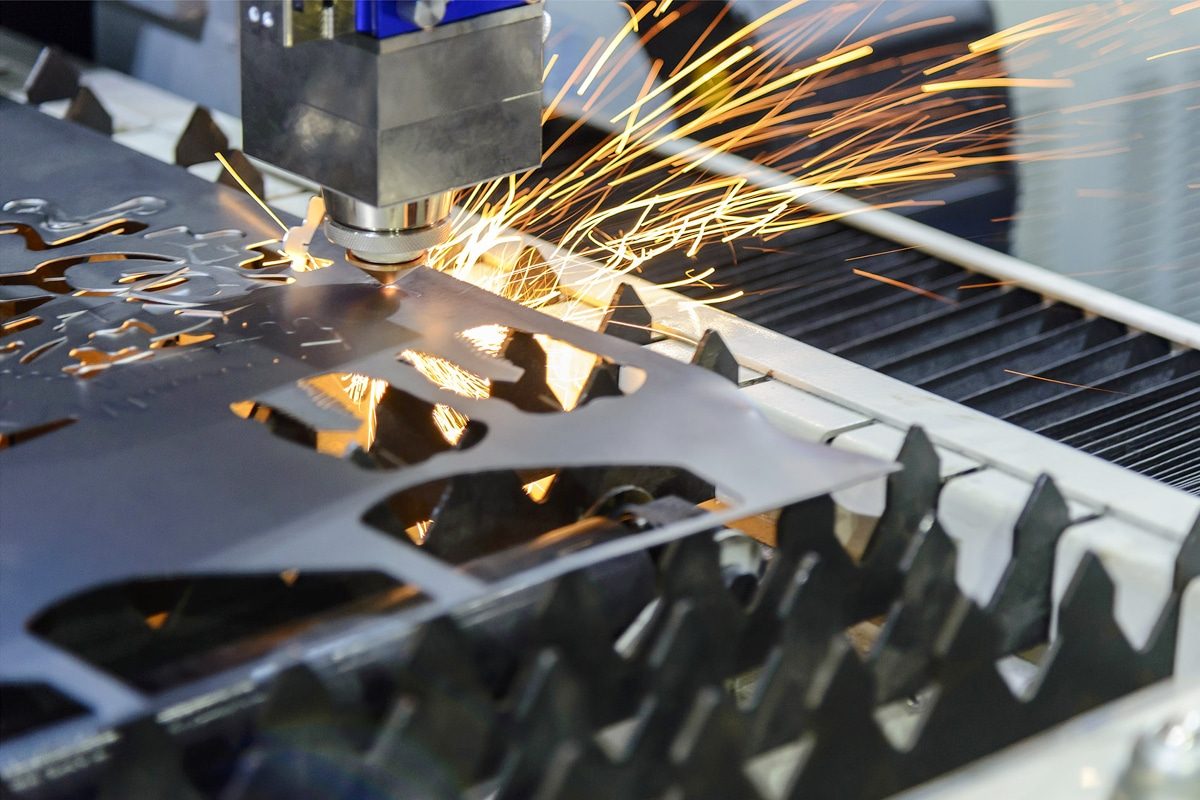
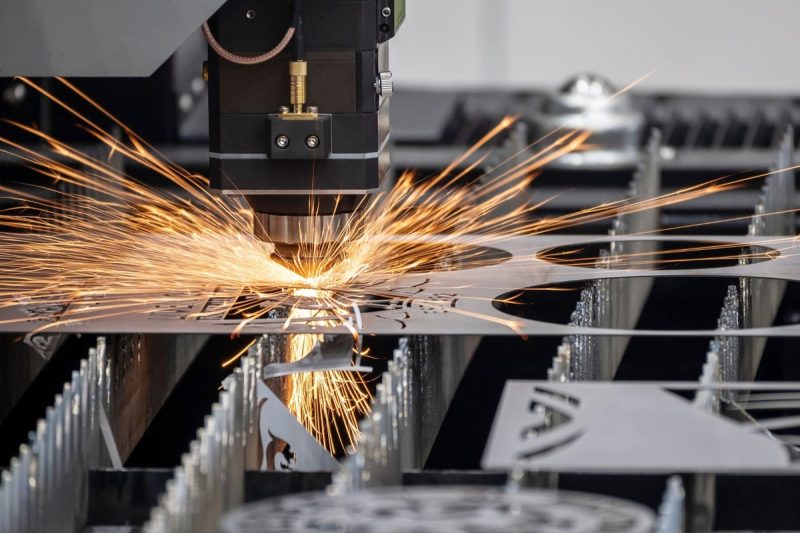
Lazer Kesim Hakkında Bilgi Edinin
Lazer Kesim Açıklaması
Kesim Uygulamalarında Kullanılan Lazer Çeşitleri
Fiber Lazer
CO2 Lazer
Lazer Kesim Sisteminin Bileşenleri
Tipik lazer kesim sistemi hassas ve verimli kesme performansı sağlamak için birlikte çalışan birkaç temel bileşenden oluşur:
- Lazer Kaynağı: Lazer ışınını üreten temel bileşendir. Uygulamaya bağlı olarak lazer kaynağı bir fiber lazer jeneratörü, bir CO2 lazer jeneratörü veya başka tipte bir lazer jeneratörü olabilir.
- Optik: Lazer ışınını kesilen malzemeye yönlendirmek ve odaklamak için aynalar ve mercekler kullanılır. Optiklerin kalitesi kesme işleminin doğruluğunu ve verimliliğini etkiler.
- Kesme Kafası: Kesme kafasında, içinden lazer ışınının ve yardımcı gazın yönlendirildiği odaklama merceği ve nozül bulunur. Doğru odak uzaklığının korunmasından ve optimum kesme koşullarının sağlanmasından sorumludur.
- Çalışma Tezgahı: Kesilen malzemeyi destekler ve genellikle malzemeyi kesme kafasının altına hareket ettiren bir mekanizma içerir.
- CNC Kontrol Cihazı: CNC kontrol cihazı, istenen şekil ve deseni üretmek için programlanan kesme yolunu takip ederek lazer kesme kafasının ve iş parçasının hareketini yönetir.
- Yardımcı Gaz Kaynağı: Yardımcı gaz, erimiş malzemeyi üfleyerek, kesme bölgesini soğutarak ve oksidasyonu önleyerek kesme işlemine yardımcı olur. Yaygın yardımcı gazlar arasında oksijen, nitrojen ve basınçlı hava bulunur.
- Egzoz Sistemi: Temiz bir çalışma ortamı sağlamak ve optikleri ve lazer bileşenlerini korumak için kesme işlemi sırasında oluşan dumanı ve kalıntıları giderir.
- Soğutma Sistemi: Lazer kesim, lazer kaynağına ve diğer bileşenlere zarar gelmesini önlemek için dağıtılması gereken çok fazla ısı üretir. Optimum çalışma sıcaklıklarını korumak için su soğutucuları gibi soğutma sistemleri kullanılır.
Lazer Kesim Performansını Etkileyen Temel Parametreler
Lazer kesim işleminin performansını ve kalitesini çeşitli parametreler etkileyebilir. Bu parametreleri anlamak ve optimize etmek istenen sonuçların elde edilmesine yardımcı olabilir:
- Lazer Gücü: Lazer kaynağının güç çıkışı, kesilebilecek malzemenin kalınlığını ve türünü belirler. Daha yüksek güçler, daha kalın malzemelerin kesilmesine olanak tanır, ancak kesim kalitesini korumak için diğer parametrelerin ayarlanması gerekebilir.
- Kesme Hızı: Kesme kafasının iş parçası boyunca hareket etme hızı. Optimum kesme hızı, üretkenlik ve kesim kalitesi arasında denge sağlar. Çok yüksek bir hız, eksik kesimlere yol açabilirken, çok düşük bir hız, aşırı ısı oluşumuna ve maddi hasara neden olabilir.
- Odak Konumu: Lazer ışınının odak noktasının malzeme yüzeyine göre konumu. Doğru odaklanma, kesme noktasında maksimum enerji yoğunluğunu sağlayarak temiz ve hassas kesimler sağlar. Yanlış hizalama, kesim kalitesinin düşmesine ve verimliliğin azalmasına neden olabilir.
- Yardımcı Gaz Tipi ve Basıncı: Kullanılan yardımcı gazın (oksijen, nitrojen veya basınçlı hava) türü ve basıncı, kesme işlemi üzerinde önemli bir etkiye sahiptir. Doğru gaz seçimi ve basıncı, erimiş malzemenin uzaklaştırılmasını optimize eder, oksidasyonu önler ve kesim kalitesini artırır.
- Malzeme Türü ve Kalınlığı: Farklı malzemeler ve kalınlıklar lazer kesime farklı tepki verir. Kesme parametrelerini ayarlarken yansıtma, termal iletkenlik ve erime noktası gibi malzeme özellikleri dikkate alınmalıdır.
- Işın Kalitesi: Odak ve mod yapısıyla karakterize edilen lazer ışınının kalitesi, kesimin hassasiyetini ve kalitesini etkiler. Küçük odak noktası boyutuna sahip yüksek kaliteli ışın, minimum kesim genişliğinde daha ince kesimler üretir.
- Nozul Tasarımı: Nozulun çapı ve şekli de dahil olmak üzere tasarımı, yardımcı gaz akışını ve erimiş malzemenin uzaklaştırılmasını etkiler. Optimize edilmiş nozul tasarımı, kesme verimliliğini ve kalitesini artırır.
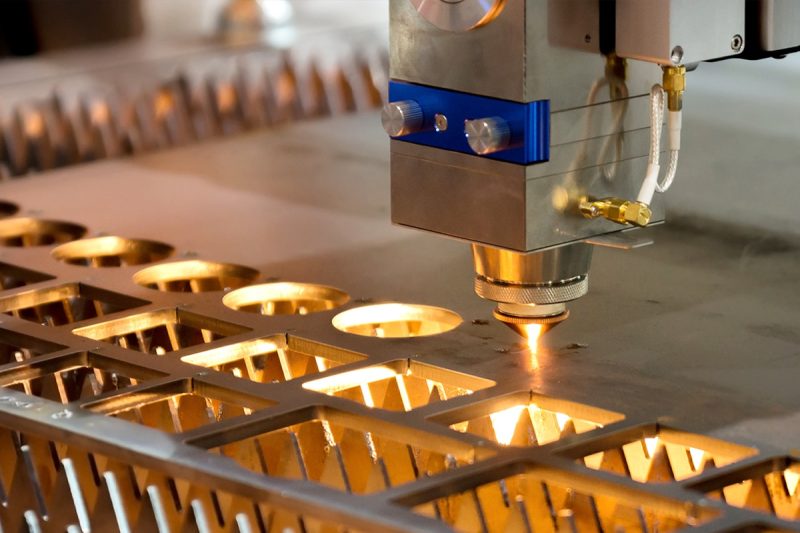
Lazer Kesimde Yardımcı Gazların Rolü
Erimiş Malzemenin Çıkarılması
Lazer kesim işlemi sırasında yüksek yoğunluklu bir lazer ışını, malzemeyi kesim noktasında eritir. Yardımcı gaz, bir nozül aracılığıyla kesme alanına yönlendirilir ve burada erimiş malzemenin çentikten (lazer tarafından oluşturulan boşluk) çıkarılmasına yardımcı olur. Erimiş malzemenin etkili bir şekilde çıkarılması kesim kalitesini korur ve kusurları önler.
- Verimli Püskürtme: Yardımcı gazın yüksek basıncı erimiş malzemeyi çentikten uzaklaştırarak iş parçası üzerinde yeniden katılaşmasını önler ve temiz bir kesim sağlar.
- Cüruf Oluşumunun Önlenmesi: Yardımcı gaz, erimiş malzemeyi hızlı bir şekilde tahliye ederek cüruf oluşumunu (kesiğin alt yüzeyine yapışan artık malzeme) en aza indirir ve son işlem ihtiyacını azaltır.
- Kerf Genişliğinin Korunması: Erimiş malzemenin sürekli olarak uzaklaştırılması, istenen kerf genişliğinin korunmasına yardımcı olarak son kesimde boyutsal doğruluk ve hassasiyet sağlar.
Kesim Bölgesini Soğutma
Lazer ışınının ürettiği yoğun ısı, iş parçası üzerinde bükülme, deformasyon ve malzeme özelliklerinde değişiklikler dahil olmak üzere önemli termal etkilere neden olabilir. Yardımcı gaz, kesme bölgesini soğutarak bu termal etkilerin kontrol altına alınmasına yardımcı olur.
- Isıyı Dağıtma: Yardımcı gaz akışı, kesme alanındaki fazla ısıyı emer ve dağıtır, aşırı ısınmayı önler ve malzemenin termal deformasyonunu en aza indirir.
- Isıdan Etkilenen Bölgenin (HAZ) Azaltılması: Kesme bölgesinin soğutulması, HAZ'ın boyutunun sınırlandırılmasına yardımcı olur, malzemenin mekanik özelliklerini korur ve çarpılma veya diğer termal hasar riskini azaltır.
- Kesme Hızlarının Artırılması: Verimli soğutma, malzemenin termal olarak kaynaklanan kusurlar geliştirme olasılığı daha düşük olduğundan kesme hızlarını artırır, bu da daha hızlı, daha verimli üretim sağlar.
Lensin Korunması
Kesme kafasındaki mercek, lazer ışınını iş parçası üzerine odaklar. Kesme işlemi sırasında oluşan duman, toz ve döküntü gibi kirletici maddeler merceğe zarar verebilir veya performansını düşürebilir. Yardımcı gaz lensi kirletici maddelerden korur.
- Lens Koruması: Yardımcı gaz, lens ile kesme alanı arasında bir bariyer oluşturarak kirletici maddelerin lens yüzeyine ulaşmasını ve birikmesini önler.
- Optik Kalitenin Korunması: Yardımcı gaz, merceği temiz ve kalıntılardan uzak tutarak optimum ışın odağı ve tutarlı kesme performansı sağlar.
- Lens Ömrünün Uzatılması: Kirlenmenin önlenmesi lensteki aşınmayı azaltır, ömrünü uzatır ve bakım maliyetlerini azaltır.
Kesme Reaksiyonunu Geliştirin
Yardımcı gazlar, lazer kesim sırasında meydana gelen kimyasal reaksiyonları etkileyebilir ve böylece farklı malzemelerin kesim performansını artırabilir. Kullanılan gazın türü, kesme kalitesini ve verimliliğini etkileyebilecek belirli reaksiyonları teşvik edebilir veya engelleyebilir.
- Oksijen (O₂): Oksijen yaygın olarak karbon çeliğini kesmek için kullanılır. Erimiş metalle ekzotermik bir reaksiyonu teşvik ederek ek ısı üretir ve bu da kesme hızını artırır. Bu reaksiyon daha az cürufla temiz bir kesim yapılmasına yardımcı olur ancak kesim kenarında oksidasyona neden olabilir.
- Azot (N₂): Azot, paslanmaz çelik, alüminyum ve diğer demir dışı metalleri kesmek için yaygın olarak kullanılan inert bir gazdır. Kesim bölgesinin etrafında inert bir atmosfer oluşturarak oksidasyonu önler. Bu, temiz, oksitsiz bir kenar üreterek yüksek kaliteli yüzey kalitesi gerektiren uygulamalar için idealdir.
- Basınçlı Hava: Basınçlı hava, çeşitli malzemeleri kesmek için kullanılabilecek uygun maliyetli bir alternatiftir. Daha düşük maliyetle yeterli kesme performansı sağlamak için oksijen ve nitrojenin özelliklerini birleştirir. Ancak kesim kalitesini etkileyen yabancı maddelerin ortaya çıkmasına neden olabilir.
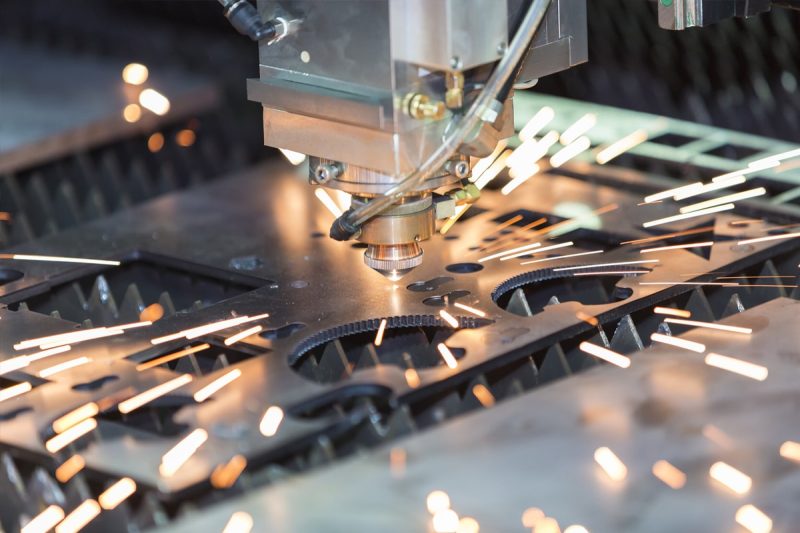
Yardımcı Gaz Türleri
Oksijen (O₂)
Avantajlar
- Artan Kesme Hızı: Oksijen, ekzotermik bir reaksiyonla malzemeyle reaksiyona girerek ilave ısı açığa çıkarır. Bu ek ısı, kesme hızını artırarak, özellikle kalın malzemelerde oksijen destekli kesimi önemli ölçüde daha hızlı hale getirir.
- Geliştirilmiş Verimlilik: Ekzotermik reaksiyon, malzemeyi kesmek için gereken lazer gücünü azaltarak kesme işleminin genel enerji verimliliğini artırır.
- Kalın Malzemelerde Daha Temiz Kesimler: Oksijen, daha kalın malzemelerde daha temiz kesimler yapılmasına yardımcı olur, cüruf ve cürufu azaltır, bu da kapsamlı son işlem ihtiyacını azaltır.
Dezavantajları
- Oksidasyon: Oksijen ve malzeme arasındaki reaksiyon, kesici kenarın oksidasyonuna neden olabilir, bu da daha pürüzlü bir yüzey kalitesine ve olası korozyon sorunlarına neden olabilir.
- Isıdan Etkilenen Bölge (HAZ): Ekzotermik reaksiyon tarafından üretilen ilave ısı, HAZ'ın boyutunu arttırır; bu da, kesme kenarı yakınındaki malzemenin mekanik özelliklerini değiştirebilir ve eğrilme veya yapısal bütünlüğün azalması gibi sorunlara neden olabilir.
- Demir Dışı Metallere İlişkin Sınırlamalar: Oksijen, oksijenle kolayca reaksiyona girmeyen alüminyum ve bakır gibi demir dışı metaller kadar etkili değildir.
Azot (N₂)
Avantajlar
- Oksidasyonsuz Kesim: Azot, kesme işlemi sırasında malzeme ile reaksiyona girmeyen inert bir gazdır. Bu özellik oksidasyonu önleyerek yüksek kaliteli yüzey kalitesi gerektiren uygulamalar için ideal olan temiz, parlak, oksitsiz bir kenar sağlar.
- Yüksek Kaliteli Yüzey Kaplaması: Oksidasyonun olmaması, daha pürüzsüz bir kenar ve daha pürüzsüz bir yüzey kaplamasıyla sonuçlanır, bu da son işlem ihtiyacını azaltır veya ortadan kaldırır.
- Minimize Edilmiş Isıdan Etkilenen Bölge (HAZ): Azot, ısıdan etkilenen küçük bir bölgenin korunmasına yardımcı olarak malzemenin mekanik özelliklerini korur ve termal deformasyonu en aza indirir. Bu, hassas kesimler ve sıkı toleranslar gerektiren uygulamalar elde etmek için kullanılabilir.
Dezavantajları
- Daha Yavaş Kesme Hızları: Oksijenin sağladığı ekzotermik reaksiyon olmadan, nitrojen destekli kesme, özellikle daha kalın malzemelerde genellikle daha yavaş kesme hızlarına neden olur. Bu yavaş hız genel üretkenliği etkiler.
- Daha Yüksek Lazer Gücü Gereksinimleri: Nitrojen kesme işlemine ek ısı sağlamadığından, malzemeyi kesmek için gereken tüm enerjiyi lazerin sağlaması gerekir. Bu gereklilik daha yüksek enerji tüketimine ve işletme maliyetlerine neden olabilir.
- Maliyet Konuları: Nitrojen diğer gazlardan daha pahalı olabilir ve daha yüksek lazer gücü gereksinimlerinin neden olduğu artan tüketim, işletme maliyetlerini daha da artırabilir.
Sıkıştırılmış hava
Avantajlar
- Uygun Maliyet: Basınçlı hava, nitrojen ve oksijen gibi saf gazlara göre daha kolay temin edilebilir ve daha ucuzdur. Bu, özellikle daha ince malzemeler içeren birçok lazer kesim uygulaması için ekonomik bir seçimdir.
- Çok yönlülük: Basınçlı hava, yumuşak çelik, paslanmaz çelik ve alüminyum dahil çok çeşitli malzemeleri kesmek için kullanılabilir. Çok yönlülüğü onu genel amaçlı kesim için pratik bir seçim haline getirir.
- Azalan İşletme Maliyetleri: Basınçlı hava ucuz olduğundan ve yaygın olarak bulunabildiğinden, basınçlı havanın kullanılması genel işletme maliyetlerini azaltabilir, bu da onu küçük ölçekli işlemler veya bütçeye duyarlı projeler için uygun hale getirir.
- Çevresel Faydaları: Basınçlı hava kullanmak, şişelenmiş gaza olan bağımlılığı azaltır, bu da gaz üretimi ve nakliyesiyle ilişkili karbon ayak izini azaltarak çevresel fayda sağlar.
Dezavantajları
- Daha Düşük Kesim Kalitesi: Basınçlı havadaki oksijen ve yabancı maddeler kesim kalitesini etkileyebilir, bu da kenarların daha pürüzlü olmasına, cürufun artmasına ve kesim yüzeyinin potansiyel kirlenmesine neden olabilir. Bu sorun özellikle yüksek yüzey kalitesi veya hassasiyet gerektiren uygulamalarda fark edilir.
- Sınırlı Kesme Hızları: Basınçlı hava, özellikle daha kalın malzemeler için genellikle oksijen destekli kesmeye göre daha yavaş hızlarda keser. Bu sınırlama üretkenliği etkiler ve yüksek hacimli üretim için uygun olmayabilir.
- Tutarsız Sonuçlar: Basınçlı havayla kesmenin kalitesi ve performansı, hava kaynağının bileşimi ve basıncındaki farklılıklar nedeniyle tutarsız olabilir. Bu tutarsızlık, bir kesme işinden diğerine aynı sonuçların elde edilmesini zorlaştırır.
- Oksidasyon ve Cüruf Oluşumu: Basınçlı hava, kesme kenarında oksidasyona ve cüruf oluşumuna neden olabilen, istenen sonuçların elde edilmesi için ilave son işlem gerektirebilen, aralarında oksijenin de bulunduğu çeşitli gazlar içerir.
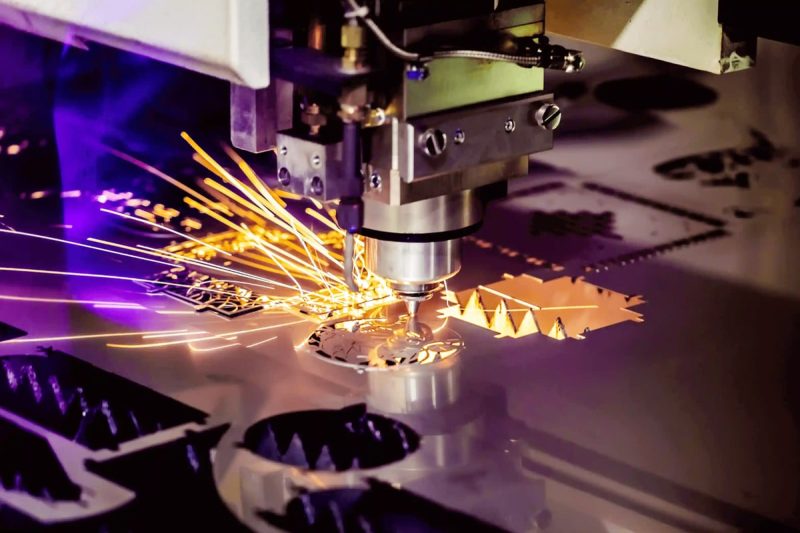
Farklı Malzemeler Üzerindeki Etki
Karbon çelik
Oksijen
- Avantajları: Karbon çeliğini kesmek için sıklıkla oksijen kullanılır çünkü malzeme ile ekzotermik reaksiyona girer. Bu reaksiyon, kesme hızını ve verimliliğini önemli ölçüde artıran ek ısı üretir. Ortaya çıkan kesimler genellikle minimum cürufla temizdir ve artırılmış ısı, daha kalın karbon çeliği bölümlerin kesilmesine yardımcı olur.
- Dezavantajları: Oksijen ile ekzotermik reaksiyon oksidasyona neden olur ve bu işlem yapılmadığı takdirde daha pürüzlü bir yüzey kalitesine ve olası korozyona neden olabilir. Isıdan etkilenen bölge (HAZ) de daha büyüktür ve bu durum, kesme kenarına yakın malzemenin mekanik özelliklerini etkileyebilir.
Azot
- Avantajları: Azot karbon çeliğiyle reaksiyona girmez, oksidasyonu önler ve temiz, oksitsiz bir kesim sağlar. Bu, yüksek kaliteli bir yüzey kalitesi ve malzemenin mekanik özelliklerini koruyan daha küçük bir HAZ ile sonuçlanır.
- Dezavantajları: Ekzotermik reaksiyonun olmaması, nitrojen destekli kesimin oksijen destekli kesime göre daha yavaş olduğu anlamına gelir. Aynı kesme hızına ulaşmak için daha yüksek lazer gücü gerekir, bu da işletme maliyetlerini artırır.
Sıkıştırılmış hava
- Avantajları: Basınçlı hava, karbon çeliğini kesmek için uygun maliyetli bir alternatiftir. Maliyet ve performans arasında bir denge kurar ve daha ince karbon çeliği bölümlerin kesilmesi için uygundur.
- Dezavantajları: Basınçlı havadaki oksijen, bir miktar oksidasyona ve cüruf oluşumuna neden olarak kesim kalitesini etkileyebilir. Kesim hızları ve kalitesi genellikle saf oksijen veya nitrojen kullanımına göre daha düşüktür.
Paslanmaz çelik
Oksijen
- Avantajları: Oksijen, paslanmaz çeliği kesmek için kullanılabilir ve ekzotermik reaksiyon nedeniyle yüksek kesme hızları sağlar. Bu reaksiyon aynı zamanda minimum cürufla temiz kesimlerin elde edilmesine de yardımcı olabilir.
- Dezavantajları: Oksijen kullanılması oksidasyona neden olabilir, bu da kenarlarda renk bozulmasına ve potansiyel korozyon sorunlarına yol açabilir. Oksit tabakası, istenen yüzey kalitesini elde etmek için ek son işlemler gerektirebilir.
Azot
- Avantajları: Azot, paslanmaz çeliğin kesilmesinde tercih edilen gazdır çünkü oksidasyonu önleyerek temiz, parlak, oksitsiz bir kenar sağlar. Azotun inert doğası, minimum düzeyde son işleme ihtiyacı ile yüksek kaliteli kesimler üretir. Azot ayrıca ısıdan etkilenen bölgeyi en aza indirerek malzemenin mekanik özelliklerinin korunmasına yardımcı olur.
- Dezavantajları: Azotun kesme hızı daha yavaştır ve oksijenden daha yüksek lazer gücü gerektirir, bu da enerji tüketiminin ve işletme maliyetlerinin artmasına neden olur.
Sıkıştırılmış hava
- Avantajları: Paslanmaz çeliğin daha ince kesitlerini kesmek için basınçlı hava kullanılabilir. Saf gaza göre daha uygun maliyetlidir ve yüksek hassasiyet gerektirmeyen uygulamalar için uygun bir seçenektir.
- Dezavantajları: Basınçlı havadaki oksijen, oksidasyona ve cüruf oluşumuna neden olarak kesim kalitesini etkileyebilir. Kenar kesimden sonra ek temizlik ve son işlem gerektirebilir.
Alüminyum ve Demir Dışı Metaller
Oksijen
- Avantajları: Yüksek yansıtma ve lazer ışınının düşük emilimi nedeniyle alüminyum ve diğer demir dışı metallerin kesilmesi için genellikle oksijen önerilmez. Ancak bazı durumlarda oksijen, ekzotermik reaksiyonu teşvik ederek daha kalın bölümlerin kesilmesine yardımcı olabilir.
- Dezavantajları: Oksijen ciddi oksidasyona neden olabilir ve bu da pürüzlü ve gözenekli bir kesim yüzeyi oluşmasına neden olabilir. Bu oksidasyon, malzemenin özelliklerini ve görünümünü olumsuz yönde etkileyerek kapsamlı bir son işlem gerektirebilir.
Azot
- Avantajları: Azot, alüminyum ve diğer demir dışı metallerin kesilmesinde çok etkilidir. Oksidasyonu önleyerek temiz, parlak ve kaliteli bir kenar elde edilmesini sağlar. Azot ayrıca malzemenin mekanik özelliklerini koruyarak ısıdan etkilenen bölgeyi en aza indirmeye yardımcı olur.
- Dezavantajları: Azot destekli kesim, oksijen kullanımına göre daha yavaştır ve malzemeyi kesmek için daha yüksek lazer gücü gerektirir, bu da işletme maliyetlerini artırır.
Sıkıştırılmış hava
- Avantajları: Basınçlı hava, alüminyum ve demir dışı metallerin daha ince kesitlerini kesmek için uygun maliyetli bir seçenektir. Hassasiyetin kritik olmadığı uygulamalarda tatmin edici kesme performansı sağlayabilir.
- Dezavantajları: Basınçlı havadaki oksijen, oksidasyona ve cüruf oluşumuna neden olarak kesim kalitesini etkileyebilir. İstenilen bitişi elde etmek için kenarlarda ilave işlem sonrası işlemler gerekebilir.
Metalik Olmayan Malzemeler
Oksijen
- Avantajları: Oksijen ahşap, akrilik ve plastik gibi metalik olmayan malzemeleri kesmek için kullanılabilir. Oksijen ile ekzotermik reaksiyon, bazı malzemeler için kesme hızını ve verimliliğini artırabilir.
- Dezavantajları: Oksijen kullanımı ahşap, akrilik gibi malzemelerin kavrulmasına ve yanmasına neden olarak yüzey kalitesini olumsuz etkileyebilir. Bu, istenen görünümü elde etmek için ek bitirme işlemlerine ihtiyaç duyulmasına neden olabilir.
Azot
- Avantajları: Azot, plastik ve seramik gibi oksidasyondan korunması gereken metalik olmayan malzemelerin kesilmesi için çok uygundur. Renk bozulmasını önler ve termal hasarı en aza indirirken temiz, yüksek kaliteli kenarlar üretir.
- Dezavantajları: Azot destekli kesim, oksijenden daha yavaş olabilir ve istenen kesme hızına ulaşmak için daha yüksek lazer gücü gerektirir.
Sıkıştırılmış hava
- Avantajları: Basınçlı hava, metalik olmayan malzemeleri kesmek için uygun maliyetli bir çözümdür ve çeşitli uygulamalar için yeterli kesme performansı sağlar. Hassasiyet ve kalitenin kritik olmadığı uygulamalar için uygundur.
- Dezavantajları: Basınçlı havadaki yabancı maddeler kesim kalitesini etkileyebilir, bu da pürüzlü kenarlara ve potansiyel kirlenmeye neden olabilir. Kesim kalitesi ve hızı, oksijen veya nitrojen gibi saf gazlarınkiyle karşılaştırılamaz.
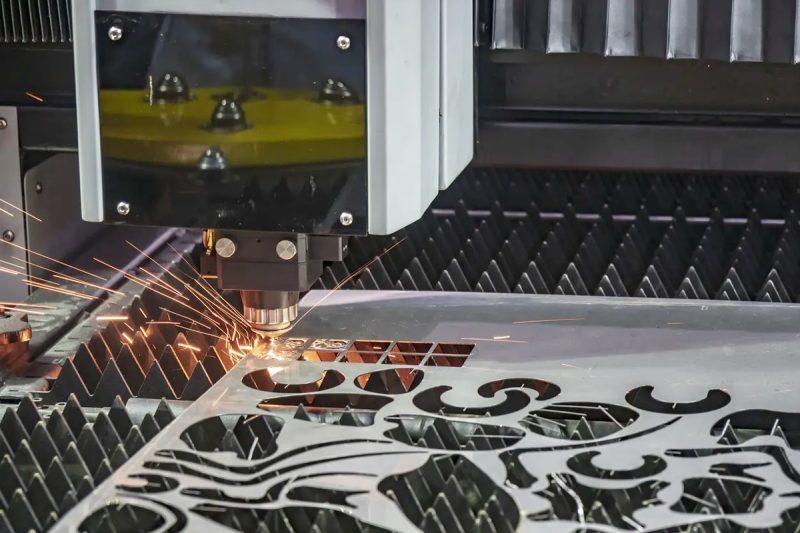
Yardımcı Gaz Seçimini Optimize Etme
Malzeme Türü ve Kalınlığı
Yardımcı gaz seçerken, kesilen malzemenin türü ve kalınlığı önemli hususlardır. Farklı malzemeler çeşitli gazlara farklı tepki vererek kesim kalitesini ve verimliliğini etkiler.
- Karbon Çeliği: Oksijen, karbon çeliğini kesmek için genellikle ilk tercihtir çünkü ekzotermik olarak reaksiyona girerek kesme hızını ve verimliliğini artırır. Daha kalın karbonlu çelikler için oksijen, malzemeyi etkili bir şekilde kesmek için gereken ısıyı sağlayabilir. Daha ince karbonlu çelikler için, daha yavaş bir hızda da olsa temiz, oksidasyonsuz bir kesim elde etmek için nitrojen kullanılabilir.
- Paslanmaz Çelik: Azot, paslanmaz çeliğin kesilmesi için idealdir çünkü oksidasyonu önler ve yüksek kaliteli, pürüzsüz bir kenar üretir. Çok kalın paslanmaz çeliklerde, kesme hızlarını artırmak için oksijen kullanılabilir ancak oksidasyona neden olur ve sonradan işlem yapılmasını gerektirir.
- Alüminyum ve Demir Dışı Metaller: Oksidasyonu önlemek ve temiz bir kesim elde etmek için alüminyum ve demir dışı metallerin kesilmesinde nitrojen ilk tercihtir. Daha az kritik uygulamalar için basınçlı hava, bir miktar oksidasyona neden olsa da uygun maliyetli bir alternatif olabilir.
- Metalik Olmayan Malzemeler: Plastik, seramik ve ahşap gibi metal olmayan malzemelerin kesilmesinde renk bozulmasını önlemek ve yüksek kaliteli bir kenar elde etmek için genellikle nitrojen kullanılır. Oksijen bazı ametalleri daha hızlı kesmek için kullanılabilir ancak kavurucu veya yanmaya neden olabilir.
Gerekli Kesim Kalitesi
Gerekli kesim kalitesi, uygun yardımcı gazın seçilmesinde önemli bir faktördür. Hassas uygulamalar genellikle minimum oksidasyon ve pürüzsüz kenarlarla yüksek kaliteli kesim gerektirir.
- Yüksek Kaliteli Yüzey İşlemi: Azot genellikle hassas, temiz ve oksidasyonsuz kesimler gerektiren uygulamalar için en iyi seçimdir. Oksidasyonu önleyerek pürüzsüz kenarlar ve yüksek kaliteli yüzey kalitesi sağlar.
- Genel Kalite: Oksijen minimum cürufla yüksek kalitede kesim sağlayabilir ancak oksidasyon nedeniyle kenarlar ek temizlik gerektirebilir. Basınçlı hava, en yüksek kalitede yüzey kalitesinin gerekli olmadığı, daha az kritik uygulamalar için uygun olabilir.
Kesim Hızı ve Verimliliği
Kesme hızı ve verimliliği kullanılan yardımcı gazın türüne göre etkilenir. Amaç, kesim kalitesinden ödün vermeden mümkün olan en yüksek hıza ulaşmaktır.
- Maksimum Hız: Oksijenin ekzotermik reaksiyonu nedeniyle karbon çeliği ve daha kalın malzemeler için en yüksek kesme hızlarını sağlar, bu da kesme işlemine ilave ısı katar.
- Dengeli Hız ve Kalite: Nitrojen, hız ve yüksek kaliteli kesimler arasında bir denge kurar, ancak oksijene kıyasla daha yüksek lazer gücü gerektirebilir ve daha yavaş bir hızda kesim yapabilir.
- Uygun Maliyetli Hız: Basınçlı hava, hız ve maliyet arasında bir uzlaşma sunar; orta düzeyde kesme hızlarının ve makul kalitenin kabul edilebilir olduğu uygulamalar için uygundur.
Maliyet Hususları
Maliyet, gaz seçimine yardımcı olan, işletme giderlerini ve genel maliyet etkinliğini etkileyen önemli bir faktördür.
- Azalan İşletme Maliyetleri: Basınçlı hava en ekonomik seçimdir çünkü kolaylıkla temin edilebilir ve oksijen ve nitrojen gibi saf gazlardan daha ucuzdur. Daha az kritik malzemelerin kesilmesi veya bütçe kısıtlamalarının öncelikli olduğu durumlarda idealdir.
- Daha Yüksek Kalite ve Daha Yüksek Maliyet: Azot daha pahalı olmasına rağmen daha iyi kesim kalitesi sağlar. Ek maliyet, artan kalite ve azaltılmış işlem sonrası ihtiyaç ile haklı çıkar.
- Maliyet ve Verimliliğin Dengelenmesi: Oksijen, makul bir maliyetle yüksek kesme hızları ve makul kalite sağlayan bir orta yol sunar. Hem hızın hem de kalitenin önemli olduğu birçok endüstriyel uygulamaya uygundur.
İşlem Sonrası Gereksinimler
Bazı gazlar daha temiz kesimler ürettiğinden ve bu da bitirme işini azaltabildiğinden, işlem sonrası ihtiyaçlar yardımcı gaz seçimini etkileyebilir.
- Minimal İşlem Sonrası İşleme: Nitrojen temiz, oksidasyonsuz kesimler üreterek kapsamlı işlem sonrası işlemleri azaltır ve son işlemlerde zaman ve maliyetten tasarruf sağlar.
- Orta İşleme Sonrası: Oksijenle kesme, oksitleri çıkarmak ve istenen yüzey kalitesini elde etmek için ek adımlar gerektirebilir. Ancak daha hızlı kesme hızları bazı ek maliyetleri dengeleyebilir.
- Artan İşlem Sonrası İşlem: Basınçlı hava daha fazla cüruf ve oksidasyona neden olabilir, bu da kenarın temizlenmesi ve bitirilmesi için daha kapsamlı bir işlem sonrası işlem gerektirebilir. Bu, genel üretim süresini ve maliyetini artırabilir.
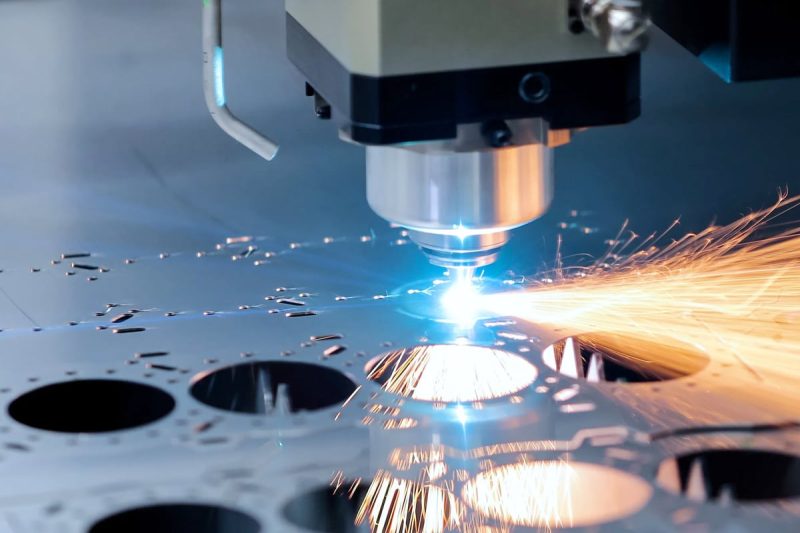
Özet
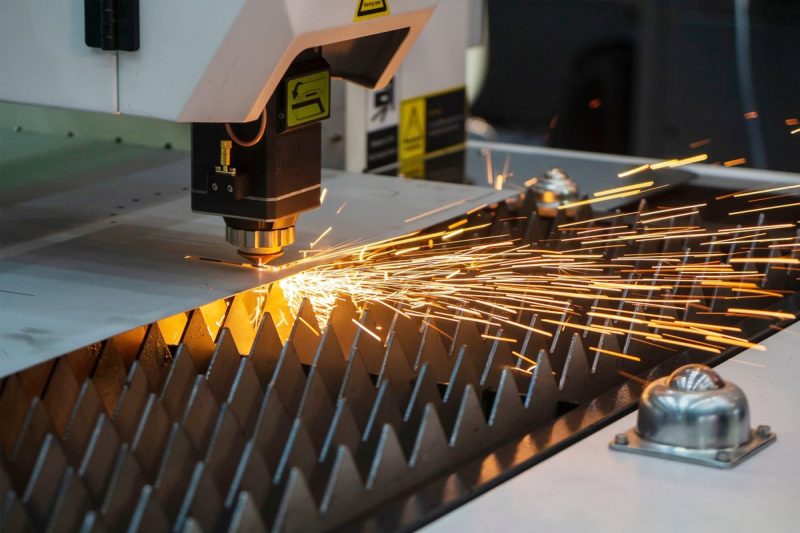
Lazer Kesim Çözümlerini Alın
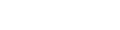
- [email protected]
- [email protected]
- +86-19963414011
- 3 Bölge A, Lunzhen Sanayi Bölgesi, Yucheng Şehri, Shandong Eyaleti.