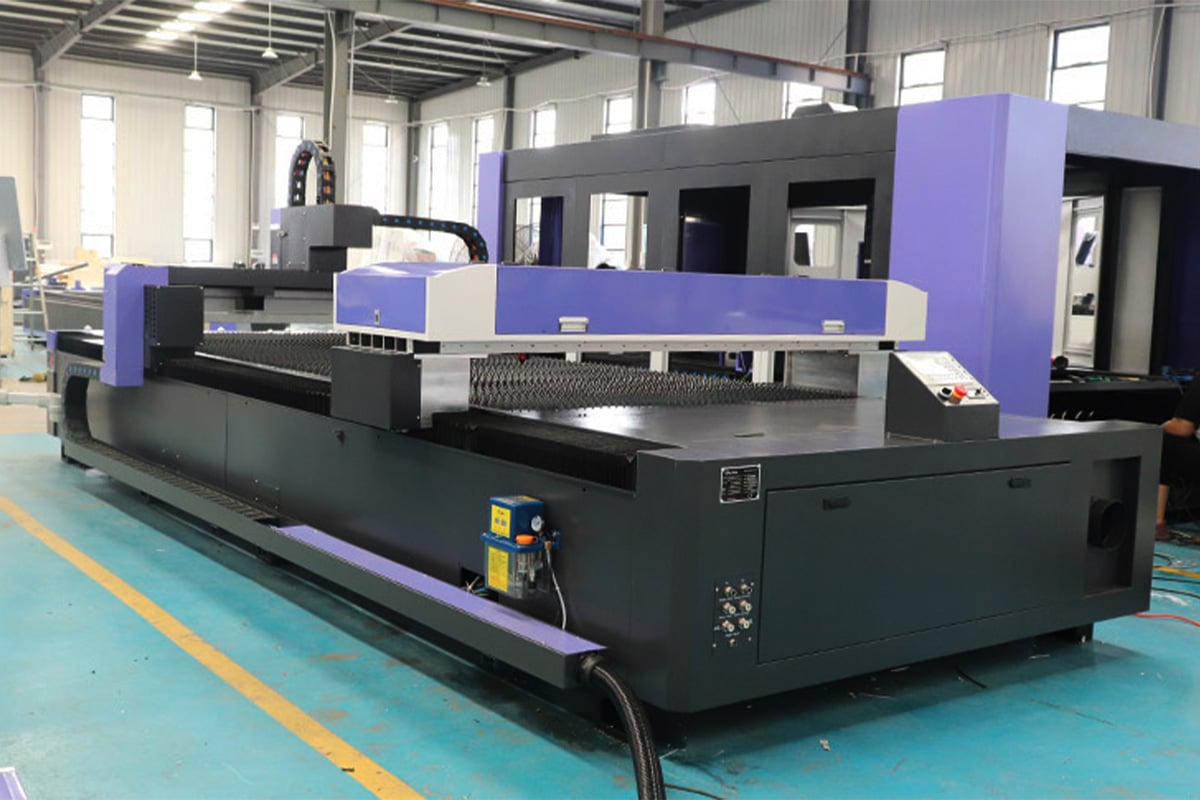
Làm thế nào để đạt được chiều rộng vết rạch tối thiểu khi cắt bằng tia laser CO2?
Công nghệ cắt laser CO2 đã được sử dụng rộng rãi trong quá trình cắt nhiều loại vật liệu khác nhau như gia công kim loại, nhựa, gỗ, vải, v.v. do ưu điểm là độ chính xác cao, tốc độ cao và gia công không tiếp xúc. Chiều rộng rãnh cắt là chiều rộng của vết cắt do chùm tia laser tạo ra trong quá trình cắt. Chỉ số này ảnh hưởng trực tiếp đến độ chính xác và chất lượng của vết cắt. Chiều rộng vết cắt nhỏ hơn có thể đạt được hiệu ứng gia công tinh tế hơn, cải thiện độ chính xác của sản phẩm, giảm lãng phí vật liệu và giảm chi phí sản xuất. Do đó, đây là tiêu chí quan trọng để đo chất lượng cắt laser.
Kiểm soát độ rộng vết rạch không chỉ để cải thiện chất lượng sản phẩm mà còn liên quan chặt chẽ đến tỷ lệ sử dụng vật liệu, sự tiện lợi của quá trình gia công tiếp theo và hiệu quả sản xuất chung. Đối với các nhà sản xuất, việc tối ưu hóa độ rộng vết rạch có liên quan trực tiếp đến việc kiểm soát chi phí sản xuất. Đặc biệt là trong sản xuất quy mô lớn, độ rộng vết rạch quá lớn có thể dẫn đến lãng phí vật liệu và ảnh hưởng đến tiến độ suôn sẻ của các quy trình tiếp theo. Do đó, kiểm soát chính xác độ rộng vết rạch là một mắt xích quan trọng để đạt được sản xuất hiệu quả và chi phí thấp.
Mục lục
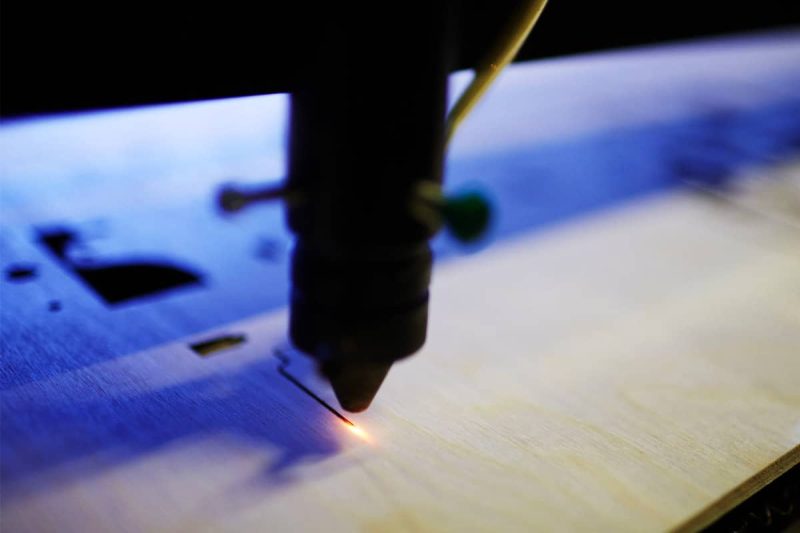
Các yếu tố chính ảnh hưởng đến chiều rộng rãnh cắt laser CO2
Hiệu quả cắt của công nghệ cắt laser CO2 bị ảnh hưởng bởi nhiều yếu tố, trong đó độ rộng rãnh cắt là một trong những chỉ số quan trọng nhất. Bằng cách điều chỉnh và tối ưu hóa hợp lý các yếu tố này, các nhà sản xuất có thể cải thiện hiệu quả sản xuất và giảm tổn thất vật liệu trong khi vẫn đảm bảo độ chính xác cao. Sau đây là một số yếu tố chính ảnh hưởng đến độ rộng rãnh cắt và các chiến lược tối ưu hóa của chúng:
Kích thước tiêu điểm laser: Kích thước tiêu điểm laser ảnh hưởng trực tiếp đến đường kính của điểm, điểm càng nhỏ thì độ rộng vết cắt càng hẹp. Độ chính xác càng cao thì nồng độ năng lượng chùm tia laser càng cao, do đó cải thiện độ chính xác của vết cắt. Để tối ưu hóa độ rộng vết cắt, điều quan trọng là phải chọn đúng ống kính tiêu cự. Nhìn chung, ống kính tiêu cự ngắn có thể cung cấp đường kính tiêu cự nhỏ hơn, do đó đạt được hiệu ứng cắt tinh tế hơn. Đối với các vật liệu và yêu cầu cắt khác nhau, có thể tối ưu hóa kích thước tiêu cự bằng cách điều chỉnh độ dài tiêu cự để đảm bảo hiệu ứng cắt tốt nhất.
Công suất laser: Công suất laser quyết định trực tiếp cường độ năng lượng nhiệt của chùm tia laser, ảnh hưởng đến hiệu ứng nóng chảy, bốc hơi và cắt trong quá trình cắt. Nếu công suất laser quá cao, dễ khiến vết cắt quá rộng hoặc thậm chí đốt cháy vật liệu; nếu công suất quá thấp, có thể không thể xuyên qua hoàn toàn vật liệu, dẫn đến cắt không hoàn chỉnh. Điều quan trọng là phải điều chỉnh công suất laser đến giá trị tối ưu theo độ dày và tính chất của các vật liệu khác nhau. Ví dụ, đối với vật liệu dày hơn, cần tăng công suất phù hợp, trong khi đối với vật liệu mỏng, có thể giảm công suất để tránh vết cắt quá rộng. Bằng cách điều chỉnh công suất chính xác, các nhà sản xuất có thể đạt được hiệu quả cắt chính xác và hiệu quả.
Tốc độ cắt: Tốc độ cắt cũng đóng vai trò quan trọng trong cắt laser. Tăng tốc độ cắt hợp lý không chỉ có thể làm giảm vùng ảnh hưởng nhiệt và giảm tác động của vật liệu nóng chảy lên cạnh cắt mà còn cải thiện hiệu quả sản xuất. Tuy nhiên, nếu tốc độ cắt quá nhanh, chùm tia laser có thể không đủ thời gian để xuyên hoàn toàn vào vật liệu, dẫn đến cắt không hoàn chỉnh; ngược lại, tốc độ quá chậm có thể khiến vết cắt quá rộng và tạo ra quá nhiều chất nóng chảy. Để tối ưu hóa hiệu quả cắt, tốc độ cắt cần được điều chỉnh chính xác theo loại và độ dày của vật liệu để đảm bảo chiều rộng cắt được giảm thiểu.
Loại khí phụ trợ và áp suất: Khí phụ trợ đóng vai trò quan trọng trong quá trình cắt laser. Các loại khí phụ trợ thường được sử dụng là oxy, nitơ và không khí. Oxy có thể tăng cường phản ứng cháy trong quá trình cắt và phù hợp để cắt các vật liệu như sắt và thép; nitơ có thể làm giảm quá trình oxy hóa và phù hợp với các vật liệu như thép không gỉ; không khí được sử dụng rộng rãi trong nhiều loại vật liệu do tính kinh tế của nó. Ngoài loại khí, áp suất khí cũng ảnh hưởng đến chất lượng cắt. Áp suất khí thích hợp có thể giúp loại bỏ chất nóng chảy và ngăn không cho nó bám vào mép của vết cắt, do đó làm giảm chiều rộng vết cắt. Áp suất khí thấp hơn có thể dẫn đến việc không thể loại bỏ chất nóng chảy một cách hiệu quả và tăng chiều rộng vết cắt, do đó phải lựa chọn áp suất và loại khí thích hợp để tối ưu hóa hiệu quả cắt.
Tính chất vật liệu: Tính chất của các vật liệu khác nhau có thể ảnh hưởng đáng kể đến độ chính xác của quá trình cắt laser. Các tính chất của vật liệu như tỷ lệ hấp thụ, độ dẫn nhiệt và điểm nóng chảy ảnh hưởng trực tiếp đến hiệu suất truyền của chùm tia laser và chất lượng cắt. Các vật liệu có độ phản xạ cao (như nhôm, đồng, v.v.) có xu hướng khiến chùm tia laser phản xạ và phân tán, do đó làm giảm hiệu quả cắt. Đối với các vật liệu này, cần tối ưu hóa các thông số laser, đặc biệt là tăng mật độ công suất, để đảm bảo rằng laser có thể xuyên qua vật liệu một cách hiệu quả. Ngược lại, các vật liệu có độ phản xạ thấp như thép dễ cắt hơn. Khi cắt các vật liệu khác nhau, nhà sản xuất nên điều chỉnh các thông số cắt theo đặc tính của vật liệu để đảm bảo chất lượng cắt tốt nhất và chiều rộng vết cắt nhỏ nhất.
Tối ưu hóa đường cắt: Tối ưu hóa đường cắt cũng rất quan trọng để kiểm soát chiều rộng vết cắt. Đường cắt trơn tru có thể giảm lỗi của chùm tia laser khi hướng thay đổi và tránh các vết cắt không đều. Đặc biệt khi cắt các hình dạng phức tạp, thiết kế đường cắt hợp lý và giảm số lần rẽ và dừng khẩn cấp có thể cải thiện đáng kể độ chính xác khi cắt. Ngoài ra, tối ưu hóa các chiến lược đưa vật liệu vào và rút lại cũng có thể giúp giảm sự phá hủy vật liệu và tránh biến dạng vết cắt do quá nhiệt. Khi thiết kế đường cắt, nên tránh các lần rẽ nhanh và các tuyến đường không đều càng nhiều càng tốt để đảm bảo năng lượng được phân bổ đều trong quá trình cắt, do đó kiểm soát được chiều rộng vết cắt.
Bằng cách kiểm soát chính xác và tối ưu hóa các yếu tố quan trọng này, các nhà sản xuất có thể giảm chi phí sản xuất, cải thiện việc sử dụng vật liệu và tăng hiệu quả sản xuất đồng thời đảm bảo cắt có độ chính xác cao.
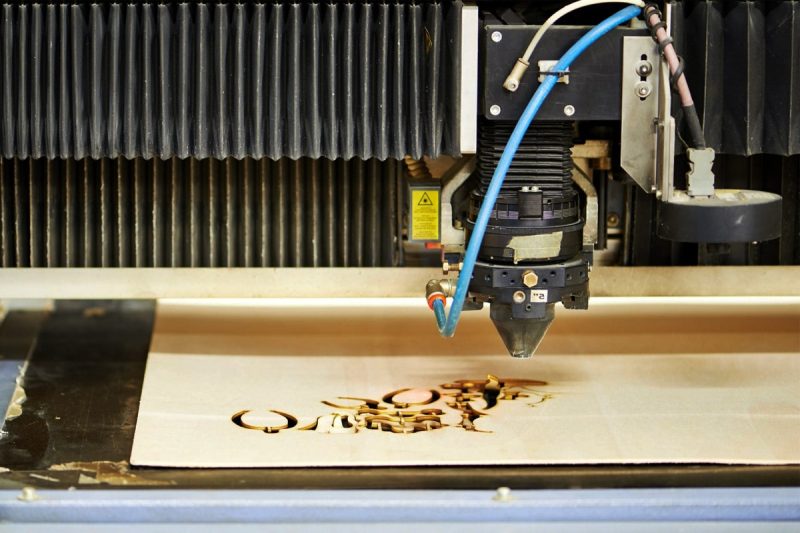
Chiến lược tối ưu hóa để đạt được chiều rộng rãnh cắt tối thiểu
Để đạt được độ rộng rãnh cắt tối thiểu trong cắt laser CO2, cần phải cân nhắc nhiều chiến lược tối ưu hóa. Các chiến lược này không chỉ có thể cải thiện độ chính xác cắt mà còn có thể giảm thiểu hiệu quả lãng phí vật liệu và cải thiện hiệu quả sản xuất. Sau đây là các phương pháp tối ưu hóa chính để đạt được độ rộng rãnh cắt tối thiểu:
Tối ưu hóa hệ thống quang học: Chất lượng của hệ thống quang học ảnh hưởng trực tiếp đến hiệu ứng hội tụ của chùm tia laser, từ đó ảnh hưởng đến độ mịn của đường rạch. Việc lựa chọn thấu kính quang học chất lượng cao có thể đảm bảo chùm tia laser được hội tụ đều trên bề mặt vật liệu mục tiêu, do đó có được hiệu ứng cắt ổn định và chính xác. Sử dụng thấu kính tiêu cự ngắn (chẳng hạn như tiêu cự 2,5 inch) là một chiến lược quan trọng để tối ưu hóa việc hội tụ của chùm tia laser. Một thấu kính tiêu cự ngắn có thể hội tụ đường kính điểm nhỏ hơn, do đó làm giảm sự khuếch tán của chùm tia laser và giảm đáng kể chiều rộng đường rạch. Một điểm nhỏ hơn không chỉ có thể cải thiện độ chính xác khi cắt mà còn giảm tác động nhiệt lên vật liệu và đảm bảo tính ổn định trong quá trình cắt.
Điều chỉnh chính xác công suất và tốc độ laser: Công suất laser và tốc độ cắt là hai yếu tố quan trọng ảnh hưởng đến chiều rộng vết rạch. Hiệu quả cắt tốt nhất có thể đạt được bằng cách điều chỉnh chính xác sự kết hợp giữa công suất và tốc độ laser. Sử dụng chế độ xung có thể giảm thời gian gia nhiệt liên tục, do đó giảm vùng ảnh hưởng nhiệt (HAZ) và giảm hiện tượng nóng chảy ở rìa vết rạch. Chế độ xung làm cho phân phối năng lượng laser đồng đều hơn và tránh được vấn đề quá nhiệt do đầu ra liên tục công suất cao gây ra. Đồng thời, điều chỉnh công suất laser kết hợp với độ dày của vật liệu có thể đảm bảo rằng chùm tia laser có thể xuyên hoàn toàn vào vật liệu và kiểm soát được chiều rộng của vết rạch. Đối với vật liệu mỏng hơn, hãy giảm công suất một cách thích hợp để tránh tích tụ nhiệt quá mức; đối với vật liệu dày hơn, hãy tăng công suất một cách thích hợp để đảm bảo chất lượng cắt, nhưng vẫn chú ý kiểm soát chiều rộng vết rạch.
Điều chỉnh các thông số khí phụ trợ: Khí phụ trợ đóng vai trò quan trọng trong quá trình cắt laser CO2. Nó không chỉ giúp loại bỏ chất nóng chảy sinh ra trong quá trình cắt mà còn kiểm soát chất lượng cắt bằng cách tối ưu hóa áp suất khí. Tăng áp suất khí đúng cách có thể loại bỏ hiệu quả xỉ sinh ra trong quá trình cắt và ngăn không cho xỉ bám vào mép vết cắt, do đó duy trì chiều rộng vết cắt hẹp. Khi lựa chọn khí phụ trợ, nitơ là một trong những loại khí thường được sử dụng, đặc biệt đối với các vật liệu cần giảm quá trình oxy hóa và cải thiện độ hoàn thiện khi cắt. Nitơ không chỉ có thể làm giảm hiệu quả quá trình oxy hóa bề mặt vật liệu mà còn duy trì độ mịn của vết cắt trong quá trình cắt, do đó đạt được hiệu ứng cắt chất lượng cao hơn.
Tối ưu hóa phần mềm và các thông số CNC: Hệ thống CNC có độ chính xác cao có thể cải thiện hiệu quả độ chính xác của quá trình cắt laser và giúp giảm độ lệch cắt do lỗi cơ học. Sử dụng hệ thống CNC tiên tiến, bạn có thể tối ưu hóa đường cắt và giảm lỗi do thay đổi hướng của chùm tia laser. Việc lập kế hoạch đường cắt chính xác giúp giảm lỗi do rẽ và đường cắt không đều trong quá trình cắt. Ngoài ra, việc sử dụng hệ thống lấy nét tự động cũng là một chiến lược quan trọng để tối ưu hóa chiều rộng vết cắt. Hệ thống lấy nét tự động có thể tự động điều chỉnh vị trí lấy nét laser theo độ dày, hình dạng và yêu cầu cắt của vật liệu để đảm bảo chùm tia laser luôn được hội tụ ở vị trí tốt nhất, do đó tránh được các vết cắt không đều hoặc quá rộng do vị trí lấy nét không chính xác.
Giảm vùng ảnh hưởng nhiệt (HAZ): Kích thước của HAZ có liên quan chặt chẽ đến sự tích tụ nhiệt trong quá trình cắt laser. Nhiệt độ quá cao có thể khiến bề mặt vật liệu bị nóng chảy quá mức, do đó làm tăng chiều rộng vết cắt và ảnh hưởng đến chất lượng cắt. Để giảm vùng ảnh hưởng nhiệt, cắt tốc độ cao là một chiến lược hiệu quả. Cắt tốc độ cao có thể tăng tốc độ chuyển động của chùm tia laser, do đó làm giảm sự tích tụ nhiệt trên bề mặt vật liệu và tránh làm tan chảy và mở rộng cạnh vết cắt. Tuy nhiên, khi sử dụng cắt tốc độ cao, cần đảm bảo rằng năng lượng của chùm tia laser đủ để xuyên qua vật liệu. Để tối ưu hóa hơn nữa chất lượng cắt, có thể kết hợp công nghệ làm mát, chẳng hạn như làm mát phun hoặc phun khí kép, có thể làm giảm hiệu quả nhiệt độ của khu vực cắt, tránh quá nhiệt và đảm bảo hiệu ứng cắt chính xác và ổn định hơn.
Bằng cách kết hợp các chiến lược tối ưu hóa trên, các nhà sản xuất có thể đạt được hiệu quả chiều rộng rãnh cắt tối thiểu trong quá trình cắt laser CO2. Với sự tiến bộ liên tục của công nghệ và tối ưu hóa liên tục của thiết bị, các chiến lược này sẽ giúp cải thiện hơn nữa độ chính xác khi cắt, giảm lãng phí vật liệu và nâng cao hiệu quả sản xuất.
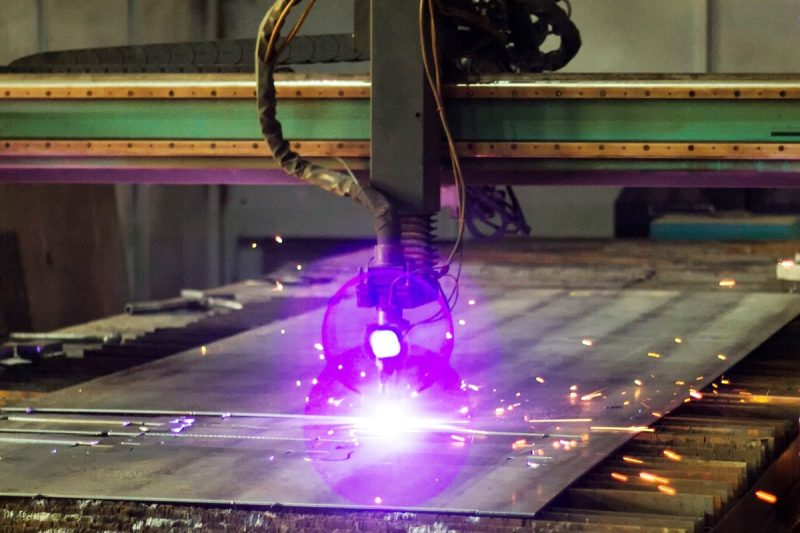
tóm tắt
Đạt được chiều rộng rãnh cắt tối thiểu không chỉ là một điều chỉnh thông số đơn giản mà là một quá trình đòi hỏi phải xem xét toàn diện nhiều yếu tố. Bằng cách tối ưu hóa chính xác tiêu điểm laser, cài đặt công suất, tốc độ cắt, loại khí phụ trợ và áp suất, cũng như kiểm soát phần mềm, các nhà sản xuất có thể tối đa hóa hiệu quả sản xuất và giảm lãng phí vật liệu trong khi vẫn đảm bảo chất lượng cắt. Việc điều chỉnh chính xác tiêu điểm laser có thể đảm bảo kích thước điểm của khu vực cắt và tránh các vùng bị ảnh hưởng bởi nhiệt quá mức trong quá trình cắt, do đó đảm bảo cắt mịn và mịn. Sự kết hợp chính xác giữa công suất và tốc độ cắt có thể tránh tích tụ nhiệt quá mức và giảm tác động của chất nóng chảy lên chiều rộng cắt. Khí phụ trợ phù hợp không chỉ có thể loại bỏ xỉ mà còn ngăn ngừa quá trình oxy hóa, cải thiện hơn nữa chất lượng cắt. Đồng thời, việc sử dụng phần mềm CNC tiên tiến và công nghệ lấy nét tự động có thể liên tục tối ưu hóa đường cắt và tiêu điểm chùm tia laser để đảm bảo tính ổn định và nhất quán của hiệu ứng cắt.
Với sự phát triển liên tục của công nghệ, hiệu suất và độ chính xác điều khiển của máy cắt laser CO2 cũng liên tục được cải thiện. Các nhà sản xuất có thể đạt được hiệu quả cắt chính xác hơn bằng cách liên tục điều chỉnh và tối ưu hóa các yếu tố trên, kết hợp với sự tiến bộ liên tục của công nghệ quang học, hệ thống điều khiển tự động và công nghệ làm mát hiệu quả. Cuối cùng, việc đạt được chiều rộng vết rạch tối thiểu không chỉ cải thiện độ chính xác khi cắt mà còn mang lại hiệu quả sản xuất cao hơn, giảm chi phí vật liệu và cải thiện đáng kể lợi ích kinh tế của dây chuyền sản xuất khi sử dụng lâu dài. Do đó, đối với người dùng máy cắt laser CO2, việc học tập liên tục và nắm vững các chiến lược tối ưu hóa này sẽ là chìa khóa để cải thiện năng lực sản xuất và khả năng cạnh tranh tổng thể.
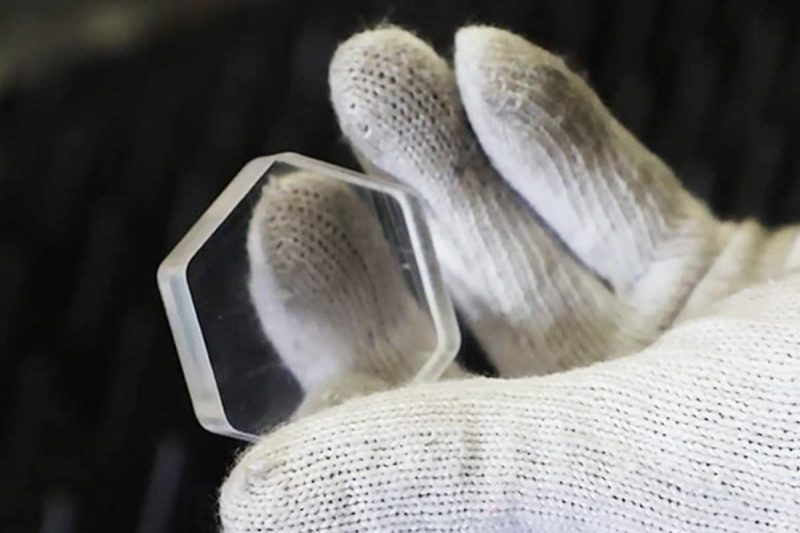
Nhận giải pháp Laser
AccTekLaser cung cấp thiết bị cắt laser CO2 có độ chính xác cao, hỗ trợ lấy nét thông minh, tối ưu hóa đường đi tự động và kiểm soát khí phụ trợ hiệu quả để đảm bảo chiều rộng vết rạch tối thiểu và đạt được độ chính xác trong gia công. Liên hệ chúng tôi để có được giải pháp cắt laser tùy chỉnh nhằm cải thiện hiệu quả sản xuất và độ chính xác gia công của bạn!
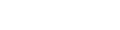
Thông tin liên lạc
- [email protected]
- [email protected]
- +86-19963414011
- Số 3 Khu A, Khu công nghiệp Lunzhen, Thành phố Yucheng, Tỉnh Sơn Đông.
Nhận giải pháp Laser