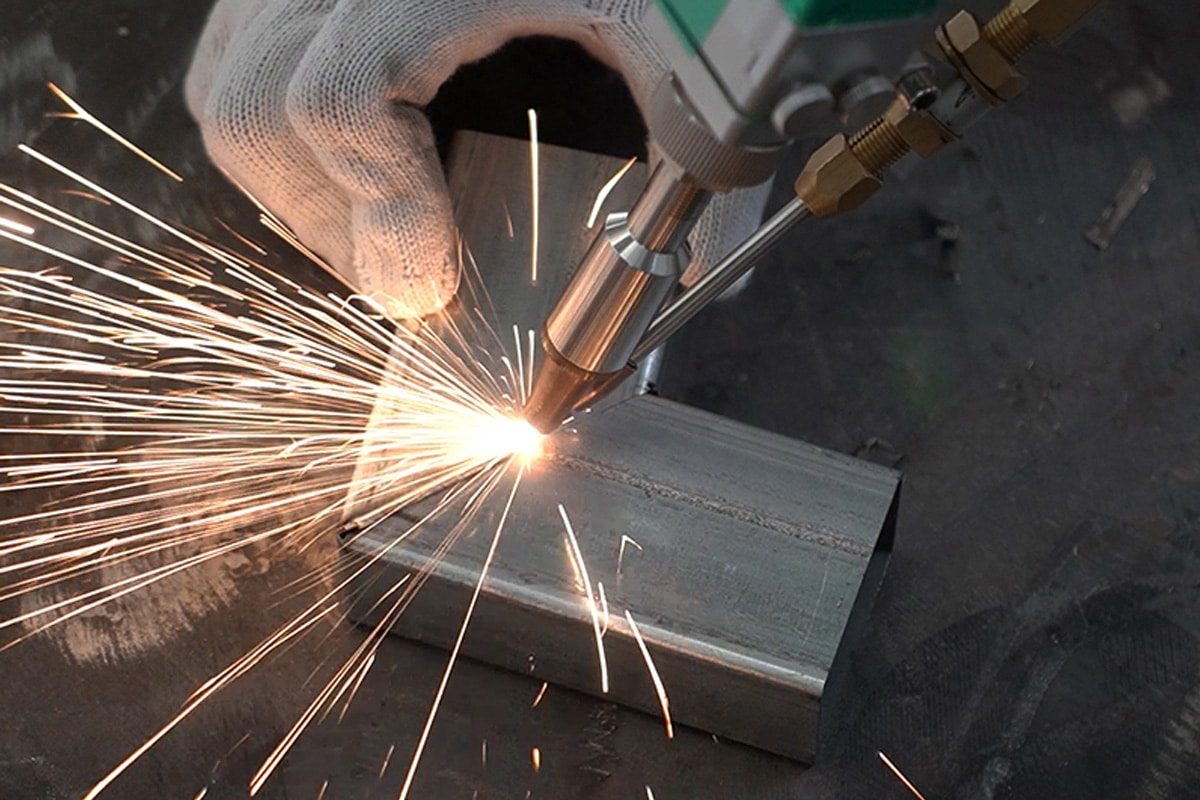
Verimli ve hassas bir kaynak teknolojisi olarak lazer kaynak, modern üretimde yaygın olarak kullanılmaktadır. Isı kaynağı olarak bir lazer ışını kullanır ve lazer jeneratörü, malzemeleri eritmek ve bağlamak için yüksek enerji yoğunluklu bir lazer ışını yayar. Geleneksel kaynak yöntemleriyle (gaz metal ark kaynağı (GMAW/MIG), gaz tungsten ark kaynağı (GTAW/TIG), korumalı metal ark kaynağı (SMAW) ve özlü ark kaynağı (FCAW)) karşılaştırıldığında, lazer kaynak, kaynak işleminin yüksek hassasiyeti ve yüksek verimliliği ve daha küçük bir ısıdan etkilenen bölge gibi birçok benzersiz avantaja sahiptir. Ancak, lazer kaynağının etkisi ve kalitesi, malzeme kalınlığının önemli bir faktör olduğu birçok faktörden etkilenir. Bu makale, malzeme kalınlığının lazer kaynak makinesi parametrelerini belirlemek ve farklı malzeme kalınlıkları için optimizasyon yöntemleri sunmak.
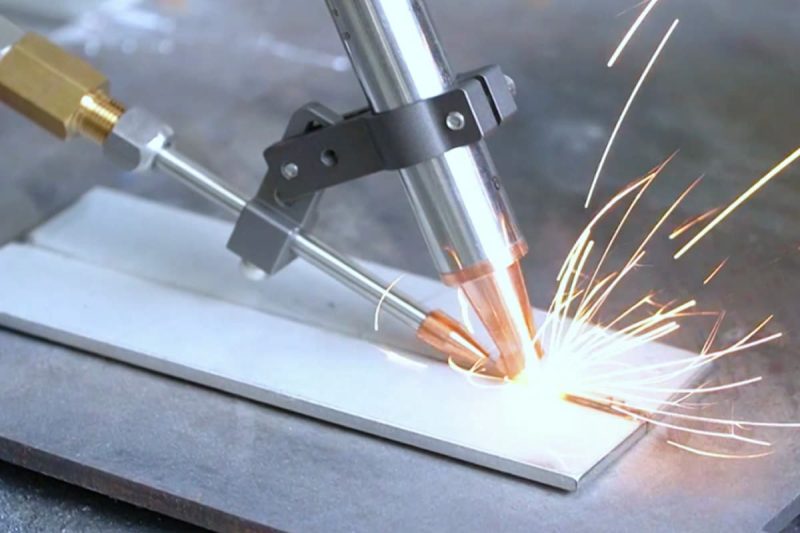
Lazer Kaynak Temelleri
Lazer Kaynak İşlemi Açıklaması
Lazer kaynak, metalleri veya diğer malzemeleri eritmek ve birbirine bağlamak için bir ısı kaynağı olarak lazer ışını kullanan bir kaynak işlemidir. İşlem aşağıdaki adımları içerir:
- Lazer ışınının odaklanması: Lazer jeneratörü tarafından yayılan lazer ışını, optik bir sistem aracılığıyla kaynak kafasına odaklanır.
- Malzemenin ısınması: Lazer ışınının yüksek enerji yoğunluğu, malzemeyi erime noktasına kadar ısıtır ve malzemenin lokal olarak erimesine veya buharlaşmasına neden olur.
- Erimiş havuz oluşumu: Erimiş malzeme bir erimiş havuz oluşturur ve lazer ışınının sürekli hareketi erimiş havuzun sıvı kalmasını sağlar.
- Katılaşma ve bağlantı: Lazer ışını hareket ettiğinde veya durduğunda, erimiş havuz soğur ve katılaşır ve kaynak işlemi tamamlanır.
Lazer kaynak yöntemleri iki türlüdür; ısıl iletim kaynağı ve anahtar deliği kaynağı.
- Isı iletim kaynağı: Lazer ışını, malzemenin yüzeyini malzemenin erime noktasının üzerine ısıtır, yalnızca kaynak yüzeyinde erime meydana getirir, iş parçasının içi tam olarak nüfuz etmez ve temelde buharlaşma meydana gelmez. Bu işlem esas olarak ince duvarlı malzemeleri kaynaklamak için kullanılır. Isı iletim kaynağı, pürüzsüz ve güzel kaynaklar üretir.
- Anahtar deliği kaynağı: Anahtar deliği kaynağında, lazer ışını malzemenin yüzeyini buharlaşma noktasına kadar ısıtır ve malzemeye nüfuz eder. Malzeme buharlaşarak küçük bir delik oluşturur. Buharla doldurulan delik, gelen ışın enerjisinin neredeyse tamamını emer. Delikteki denge sıcaklığı yaklaşık 2500℃'dir. Isı, deliğin etrafındaki metali eritmek için yüksek sıcaklıktaki deliğin dış duvarından aktarılır. Anahtar deliği, ışının ışınlaması altında malzemenin sürekli buharlaşmasıyla oluşan yüksek sıcaklıktaki buharla doldurulur. Lazer ışını sürekli olarak deliğe girer ve deliğin dışındaki malzeme sürekli olarak akar. Işın hareket ettikçe, delik her zaman kararlı bir akış halindedir. Yani, küçük delik ve delik duvarı etrafındaki erimiş metal, ışının hızında ileri doğru hareket eder. Erimiş metal, küçük deliğin hareketiyle kalan boşluğu doldurur ve daha sonra yoğunlaşarak bir kaynak oluşturur.
Lazer Kaynak Sistemlerinin Temel Bileşenleri
Lazer kaynak sisteminin temel bileşenleri şunlardır:
- Lazer jeneratörü: Lazer enerjisi üretir ve yayar. Yaygın lazer jeneratörleri arasında fiber lazer jeneratörleri, gaz lazer jeneratörleri vb. bulunur.
- Optik sistem: Lazer ışınını ayarlamak ve odaklamak için odaklayıcı mercekler ve aynalardan oluşur.
- Lazer iletim sistemi: Lazer ışınını lazer kaynağından kaynak noktasına ileten sistem.
- Kaynak kafası: Gerçek kaynak işlemi için lazer odaklama aynası, kolimatör aynası ve koruyucu gaz memesi içerir.
- Kontrol sistemi: Lazer gücü, kaynak hızı vb. gibi lazer kaynağının çeşitli parametrelerini kontrol etmek için kullanılır.
Lazer Kaynak Yöntemlerinin Geleneksel Kaynak Yöntemlerine Göre Avantajları
Kaynak Kalitesi
- Lazer kaynağının ısıdan etkilenen bölgesi küçüktür, çünkü lazer ışınının enerji yoğunluğu yüksektir, ısıtma süresi kısadır ve ısı kaybı küçüktür, bu nedenle malzemenin ısıdan etkilenen bölgesi küçüktür, bu da malzemenin deformasyonunu, çatlamasını, oksidasyonunu ve diğer sorunlarını azaltabilir.
- Lazer kaynağının kaynak derinliği-genişlik oranı yüksektir, çünkü lazer ışınının çapı küçüktür ve enerji yoğunlaşmıştır, bu nedenle derin ve dar bir kaynak oluşturabilir, bu da kaynağın mukavemetini ve sızdırmazlığını artırır.
- Lazer kaynağının kaynağı pürüzsüz ve güzeldir, çünkü lazer ışınının noktası sabittir ve kaynak pozisyonu ve parametreleri doğru bir şekilde kontrol edilebilir, böylece pürüzsüz ve güzel bir kaynak oluşturabilir, sonraki taşlama ve parlatma işlemlerini azaltabilir.
- Lazer kaynakta kaynak hataları daha azdır, çünkü lazer kaynakta elektrot, kaynak çubuğu ve koruyucu gaz gibi yardımcı malzemelerin kullanımı gerekmediğinden elektrot kirliliği, gözenekler, cüruf kalıntıları ve çatlaklar gibi kaynak hatalarının oluşması önlenebilir.
Kaynak Verimliliği
- Lazer kaynak, hızlı bir kaynak hızına sahiptir. Lazer ışınının enerji yoğunluğu yüksek ve ısıtma süresi kısa olduğundan, kaynak işlemi hızlı bir şekilde tamamlanabilir ve bu da üretim verimliliğini artırır.
- Lazer kaynak yüksek kaynak esnekliğine sahiptir. Lazer ışını temassız bir ısı kaynağı olduğundan, optik fiber, reflektör, robot vb. ile iletilebilir ve kontrol edilebilir, böylece çeşitli karmaşık kaynak pozisyonlarına ve şekillerine uyum sağlayabilir ve üretim esnekliğini artırabilir.
- Lazer kaynak, yüksek derecede kaynak otomasyonuna sahiptir. Lazer kaynak, bilgisayar veya CNC sistemi tarafından doğru bir şekilde kontrol edilebildiği ve ayarlanabildiği için, yüksek derecede otomasyon ve zeka elde edebilir, manuel müdahaleyi ve hataları azaltabilir.
Kaynak Uygulamaları
- Lazer kaynak, güçlü malzeme uyumluluğuna sahiptir, çünkü lazer kaynak ısı kaynağı temassız bir ısı kaynağıdır, bu sayede çeşitli metal veya metal olmayan malzemeleri kaynaklayabilir ve hatta farklı malzemelerin bağlantısını sağlamak için farklı malzeme türlerini kaynaklayabilir.
- Lazer kaynak, güçlü bir endüstri uyumluluğuna sahiptir, çünkü lazer kaynak ısı kaynağı, yüksek kaliteli, yüksek hızlı ve yüksek otomasyonlu kaynak elde edebilen verimli bir ısı kaynağıdır, bu nedenle havacılık, otomotiv, elektronik, tıbbi vb. gibi çeşitli üst düzey endüstrilere uygulanabilir.
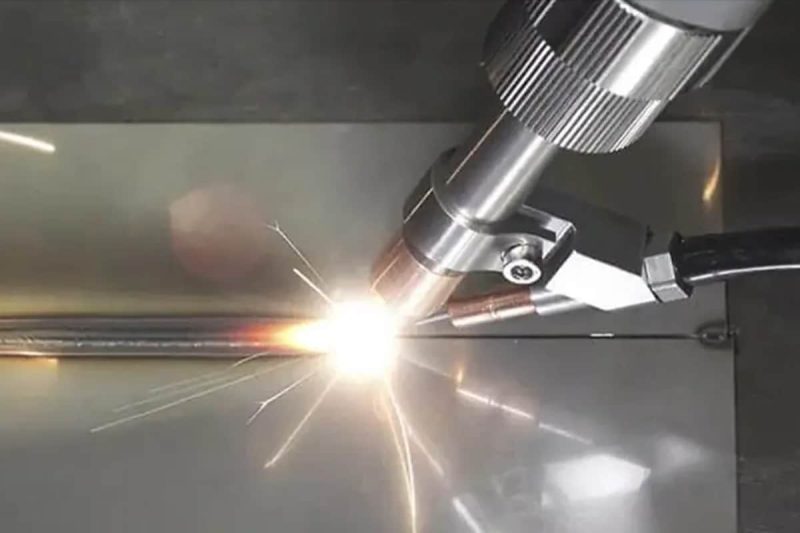
Malzeme Kalınlığının Kaynak Parametreleri Üzerindeki Etkisi
Lazer Gücü
Darbe Süresi ve Frekansı
Kaynak Hızı
Odak Konumu
Kiriş Çapı
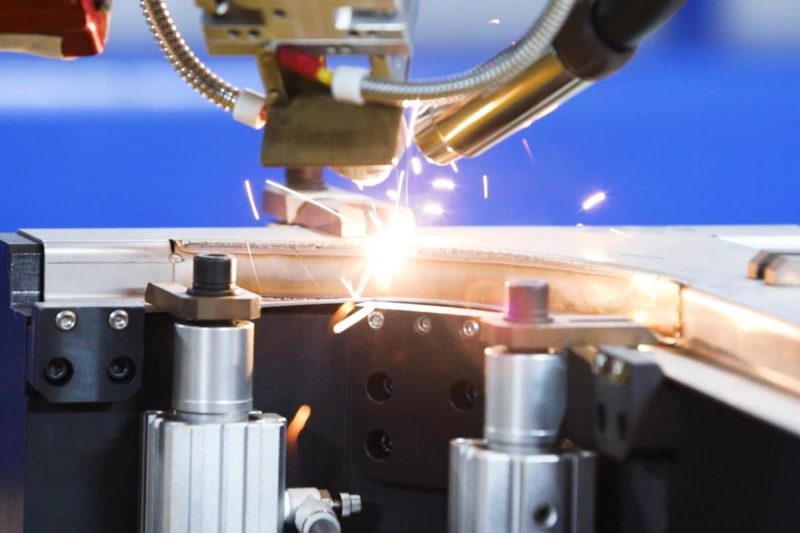
Farklı Malzeme Kalınlıkları İçin Lazer Kaynak Parametrelerinin Optimize Edilmesi
İnce Malzemeler (<1mm)
- Lazer gücü: Aşırı ısınmayı ve aşırı erimeyi önlemek için daha düşük bir lazer gücü seçilmelidir. Genellikle onlarca watt ile yüzlerce watt aralığında seçilir.
- Darbe süresi ve frekansı: Daha kısa darbe süresi ve daha yüksek frekans, hızlı ısıtma ve soğutma döngüleri sağlayarak termal etkileri azaltmaya yardımcı olur.
- Kaynak hızı: Üretim verimliliğini artırmak ve aşırı ısınmayı önlemek için daha yüksek kaynak hızları kullanılabilir.
- Odak konumu: En iyi kaynak efekti için lazer odak noktasının malzeme yüzeyine yakın ayarlanması gerekir.
- Kiriş çapı: Kaynaklamanın doğruluğunu ve detay kontrolünü artırmak için daha küçük bir kiriş çapı kullanın.
Orta Kalınlıktaki Malzemeler (1mm-5mm)
- Lazer gücü: Kaynak derinliği ve kalitesini garantilemek için orta düzeyde lazer gücü seçilmelidir. Genellikle birkaç yüz watt ile kilowatt aralığında seçilir.
- Darbe süresi ve frekansı: Isıtma ve soğutma etkilerini dengelemek için, belirli malzeme kalınlığına göre orta darbe süresi ve frekansını seçin.
- Kaynak hızı: Kaynak kalitesini ve üretim verimliliğini sağlamak için malzeme kalınlığına göre orta düzeyde kaynak hızı seçilmelidir.
- Odak konumu: Kaynak derinliği ve düzgünlüğünü sağlamak için lazer odağı malzemenin ortasına ayarlanmalıdır.
- Kiriş çapı: Enerji dağılımını ve kaynak doğruluğunu dengelemek için orta büyüklükte bir kiriş çapı seçin.
Kalın Malzeme (>5mm)
- Lazer gücü: Kaynak derinliği ve kalitesini garantilemek için yeterli ısı girişi sağlamak amacıyla daha yüksek bir lazer gücü seçilmelidir. Genellikle birkaç kilowatt aralığında seçilir.
- Darbe süresi ve frekansı: Daha uzun darbe süresi ve daha düşük frekans, daha kalın malzemeleri eritmek için daha yeterli ısı girdisi sağlayabilir.
- Kaynak hızı: Lazer ışınının malzemeye etkili bir şekilde nüfuz edebilmesini ve onu eritebilmesini sağlamak için daha yavaş bir kaynak hızı seçilmelidir.
- Odak konumu: Lazer ışınının malzemeye etkili bir şekilde nüfuz edebilmesi ve onu eritebilmesi için lazer odak noktasının malzemenin içine ayarlanması gerekir.
- Kiriş çapı: Yeterli enerji yoğunluğu ve kaynak derinliği sağlamak için daha büyük bir kiriş çapı kullanın.
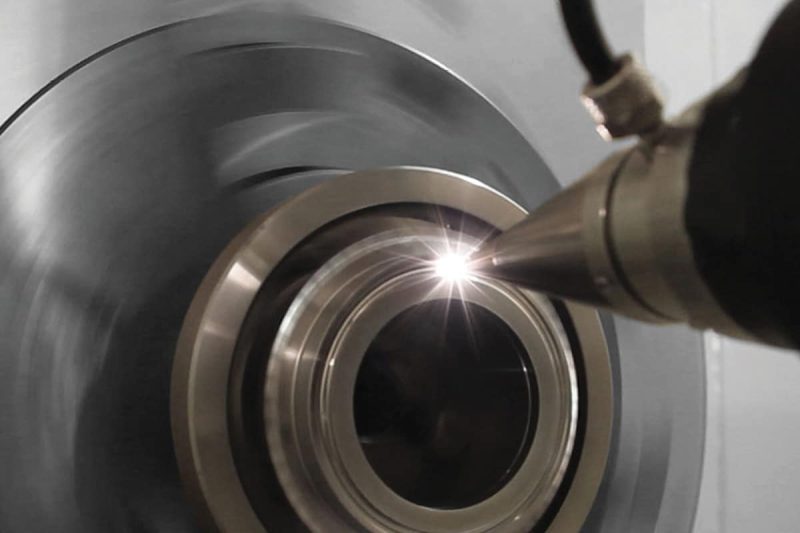
özetle

Lazer Çözümleri Alın
Doğru lazer kaynak makinesini seçmek güç tüketimini optimize etmeye ve yüksek operasyonel verimlilik elde etmeye yardımcı olabilir. Güvenilir bir tedarikçiyle çalışmak, gelişmiş teknolojiye, özel tavsiyeye ve sürekli desteğe erişimi garanti eder. AccTek Laser'da, çeşitli endüstriyel ihtiyaçları karşılamak üzere tasarlanmış kapsamlı bir lazer kaynak ekipmanı yelpazesi sunuyoruz. Uzmanlarımız, malzeme türü, kalınlık ve üretim hacmi gibi faktörleri göz önünde bulundurarak en enerji verimli modeli ve yapılandırmayı seçmenize yardımcı olabilir. Ayrıca, performansı en üst düzeye çıkarmak ve enerji kullanımını en aza indirmek için yüksek verimli lazer jeneratörleri, akıllı soğutma sistemleri ve enerji yönetim yazılımı gibi son teknoloji özellikler sunuyoruz. Ayrıca, ekibimiz ekipmanınızı en yüksek verimlilikte tutmak için düzenli bakım hizmetleri ve teknik destek sağlar. Bizimle ortaklık kurarak önemli enerji tasarrufları elde edebilir, işletme maliyetlerini düşürebilir ve sürdürülebilirlik çabalarınızı geliştirebilirsiniz. Herhangi bir sorunuz varsa lütfen zamanında bizimle iletişime geçin, AccTek Laser her müşteriye mükemmel lazer çözümleri sunmaya kendini adamıştır!
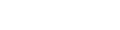
- [email protected]
- [email protected]
- +86-19963414011
- 3 Bölge A, Lunzhen Sanayi Bölgesi, Yucheng Şehri, Shandong Eyaleti.