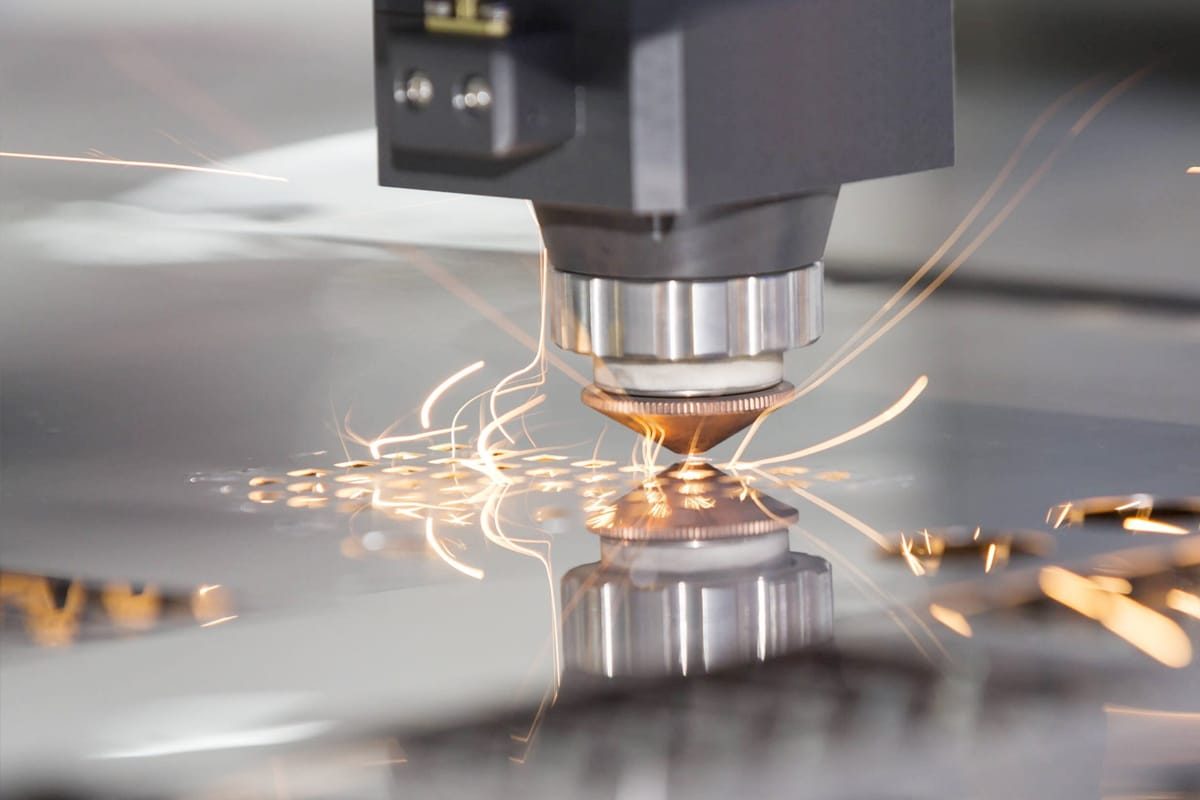
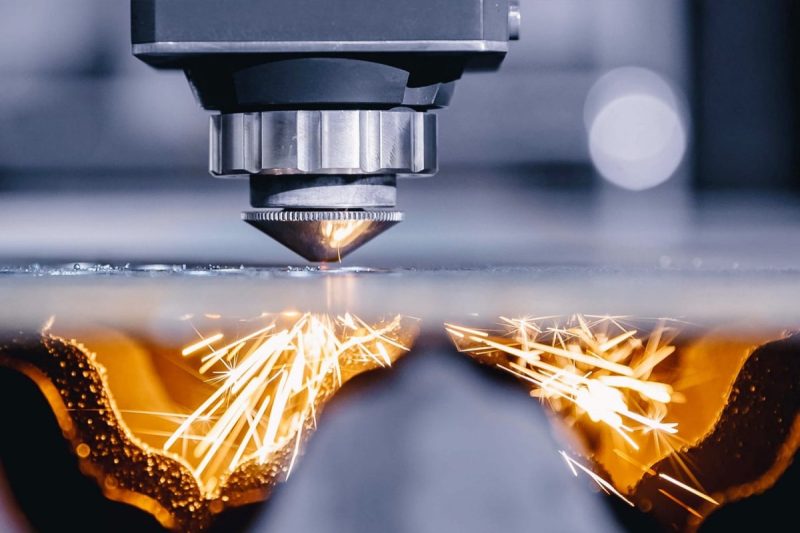
Overview of Operating Costs
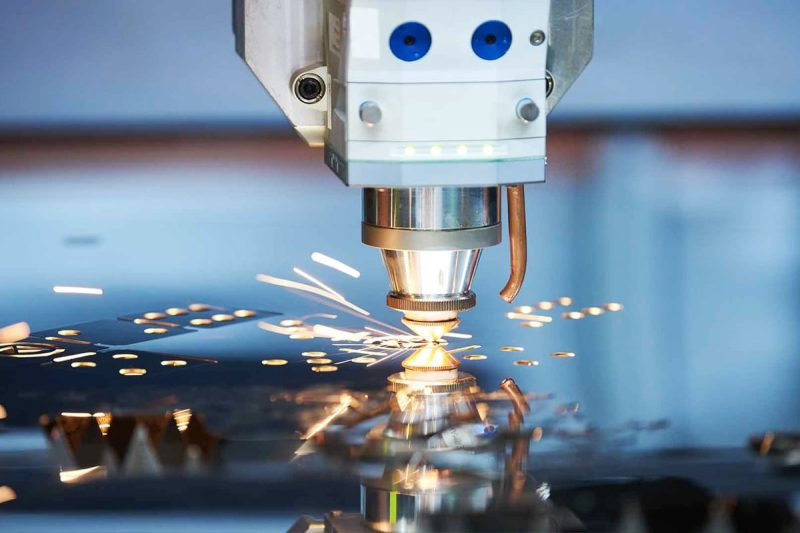
Importance of Cost Optimization
Cost optimization is more than just a financial strategy, it is an essential aspect of ensuring the competitiveness, sustainability, and profitability of your laser-cutting business. By effectively managing and reducing operating costs, manufacturers can achieve several key benefits:
- Reduce Costs: Identifying and reducing unnecessary expenses, such as excessive power consumption, avoidable maintenance costs, or consumable waste, directly impacts the bottom line. Cost-saving initiatives contribute directly to increased profitability and sustainability.
- Increase Profitability: Reducing operating costs directly contributes to increased profit margins. Cost optimization strategies, such as minimizing energy consumption, reducing waste, and optimizing maintenance schedules, can significantly impact profits.
- Increase Operational Efficiency: Streamlining processes and implementing efficient practices can help maximize machine uptime and productivity. This includes optimizing cutting parameters, utilizing advanced software for process control, and investing in automation technology to reduce manual intervention.
- Competitive Advantage: In today’s competitive manufacturing environment, cost efficiency is a key factor. Companies that can offer high-quality products at competitive prices will gain a significant advantage. Effective cost management enables companies to offer competitive prices while maintaining profitability.
- Sustainability: Cost optimization is often aligned with sustainability initiatives. For example, reducing energy consumption not only reduces operating costs but also minimizes environmental impact. Effectively managing consumables and reducing waste contributes to sustainable production practices.
- Risk Mitigation: Proactively managing operating costs reduces financial risks associated with unexpected expenses and downtime. Regular maintenance and monitoring help detect potential issues early, preventing expensive repairs and disruptions to production schedules.
- Long-Term Viability: Effective cost optimization strategies contribute to the long-term viability of manufacturing operations. Investments in technology upgrades, employee training programs, and preventive maintenance extend the life of equipment and ensure consistent performance.
- Strategic Decision Making: Accurate cost data enables informed decisions about equipment upgrades, process improvements, and capacity planning. Data-driven insights allow managers to effectively allocate resources and take advantage of growth opportunities.
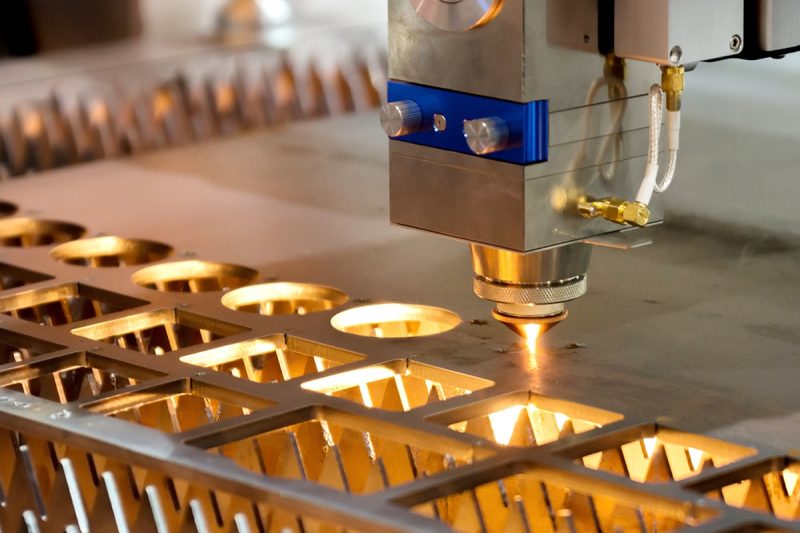
Factors That Influence Operating Costs
Power Consumption
Maintenance and Repairs
Consumables
Consumables are materials and parts that need to be replaced periodically due to wear and tear. The main consumables for laser cutting machines include:
- Assist Gases: Assist gases such as oxygen, nitrogen, or compressed air are used to assist the cutting process and improve the quality of the cut. The choice of gas affects cutting performance and cost.
- Optics: Lenses and mirrors degrade over time due to exposure to high-power laser beams. Regular replacement or refurbishment is necessary to maintain cutting efficiency.
- Nozzles: Nozzles wear during use and need to be replaced periodically to ensure precise gas flow and cut quality.
Labor Costs
Material Costs
Downtime and Productivity
Machine Depreciation
Software and Technology
Environmental Control
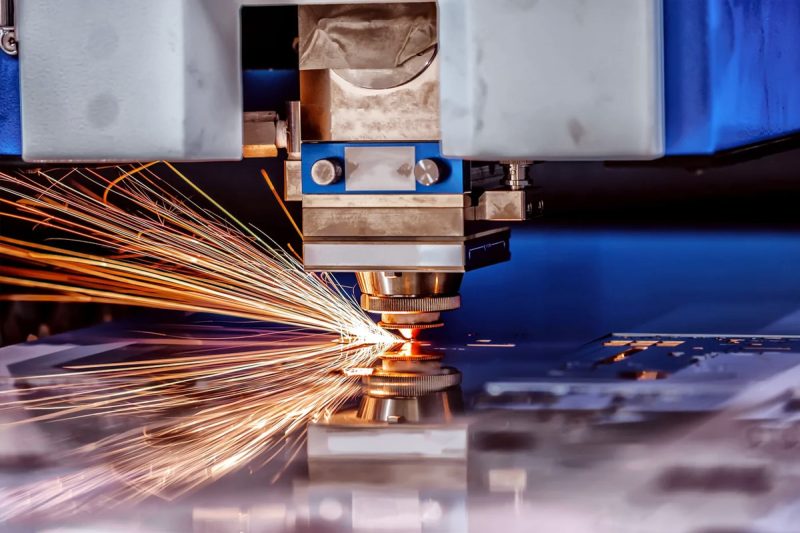
Components of Laser Cutting Machine Operating Costs
Energy Consumption
- CO2 Laser Cutting Machine (80-300W): CO2 laser cutting machines in this power range typically consume about 1-3 kW of electricity. Electricity costs range from $0.10 to $0.20 per kilowatt-hour, so operating costs are about $0.10 to $0.60 per hour.
- Fiber Laser Cutting Machine: Fiber laser cutting machines have laser powers ranging from 1 to 60 kW, and energy consumption varies widely. For lower-power machines (1-3 kW), consumption is about 8-18kW, and costs are about $0.90 to $3.6 per hour. For higher-power machines (10-60 kW), consumption ranges from 50-260 kW, and costs range from $26 to $52 per hour.
Laser Source and Maintenance
- CO2 Laser Cutting Machine: Maintenance includes regular inspections, calibration, and gas refills (CO2, nitrogen, and helium). Annual maintenance costs range from $1,000 to $3,000. The laser tube may need to be replaced every 1-2 years for $1,000 to $5,000.
- Fiber Laser Cutting Machine: Fiber laser generators have fewer maintenance requirements and a longer lifespan, typically exceeding 100,000 hours. Annual maintenance costs are lower, typically between $500 and $2,000.
Consumables
- CO2 Laser Cutting Machine: These machines require gases for both the laser and cutting processes. Gases (oxygen, nitrogen) can cost between $500 and $1,500 per year, depending on usage.
- Fiber Laser Cutting Machine: They use primarily nitrogen and oxygen for cutting. Depending on usage, the cost is between $3,000 and $5,000 per year.
Cooling Systems
- CO2 Laser Cutting Machine: CO2 laser cutting machines require cooling, but the systems are generally more efficient and less expensive to maintain, costing about $300 to $1,500 per year.
- Fiber Laser Cutting Machine: These machines generally require extensive cooling systems to keep them running at peak performance. The cost to maintain and operate the cooling system ranges from $1,000 to $3,000 per year.
Operator and Labor Costs
- Both Machines: A skilled operator is required to run and maintain a laser cutting machine. Costs can vary by location and experience but are generally between $20 and $50 per hour. Operator training is also a consideration, with initial training costs ranging from $500 to $3,000 per operator.
Replacement Parts and Repairs
- CO2 Laser Cutting Machine: These machines have more moving parts and optics that may need to be replaced frequently. Annual costs for parts and repairs range from $500 to $3,000.
- Fiber Laser Cutting Machine: Due to fewer moving parts, fiber laser cutting machines generally have lower repair and replacement costs, ranging from $200 to $1,000 per year.
Depreciation and Amortization
- Both Machines: The initial cost of a machine needs to be accounted for over its useful life. CO2 laser-cutting machines typically cost between $2,000 and $20,000, while fiber laser-cutting machines cost between $20,000 and $500,000. Depreciation is typically calculated over 5 to 10 years, with annual costs ranging from $400 to $2,000 for CO2 laser cutting machines and $4,000 to $50,000 for fiber laser cutting machines.
Software and Licenses
- Both Machines: Advanced laser cutting requires complex software with annual licensing fees ranging from $500 to $3,000.
Facility Costs
- Both Machines: These include rental, utilities, and insurance. While these indirect costs are independent of machine type, they must be considered and typically represent 10-20% of total operating costs.
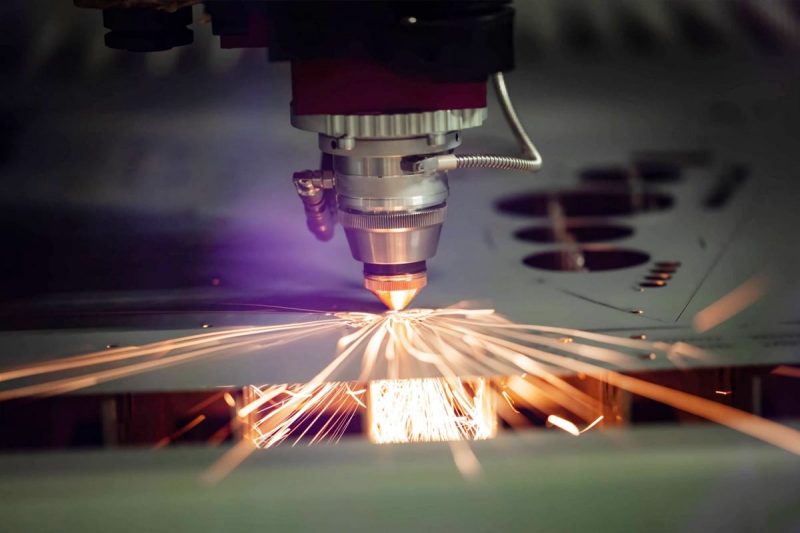
Strategies to Reduce Laser-Cutting Machine Operating Costs
Optimize Energy Use
Energy consumption is a significant component of operating costs. Implementing energy-saving measures can significantly reduce expenses:
- Use Energy-Efficient Lasers: Choose fiber lasers, which are generally more energy-efficient than CO2 lasers. Fiber lasers convert more electrical energy into laser energy, wasting less energy.
- Adjust Power Settings: Match laser power settings to the specific requirements of the job. Avoid running the laser at full power when it is not necessary, as this can save a lot of energy.
- Utilize Energy Management Systems: Implement energy management systems to monitor and control energy consumption. These systems can help identify areas where energy use can be reduced.
Regular Maintenance and Care
Regular maintenance ensures your laser cutting machine operates at optimal efficiency, reducing unexpected downtime and costly repairs:
- Regular Maintenance Checks: Schedule regular maintenance checks to ensure all components are operating at their best. This includes cleaning and replacing lenses, nozzles, and filters.
- Cleaning: Regularly clean machine components to prevent debris buildup and ensure smooth operation.
- Professional Service: Work with a professional service provider for regular in-depth maintenance and calibration.
Optimize Material Usage
Efficient material usage can reduce waste, leading to significant cost savings:
- Nesting Software: Use advanced nesting software to optimize the layout of parts on the material, maximizing the use of each sheet and minimizing waste.
- Material Selection: Choose the right material thickness and type for each job to avoid overusing expensive materials.
- Scrap Management: Implement a scrap management system to recycle and reuse material scraps whenever possible.
Improve Labor Efficiency
Labor costs can be minimized by improving operational efficiency and reducing the need for manual intervention:
- Automation: Invest in automation technologies such as automatic loading and unloading systems, robotic arms, and material handling solutions to reduce manual labor.
- Training: Provide comprehensive training to operators to improve their proficiency and reduce errors.
- Workflow Optimization: Streamline workflows to minimize idle time and ensure smooth transitions between different stages of production.
Minimize Downtime
Reducing downtime can help keep productivity high and reduce operating costs:
- Real-Time Monitoring: Implement a real-time monitoring system to detect and resolve issues promptly, reducing unplanned downtime.
- Fast Repairs: Maintain an inventory of critical spare parts to ensure fast repairs and minimize downtime.
- Reliable Equipment: Invest in high-quality, reliable machines and sign a strong support and service agreement to ensure continuous operation.
Optimize Cooling System
An efficient cooling system helps maintain optimal operating conditions while reducing energy consumption:
- Efficient Cooling Solution: Using a water cooling system ensures efficient cooling of high-power lasers compared to air-cooled systems, reducing energy costs.
- Maintenance: Regularly maintain the cooling system to ensure it operates efficiently and prevent overheating issues.
Leverage Advanced Software and Technology
Advanced software and technology can significantly improve operational efficiency and reduce costs:
- CAD/CAM Software: Leverage advanced CAD/CAM software for precise design and cutting path optimization, reduce material waste, and improve cutting accuracy.
- IoT and Industry 4.0: Implement IoT and Industry 4.0 technologies to collect, analyze, and optimize data from the cutting process in real
- Remote Diagnostics: Use remote diagnostics to quickly identify and troubleshoot faults, minimizing downtime and repair costs.
Invest in High-Quality Consumables
Using high-quality consumables reduces the frequency of replacement and improves cutting efficiency:
- Optics and Lenses: Invest in high-quality optics and lenses to provide better durability and performance, thereby reducing the need for frequent replacement.
- Assist Gas: Using high-purity assist gas ensures clean cuts and reduces the possibility of defects, thereby minimizing rework costs.
Implement Cost Management Practices
Effective cost management practices help identify and control various cost factors:
- Cost Tracking: Implement a cost tracking system to monitor and analyze operating expenses and identify areas for cost reduction.
- Budgeting: Create a detailed budget for maintenance, consumables, and energy costs to ensure that spending is controlled.
- Supplier Management: Negotiate with suppliers for better pricing on consumables and parts, and establish long-term contracts to ensure cost stability.
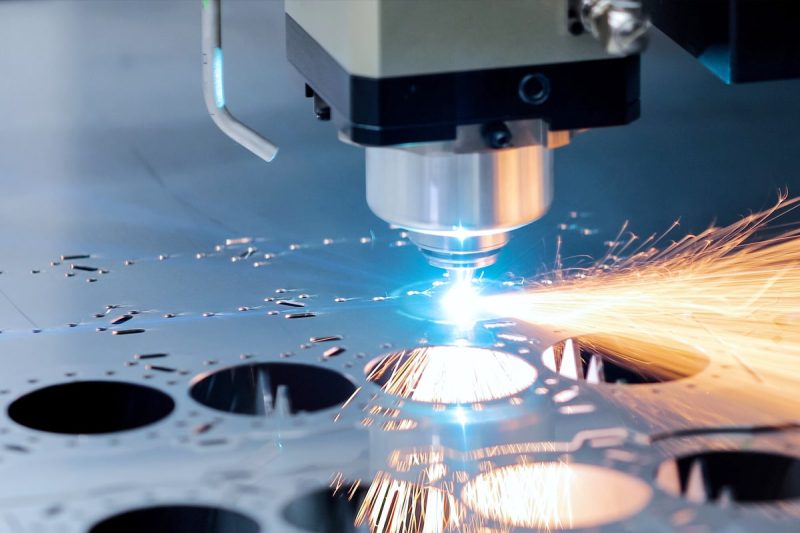
Summary
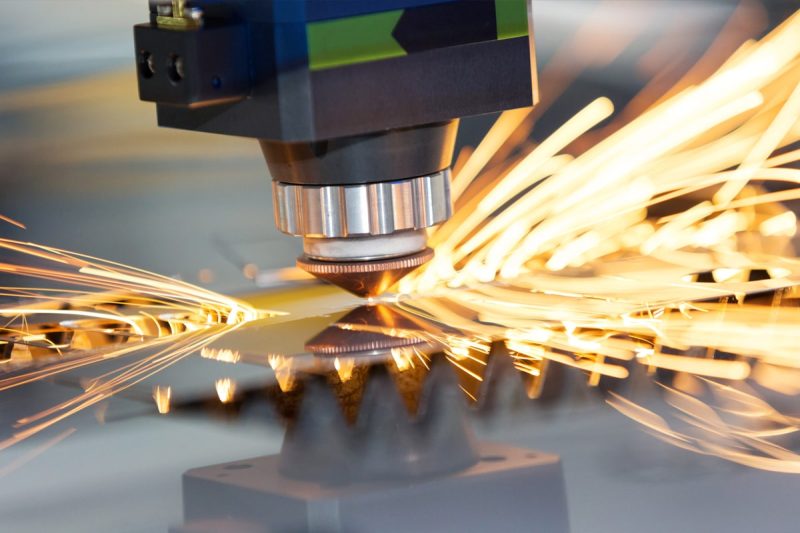
Get Laser Cutting Solutions
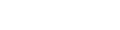
- [email protected]
- [email protected]
- +86-19963414011
- No. 3 Zone A, Lunzhen Industrial Zone,Yucheng City , Shandong Province.