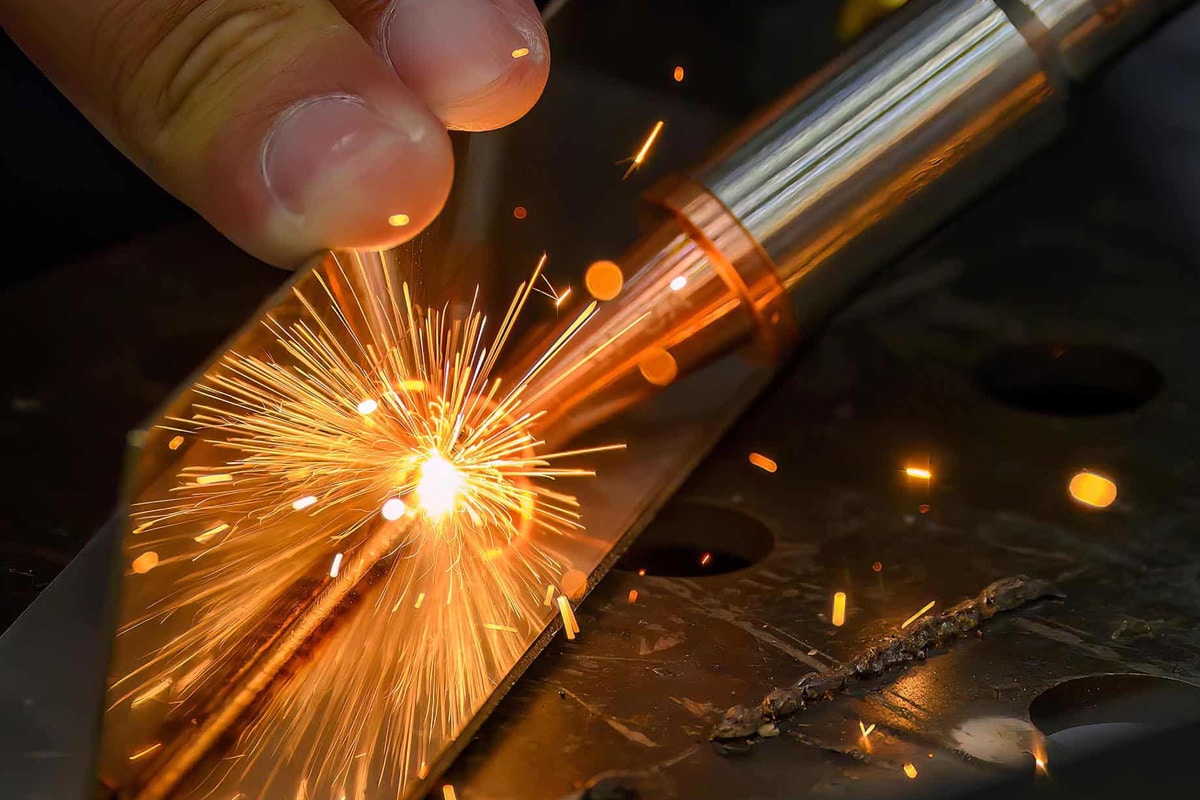
What Are the Challenges of Laser Welding Thin Materials?
Modern imalatta, lazer kaynak makineleri are widely used in automobiles, aerospace, electronic equipment, and medical devices due to their high precision, high efficiency, and non-contact processing. However, there are still many challenges when welding thin materials (usually metal sheets with a thickness of less than 2mm), requiring precise control and optimization strategies to ensure welding quality.
İçindekiler
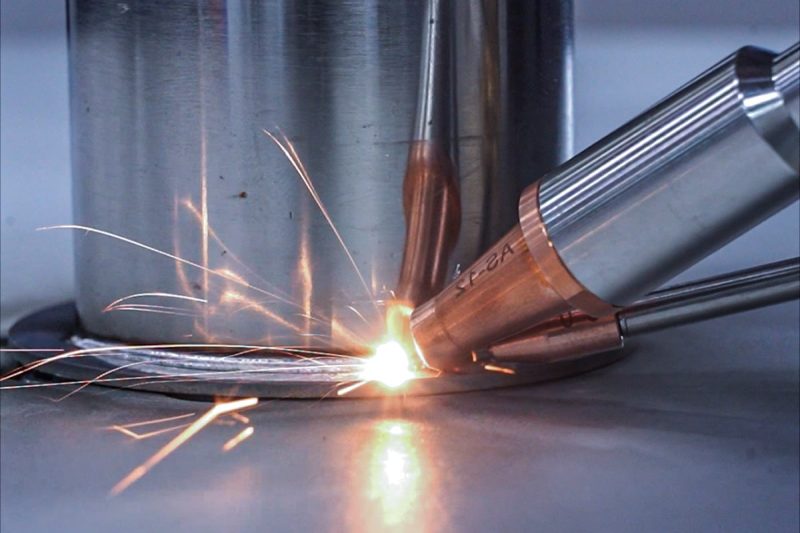
Understand laser welding of thin materials
Laser welding is an advanced process that uses a high-energy-density laser beam to melt metal materials and realize welding. Compared with traditional fusion welding methods, such as TIG welding and MIG welding, laser welding has significant advantages in processing thin materials. Its biggest feature is that its energy is highly concentrated, and the beam can be focused into an extremely small spot, allowing the metal to melt and cool quickly in a short time, thus forming a high-quality weld. This non-contact processing method not only reduces mechanical damage to the surface of the workpiece but also avoids possible electrode contamination problems during traditional welding. Since laser welding can accurately control power, welding speed, and focus position, it can be well adapted to thin plate welding of different thicknesses and materials, especially suitable for application scenarios with high precision requirements.
During this material welding, excessive heat input may cause the material to burn through, warp, or deformation, while laser welding can effectively control the heat input, and its high energy density can be completed in a very short time, minimizing heat diffusion, thereby significantly reducing the heat-affected zone (HAZ), reducing material deformation, and improving welding quality. At the same time, the welding speed of laser welding is much higher than that of traditional methods. In industrial production, the welding speed can reach several meters per minute, greatly improving production efficiency, reducing the heating time of the material, further reducing the influence of heat, and making the weld more smooth and uniform. In addition, since laser welding does not require additional welding wire or filler materials, high-strength and high-density welding can be directly realized in many application scenarios, reducing welding defects such as pores and cracks, and improving the stability and durability of the welding structure.
Thanks to these advantages, laser welding has been widely used in many industries, such as micro metal parts welding in the electronics industry, lightweight metal structure welding in automobile manufacturing, high-precision titanium alloy thin plate welding in the aerospace field, stainless steel catheters and implantable equipment welding in medical equipment manufacturing, etc. For these manufacturing fields that require high precision, low deformation, and high efficiency, laser welding is undoubtedly an ideal solution. With the continuous advancement of laser technology and the wide application of automation systems, the application prospects of laser welding in thin material processing will be broader.
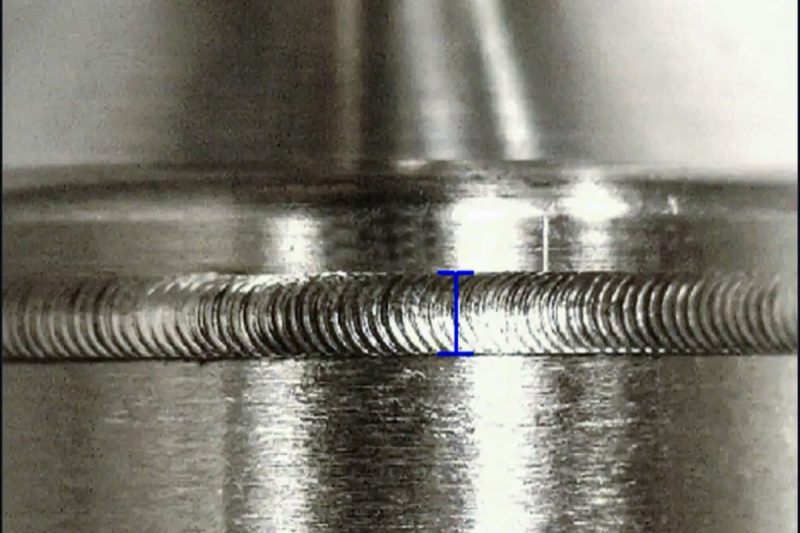
The importance of welding thin materials
Thin materials play a crucial role in the field of precision manufacturing and are widely used in the following industries:
Automobile manufacturing
- Lightweight body structure: By using thin materials, the overall weight of the body can be reduced, thereby improving fuel efficiency and reducing emissions. This not only conforms to environmental protection trends but also helps improve the economy of the vehicle.
- Improve vehicle performance: Thin materials not only reduce weight, but also improve the rigidity and safety of the vehicle body, reduce damage during collisions, and improve the overall performance of the vehicle.
- Reduce production costs: Thin material welding can reduce process complexity, reduce material waste, thereby reducing production costs and improving production efficiency.
Elektronik Sanayi
- Battery Assembly Manufacturing: In electric vehicles and consumer electronics, thin materials are often used in the manufacturing of battery housings and battery assembly. The structural stability and durability of the battery can be ensured through thin-material welding.
- Precision connector: The application of thin materials in electronic connectors can realize smaller connectors and high-density electronic component layouts, meeting the needs of miniaturization and functional integration of modern electronic devices.
- Microcircuit board manufacturing: The application of thin materials allows circuit boards to achieve a more compact design on the basis of ensuring strength and function, and promotes the rapid development of high-end electronic products such as smartphones and tablets.
Medical devices
- Stainless steel implants: Thin material welding is widely used in the medical field, especially in the production of paslanmaz çelik implants. Thin materials can improve the adaptability and biocompatibility of the implant and ensure the patient’s recovery after surgery.
- Micro-surgical instruments: In surgical procedures, micro-surgical instruments require higher accuracy and strength. Thin materials can meet this demand while ensuring the lightness of the instrument.
- Medical catheters and sensors: Thin materials can be used to manufacture medical catheters, sensors, and other equipment. The high-precision welding of these equipment helps to improve the performance and reliability of medical instruments and ensure patient safety.
The welding of thin materials not only solves problems such as weight and space limitations but also greatly improves the performance and functions of the product. As the demand for thin materials continues to increase, the precision and efficiency of welding technology are also continuing to improve, promoting the development of technologies in various industries.
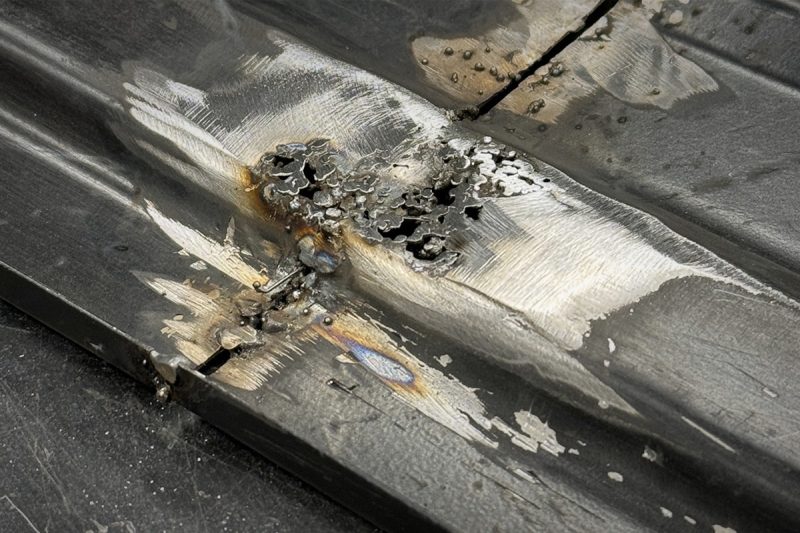
Challenges of laser welding thin materials
Laser welding thin materials face many challenges in the manufacturing process, especially due to the high thermal conductivity and low melting point of the thin materials, it is necessary to be more precise and controlled during the welding process. Here are some common challenges:
Heat-affected zone (HAZ) control
Thin materials are easily affected by excessive heat input during laser welding, resulting in too large a heat-affected zone (HAZ). Excessive heat input can cause the material surface to be overburned, warped, and even holes, which will affect the quality of the weld. Because the thickness of the thin material is small, once the heat is too concentrated, it is easy to cause deformation in the welding area, affecting the stability of the overall structure. Therefore, controlling the heat input, accurately adjusting the laser power and welding speed, and ensuring that the heat-affected zone is controlled within the minimum range, is an important issue when welding thin materials.
Welding strength and integrity
The load-bearing capacity of welded joints of thin materials is relatively low. Too narrow or insufficient weld penetration may lead to insufficient strength, affecting the structural stability of the final product. If the energy control during welding is improper, it is easy to cause defects in the welding joint, such as cold cracks, pores, etc., which will affect the welding quality. The strength and integrity of the welds are directly related to the performance and service life of the product, so ensuring welding quality meets standards and requirements is a key challenge in welding thin materials.
Precise control and monitoring
Laser welding requires highly accurate energy control to avoid uneven melting depth or weld defects. During the welding process, the dynamic changes of the molten pool are difficult to predict, and many factors such as temperature, speed, and laser power may affect the quality of the weld. Due to the extremely high welding accuracy requirements of thin materials, any small changes may have a significant impact on the welding effect. Therefore, accurate monitoring and control systems become crucial, and welding parameters can be adjusted in real-time to ensure uniform melt pool temperature and weld quality meet standards.
Joint design and assembly
Thin material welding requires higher accuracy for joint design and assembly. Excessive gaps may cause unstable welds, while over-tight joints may affect welding uniformity. Due to the poor flexibility of thin materials, the alignment and coordination of joints during welding is particularly important. If designed or assembled improperly, it will lead to uneven welds and even failure of welding. Therefore, before welding, strict control of the design and assembly accuracy of the welded parts is required to ensure the smooth progress of the welding process.
Material selection
Different metal materials have different absorption rates on lasers, which directly affects welding efficiency and quality. For example, the high reflectivity of alüminyum may lead to a large loss of laser energy, affecting welding efficiency, and are prone to uneven heating problems; materials such as stainless steel may deform during the welding process due to their high thermal expansion coefficient. In addition, the differences in thermal conductivity, melting point, and other attributes of different materials will affect the stability and results of the welding process. Therefore, it is crucial to choose the right material and optimize welding parameters.
The challenges of laser welding thin materials are mainly focused on thermal management, welding strength, precise control, design and assembly, and material selection. To solve these problems, it is necessary to finely regulate the laser welding process and make reasonable adjustments in design, material selection, etc. By continuously optimizing laser welding parameters, improving welding technology, and adopting advanced monitoring systems, these challenges can be effectively overcome and ensure the quality and reliability of thin material welding.
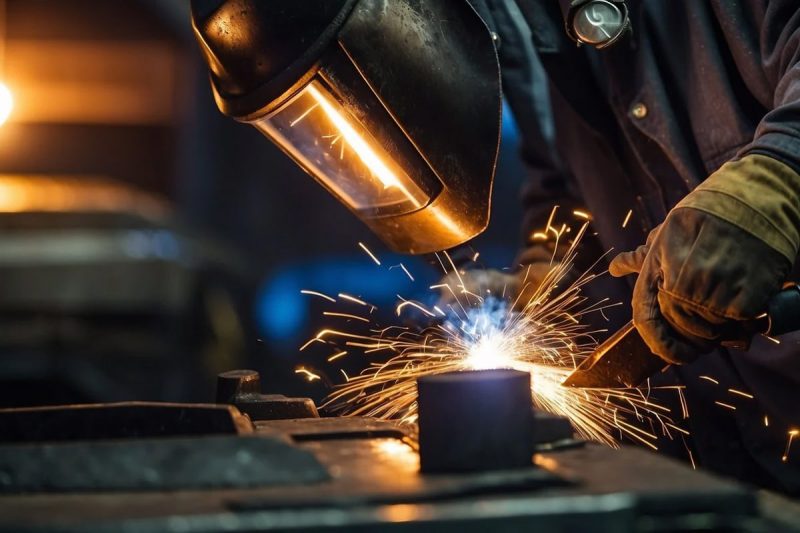
Strategies to overcome challenges
In the process of laser welding thin materials, we face many technical and technological challenges. To ensure welding quality and structural stability, it is crucial to adopt effective strategies to optimize the welding process and reduce problems in thin-material welding. Here are several common strategies to overcome the challenges of welding thin materials:
Lazer parametrelerini optimize edin
Choosing the appropriate laser power and welding parameters is the basis for ensuring the successful welding of thin materials. Optimizing laser parameters, can effectively reduce heat input and reduce thermal damage in welding:
- Selecting the right laser power: By selecting the appropriate laser power, the heat input can be effectively reduced and the risk of overburning and burning through can be reduced. Lower laser power can avoid excessive thermal effects on thin materials.
- Short-pulse laser or high-frequency pulse modulation: Short-pulse laser can accurately control the stability of the melt pool, avoid long-term heat input, and reduce the risk of thin material deformation. High-frequency pulse modulation can make the laser energy more uniform and further control the state of the melt pool.
- Adjusting welding speed: Adjusting welding speed is very critical. Too fast may lead to too narrow welds, and too slow may lead to too wide welds, which will affect the welding quality and material stability.
Innovative welding technology
The adoption of new welding technology can greatly improve thermal management and joint strength during welding:
- Dual-beam or swing welding technology: This technology helps to evenly distribute heat, reduces local heat impact, improves weld quality, and reduces material deformation by using two beams or swinging the laser beam during welding.
- Pulse welding instead of continuous welding: Pulse welding can control heat input and avoid excessive temperature peaks. It is especially suitable for welding thin materials and reducing the impact of thermal shock on thin materials.
- Laser brazing technology: Compared with traditional laser welding, laser brazing can reduce the size of the melting zone, thereby reducing the heat-affected zone and improving the strength and overall performance of the joint.
Advanced monitoring and quality assurance
During the laser welding of thin materials, real-time monitoring and quality assurance systems are important guarantees to ensure welding quality:
- Real-time optical monitoring system: By monitoring the status of the melt pool in real time, weld parameters can be dynamically adjusted to ensure uniform temperature of the melt pool and prevent weld defects such as pores and cracks.
- Machine vision detection technology: Use machine vision system to automatically identify welding defects, such as cracks, air holes, etc., promptly discover and correct problems, and ensure the consistency and stability of welding quality.
- Thermal Imaging System: Thermal Imaging technology can help optimize the welding process, provide real-time temperature monitoring, ensuring that the temperature during the welding process is controlled within the appropriate range, thereby improving welding consistency and reliability.
Material pretreatment and surface treatment
Cleaning and handling of material surfaces plays a crucial role in the welding quality of thin materials:
- Clean welding surface: Remove impurities such as oil stains, oxide layers, etc., which can effectively improve laser absorption, thereby improving welding efficiency and reducing welding defects. Surface cleaning is also an important step to improve the strength of welded joints.
- Apply laser preheating or post-treatment: Laser preheating can reduce thermal shock to thin materials, avoid rapid temperature changes during welding, reduce stress concentration, and prevent deformation. Post-treatment helps reduce residual stress and improve weld strength.
- Use of filler materials: Using filler materials (such as welding wire) during welding can enhance the strength of the joint, especially when welding thinner materials, which can improve the reliability and load-bearing capacity of the welded joint.
Thin materials laser welding faces a series of challenges such as heat-affected zones, welding strength, and precise control. To overcome these problems, it is crucial to adopt optimized laser parameters, innovative welding techniques, advanced monitoring and quality assurance methods, and appropriate material pretreatment and surface treatment strategies. By combining these strategies, the accuracy, stability, and strength of thin material welding can be effectively improved, ensuring that the quality of the final product meets high standards. With the continuous advancement of technology, the challenge of thin material welding will be better solved, providing more reliable welding solutions for various industries.
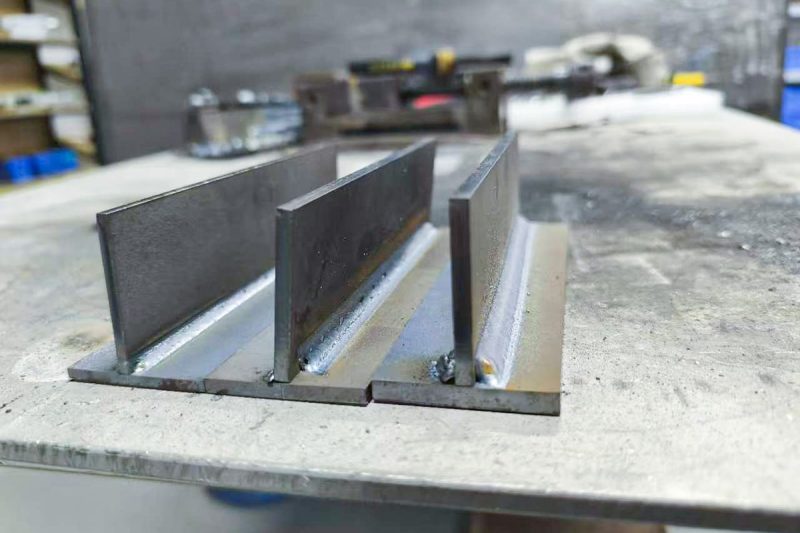
özetle
Laser welding thin materials are a precision process that requires comprehensive consideration of heat input control, welding strength, monitoring technology and material characteristics. By optimizing laser parameters, adopting innovative welding methods, and introducing intelligent monitoring systems, manufacturers can overcome welding challenges and improve welding quality and production efficiency.
AccTek Lazer focuses on the research and development of laser welding technology, providing high-performance laser welding equipment to help you with precision manufacturing needs! For more information, please bize Ulaşın! To obtain more technical support or customized solutions, please leave a message or send a private message!
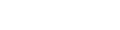
İletişim bilgileri
- [email protected]
- [email protected]
- +86-19963414011
- 3 Bölge A, Lunzhen Sanayi Bölgesi, Yucheng Şehri, Shandong Eyaleti.
Lazer Çözümleri Alın