer lazer türleriyle karşılaştırıldığında, UV lazerler çok küçük bir ısıdan etkilenen bölgeye sahiptir, bu da işaretleme işlemi sırasında termal deformasyon ve malzemeye verilen hasarın büyük ölçüde azalacağı anlamına gelir. Bu, özellikle cam, plastik ve seramik gibi ısıya duyarlı malzemeler üzerinde ince işaretleme için çok uygun hale getirir. UV lazer işaretleme genellikle elektronik ürünler, kozmetik ambalajlar ve ilaç etiketleri gibi yüksek hassasiyetli endüstrilerde kullanılır ve son derece ince ve net işaretleme efektleri elde edilebilir.
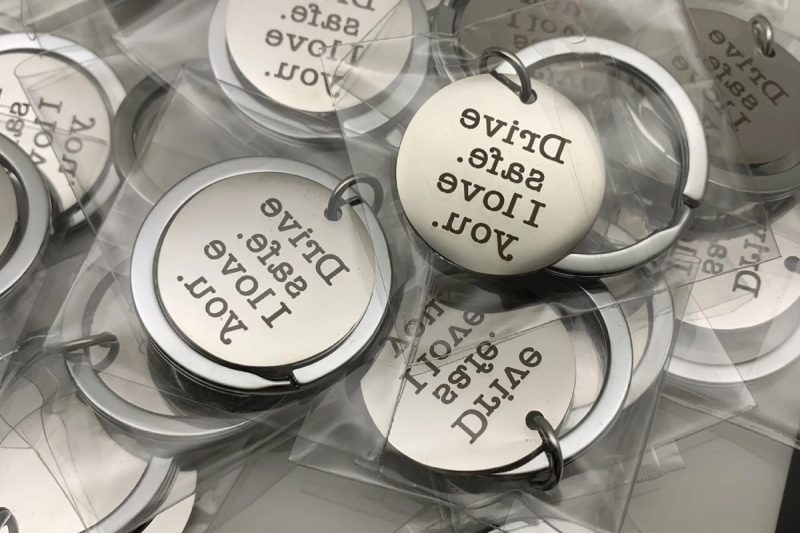
Malzeme Özelliklerinin Etkisi
- Emilim ve yansıtma: Malzemelerin farklı dalga boylarındaki lazerler için farklı emilim ve yansıtma yetenekleri vardır. Yüksek emilimli malzemeler lazer enerjisini daha iyi emebilir ve daha iyi işaretleme efektleri üretebilirken, yüksek yansıtıcılığa sahip malzemeler büyük miktarda lazer ışığını yansıtacak ve işaretleme verimliliğini azaltacaktır. Örneğin, alüminyum ve bakır gibi metal malzemeler fiber lazerler için yüksek yansıtıcılığa sahiptir ve bu da yetersiz veya belirsiz işaretlemeye neden olabilir. Bu nedenle, bu yüksek yansıtıcılığa sahip malzemeleri işaretlerken, genellikle ideal işaretleme efektini elde etmek için lazer parametrelerini ayarlamak veya emilim oranını artırmak için belirli dalga boylarına sahip lazerler kullanmak gerekir. Buna karşılık, plastik veya cam gibi metalik olmayan malzemeler CO2 ve UV lazerler için yüksek emilim oranlarına sahiptir ve işaretleme derinliği ve kontrastı kontrol etmek daha kolaydır.
- Isıl iletkenlik: Malzemenin ısıl iletkenliği, işaretleme işlemi sırasında ısı dağılımını doğrudan etkiler. Bakır, alüminyum ve diğer metaller gibi yüksek ısıl iletkenliğe sahip malzemeler, işaretleme işlemi sırasında oluşan ısıyı hızla dağıtabilir, yerel aşırı ısınmayı azaltabilir ve malzeme yüzeyinin erimesini veya yanmasını önleyebilir. Bu tür malzemeler, işaretleme alanına yeterli enerjinin uygulandığından emin olmak için genellikle lazer işaretleme sırasında artırılmış lazer gücü veya uzatılmış işaretleme süresi gerektirir. Plastik veya ahşap gibi düşük ısıl iletkenliğe sahip malzemeler için ısının hızla yayılması zordur ve işaretleme işlemi sırasında aşırı ısınma meydana gelebilir ve bu da deformasyona veya hasara neden olur. Bu nedenle, bu tür malzemeleri işlerken, aşırı ısınmayı önlemek için genellikle lazer gücünü azaltmak veya soğutma önlemlerini artırmak gerekir.
- Yüzey durumu: Malzemenin yüzey durumu da işaretleme etkisi üzerinde önemli bir etkiye sahip olabilir. Pürüzsüz, temiz bir yüzey lazerin eşit şekilde hareket etmesini ve net ve tutarlı bir işaretleme deseni üretmesini sağlar. Ancak, pürüzlü veya kaplanmış bir yüzey lazer enerjisinin eşit olmayan bir şekilde dağılmasına neden olabilir ve bu da belirsiz işaretlemeye veya yetersiz kontrasta yol açabilir. Kaplamanın kalınlığı ve düzgünlüğü özellikle önemlidir. Kaplama eşit değilse, lazer farklı alanlarda farklı etkiler üretebilir ve bu da tutarsız işaretlemeye yol açabilir. Temizleme, taşlama veya kaplama gibi işaretlemeden önce uygun yüzey hazırlığı, işaretleme etkisini önemli ölçüde iyileştirebilir.
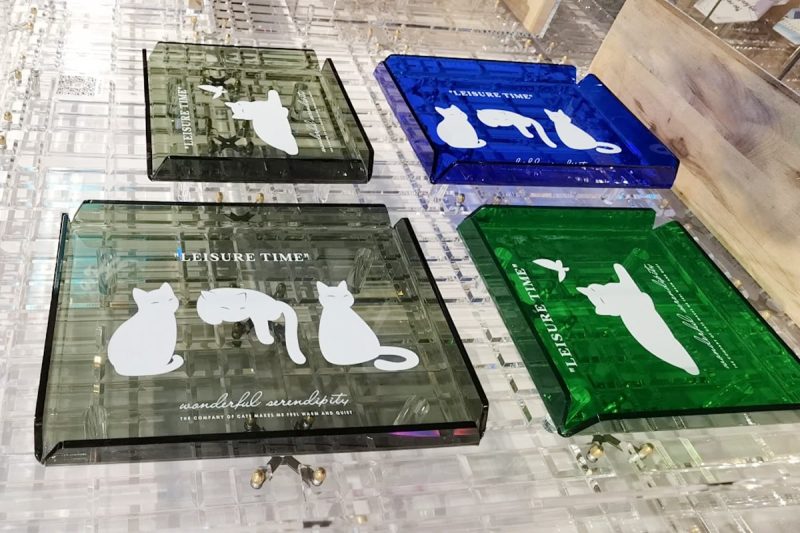
Lazer Parametrelerinin Etkisi
- Güç ayarı: Lazer gücü, işaretlemenin derinliğini ve etkisini etkileyen önemli bir faktördür. Güç ayarı çok yüksek olduğunda, lazer enerjisi çok büyüktür ve bu durum özellikle plastikler veya ince metaller gibi ısıya duyarlı malzemeler için malzeme yüzeyinin aşırı aşınmasına, erimesine veya deformasyonuna kolayca neden olabilir. Aşırı güç ayrıca işaretlemenin pürüzlü ve düzensiz kenarlarına neden olarak genel görünümü etkileyebilir. Güç çok düşük olduğunda, lazer enerjisi yetersizdir ve malzeme yüzeyinde etkili bir şekilde hareket edemez, bu da belirsiz veya hatta tanımlanması zor işaretlemelerle sonuçlanır. Bu nedenle, malzeme yüzeyine zarar vermeden yeterli işaretleme derinliğinin elde edilebilmesini sağlamak için güç ayarının malzemenin özelliklerine ve işaretlemenin özel gereksinimlerine göre hassas bir şekilde ayarlanması gerekir.
- Darbe frekansı: Darbe frekansı, lazer jeneratörü tarafından saniyede yayılan darbe sayısını ifade eder ve bu, işaretlemenin hızı ve yüzey kalitesi üzerinde önemli bir etkiye sahiptir. Daha yüksek bir darbe frekansı, lazer enerjisinin daha eşit şekilde dağıtıldığı anlamına gelir; bu, daha pürüzsüz bir işaretleme yüzeyi üretmeye yardımcı olur ve ince işaretleme gerektiren uygulamalar için uygundur. Ancak, çok yüksek bir frekans, lazer enerjisinin çok dağılmasına da neden olarak işaretlemenin derinliğini ve kontrastını etkileyebilir. Daha düşük bir darbe frekansı, lazer enerjisini daha yoğun hale getirecek ve daha büyük bir işaretleme derinliği gerektiren sahneler için uygundur, ancak yüzeyde hafif bir pürüzlülüğe neden olabilir. Bu nedenle, farklı malzemelere ve işaretleme gereksinimlerine göre, doğru darbe frekansını seçmek derinlik ve yüzey kalitesi arasında bir denge sağlayabilir.
- İşaretleme hızı: İşaretleme hızı, lazerin malzeme yüzeyinde hareket ettiği hızı ifade eder ve bu, işaretlemenin derinliği, verimliliği ve etkisi üzerinde doğrudan bir etkiye sahiptir. Daha yüksek işaretleme hızları üretim verimliliğini artırabilir ve büyük ölçekli işleme ihtiyaçları için uygundur. Ancak hız arttıkça lazer malzeme üzerinde daha kısa süre kalır ve işaretleme derinliği de azalır, bu da işaretlemenin netliğini ve kontrastını etkileyebilir. Derin işaretleme veya daha yüksek hassasiyet gerektiren uygulamalar için, lazerin malzemeyle etkili bir şekilde etkileşime girmesi için yeterli zamana sahip olmasını sağlamak amacıyla genellikle işaretleme hızını düşürmek gerekir. Hız ayarı, verimlilik ve kalite arasında bir denge sağlamak için işaretleme gereksinimlerini ve malzemenin özelliklerini kapsamlı bir şekilde dikkate almalıdır.
- Odak uzaklığı ayarı: Lazer odak uzaklığının doğruluğu, işaretlemenin kalitesi için kritik öneme sahiptir. Odak uzaklığı, lazer ışını ile malzemenin yüzeyi arasındaki mesafeyi ifade eder. Lazer enerjisi, optimum odak uzaklığında yoğunlaşır ve bu da malzemenin yüzeyinde net ve doğru işaretleme efektleri üretebilir. Odak uzaklığı doğru şekilde ayarlanmazsa, lazer ışınının enerjisi dağılır, bu da bulanık ve odak dışı işaretlemeyle sonuçlanır ve net desenler veya metin elde etmek imkansızdır. Özellikle ince işaretlemede, odak uzaklığındaki hafif bir sapma bile nihai efekt üzerinde önemli bir etkiye sahip olacaktır. Ekipmanın odağını düzenli olarak kalibre etmek ve işaretlemeden önce odak uzaklığının doğruluğunu teyit etmek, işaretleme efektinin tutarlılığını sağlamak için önemli adımlardır.
Genel olarak, lazer parametrelerinin doğru ayarlanması, yüksek kaliteli lazer işaretleme sonuçları elde etmek için çok önemlidir. Gücü, darbe frekansını, işaretleme hızını ve odak uzaklığını doğru şekilde ayarlayarak, işaretlemenin netliği, derinliği ve kontrastı etkili bir şekilde iyileştirilebilir ve lazer işaretlemenin farklı malzemelerde ve uygulamalarda en iyi performansı göstermesini sağlar.
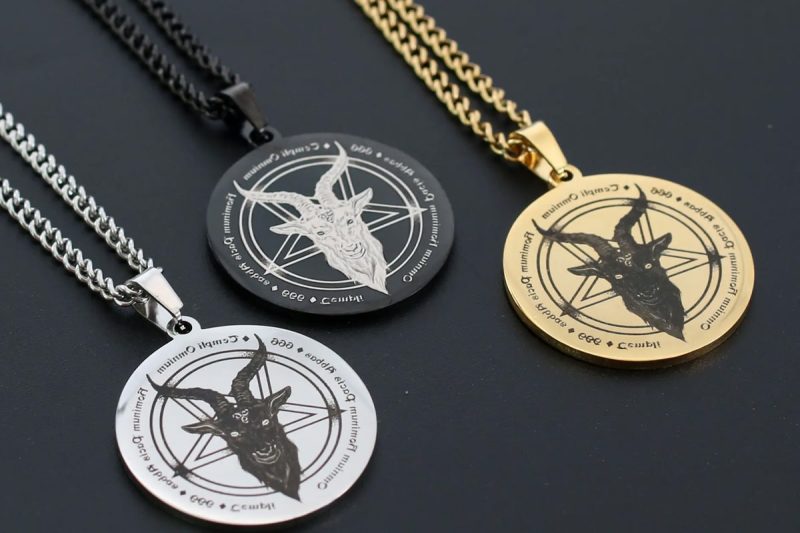
Çevresel Koşulların Etkisi
- Sıcaklık: Ortam sıcaklığı, lazer markalama makinesinin çalışma durumu üzerinde doğrudan bir etkiye sahiptir. Aşırı sıcaklık, özellikle lazer kaynağı ve elektronik bileşenler olmak üzere ekipmanın içinde aşırı ısınmaya neden olabilir. Aşırı ısınma, ekipmanın çalışma verimliliğini düşürecek ve hatta arızaya veya hasara neden olacaktır. Ek olarak, lazer jeneratörünün çıkış gücü yüksek sıcaklıktaki bir ortamda dengesiz hale gelebilir, bu da markalama işlemi sırasında lazer ışınının yoğunluğunda dalgalanmalara ve markalamanın tutarlılığını ve netliğini etkilemeye neden olabilir. Aksine, çok düşük bir sıcaklık, özellikle lazer jeneratörünün ısınmasının daha uzun sürebileceği soğuk bölgelerde veya mevsimlerde ekipmanın başlatılmasını ve normal çalışmasını da etkileyebilir. Bu nedenle, ekipmanın ortam sıcaklığının üreticinin önerdiği aralıkta (genellikle 15°C ila 30°C) tutulması, lazer markalama makinesinin istikrarlı çalışmasını sağlamanın anahtarıdır.
- Nem: Aşırı nem, lazer markalama ekipmanının performansını etkileyen bir diğer büyük gizli tehlikedir. Yüksek nemli bir ortam, lazer markalama makinesinin lensler, mercekler ve diğer önemli bileşenler gibi optik bileşenlerinin nemli olmasına neden olabilir. Bu optik bileşenler nemliyse, lazer ışını iletim sırasında dağılır ve zayıflar ve bu da belirsiz veya bulanık markalama efektlerine neden olur. Ek olarak, yüksek nem, ekipmanın içindeki oksidasyonu ve korozyonu hızlandırabilir ve ekipmanın ömrünü kısaltabilir. Nem sorunlarından kaçınmak için, markalama ekipmanı özellikle yağmurlu mevsimlerde veya nemli alanlarda iyi nem kontrolü olan bir ortama kurulmalıdır. Optik bileşenlerin ve ekipmanın ıslanmasını önlemek için ortam nemini 40%-60% arasında tutmak için nem gidericiler gibi ekipmanların kullanılması önerilir.
- Temizlik: Çalışma ortamının temizliği, lazer markalamanın doğruluğu ve kalitesi üzerinde önemli bir etkiye sahiptir. Toz, kir ve yağ lekeleri gibi parçacıklar, markalama malzemesinin yüzeyine veya ekipmanın optik bileşenlerine birikerek lazer ışınının iletimini ve odak uzaklığının doğruluğunu engelleyebilir ve böylece markalamanın netliğini ve kontrastını azaltabilir. Bir üretim ortamında, özellikle endüstriyel bir alanda, havada çok sayıda toz parçacığı bulunur ve bu da lazer ışını ile malzeme yüzeyi arasındaki etkileşimi etkileyerek düzensiz markalamaya neden olabilir. En iyi markalama etkisini sağlamak için, markalama malzemesinin yüzeyini temiz ve tozsuz tutmak için ekipmanı, özellikle lensi ve optik bileşenleri düzenli olarak temizlemeniz önerilir. Temizleme işlemi sırasında, optik bileşenlerin çizilmesini veya malzeme yüzeyinin hasar görmesini önlemek için uygun temizleme araçlarını ve yöntemlerini kullanın.
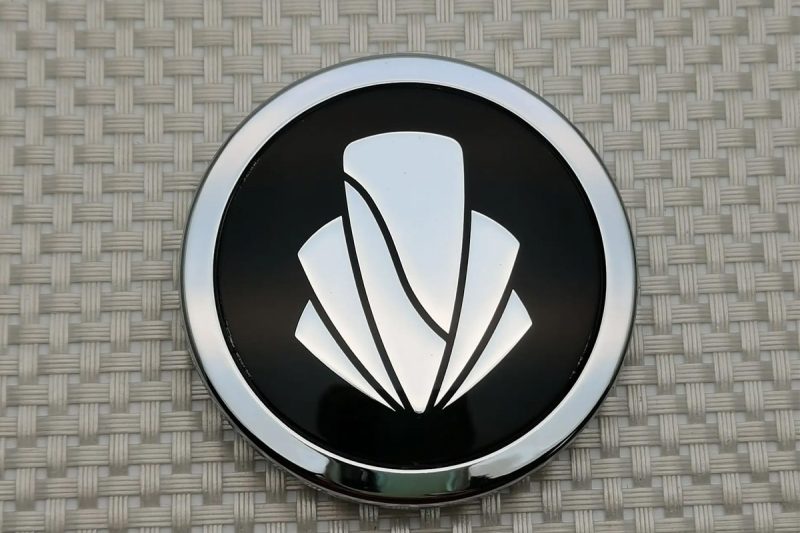
Optik Bileşenlerin Etkisi
- Mercek kalitesi: Mercek, lazer sistemindeki en önemli optik bileşenlerden biridir. İşlevi, lazer ışınını odaklamak ve onu malzemenin yüzeyine doğru bir şekilde yansıtmaktır. Mercek kalitesi düşükse, örneğin çizikler, toz veya mercek yüzeyinde yetersiz optik performans varsa, lazer ışını odaklama işlemi sırasında sapacak veya enerji kaybedecektir, bu da işaretlemenin doğruluğunu ve netliğini etkileyecektir. Düşük kaliteli mercekler, özellikle ince işlemenin gerektiği durumlarda bulanık işaretlemeye, odak dışı kalmaya veya düzensiz enerji dağılımına neden olabilir, işaretleme efekti kaba ve düzensiz görünecektir. Bu nedenle, yüksek kaliteli optik mercekler seçmek ve istikrarlı optik performanslarını sağlamak için bunları düzenli olarak temizlemek ve bakımını yapmak, işaretleme doğruluğunu sağlamanın anahtarıdır.
- Işın iletim sistemi: Işın iletim sistemi, lazeri lazer kaynağından markalama malzemesinin yüzeyine iletmekten sorumludur. Bu işlem sırasında, lazerin enerjisi herhangi bir enerji kaybı veya ışın saçılması olmadan verimli bir şekilde iletilmelidir. İletim işlemi sırasında herhangi bir kayıp, lazerin yoğunluğunu ve odaklama etkisini etkileyerek yetersiz işaretleme derinliğine veya azalmış netliğe neden olur. Işın iletiminin verimliliğini sağlamak için, reflektörler ve iletim optik lifleri gibi iletim sisteminin çeşitli bileşenleri son derece temiz ve sağlam tutulmalıdır. Optik bileşenlerdeki herhangi bir toz, kir veya hasar, ışının saçılmasına ve zayıf bir şekilde yansımasına neden olarak işaretleme sonuçlarını etkiler. Verimli ve kayıpsız bir ışın iletim sistemi, işaretleme işleminin kararlılığını ve tutarlılığını sağlayarak her seferinde ideal etkinin elde edilmesini sağlar.
- Galvanometre tarayıcı: Galvanometre tarayıcı, lazer ışınının hızlı hareketini ve hassas konumlandırmasını kontrol eden ve işaretleme deseninin hızını, doğruluğunu ve tutarlılığını doğrudan belirleyen önemli bir bileşendir. Galvanometre tarayıcı, malzemenin yüzeyine gerekli deseni veya karakteri çizmek için lazer ışınının yönünü yüksek hızlı bir reflektör aracılığıyla ayarlar. Tarama hızı ve doğruluğu, işaretleme efekti için özellikle önemlidir. Yüksek hassasiyetli galvanometre tarayıcılar, çizgilerde veya desenlerde sapmaları önlemek için lazer ışınının karmaşık veya küçük desenlerde hassas bir şekilde konumlandırılmasını sağlayabilir. Yüksek hızlı galvanometre tarayıcılar işaretleme verimliliğini artırabilir ve seri üretim ihtiyaçları için uygundur. Ancak, çok hızlı tarama hızı, işaretlemenin derinliğini ve kontrastını etkileyen eşit olmayan enerji dağılımına neden olabilir. Bu nedenle, hızı sağlarken, galvanometrenin doğruluğunun makul bir aralıkta kalmasını sağlamak da gereklidir. Galvanometre tarayıcının kalitesi ve performansı, işaretleme efektinin istikrarı için çok önemlidir. Bu nedenle, yüksek hızlı taramalarda bile doğru işaretleme efektlerini koruyabilmesini sağlamak için yüksek performanslı bir galvanometre sistemi seçilmeli, kalibre edilmeli ve düzenli olarak bakımı yapılmalıdır.
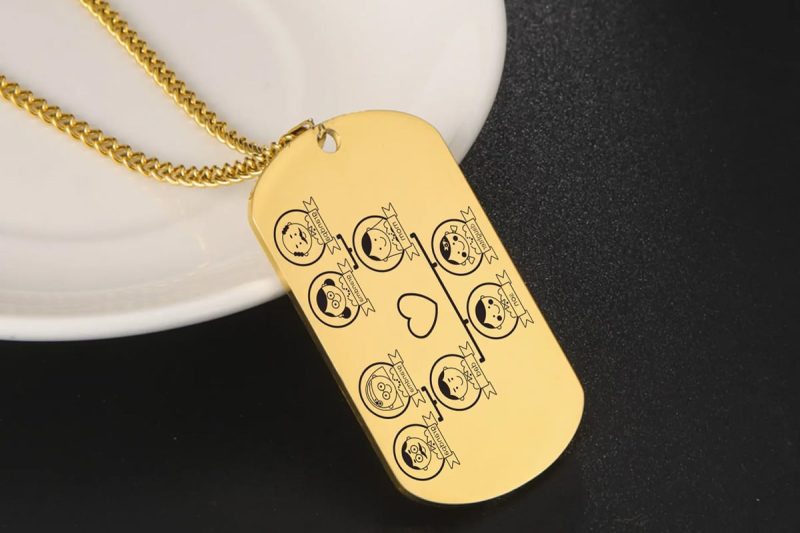
Yazılım ve Kontrol Sistemlerinin Etkisi
- Markalama yazılımı: Markalama yazılımı, lazer markalama ekipmanını kontrol etmek için önemli bir araçtır. Lazer gücü, markalama hızı, darbe frekansı vb. gibi lazer jeneratör parametrelerini ayarlamak ve ayarlamakla sorumludur. Yüksek kaliteli yazılım yalnızca bu temel parametreleri doğru bir şekilde kontrol etmekle kalmaz, aynı zamanda desen tasarımı, yazı tipi seçimi, barkod ve QR kodu oluşturma vb. gibi zengin markalama işlevleri de sağlar. Ek olarak, markalama yazılımı çok seviyeli markalama sağlayabilir ve metal, plastik, cam ve diğer malzemeler üzerinde yüksek hassasiyet ve farklı derinlik markalama gibi farklı malzemelerin çeşitli işleme gereksinimlerini destekleyebilir. Gelişmiş markalama yazılımları genellikle kullanıcı dostu bir arayüze sahiptir, işlem sürecini basitleştirir, operatörlerin sistemle hızlı bir şekilde tanışmasını ve ustalaşmasını sağlar, insan operasyon hatalarını azaltır ve böylece üretim verimliliğini ve markalama kalitesini artırır. Aynı zamanda, yazılımın yükseltilebilirliği de çok önemlidir. Teknolojinin gelişmesi ve pazar talebindeki değişikliklerle birlikte, markalama yazılımının yeni markalama gereksinimlerine uyum sağlamak için sürekli olarak güncellenmesi ve optimize edilmesi gerekir.
- Hareket kontrol sistemi: Hareket kontrol sistemi, lazer markalama makinesinde lazer kafası ile iş parçası arasındaki koordineli hareketi kontrol etmek için kullanılan temel bileşendir. Markalama işlemi sırasında lazer kafası ile işlenecek iş parçasının doğru bir şekilde senkronize edilmesini ve böylece lazer ışınının belirlenen yörüngeye göre malzeme yüzeyinde hareket etmesini sağlar. Bu senkronizasyon, markalama deseninin tutarlılığını ve doğruluğunu elde etmek için önemlidir. Hareket kontrol sistemleri genellikle motorlar, sensörler ve denetleyiciler gibi donanımları içerir ve gerçek zamanlı izleme ve ayarlama için markalama yazılımıyla işbirliği yapar. Yüksek hassasiyetli markalamada, özellikle karmaşık desenlerin malzemelerin geniş alanlarına işaretlenmesi gerektiğinde, hareket kontrol sisteminin doğruluğu ve tepki hızı özellikle önemlidir. Hareket kontrol sistemi yeterince hassas değilse, lazer markalama kafası sapabilir ve desen deformasyonu ve düzensiz çizgiler gibi sorunlara neden olabilir. Bu nedenle, istikrarlı ve verimli bir hareket kontrol sistemi, lazer markalamanın tutarlılığını ve netliğini sağlamak için temel faktörlerden biridir.
- Otomasyon: Son derece otomatik bir lazer markalama sistemi, üretim verimliliğini önemli ölçüde artırabilir, insan operasyonundaki hataları azaltabilir ve her ürün partisinin tutarlı markalama efektleri elde etmesini sağlayabilir. Otomatik bir kontrol sistemi tanıtılarak, lazer markalama ekipmanı, parti ve sürekli markalama işlemlerini elde etmek için üretim hattına sorunsuz bir şekilde bağlanabilir. Örneğin, otomatik sistem iş parçasını otomatik olarak tanımlayabilir ve yerini belirleyebilir, lazer markalama kafasının yüksekliğini ve odak uzaklığını ayarlayabilir ve her markalamanın optimum koşullar altında gerçekleştirilmesini sağlayabilir. Otomatik sistem ayrıca, insan müdahalesi olmadan farklı partilerin markalama desenini ve parametrelerini otomatik olarak değiştirebilir ve üretim esnekliğini büyük ölçüde artırabilir. Ek olarak, otomasyon sistemi, üretim verilerinin gerçek zamanlı izlenmesini ve analizini sağlamak için diğer fabrika yönetim sistemlerine bağlanabilir ve işletmelerin üretim süreçlerini optimize etmesine, ürün kalitesini iyileştirmesine ve maliyetleri düşürmesine yardımcı olur. Otomatik markalama sistemi ayrıca operatör katılımını azaltabilir ve özellikle avantajlarının özellikle belirgin olduğu yüksek talep ve yüksek hacimli üretim ortamlarında işçilik maliyetlerini düşürebilir.
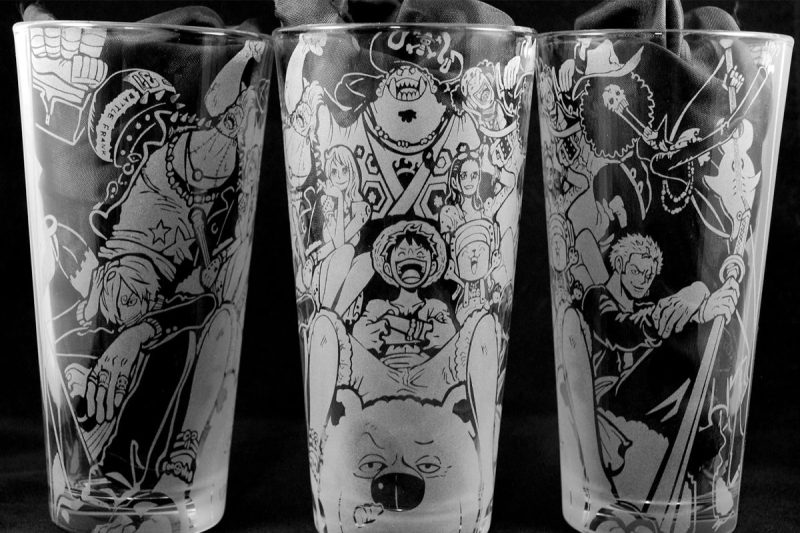
Soğutma Sisteminin Etkisi
- Hava soğutma: Hava soğutma sistemleri genellikle bazı küçük fiber lazer markalama makineleri gibi düşük güçlü lazer ekipmanları için kullanılır. Bu soğutma yöntemi, fanlar gibi hava sirkülasyon cihazları aracılığıyla lazer jeneratöründen ve diğer önemli bileşenlerden ısıyı uzaklaştırır. Hava soğutma sisteminin basit yapısı ve düşük bakım maliyeti nedeniyle, düşük ısı dağılımı gereksinimleri olan uygulama senaryoları için uygundur. Hava soğutma sistemi, küçük bir ayak izi ve kompakt tasarım avantajlarına sahiptir. Genellikle harici soğutma ekipmanına ihtiyaç duymadan ekipmana entegre edilir. Bu nedenle, sınırlı hacme sahip küçük lazer markalama makinelerinde yaygın olarak kullanılır. Ancak, hava soğutmanın ısı dağıtma etkisi nispeten zayıftır ve yüksek güçlü lazer jeneratörleri tarafından üretilen büyük miktardaki ısıyla baş edemez. Yüksek güçlü ekipman hava ile soğutulursa, ısı birikimi meydana gelebilir ve lazer jeneratörünün performansını ve ömrünü etkileyebilir. Bu nedenle, hava soğutma sistemi esas olarak düşük güç ve düşük ısı dağılımı gereksinimleri olan lazer ekipmanları için uygundur.
- Su soğutma sistemi: Hava soğutma ile karşılaştırıldığında, su soğutma sistemi yüksek güçlü lazer markalama ekipmanları için uygundur, özellikle uzun süreli sürekli çalışma gerektiğinde daha etkili ısı dağılımı sağlayabilir. Su soğutma sistemi, soğutma sıvısını (genellikle su veya soğutma sıvısı) bir su pompası aracılığıyla lazer jeneratörünün ve diğer ısı üreten bileşenlerin yakınına dolaştırır ve suyun verimli ısı transferi yoluyla ısıyı hızla uzaklaştırır. Hava soğutma ile karşılaştırıldığında, su soğutma sistemi daha yüksek ısı kapasitesine ve iletim verimliliğine sahiptir, bu da ekipmanın yüksek sıcaklık ortamlarında veya yüksek yoğunluklu çalışma koşullarında kararlı çalışmasını sağlayabilir ve lazer jeneratörünün aşırı ısınmasından kaynaklanan güç zayıflamasını veya markalama kalitesinin bozulmasını önleyebilir. Ek olarak, su soğutma sistemi sıcaklık dalgalanmalarını kontrol edebilir ve lazer jeneratörünün her zaman optimum sıcaklık aralığında çalışmasını sağlayarak ekipmanın hizmet ömrünü uzatabilir.
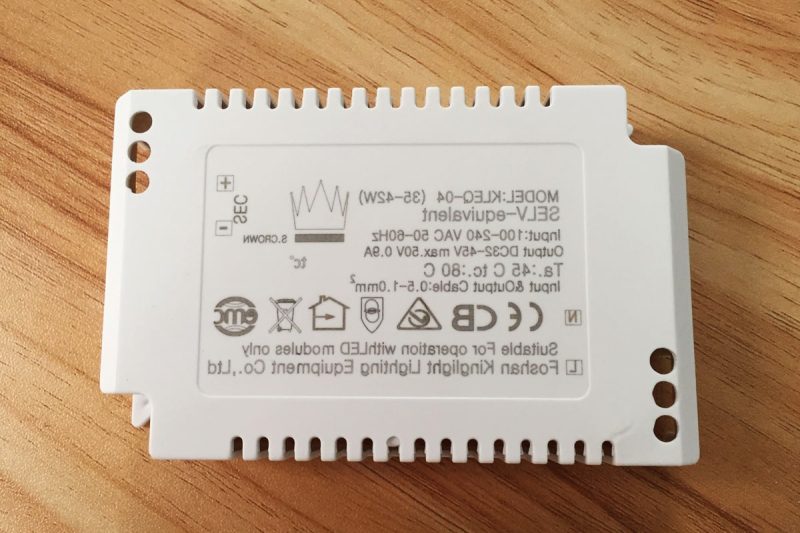
Operatör Becerileri ve Eğitimi
- Uzmanlık: Lazer markalama operatörlerinin sağlam bir uzmanlığa, özellikle farklı malzeme özellikleri ve lazer parametreleri hakkında bilgiye sahip olmaları gerekir. Farklı malzemelerin farklı emilim oranları, yansıtma oranları ve lazerlerin termal iletkenlikleri vardır, bu nedenle operatörler lazer gücü, markalama hızı, darbe frekansı vb. gibi lazer parametrelerini malzemelerin özelliklerine göre makul bir şekilde ayarlamalıdır. Örneğin, metal malzemeler genellikle daha yüksek güçlü fiber lazer jeneratörleri gerektirirken, plastik veya cam gibi metal olmayan malzemeler UV lazerler veya CO2 lazer jeneratörleri için daha uygun olabilir. Operatörün malzeme özellikleri ve lazer jeneratörü türleri hakkında yeterli bilgisi yoksa, bu tatmin edici olmayan markalama sonuçlarına, düzensiz derinliğe, bulanıklığa ve yanmaya yol açabilir. Sistematik eğitim yoluyla, operatörler farklı malzemelerin markalama gereksinimlerinde ustalaşabilir ve her markalamanın en iyi sonuçları elde edebilmesini sağlayabilir.
- Kalibrasyon ve bakım: Lazer markalama ekipmanları, uzun süreli kullanım sırasında lensler, galvanometreler ve ışın iletim sistemleri gibi temel bileşenlerde aşınma veya sapma yaşayabilir. Bu nedenle, ekipmanın ışın kalitesinin ve işaretleme doğruluğunun her zaman en iyi durumda olmasını sağlamak için düzenli ekipman kalibrasyonu ve bakımı esastır. Operatörlerin, sorunları derhal tespit edip çözmek için ekipmanın günlük denetimlerini ve basit sorun giderme işlemlerini gerçekleştirme yeteneğine sahip olması gerekir. Örneğin, lazer jeneratörünün güç zayıflaması, galvanometre taramasının azalan doğruluğu ve optik bileşenlerin kirlenmesi, işaretleme etkisini etkileyecektir. İyi eğitimli operatörler, lazer markalama ekipmanının istikrarlı çalışmasını sağlamak ve ekipman arızası veya parametre sapmasından kaynaklanan üretim durgunluğunu veya kalite düşüşünü azaltmak için ekipmanı düzenli olarak kalibre edebilir. Ek olarak, bakım yalnızca ekipmanın hizmet ömrünü uzatmakla kalmaz, aynı zamanda beklenmeyen duruş sürelerini veya büyük arızaları önleyebilir ve onarım maliyetlerini azaltabilir.
- Operasyon yeterliliği ve güvenlik bilinci: Lazer markalama ekipmanının operasyonu basit hale gelmiş olsa da operatörlerin ekipmanı verimli bir şekilde çalıştırmak için hala belirli bir yeterlilik seviyesine sahip olmaları gerekir. Operatörler, markalama yolunu ayarlama, odak uzaklığını ayarlama ve uygun markalama hızı ve gücünü seçme gibi işteki çeşitli markalama görevlerinin operasyon prosedürlerine hakim olmalıdır. Nitelikli operatörler, farklı markalama ihtiyaçlarını karşılamak için parametreleri hızlı bir şekilde değerlendirebilir ve ayarlayabilir, böylece üretim verimliliğini artırabilir. Ayrıca, operatörler belirli bir güvenlik bilinci seviyesine de sahip olmalıdır. Lazer ekipmanları, çalışma sırasında lazer radyasyonu ve ısı üretimi gibi belirli güvenlik tehlikelerine sahip olabilir. Profesyonel eğitim almış operatörler, uygunsuz operasyondan kaynaklanan güvenlik sorunlarını etkili bir şekilde önleyebilir ve üretim ortamının güvenliğini sağlayabilir.
- Sürekli öğrenme ve teknoloji güncellemeleri: Lazer markalama teknolojisi sürekli olarak güncellenir ve yeni markalama ekipmanı ve yazılım işlevleri de piyasaya sürülür. Bu nedenle, operatörlerin yeni teknolojileri öğrenmeye ve bunlara uyum sağlamaya, eğitim yoluyla yeni lazer jeneratörlerinin ve markalama yazılımlarının işleyişinde ustalaşmaya ve en son süreç iyileştirmelerini anlamaya devam etmesi gerekir. Operatörlerin sürekli öğrenmesi, şirketlerin rekabet gücünü korumasına, markalama verimliliğini ve ürün kalitesini iyileştirmesine ve değişen pazar taleplerini karşılamasına yardımcı olabilir.
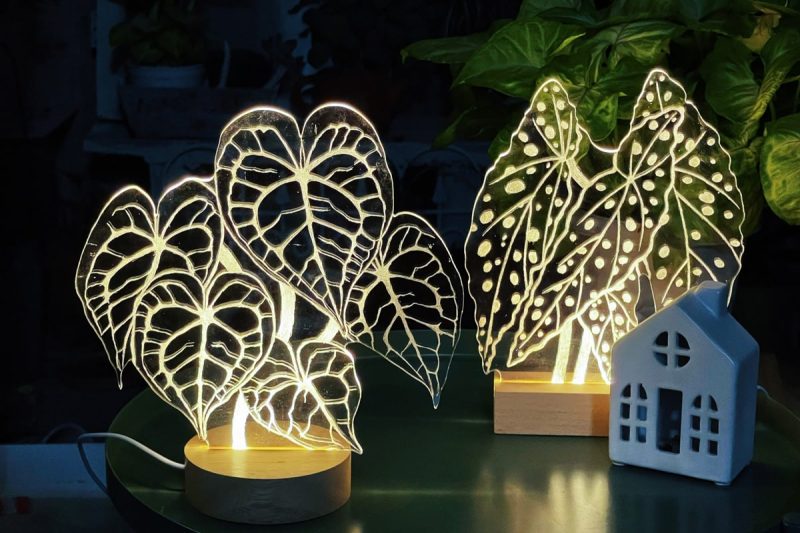
Malzeme Taşıma ve Fikstürlemenin Etkisi
Fikstür
- İş parçasının sabitliğini sağlayın: Hassas sıkıştırma ve sabitleme, iş parçasının işaretleme işlemi sırasında hafifçe hareket etmesini önleyerek, işaretleme deseninin doğru konumlandırılmasını ve tutarlılığını sağlar. Bu, özellikle küçük karakterlerin veya karmaşık desenlerin işaretlenmesi gibi yüksek hassasiyetli işaretleme görevleri için önemlidir.
- Hataları azaltın: Sabit bir fikstür, iş parçasının pozisyonundaki değişikliklerden kaynaklanan işaretleme hatalarını etkili bir şekilde azaltabilir, ürün tutarlılığını ve kalitesini iyileştirebilir. Özellikle büyük ölçekli üretimde, tutarlı fikstür ayarları her iş parçasının aynı koşullar altında işaretlenmesini sağlayabilir.
- Farklı iş parçalarına uyum sağlayın: Fikstürün tasarımı, çeşitli üretim görevlerinde esnek bir şekilde uygulanabilmesi için farklı şekil ve boyutlardaki iş parçalarını dikkate almalıdır. Fikstür, operatörün farklı iş parçası gereksinimlerine göre ayarlamasını kolaylaştırmak için hızlı ayarlama işlevine sahip olmalı ve böylece üretim verimliliğini artırmalıdır.
Malzeme hazırlama
- Temizlik: İşaretlemeden önce, malzeme yüzeyinin temizliği kritik öneme sahiptir. Kir, gres ve toz gibi kirlilikler lazer ışınının iletimini engelleyerek bulanık ve düzensiz işaretleme desenlerine neden olabilir. Ultrasonik temizleme veya kimyasal temizleme gibi uygun temizleme yöntemlerinin kullanılması, yüzey kirliliğini etkili bir şekilde giderebilir ve lazer işaretlemenin netliğini ve tutarlılığını sağlayabilir.
- İşlem: Bazı malzemeler, yüzey bitişlerini ve lazer yapışmasını iyileştirmek için taşlama, kumlama veya kimyasal işlem gibi ek yüzey işlemleri gerektirebilir. Bu işlem adımları, malzeme yüzeyinin pürüzlülüğünü azaltabilir ve özellikle yüksek pürüzsüzlüğün gerekli olduğu uygulama senaryolarında işaretleme etkisini artırabilir.
- Muayene: İşaretlemeden önce, malzeme yüzeyi işaretleme gerekliliklerini karşıladığından emin olmak için incelenmelidir. Belirgin kusurları veya düzensiz yüzeyleri olan malzemeler, son işaretleme etkisini olumsuz etkilememek için ek işlem gerektirebilir.
Toplu İşleme
- Standardizasyon: Seri üretimde tutarlı markalama sonuçlarını korumak için, standartlaştırılmış işletme prosedürleri ve fikstür tasarımları benimsenmelidir. Standardizasyon, operasyonel farklılıklardan veya tutarsız iş parçası konumlarından kaynaklanan markalama hatalarını azaltabilir.
- Otomasyon: Seri üretimde, otomasyon sistemlerinin uygulanması üretim verimliliğini ve tutarlılığını önemli ölçüde iyileştirebilir. Otomatik sistemler, çok sayıda iş parçasının işaretlenmesi görevini hızlı ve verimli bir şekilde tamamlayabilir ve her bir iş parçasının aynı koşullar altında işlenmesini sağlayarak insan hatasını ve üretimdeki dalgalanmaları azaltabilir.
- Kalite Kontrolü: Toplu üretimde, her ürün partisinin kalite standartlarını karşıladığından emin olmak için düzenli denetimler ve testler de dahil olmak üzere sıkı kalite kontrol önlemlerinin uygulanması gerekir. İşaretleme etkisinin gerçek zamanlı izlenmesi, ürün tutarlılığını ve istikrarını sağlamak için potansiyel sorunları derhal tespit edebilir ve düzeltebilir.
Özetle, fikstür tasarımı, malzeme hazırlama ve toplu işleme, lazer markalamanın kalitesini etkileyen önemli faktörlerdir. Fikstürün kararlılığını optimize ederek, malzeme yüzeyinin temizliğini ve tutarlılığını iyileştirerek ve toplu üretimde standardizasyon ve otomasyon uygulayarak, şirketler markalama sürecinin yüksek hassasiyetini, yüksek verimliliğini ve yüksek kalitesini sağlayabilir.
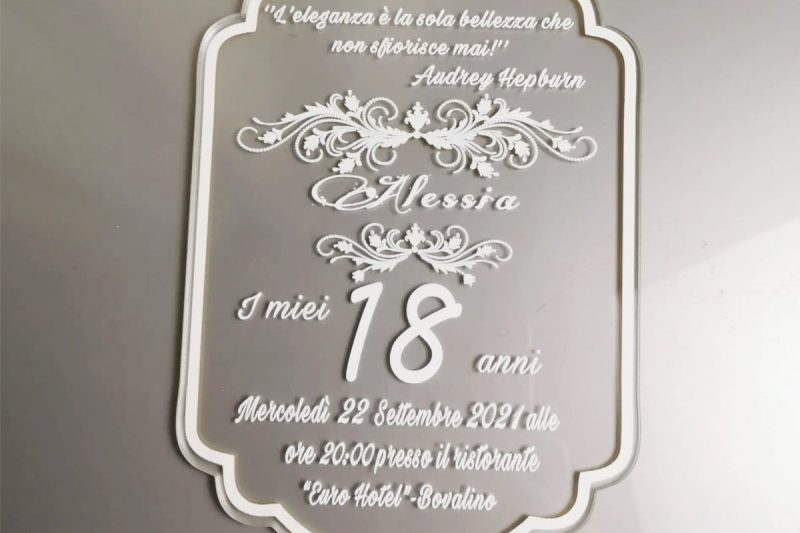
Uygulamaya Özel Faktörlerin Etkisi
Markalama Derinliği
- Derinlik gereksinimleri: Üretim ve endüstriyel parçalar gibi bazı özel uygulamalarda, işaretin dayanıklı olmasını ve uzun süreli kullanımda okunabilir kalmasını sağlamak için daha derin bir işaret gerekebilir. Örneğin, havacılık parçaları ve aletleri genellikle yüksek sürtünmeli ve zorlu ortamlarda okunabilir kalmak için daha derin bir işaret gerektirir. Derin işaretler yalnızca işaretin dayanıklılığını iyileştirmekle kalmaz, aynı zamanda aşınmaya karşı direncini de artırır.
- Yüzey işaretleme: Buna karşılık, tüketici ürünü etiketleri veya dekoratif işaretlemeler gibi yalnızca yüzey işaretlemesi gerektiren bazı uygulamalar için daha sığ bir işaretleme derinliği yeterlidir. Bu durumda, daha sığ bir işaretleme derinliği, işaretlemenin okunabilirlik gereksinimlerini karşılarken malzeme kaybını ve işleme maliyetlerini azaltabilir.
İşaretleme Kontrastı
- QR kodları ve barkodlar: QR kodları ve barkodlar gibi makine tarafından okunabilen işaretler için yüksek kontrast esastır. Yüksek kontrastlı işaretler, tarama cihazlarının bilgileri doğru bir şekilde okuyabilmesini ve bulanık işaretler veya yetersiz kontrast nedeniyle okuma hatalarından kaçınmasını sağlar. Uygun lazer parametreleri ve malzeme işleme teknolojisi kullanılarak, işaretin kontrastı artırılarak bilgilerin güvenilir bir şekilde iletilmesi sağlanabilir.
- Görsel işaretleme: Ürün numaraları, marka logoları vb. gibi manuel tanımlama gerektiren bazı uygulamalarda yüksek kontrast aynı derecede önemlidir. Net işaretleme, tanıma verimliliğini ve doğruluğunu artırabilir ve yanlış tanımlama olasılığını azaltabilir. Bu durumlarda, işaretleme makinesinin işaretin netliğini ve okunabilirliğini sağlamak için parametreleri farklı malzemelerin özelliklerine göre ayarlaması gerekir.
Markalama Dayanıklılığı
- Zorlu ortamlar: Bazı endüstriyel uygulamalarda, işaretlemenin yüksek sıcaklıklar, kimyasal korozyon ve ultraviyole radyasyon gibi zorlu ortamlara dayanıklı olması gerekir. Örneğin, otomotiv parçaları ve mekanik ekipmanlar kullanım sırasında çeşitli dış etkenlere maruz kalır ve bu da işaretlemenin yüksek dayanıklılığa ve kayba karşı dirence sahip olmasını gerektirir. Doğru lazer türünü ve malzeme işleme sürecini seçmek, işaretlemenin dayanıklılığını artırabilir ve işaretlemenin uzun süreli kullanımda net ve okunabilir kalmasını sağlayabilir.
- Uzun süreli kullanım: Elektronik bileşenlerdeki seri numaraları veya tıbbi cihazlardaki logolar gibi uzun süre korunması gereken bazı işaretler için dayanıklılık da aynı derecede önemlidir. Lazer işaretleme makinesinin, işaretlemenin uzun süreli kullanımda solmamasını, aşınmamasını veya kaybolmamasını sağlamak için lazer parametrelerini ayarlaması, orijinal durumunu ve işlevini koruması gerekir.
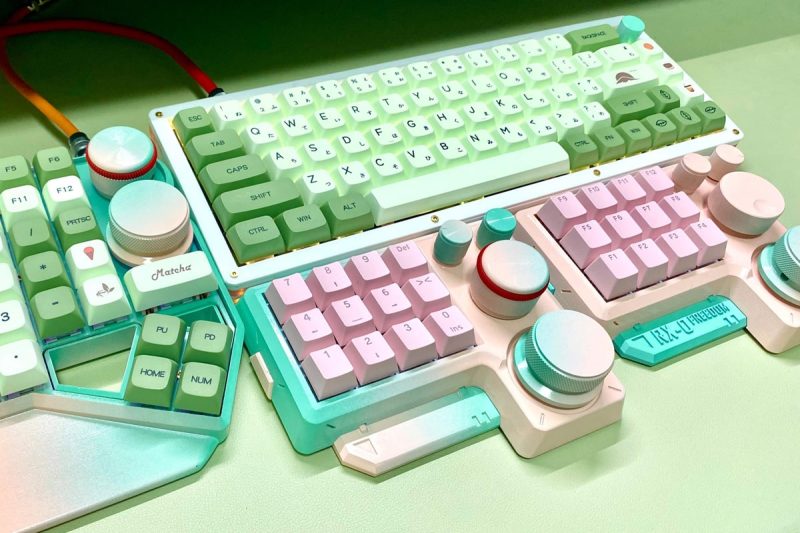
özetle
- Lazer kaynağının seçimi doğrudan uygulanabilir malzemeleri ve işaretleme sonuçlarını belirler. Örneğin, fiber lazerler metal malzemeler için uygundur, CO2 lazerler metal olmayan malzemeler için uygundur ve ultraviyole (UV) lazerler ince işaretleme gerektiren uygulamalar için uygundur.
- Emilim, yansıtma ve yüzey durumu gibi malzeme özellikleri lazer ışınının iletimini ve nihai işaretleme etkisini etkileyecektir. Malzeme elleçleme ve yüzey hazırlığı da işaretleme kalitesi üzerinde doğrudan bir etkiye sahiptir.
- Lazer parametreleri arasında güç ayarları, darbe frekansı, işaretleme hızı ve odak uzaklığı ayarı yer alır ve net ve uyumlu işaretlemeyi sağlamak için bunların doğru bir şekilde ayarlanması gerekir.
- Sıcaklık, nem ve temizlik gibi çevresel koşullar ekipmanın stabilitesini ve lazer ışınının kalitesini etkileyecektir.
- Mercek kalitesi, ışın iletim sistemi ve galvanometre tarayıcısı gibi optik bileşenlerin performansı da doğrudan işaretlemenin doğruluğu ve tutarlılığıyla ilgilidir.
- Yazılım ve kontrol sistemlerinin kalitesi, işaretlemenin doğruluğunu ve kullanım kolaylığını belirler. Mükemmel yazılım ve otomasyon sistemleri, işaretleme verimliliğini ve kalitesini artırabilir.
- Soğutma sistemi, lazer ekipmanının istikrarlı çalışması için hayati önem taşır. Verimli bir soğutma sistemi, ekipmanın ömrünü uzatabilir ve ekipman performansını koruyabilir.
- Operatör becerileri ve eğitimi, işaretleme kalitesinin sağlanmasının temelini oluşturur. Profesyonel bir operatör, ekipman parametrelerini doğru bir şekilde ayarlayabilir ve ekipmanın en iyi performansını sağlamak için düzenli bakım yapabilir.
- Malzeme taşıma ve fikstür tasarımı da işaretleme etkisini etkileyen önemli faktörlerdir. Sabit fikstürler ve uygun malzeme taşıma, işaretlemenin tutarlılığını ve doğruluğunu artırabilir.
- Markalama derinliği, kontrast, dayanıklılık gibi uygulamaya özgü faktörler olmakla birlikte, uygulama gereksinimlerine bağlı olarak markalama kalite standartları da farklılık göstermektedir.
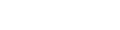
- [email protected]
- [email protected]
- +86-19963414011
- 3 Bölge A, Lunzhen Sanayi Bölgesi, Yucheng Şehri, Shandong Eyaleti.