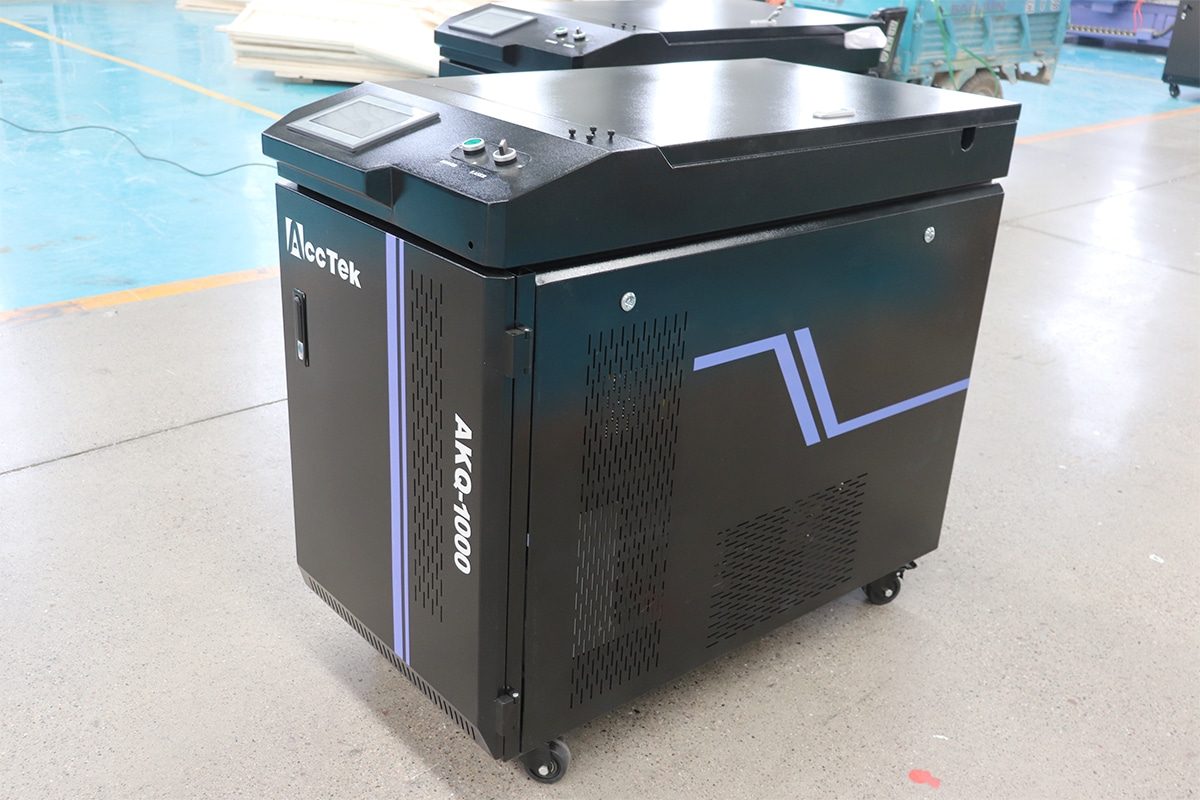
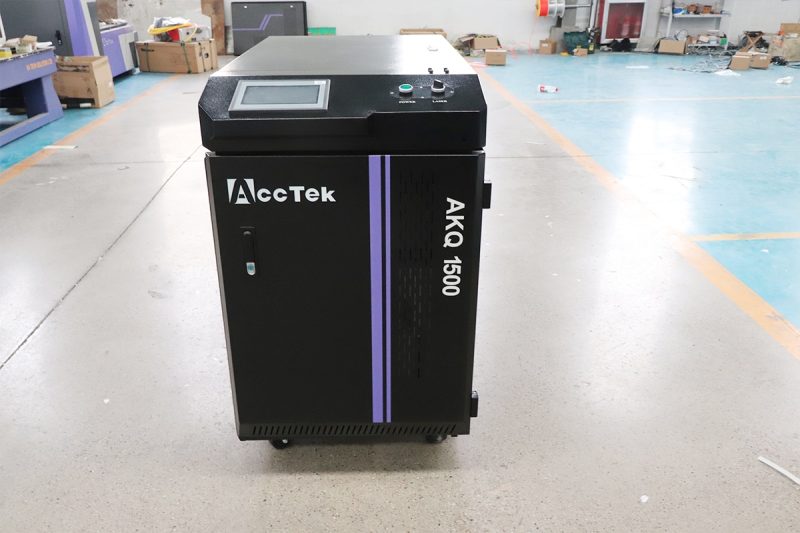
Lazer Parametreleri
dalga boyu
Nabız Süresi
Darbe Tekrarlama Oranı
Enerji Yoğunluğu (Akı)
Işın Profili ve Odak
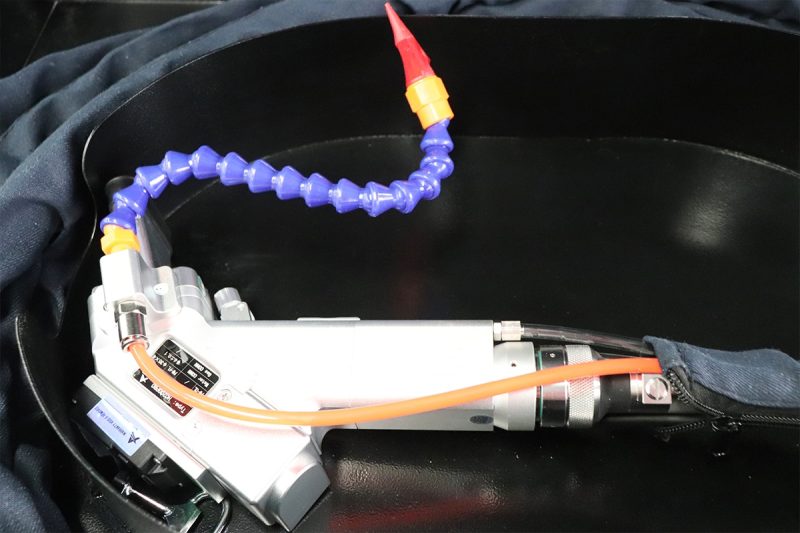
Malzeme özellikleri
Emilim Özellikleri
İlgili malzemelerin emme özellikleri, lazer temizliğinin etkinliğinin belirlenmesinde önemli bir rol oynar. Soğurma özellikleri, bir malzemenin belirli bir dalga boyunda lazer enerjisini ne kadar iyi emdiğini ifade eder. Farklı malzemeler, atomik ve moleküler yapılarına bağlı olarak lazer enerjisini farklı şekilde emer:
- Substrat Emilimi: Bir substratın lazer enerjisini absorbe etme yeteneği, malzeme içinde üretilen ısı miktarını etkiler. Lazer dalga boyunda yüksek emme katsayılarına sahip malzemeler daha hızlı ısınır ve bu da temizleme işlemine yardımcı olabilir veya uygun şekilde kontrol edilmezse alt tabakaya zarar verme potansiyeline sahiptir.
- Kirletici Madde Emilimi: Etkili lazer temizliği, kirletici maddenin lazer enerjisini alt tabakaya göre daha kolay absorbe etmesini gerektirir. Bu diferansiyel emilim, kirletici maddenin alt tabakayı önemli ölçüde etkilemeden yok edilmesini sağlar. Örneğin pas (demir oksit), kızılötesi lazer enerjisini etkili bir şekilde emer ve kızılötesi lazerler kullanılarak metal yüzeylerden daha kolay uzaklaştırılır.
Termal Özellikler
Hem alt tabakanın hem de kirletici maddenin termal özellikleri, lazerle temizleme sırasında ısının nasıl yönetildiğini etkiler. Temel termal özellikler arasında termal iletkenlik, özgül ısı ve erime noktası bulunur:
- Isı iletkenliği: Metaller gibi yüksek ısı iletkenliğine sahip malzemeler ısıyı hızlı bir şekilde dağıtarak yerel aşırı ısınma ve hasar riskini azaltabilir. Tersine, bazı polimerler gibi düşük ısı iletkenliğine sahip malzemeler ısıyı tutabilir ve bu da temizleme işlemi sırasında termal hasar riskini artırır.
- Özgül ısı: Bir malzemenin özgül ısısı, sıcaklığını yükseltmek için gereken enerji miktarını temsil eder. Yüksek özgül ısıya sahip malzemeler, sıcaklıklarını önemli ölçüde yükseltmeden daha fazla enerji emebilir, bu da onları lazerle temizleme sırasındaki termal hasara karşı daha dayanıklı hale getirir.
- Erime ve kaynama noktaları: Alt tabakanın ve kirletici maddelerin erime ve kaynama noktaları, bunların lazer ısıtmaya tepkisini etkiler. Amaç genellikle kirleticiyi alt tabakanın erime noktasına ulaşmadan buharlaştırmak veya süblimleştirmektir. Bu eşikleri anlamak, etkili temizlik için uygun lazer parametrelerinin seçilmesine yardımcı olur.
Mekanik özellikler
Alt tabakanın ve kirletici maddelerin sertlik, kırılganlık ve süneklik dahil olmak üzere mekanik özellikleri lazer temizleme işlemini etkileyebilir:
- Sertlik: Daha sert malzemeler aşındırmaya karşı dirençli olabilir ve etkili temizlik için daha yüksek enerji yoğunlukları gerektirebilir. Alt tabakanın kirletici maddeye göre sertliği, kirletici maddenin alt tabakaya zarar vermeden ne kadar kolay giderilebileceğini etkiler.
- Kırılganlık: Bazı seramikler veya camlar gibi kırılgan malzemeler, lazer darbesinin neden olduğu gerilim altında çatlamaya veya kırılmaya daha duyarlıdır. Kırılgan yüzeylere zarar vermemek için lazer parametreleri dikkatlice kontrol edilmelidir.
- Sünek: Birçok metal gibi sünek malzemeler, lazerin neden olduğu stres altında plastik olarak deforme olur. Bu bazen enerjinin emilmesi ve hasarın önlenmesi açısından yararlı olsa da aşırı süneklik, hassas temizleme uygulamalarında istenmeyen yüzey değişikliklerine yol açabilir.
Kirletici Özellikleri
Kirleticinin doğası, lazer temizliğinin etkinliğini belirlemede önemli bir faktördür. Kirletici maddeler kimyasal bileşimleri, fiziksel durumları, kalınlıkları ve alt tabakaya yapışmaları açısından büyük farklılıklar gösterebilir.
- Kimyasal bileşim: Farklı kirletici maddeler lazer enerjisine farklı tepki verir. Örneğin, yağ ve gres gibi organik kirleticiler lazere maruz kaldığında buharlaşabilir veya ayrışabilir; pas veya kireç gibi inorganik kirleticiler ise etkili bir şekilde uzaklaştırılması için daha yüksek enerji yoğunlukları gerektirebilir. Kimyasal bileşim aynı zamanda kirleticinin emme özelliklerini ve termal tepkisini de etkiler.
- Kalınlık: Kirletici katmanın kalınlığı, uzaklaştırma için gereken enerjiyi etkiler. Daha kalın katmanların tamamen yok edilmesi için genellikle daha fazla enerji ve birden fazla lazere maruz kalma gerekir. Öte yandan, ince katmanların çıkarılması daha kolay olabilir ancak alt tabakaya zarar vermemek için hassas kontrol gerektirir.
- Fiziksel durum: Kirleticiler katı, sıvı veya gaz halinde olabilir. Pas veya boya gibi katı kirleticilerin giderilmesi genellikle sıvı veya buharlardan daha fazla enerji gerektirir. Fiziksel durum aynı zamanda lazer ile kirletici madde arasındaki etkileşimi de etkiler ve bu da temizleme işleminin verimliliğini etkiler.
- Alt tabaka yapışması: Kirletici madde ile alt tabaka arasındaki bağın gücü, giderilme kolaylığını etkiler. Gevşek bir şekilde yapışan kirletici maddeler daha düşük enerji yoğunluklarıyla giderilebilirken, güçlü bir şekilde bağlanan kirletici maddeler, bağı kırmak ve etkili bir temizlik elde etmek için daha yüksek enerji seviyeleri veya farklı lazer parametreleri gerektirebilir.
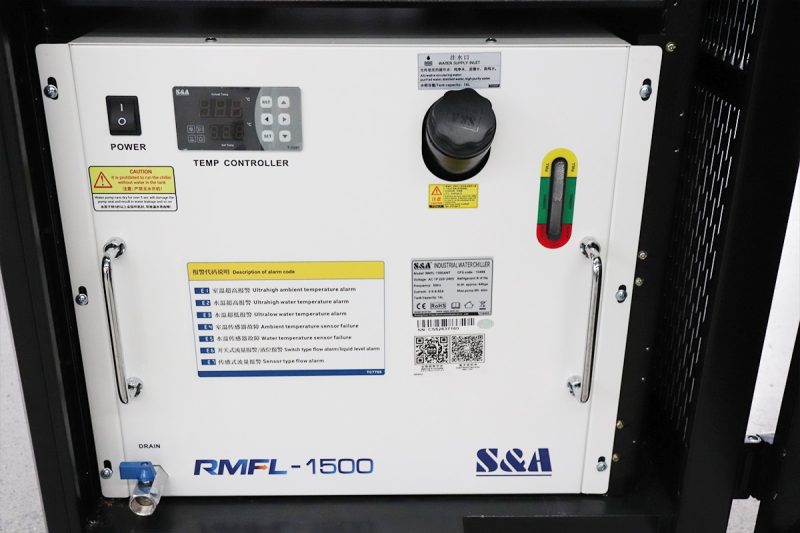
Yüzey Kirleticileri
Kirletici Bileşimi
Yüzey kirleticilerinin kimyasal bileşimi, bunların lazer enerjisiyle nasıl etkileşime gireceğini belirler. Farklı malzemelerin farklı soğurma özellikleri ve termal tepkileri vardır ve bu da lazer tarafından ne kadar etkili bir şekilde yok edildiklerini etkileyebilir.
- Organik Kirleticiler: Buna yağlar, gresler ve biyolojik kalıntılar dahildir. Organik malzemeler genellikle lazer enerjisini inorganik malzemelerden farklı şekilde emer. Örneğin hidrokarbonlar lazer ışınımı altında ayrışabilir veya buharlaşabilir, biyolojik kirleticiler ise kömürleşebilir veya buharlaşabilir. Mevcut spesifik organik bileşiklerin bilinmesi, uygun lazer dalga boyu ve parametrelerinin seçilmesine yardımcı olabilir.
- İnorganik Kirleticiler: Buna pas, oksitler ve mineral birikintileri dahildir. Daha yüksek erime noktaları ve termal stabiliteleri nedeniyle inorganik malzemeler, etkili bir şekilde uzaklaştırılması için genellikle daha yüksek enerji yoğunluklarına ihtiyaç duyar. Bu kirletici maddelerin bileşimi, etkili ablasyon sağlamak için dalga boyu ve enerji yoğunluğu gibi lazer parametrelerinin seçimini etkileyebilir.
- Karışık Kirleticiler: Yüzeyler genellikle organik ve inorganik kirleticilerin bir kombinasyonunu içerir. Bu gibi durumlarda, lazer parametrelerinin alt tabakaya zarar vermeden her tür kirletici maddeyi etkili bir şekilde ortadan kaldıracak şekilde ayarlandığı çok adımlı veya birleşik bir yaklaşım gerekli olabilir.
Kirletici Kalınlığı
Kirletici tabakanın kalınlığı lazer temizlemede kritik bir faktördür. Gerekli enerjiyi ve etkili uzaklaştırma stratejisini etkiler.
- İnce Katmanlar: Hafif toz veya ince oksit katmanları gibi ince kirletici katmanlar genellikle daha düşük enerji yoğunlukları ve daha az lazer geçişi ile giderilebilir. İnce katmanlarla ilgili zorluk, alt tabakayı hasara neden olabilecek lazer enerjisine aşırı maruz bırakmadan tamamen çıkarılmasını sağlamaktır.
- Kalın Katmanlar: Daha kalın kirletici katmanlar daha fazla enerji gerektirir ve tamamen ortadan kaldırılması için birden fazla lazer geçişi gerektirebilir. Kalın katmanlarla ilgili zorluk, her geçişte alt tabakanın aşırı ısınmadan veya zarar görmeden istenen miktarda malzemeyi uzaklaştırmasını sağlamaktır. Lazerin enerji yoğunluğunun ve tekrarlama oranının ayarlanması, daha kalın katmanlar için kaldırma işleminin yönetilmesine yardımcı olabilir.
Yapışma
Kirletici madde ile alt tabaka arasındaki yapışma, kirletici maddenin lazerle ne kadar kolay giderilebileceğini etkiler.
- Zayıf Yapışma: Gevşek toz veya yüzey kiri gibi yüzeye gevşek bir şekilde yapışan kirletici maddeler, daha düşük enerji yoğunluklarıyla nispeten kolay bir şekilde giderilebilir. Lazer enerjisi zayıf bağları kırarak kirletici maddenin ortaya çıkan duman tarafından uzaklaştırılmasına veya uçup gitmesine neden olur.
- Güçlü Yapış: İnatçı pas veya güçlü bir şekilde yapışan kaplamalar gibi güçlü bir şekilde yapışan kirletici maddeler, bağları kırmak ve kirletici maddeyi etkili bir şekilde ortadan kaldırmak için daha yüksek enerji yoğunlukları ve daha hassas lazer parametreleri gerektirir. Bazı durumlarda, tamamen çıkarılmadan önce yapışmayı zayıflatmak için ön işlem veya çok adımlı lazer temizleme işlemi gerekebilir.
Katman Bileşimi
Kirletici katmanların bileşimi ve yapısı büyük ölçüde değişiklik gösterebilir ve lazer-malzeme etkileşimini etkileyebilir.
- Homojen Katmanlar: Tek bir malzeme türünden oluşan homojen kirletici katmanlar genellikle lazerle temizliğe öngörülebilir şekilde yanıt verir. Tekdüzelik, verimli temizlik için lazer parametrelerinin daha basit bir şekilde optimize edilmesine olanak tanır.
- Heterojen Katmanlar: Gerçek dünya kirleticilerinin çoğu heterojendir ve farklı özelliklere sahip birden fazla malzemeden oluşur. Örneğin bir katman, organik yağ ve inorganik toz parçacıklarının bir karışımından oluşabilir. Farklı bileşenler lazer enerjisine farklı şekilde tepki verebileceğinden, bu katmanlar daha incelikli bir yaklaşım gerektirir. Lazer dalga boyunun, enerji yoğunluğunun ve darbe süresinin ayarlanması, bir katman içindeki farklı özelliklerin çözümlenmesine yardımcı olabilir.
- Çok Katmanlı Kirleticiler: Boya, pas ve kirin birleşimi gibi çok katmanlı kirleticiler daha karmaşık bir yaklaşım gerektirir. Her katman farklı emme özelliklerine, termal özelliklere ve yapışma mukavemetine sahip olabilir. Alt tabakaya zarar vermeden her katmanı etkili bir şekilde kaldırmak için lazer parametrelerini sırayla ayarlamak veya farklı dalga boyları kullanmak gerekebilir.
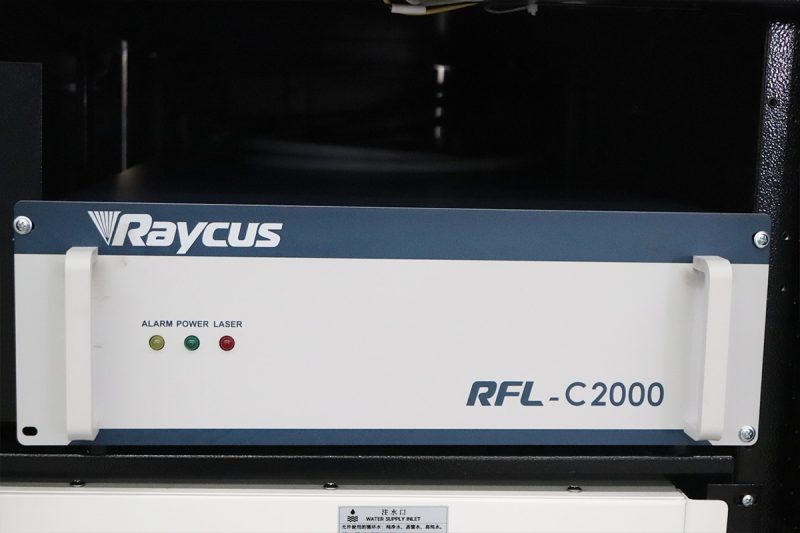
Çevre koşulları
Ortam sıcaklığı
Ortam sıcaklığı lazer temizlemede kritik bir rol oynar ve hem alt tabakaları hem de kirleticileri etkileyebilir.
- Substrat Tepkisi: Substratın sıcaklığı, termal iletkenlik ve özgül ısı gibi termal özelliklerini etkiler. Daha yüksek ortam sıcaklıkları, lazer temizleme işlemi sırasında alt tabakanın daha hızlı ısınmasına neden olur ve bu da termal hasar riskini artırabilir. Tersine, daha düşük ortam sıcaklıkları, alt tabakanın ısı oluşumuna karşı duyarlılığını azaltabilir, ancak aynı zamanda bazı malzemeleri daha kırılgan ve çatlamaya karşı daha duyarlı hale getirebilir.
- Lazer Verimliliği: Lazer sisteminin verimliliği ortam sıcaklığından etkilenebilir. Lazer bileşenleri, özellikle yüksek güçlü sistemlerde bulunanlar, sıcaklık değişimlerine karşı hassastır ve bu da performanslarını ve kararlılıklarını etkileyebilir. Sabit bir ortam sıcaklığının korunması, lazer çıkışının ve etkili temizliğin dengelenmesine yardımcı olur.
- Kirletici Davranışı: Lazer ışınlaması altındaki kirletici maddelerin davranışı da ortam sıcaklığına göre değişebilir. Örneğin, bazı kirletici maddeler yüksek sıcaklıklarda daha uçucu veya reaktif hale gelebilirken, diğerleri daha viskoz hale gelebilir veya alt tabakaya daha sıkı yapışabilir. Ortam sıcaklığının kontrol edilmesi, kirletici maddelerin öngörülebilir ve etkili bir şekilde giderilmesini sağlamaya yardımcı olur.
Nem
Ortamdaki nem düzeyi lazerle temizleme işlemini önemli ölçüde etkileyebilir.
- Yoğuşma ve emilim: Yüksek nem, özellikle alt tabaka çevredeki havadan daha soğuk olduğunda, alt tabaka yüzeyinde nemin yoğunlaşmasına neden olabilir. Bu nem tabakası, lazer enerjisinin emilimini etkileyebilir ve bu da kirletici giderme verimliliğini azaltabilir. Ayrıca emilen nem, kirletici maddelerin şişmesine veya özelliklerinin değişmesine neden olarak temizleme işlemini zorlaştırabilir.
- Statik yük: Düşük nem seviyeleri, alt tabaka ve kirletici maddeler üzerinde statik birikme riskini artırır. Statik yükler toz ve diğer havadaki parçacıkları çekerek temizlikten sonra yeniden kirlenmeye neden olur. Ayrıca lazer ışınına müdahale ederek eşit olmayan enerji dağıtımına ve tutarsız temizleme sonuçlarına neden olabilirler.
- Malzeme etkileşimi: Nem, lazer ile belirli malzemeler arasındaki etkileşimi değiştirebilir. Örneğin, organik kirleticiler nemi emebilir ve uzaklaştırılması daha zor hale gelebilir, inorganik kirleticiler ise hidratlar oluşturarak bunların ablasyon özelliklerini değiştirebilir. Optimum nem seviyelerini korumak, istikrarlı ve öngörülebilir temizlik sonuçları sağlar.
Hava kirleticileri
Ortamdaki hava kirleticileri lazerle temizleme işlemini olumsuz yönde etkileyebilir.
- Işın girişimi: Havada asılı parçacıklar, lazer ışınını malzeme yüzeyine ulaşmadan dağıtabilir veya emebilir. Bu girişim, lazerin enerji yoğunluğunu azaltarak temizleme etkinliğinin azalmasına ve tutarsız sonuçlara yol açar. Uygun bir hava filtreleme sistemiyle temiz bir çalışma ortamı sağlamak ışın girişimini en aza indirebilir.
- Optik: Havadaki kirletici maddeler, bir lazer sisteminin lensler ve aynalar gibi optik bileşenleri üzerinde birikerek bunların netliğini ve verimliliğini azaltabilir. Kirlenmiş optikler lazer ışınının kalitesini düşürebilir, bozulmalara neden olabilir ve temizleme işleminin genel verimliliğini azaltabilir. Bu tür sorunları önlemek için optiklerin düzenli bakımı ve temizliği gereklidir.
- İşyeri Güvenliği: Lazerle temizleme işlemi sırasında oluşan ablasyon parçacıkları, dumanlar ve gazlar gibi havadaki kirleticiler, operatörlerin sağlığı ve güvenliği açısından risk oluşturabilir. Bu kirletici maddelerin yakalanıp uzaklaştırılması ve böylece güvenli bir çalışma ortamının sağlanması için uygun havalandırma ve filtreleme sistemlerinin uygulanması çok önemlidir. Operatörleri maruziyetten korumak için maskeler ve gözlükler gibi kişisel koruyucu ekipmanlar (PPE) de kullanılmalıdır.
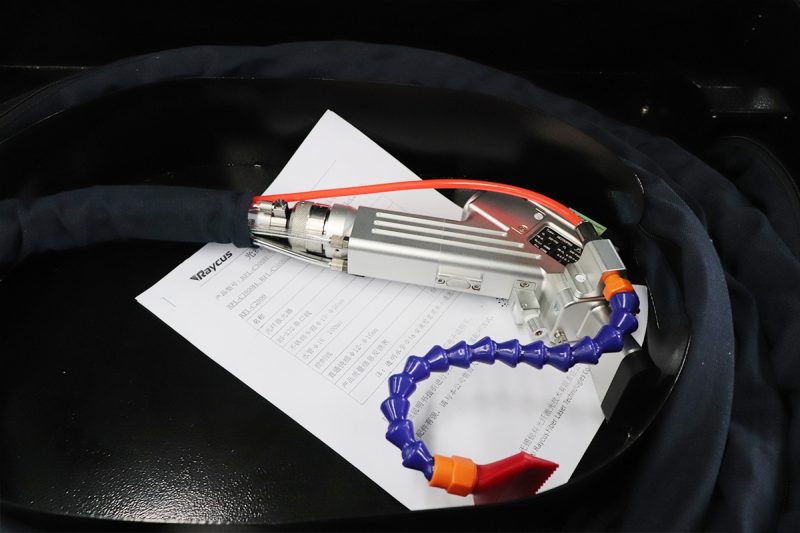
Operasyonel Hususlar
Tarama Hızı
Tarama hızı, lazer ışınının temizlenen yüzey boyunca hareket etme hızını ifade eder. Malzemenin lazer enerjisine maruz kalma süresini etkileyen önemli bir faktördür.
- Temizleme Verimliliğine Etkisi: Daha yüksek tarama hızları, herhangi bir alanda ısı oluşumunu sınırlandırarak termal hasar riskini azaltabilir. Ancak hız çok yüksekse, lazer her noktada kirletici maddeyi etkili bir şekilde ortadan kaldıracak kadar uzun süre kalamayabilir ve bu da temizliğin tamamlanmamasına neden olabilir.
- Denge ve Optimizasyon: Daha yavaş tarama hızları, daha uzun pozlamalara izin verir; bu da kirletici maddelerin uzaklaştırılmasını artırabilir, ancak aşırı ısınma ve potansiyel alt tabaka hasarı riskini de artırabilir. Optimum tarama hızının bulunması, etkili kirletici madde giderme ihtiyacı ile termal etki riskinin dengelenmesini gerektirir. Bu denge genellikle belirli malzeme ve kirletici özelliklerine göre deneysel olarak belirlenir.
Darbe Örtüşmesi
Ardışık lazer darbeleri arasındaki örtüşme derecesi, temizleme işleminin tekdüzeliğini ve eksiksizliğini etkiler.
- Tutarlı Enerji Dağıtımı: Uygun örtüşme, yüzeyin her alanının tutarlı lazer enerjisi almasını sağlar. Bu, eşit temizleme sonuçlarının elde edilmesine yardımcı olur; bu önemlidir, çünkü yetersiz örtüşme temizlenmemiş alanlar bırakabilir, aşırı örtüşme ise ısı birikiminin artmasına ve potansiyel hasara yol açabilir.
- Darbe Tekrarlama Hızı ve Tarama Hızı: Örtüşme, darbe tekrarlama oranından ve tarama hızından etkilenir. Daha yüksek tekrarlama oranları ve daha yavaş tarama hızları örtüşmeyi artırır, bu da temizlemenin daha kapsamlı olmasını sağlar, ancak aynı zamanda alt tabaka üzerindeki termal yükü de arttırır. Tersine, daha düşük tekrarlama oranları ve daha hızlı tarama hızları örtüşmeyi azaltır ve bu da tam bir temizlik elde etmek için birden fazla tarama gerektirebilir.
- Örtüşmenin Ayarlanması: Örtüşme derecesinin ayarlanması, darbe tekrarlama hızının, tarama hızının ve lazer enerjisinin dikkatli bir şekilde koordine edilmesini gerektirir. Amaç, termal hasara neden olmadan veya kirletici artıkları geride bırakmadan kapsamlı temizlik sağlamaktır.
Lazer-Yüzey Mesafesi
Lazer kaynağı ile malzeme yüzeyi arasındaki mesafe, aynı zamanda mesafe mesafesi olarak da bilinir, lazer temizlemede kritik bir faktördür.
- Odaklanma ve Enerji Yoğunluğu: Uzaklık mesafesi, lazer ışınının hedef yüzey üzerindeki odağını ve enerji yoğunluğunu etkiler. Optimum mesafenin korunması, lazer ışınının uygun şekilde odaklanmasını sağlar, kirletici maddelere enerji dağıtımını maksimuma çıkarır ve ablasyon verimliliğini artırır.
- Mesafe Değişimi: Uzak mesafe değişiklikleri tutarsız temizleme sonuçlarına yol açabilir. Mesafe çok büyükse lazer ışını odak dışı olabilir, bu da enerji yoğunluğunu ve temizleme etkinliğini azaltır. Mesafe çok kısaysa, enerjinin aşırı yoğunlaşması nedeniyle alt tabakaya zarar verme riski artar.
- Optimum Mesafeyi Korumak: Hassas konumlandırma sistemleri ve geri bildirim mekanizmalarının kullanılması, temizleme işlemi sırasında optimum mesafenin korunmasına yardımcı olabilir. Bu, eşit ve etkili temizlik için tutarlı odaklanma ve enerji dağıtımı sağlar.
Olay Açısı
Lazer ışınının yüzeye çarptığı açıya geliş açısı denir ve bu açı, temizleme işleminin emilimini ve etkinliğini önemli ölçüde etkileyebilir.
- Enerji Emilimi ve Yansıması: Geliş açısı, lazer enerjisinin yüzey tarafından emilimini ve yansımasını etkiler. Optimum geliş açısı, kirletici maddeler tarafından enerji emilimini maksimuma çıkarır ve bu da ablasyon sürecini geliştirir. Tipik olarak dik bir açı (90 derece) en etkili enerji dağıtımını sağlar.
- Yüzey Geometrisi: Temizlenen yüzeyin geometrisi, geliş açısının ayarlanmasını gerektirebilir. Örneğin karmaşık veya kavisli yüzeyler, tüm alanların etkili bir şekilde temizlenmesini sağlamak için farklı açılar gerektirebilir. Ayarlanabilir bir lazer kafası veya robotik sistem kullanmak, farklı yüzey geometrileri için en uygun açının korunmasına yardımcı olabilir.
- Yansıma Güvenliği: Geliş açısını yönetmenin aynı zamanda güvenlikle ilgili sonuçları da vardır. Açının doğru şekilde kontrol edilmesi, operatörler ve ekipman için tehlikeli olabilecek istenmeyen yansımaların en aza indirilmesine yardımcı olur. Koruyucu bariyerler ve kontrollü ortamlar gibi güvenlik önlemleri bu riskleri azaltabilir.

Özet
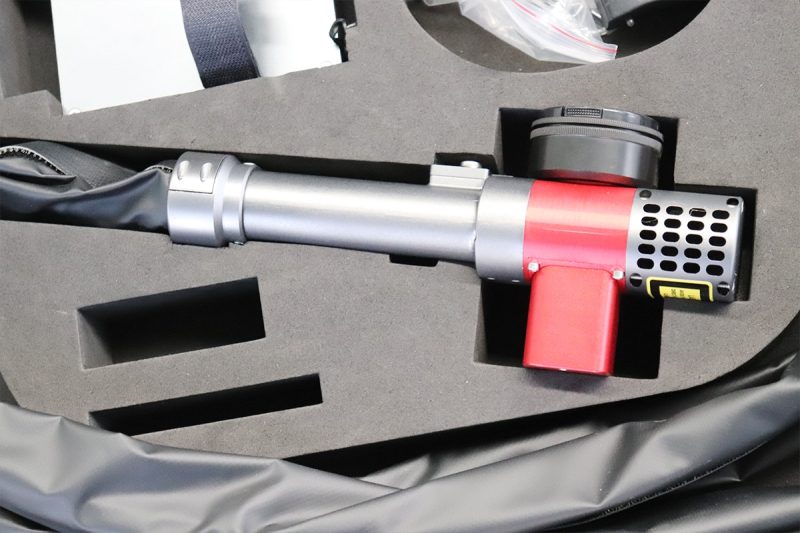
Lazer Temizleme Çözümlerini Alın
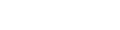
- [email protected]
- [email protected]
- +86-19963414011
- 3 Bölge A, Lunzhen Sanayi Bölgesi, Yucheng Şehri, Shandong Eyaleti.