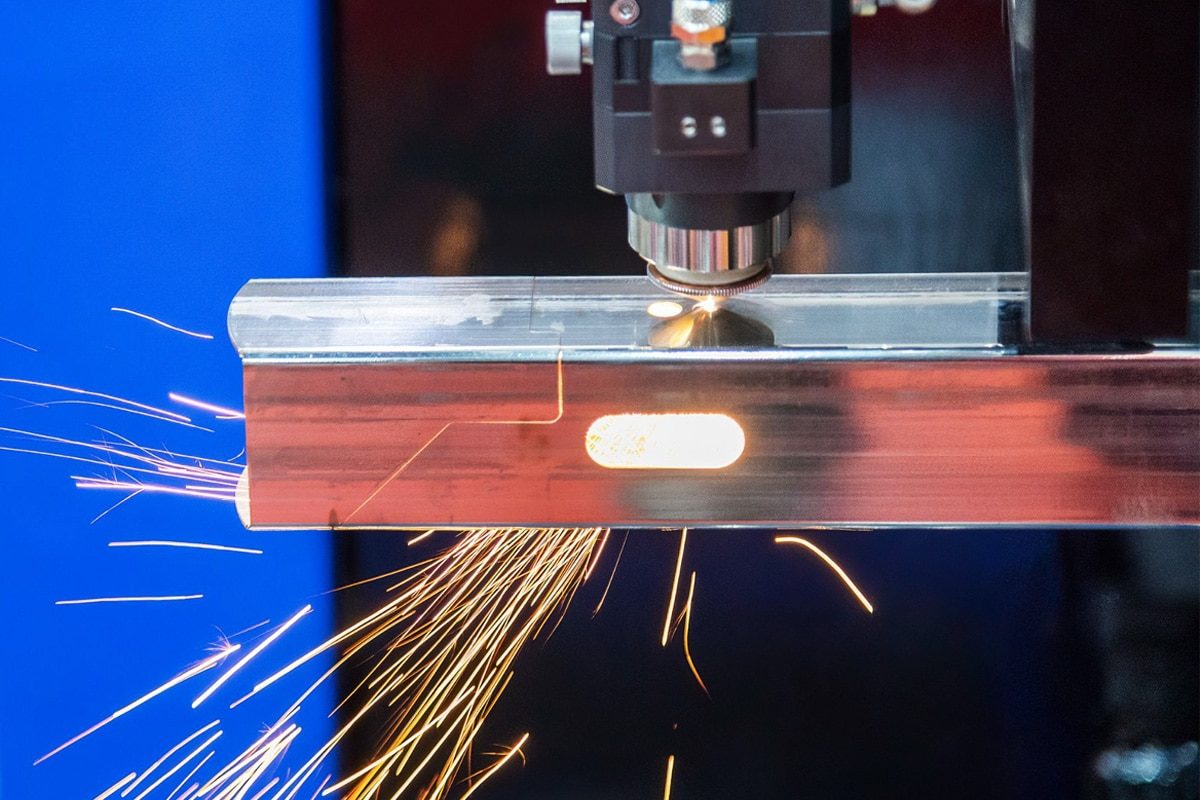
Understanding Operating Costs: Factors Affecting Fiber Laser Cutting Machine Costs
Fiber laser cutting machines have become the core equipment of the modern metal processing industry. Their high efficiency, precision, and flexibility make them widely used in automobile manufacturing, sheet metal processing, aerospace, and other fields. However, high operating costs are still a key issue for many companies. Many factors affect the operating costs of fiber laser cutting machines, including energy consumption, consumables, labor costs, material costs, equipment depreciation, technology investment, regulatory compliance costs, and market competition. This article will analyze these factors in depth and propose optimization strategies to help companies reduce operating costs and improve return on investment (ROI).
Table of Contents
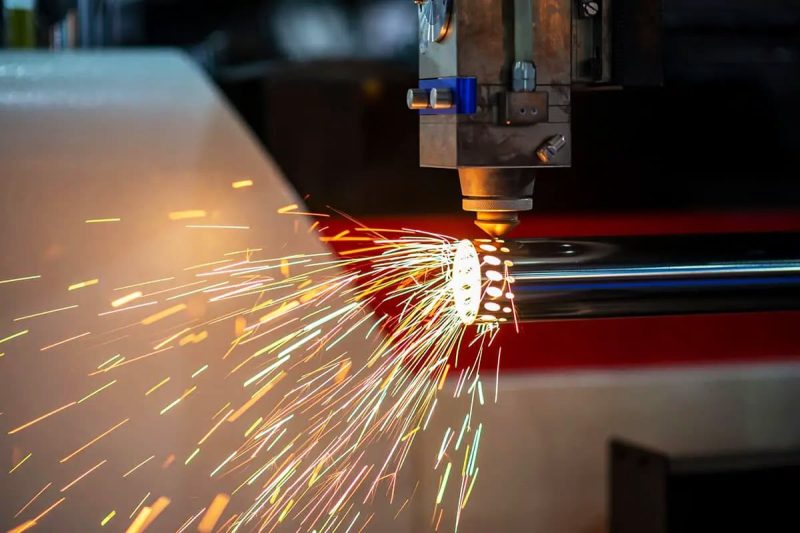
Energy consumption
Energy consumption is an important part of the operating cost of fiber laser cutting machines, which directly affects the economic and production efficiency of the equipment. Its energy consumption is mainly affected by factors such as laser power output, cutting speed, equipment idle time, and overall operating efficiency. High-power equipment is more energy-efficient when processing thick plates, but may increase unnecessary power consumption in thin plate cutting. In addition, long standby time or inefficient production scheduling will lead to energy waste and increase operating costs. Therefore, optimizing cutting parameters, arranging production plans reasonably, and investing in energy-saving equipment are key strategies to reduce energy consumption and improve economic benefits.
Key factors affecting energy consumption
The energy consumption of fiber laser cutting machine mainly depends on the following aspects:
- Laser power output: High-power fiber laser generators are relatively energy-efficient when cutting thick plates, but the proper matching of power is essential for different processing requirements.
- Cutting speed: Cutting speed affects energy consumption per unit of time, and overall energy costs can be reduced by optimizing parameters.
- Idle time: Long standby time may lead to additional energy waste, so it is essential to arrange production schedules properly.
- Equipment efficiency: Equipment of different brands and models differ in energy consumption performance, and choosing high-efficiency equipment can help reduce long-term operating costs.
Strategies to reduce energy consumption
- Optimize cutting parameters: Adjust laser power, cutting speed, and auxiliary gas pressure based on different materials (such as carbon steel, stainless steel, and aluminum alloy) to improve energy efficiency.
- Efficiently arrange production operations: Reduce equipment idle time and optimize production plans to reduce unnecessary energy consumption.
- Invest in energy-saving equipment: Use high-efficiency fiber laser generators and combine them with intelligent energy-saving modes to reduce overall operating costs.
Energy consumption is a significant part of the operating costs of fiber laser cutting machines, mainly influenced by factors such as laser power, cutting speed, idle time, and equipment efficiency. By optimizing cutting parameters, improving production scheduling, reducing equipment idle time, and investing in high-efficiency energy-saving equipment, businesses can effectively reduce energy consumption and improve economic benefits. Refining management and using intelligent equipment will further drive companies toward energy saving and efficiency, improving overall operational performance.
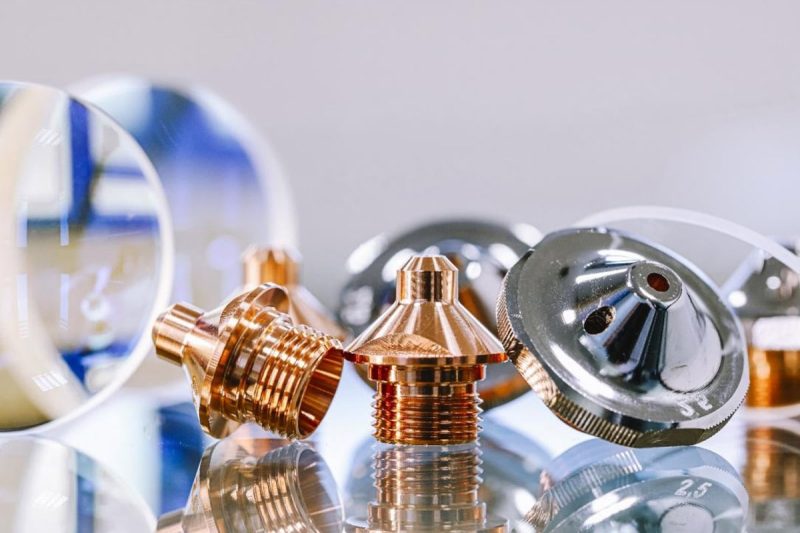
Consumables and spare parts
The long-term operation of fiber laser cutting machines cannot be separated from the support of various consumables and spare parts. The quality and service life of these parts directly affect the cutting efficiency, production stability, and the overall operating cost of the equipment. Reasonable selection of high-quality consumables and implementation of scientific maintenance management can not only reduce the frequency of replacement but also reduce unexpected downtime and improve the return on investment (ROI) of the equipment.
Consumables
The operation of the fiber laser cutting machine requires the regular replacement of some key consumables to ensure the performance and service life of the equipment. The main consumables include:
- Nozzle: responsible for controlling the flow of auxiliary gas, long-term use will wear and affect the cutting quality and gas flow stability. Worn nozzles will cause inaccurate cutting or even non-penetration, so they need to be replaced regularly.
- Lens: A key component for focusing the laser beam. Surface contamination or damage will cause the quality of the laser beam to deteriorate, affecting the cutting accuracy and speed. Regular inspection and replacement are necessary measures to ensure cutting quality.
- Protective window: Protects the optical lens from metal splashes and smoke pollution. If the surface is contaminated or damaged, it will reduce the transmittance and affect the cutting effect, so it needs to be replaced regularly.
- Filter: Used to purify smoke and dust to ensure the exhaust effect. If the filter is clogged, it will cause the equipment to overheat or exhaust, affecting the operation of the equipment, and needing to be replaced regularly.
The quality of consumables and maintenance practices have a significant impact on the life and cost-effectiveness of fiber laser cutting machines. High-quality consumables such as nozzles, lenses, and filters can effectively reduce wear and contamination, extend the service life, and reduce the frequency of replacement, thereby reducing long-term operating costs. Regular maintenance, such as timely replacement of consumables, and cleaning of lenses and protective windows, can ensure the stable operation of the equipment and avoid downtime and high repair costs caused by failures. Overall, high-quality consumables and good maintenance can improve the efficiency of the equipment, extend its life, and ultimately achieve better cost-effectiveness.
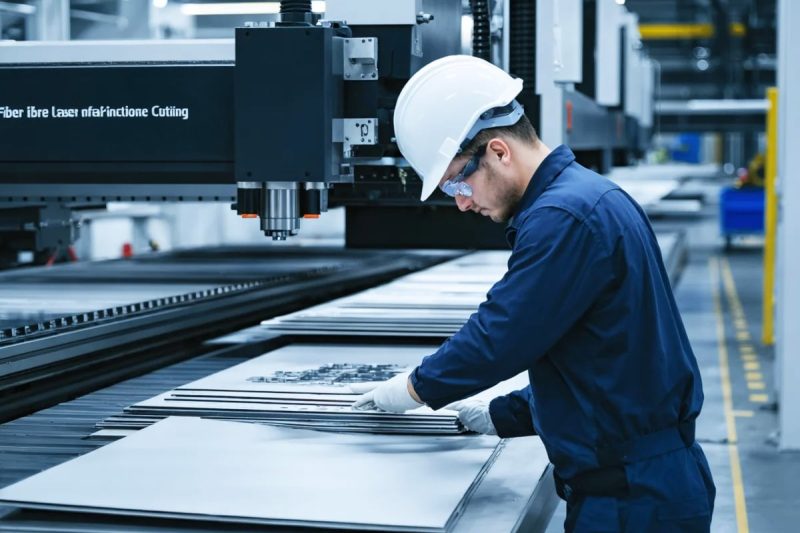
Labor cost
Labor cost is an important expense in the operation of fiber laser cutting machines, which is affected by many factors. Through reasonable management and strategy, labor costs can be effectively reduced and overall production efficiency can be improved.
Factors affecting labor costs
- Operator skills: The operator’s skill level directly affects the equipment’s operating efficiency and production quality. Experienced operators can quickly judge and solve problems, ensure smooth production processes, and thus reduce production stagnation and losses. On the contrary, inexperienced operators may cause operating errors, and increase equipment failure rates and rework costs. Therefore, improving the skill level of operators is crucial to reducing labor costs.
- Training requirements: Systematic training helps reduce misoperation and improve the efficiency of equipment use during production. Regular training can ensure that operators are proficient in equipment operating specifications and maintenance procedures, reducing loss costs caused by operating errors. At the same time, training can also improve employees’ overall understanding of the equipment, reduce equipment maintenance and downtime, and effectively reduce labor costs.
- Staffing level: The rationality of staffing directly affects the operating efficiency of the production line. By improving the level of automation, the need for manual intervention can be effectively reduced. For example, automated equipment and systems can reduce the frequency of manual operations and reduce management costs caused by insufficient or excessive staff. In addition, optimizing staffing and improving work efficiency can also better allocate human resources and improve production efficiency.
Strategies to optimize labor efficiency and minimize costs
- Invest in operator training: Establishing a standardized training system and regularly providing technical training and operation process guidance to operators can significantly improve employees’ production efficiency and operation accuracy. Through training, operators can master the best operating skills, reduce equipment loss, and improve production quality, thereby reducing costs caused by human errors.
- Implement efficient workflows: Optimizing operational processes and reducing unnecessary operations steps can greatly improve production efficiency. By reasonably arranging the production rhythm and optimizing the operation sequence, waiting time in production can be reduced, and personnel work efficiency can be improved. This can not only reduce labor costs but also increase the output of the overall production line.
- Utilize automation: Introducing advanced automation equipment such as automatic loading and unloading systems and automatic detection systems can effectively reduce human intervention. Automation systems can improve work efficiency, reduce human errors, and reduce staffing requirements. By reducing human involvement, enterprises can further reduce labor costs and improve the overall benefits of production.
In short, by improving operator skills, strengthening training, optimizing staffing and increasing investment in automation, companies can reduce labor costs while improving production efficiency and quality, thereby achieving higher cost-effectiveness.
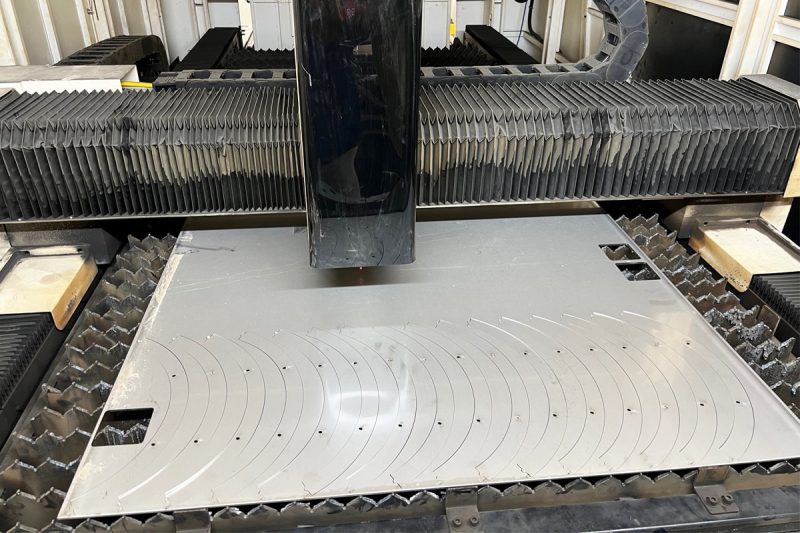
Material Cost
Material cost is a key expenditure in the fiber laser cutting production process, which directly affects the overall operating expenses of the enterprise. How to effectively control and optimize material costs can not only improve the profitability of the enterprise but also improve production efficiency.
Impact of material costs on overall operating expenses
- Cutting cost: Material consumption during laser cutting is mainly determined by factors such as cutting speed, power setting, and material thickness. Different materials and cutting conditions will directly affect the amount of material used. The thicker the material, the higher the energy consumption and time cost during cutting, which puts higher requirements on the control of material cost. Therefore, choosing the right cutting parameters and ensuring the optimization of the production process is crucial to reducing material costs.
- Waste: Waste is an inevitable by-product of the production process. Although some waste can be recycled and reused, a high proportion of waste will still increase the cost of material procurement and handling. Especially in complex or small batch cutting processes, the proportion of waste is often high. Therefore, how to reduce waste and improve material utilization is an important way to reduce material costs.
- Material handling: The storage, handling, and preparation of materials will also increase the overall cost. Efficient material handling processes can reduce material loss and improve production efficiency. For example, the way materials are transported and stored directly affects their service life and loss rate. Reasonable planning of storage space and handling processes can reduce material waste and thus control material costs.
Considerations for optimizing material usage and reducing waste
- Nesting software: Nesting software can maximize the utilization of materials through intelligent nesting schemes. According to the shape and size of the cut pieces, the software can accurately calculate the optimal nesting scheme to avoid unnecessary gaps and waste. Through reasonable nesting, the efficiency of material use is greatly improved, waste generation is reduced, and material costs are reduced.
- Material utilization strategy: Optimizing material utilization strategies, especially detailed material demand planning in the early stage of production, can effectively reduce over-purchasing and waste. For example, by formulating a reasonable production plan, the accuracy of material procurement can be ensured to avoid resource waste caused by excess or insufficient inventory. In addition, reasonable cutting sequence and job scheduling can also improve the overall utilization rate of materials.
- Inventory management practice: Inventory management is directly related to the liquidity and cost control of materials. By tracking inventory status in real-time, enterprises can effectively grasp the use of materials and avoid excessive backlogs or unsalable materials. Reasonable inventory management can also reduce losses caused by obsolete or expired materials and ensure the efficient use of materials. With the help of modern inventory management systems and data analysis, enterprises can more accurately control the purchase and use of materials, thereby reducing inventory costs.
Material cost plays an important role in fiber laser cutting production. Controlling material consumption and reducing waste are the keys to reducing overall operating costs. By using nesting software to optimize nesting, improve material utilization, and manage inventory properly, waste can be effectively reduced and costs can be lowered. These measures not only improve material utilization efficiency but also significantly improve production benefits.
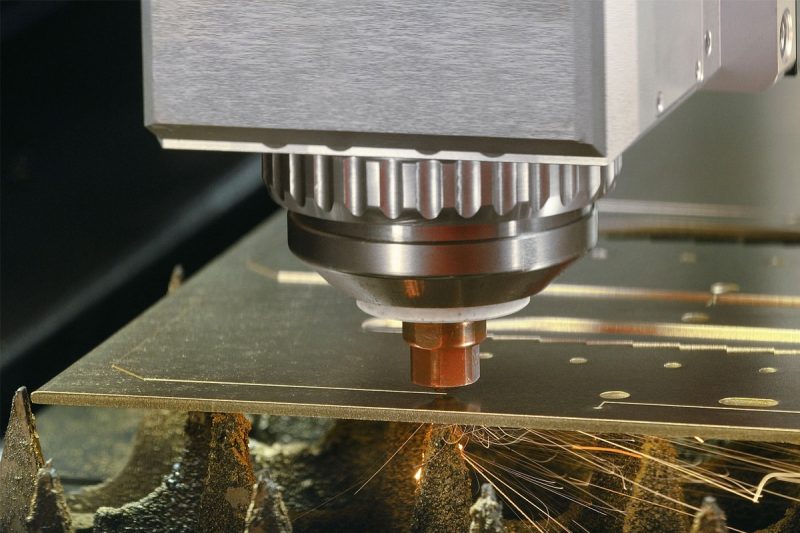
Equipment Depreciation and Financing
Equipment depreciation and financing are two important financial factors in the purchase and operation of fiber laser-cutting machines. Reasonable depreciation plans and optimized financing plans can help companies balance initial investment with long-term financial returns, reduce capital pressure, and ensure financial health.
Consider equipment depreciation and financing costs
- Initial capital investment: The initial capital investment of a fiber laser cutting machine is usually high, which is an important expenditure in the financial planning of an enterprise. Equipment procurement costs often occupy a large part of the annual budget of an enterprise. Reasonable planning and management of this investment is essential for the financial stability of the enterprise. When considering the purchase of equipment, in addition to paying attention to the function and performance of the equipment itself, it is also necessary to evaluate the equipment’s payback period and future maintenance costs.
- Depreciation plan: Depreciation is a reflection of the gradual decrease in the value of the equipment over time. In financial management, a reasonable depreciation plan helps enterprises to reasonably allocate equipment costs and avoid the burden of excessive one-time expenses. Choosing a suitable depreciation method (such as straight-line method, accelerated depreciation method, etc.) can depreciate according to the use of the equipment and the expected service life, thereby reducing the annual financial pressure of the enterprise and accumulating funds for future equipment updates or replacements.
- Financing options: Equipment financing is a common choice for many enterprises when purchasing equipment in the early stage. Through financing, enterprises can repay equipment expenses in installments without paying the full purchase amount immediately. The choice of financing method (such as loan, lease, financial lease, etc.) directly affects the cash flow of the enterprise. Reasonable financing solutions can help enterprises reduce initial capital pressure and, through flexible repayment arrangements, enable enterprises to obtain the right to use equipment while ensuring capital liquidity.
Balancing upfront costs with long-term financial considerations
Balancing upfront costs with long-term financial considerations requires a reasonable choice of depreciation methods and optimized financing options. Choosing the right depreciation method not only helps balance financial burdens, but also optimizes tax management. For high-value equipment, accelerated depreciation can accelerate depreciation in the early stages, thereby reducing the tax burden, while the straight-line method provides stable depreciation expenses throughout the service life to help financial forecasting. At the same time, companies should choose appropriate financing methods based on their own financial situation, such as financial leasing or installments, to reduce initial capital expenditure pressure, and evaluate financing costs and repayment periods to ensure long-term financial stability. Through reasonable depreciation planning and financing optimization, companies can better manage cash flow and balance upfront investment with long-term capital returns.
In summary, reasonable equipment depreciation and financing options are the key to a company’s successful management of initial investment and long-term financial returns. Through accurate depreciation planning and optimized financing strategies, companies can better balance liquidity and long-term capital returns and improve overall financial management.
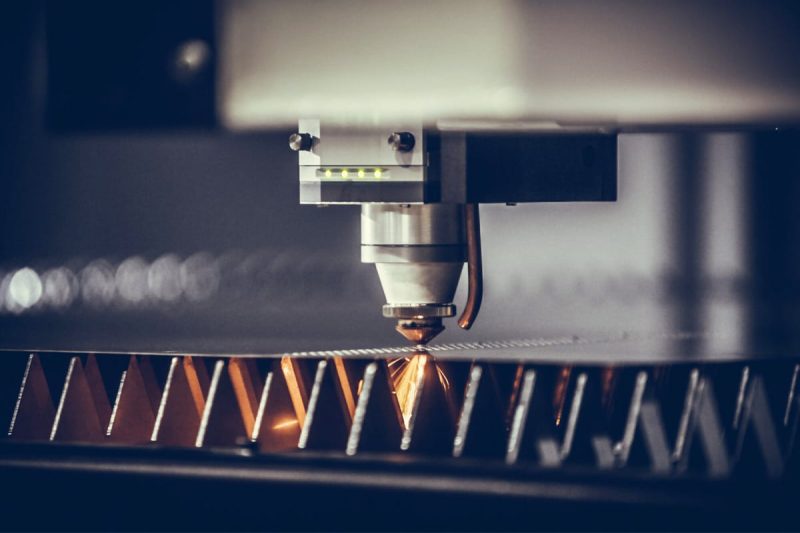
Software and technology investment
Investment in software and technology can effectively improve the level of intelligent production, bring more efficient operations and lower costs. By introducing advanced technologies, enterprises can not only improve production efficiency, but also reduce resource waste and equipment maintenance costs.
Evaluate the return on investment (ROI) of software upgrades and technology investments
- AI intelligent cutting: AI intelligent cutting technology can maximize material utilization and reduce unnecessary waste by optimizing the cutting path. The system will automatically adjust the cutting parameters according to real-time data to improve cutting accuracy and speed, thereby improving production efficiency and effectively reducing material costs.
- Intelligent monitoring system: The intelligent monitoring system can predict potential equipment failures and perform maintenance in advance by monitoring the equipment’s operating status in real-time, combined with big data and IoT technology, to avoid unplanned downtime. This not only improves the stability of the equipment and reduces downtime, but also reduces maintenance costs and extends the service life of the equipment.
In general, investing in AI smart cutting and intelligent monitoring systems can bring significant benefits in improving production efficiency, reducing resource waste, extending equipment life, etc., thereby improving the return on investment.
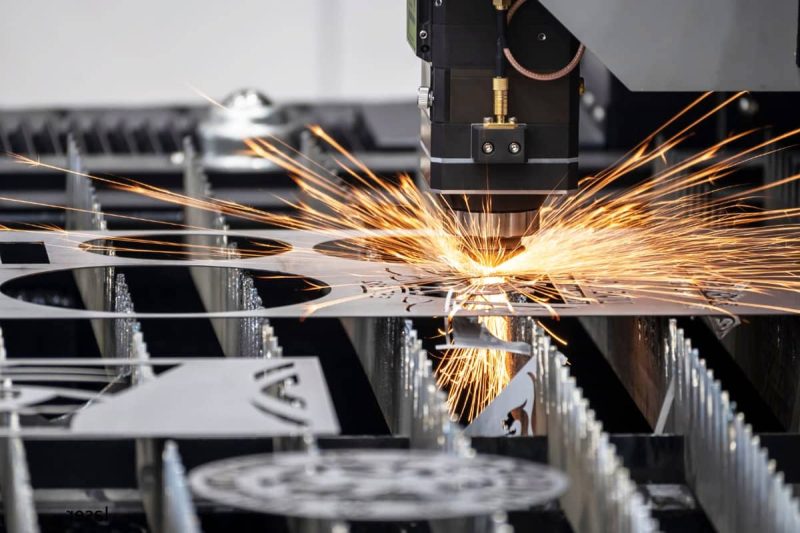
Regulatory Compliance and Security
In laser cutting and other industrial production processes, compliance with regulations and ensuring safety are important parts of business operations. Reasonable regulatory compliance and safety measures can not only protect the lives of employees but also avoid potential legal risks and economic losses.
Costs associated with regulatory compliance and security measures
- Training program: To ensure that employees fully understand and comply with safety regulations, companies need to invest resources in regular safety training. Training content usually includes operational safety, equipment usage specifications, emergency response procedures, etc. Although training may require a large investment in the early stage, it helps reduce accidents and improve employee safety awareness, thereby reducing accidents and losses caused by improper operation.
- Safety equipment: To ensure employee safety, companies also need to invest money to purchase and maintain necessary safety equipment, such as protective glasses, protective gloves, laser protection screens, etc. In addition, it is necessary to ensure that the equipment is regularly inspected and replaced to ensure its long-term effectiveness. Although the purchase and maintenance of these safety equipment will increase operating costs, they can greatly reduce the risk of work-related injuries and accidents.
- Industry standards and regulatory compliance: Laser cutting and other manufacturing fields usually have strict industry safety standards and regulatory requirements. Companies must follow these regulations to ensure that the equipment and working environment meet the relevant standards. This includes regular equipment inspections, risk assessments, and ensuring that the working environment meets safety requirements. These compliance measures may require companies to invest additional funds, but they can effectively reduce legal risks and avoid fines or litigation costs caused by non-compliance.
Prioritize safety to minimize risk and potential liability
Prioritizing safety can help companies reduce potential safety risks, lower the incidence of accidents, and avoid potential legal liabilities. By implementing strict safety measures and regulatory compliance programs, companies can not only protect the health and safety of their employees but also enhance brand reputation and enhance corporate social responsibility. In addition, companies that comply with safety regulations and standards can reduce the risk of legal proceedings due to non-compliance with safety regulations and ensure long-term stable operations.
Regulatory compliance and safety measures are fundamental to the successful operation of a business. By investing the necessary resources in employee training, purchasing safety equipment, and ensuring compliance with industry regulations, companies can not only ensure the safety and health of their employees but also reduce legal risks and potential liabilities. Prioritizing safety measures can help companies avoid possible financial losses, improve overall operational efficiency, and ensure long-term sustainable development.
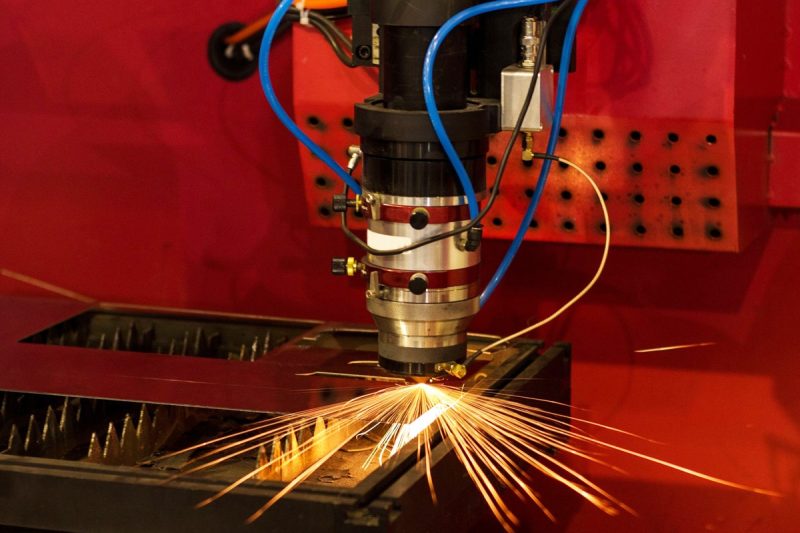
Market Conditions and Competition
In the laser cutting and manufacturing industry, market conditions and competition have a significant impact on the operating costs and profitability of enterprises. External factors such as market demand, competitive pressure, and pricing pressure will directly affect the pricing strategy, cost control, and market performance of enterprises. Therefore, understanding market dynamics and adjusting operating strategies according to actual conditions is the key to maintaining competitiveness.
External factors affecting operating costs
- Market demand: Market demand is a key factor in determining production scale and product sales price. Demand fluctuations directly affect production plans and raw material procurement, which in turn affects operating costs. During peak demand periods, companies may need to speed up production and increase equipment operating time, which will lead to increased energy consumption, labor costs, and maintenance costs. When demand decreases, companies may need to adjust production plans to avoid excessive inventory and overproduction and reduce unnecessary waste.
- Competition: Industry competition has a direct impact on operating costs. In a highly competitive market, companies often need to adopt price competition strategies and lower product prices to attract more customers. This will lead to a narrowing of profit margins, forcing companies to make more efforts in cost control. To stand out in the market, companies also need to continue to innovate in R&D, production efficiency, and quality control to reduce costs and maintain competitiveness.
- Pricing pressure: With the intensification of competition and changes in market demand, the pricing pressure faced by companies is also increasing. In many cases, to meet customer needs and maintain market share, companies may need to lower prices, which will directly affect their gross profit margins. To cope with this pressure, companies must maintain profitability by optimizing production processes, improving efficiency, and reducing unnecessary expenses.
Strategies to adapt to market conditions and stay competitive
- Differentiation: Companies can respond to market competition through differentiation strategies. By providing unique product features or higher quality services, companies can avoid pure price competition and attract specific customer groups. Differentiation can not only help companies maintain a high gross profit margin but also form a unique market positioning in the competition.
- Value-added services: In addition to providing basic laser cutting services, companies can also improve customer experience and increase revenue sources through value-added services. For example, providing additional services such as customized services, after-sales support, equipment maintenance, and technical consulting can enhance customer stickiness and enhance the company’s market competitiveness.
- Cost management technology: In response to pricing pressure and improving production efficiency, companies need to adopt effective cost management technology. By introducing automation technology, optimizing production processes, rationally purchasing raw materials, and reducing energy consumption, companies can reduce operating costs, improve production efficiency, and thus maintain competitiveness.
Market conditions and competition directly affect the operating costs and profitability of enterprises. To maintain their advantages in the fierce market competition, enterprises need to understand market demand fluctuations, competitive situations, and pricing pressure, and adopt strategies such as differentiation, value-added services, and cost management. By continuously optimizing production efficiency, improving product value, and reducing costs, enterprises can not only adapt to market changes but also stand out from the competition and maintain long-term market competitiveness.
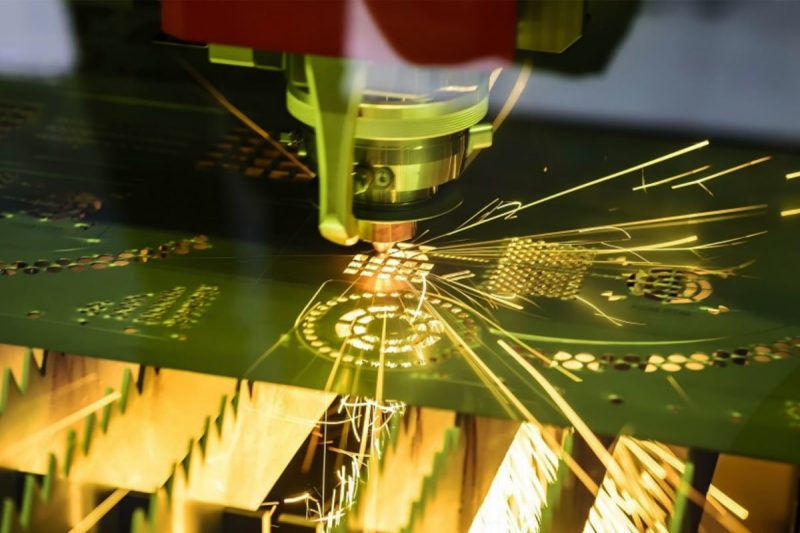
Summarize
The operation cost management of fiber laser cutting machines is the key to achieving efficient production and improving competitiveness. By optimizing energy consumption, improving material utilization, reasonably controlling labor costs, implementing automation, investing in intelligent technology, and fine management, enterprises can effectively reduce operating costs and improve return on investment. With the continuous development of intelligent manufacturing, digital twins, and AI optimization technologies, the industry will transform towards a more efficient and low-cost operation model.
AccTek Laser is committed to providing efficient and low-energy fiber laser cutting solutions. Our equipment excels in optimizing energy consumption, improving material utilization, and reducing maintenance costs, helping companies improve production efficiency. We continue to innovate and combine cutting-edge technologies to help customers reduce operating costs, improve overall production efficiency, and drive companies to maintain a leading position in the fierce market competition.
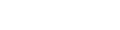
Contact information
- [email protected]
- [email protected]
- +86-19963414011
- No. 3 Zone A, Lunzhen Industrial Zone,Yucheng City , Shandong Province.
Get Laser Solutions