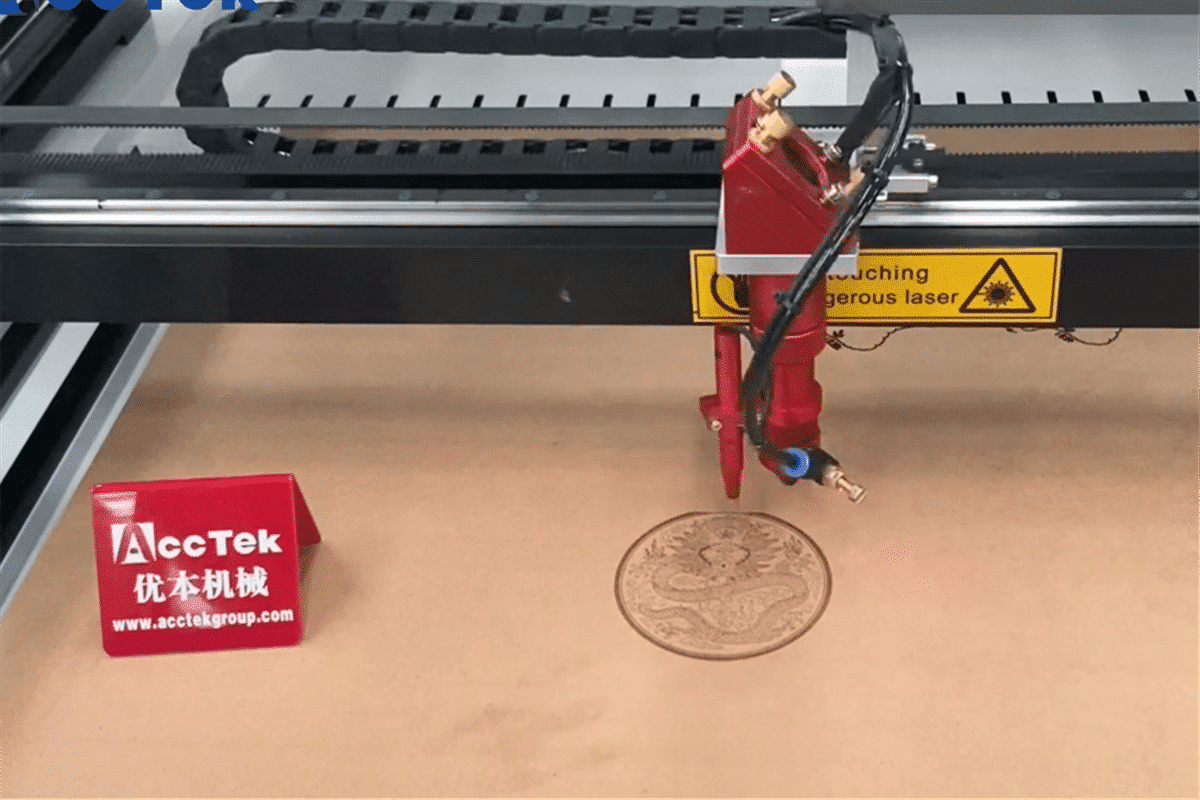
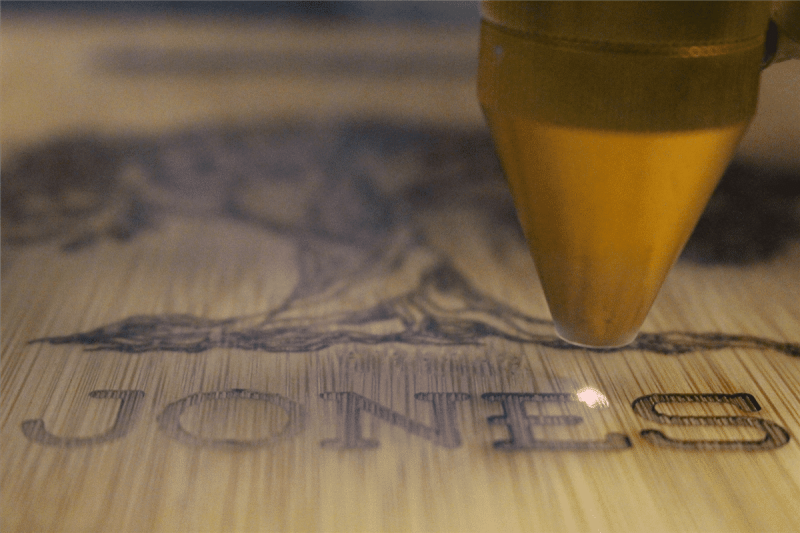
How CO2 Laser Cutting Machine Works
Working principle of CO2 laser cutting machine
The working principle of a CO2 laser cutting machine is to use carbon dioxide (CO2) gas mixture as the active medium to generate a high-power laser beam that can cut various materials. The laser beam is then focused and directed onto the workpiece to cut or engrave various materials. The working principle of the CO2 laser-cutting machine involves several key steps:
- Laser medium: The core of the CO2 laser cutting machine is the laser medium, which is a mixture of carbon dioxide (CO2), nitrogen (N2), and helium (He). This gas mixture is sealed inside a laser tube, usually a long glass tube with mirrors at each end.
- Energy input: The gas mixture is excited by applying a high-voltage discharge to the gas inside the laser tube. This discharge ionizes the gas atoms, producing a population inversion. In short, it energizes the gas to put it in a higher energy state.
- Gross inversion: When gas atoms are excited, some electrons are lifted to a higher energy level. These excited electrons are in an unstable state and tend to return to their original lower energy levels, releasing photons (particles of light) in the process. This emission of photons results in a population inversion, where there are more molecules in higher energy states than in lower energy states.
- Photon Emission: When excited electrons return to a lower energy level, they emit photons. These photons are in the form of laser light, with a specific wavelength (typically in the far-infrared to mid-infrared range, about 10.6 microns for CO2 lasers).
- Optical Resonator: The laser tube is designed as an optical resonator with two mirrors placed at each end. One mirror is fully reflective, while the other is partially reflective. Partial mirrors allow a portion of the generated laser light to escape as a laser beam.
- Zooming in: Photons released during population inversion bounce back and forth between the mirrors, continually stimulating more excited gas molecules to release more photons. This results in the amplification of the light energy, producing a coherent and intense laser beam.
- Laser Beam Forming: Partially reflective mirrors allow the amplified laser light to exit the laser tube in the form of a concentrated high-power laser beam form laser beam. The properties of the CO2 gas mixture determine the wavelength of the laser, which is typically around 10.6 microns in the infrared spectrum.
- Focusing Optics: The laser beam is directed through a series of focusing optics, including lenses or mirrors, to concentrate energy into a very small spot size. This focused beam enables the precise cutting of materials.
- Matter interaction: When a focused laser beam interacts with a material surface, the intense energy causes localized heating. This heat causes the material to vaporize, melt, or be removed by ablation, depending on the properties of the material and the laser parameters used.
- Cutting Process: The laser beam can effectively cut the material by moving the material or the laser beam along a programmed path. The material absorbs the laser energy, causing it to heat up rapidly and be removed layer by layer.
- Computer control: The CO2 laser cutting machine is controlled by a computer, which precisely directs the movement of the laser head and adjusts the power, speed, and other parameters of the laser. This computer control allows complex and precise cutting or engraving on a variety of materials.
Working steps of CO2 laser cutting machine
Modern CO2 laser cutting machines are CNC machines that involve several basic steps in performing the cutting.
- Ready to design. The design consists of a digital file that graphically represents the desired cut. This is one of the most critical steps in the CO2 laser cutting process, as any mistakes here will be reflected in the final cut shape. You can use a variety of free and paid laser cutting software to prepare designs (CAD), convert designs to G-code (CAM) and interact with the laser cutter.
- Setting parameters. CO2 laser cutting machines can be used to cut various materials such as wood, paper, plastic, acrylic, metal, etc. The key to successfully performing every cutting task is setting the optimal laser parameters according to the type of material. Cutting tests with a portion of the material can help to find the optimum laser parameters to produce the best results for the desired application.
- Prepare the workpiece. Once tests have been performed and the optimum parameters for the desired material have been determined, the workpiece is ready for laser cutting.
- Execute the cut. Once the workpiece is prepared, you can place it on the table and perform the cut. Although CO2 laser cutting is an automated cutting process, it is highly recommended to monitor the cutting process to avoid accidents.
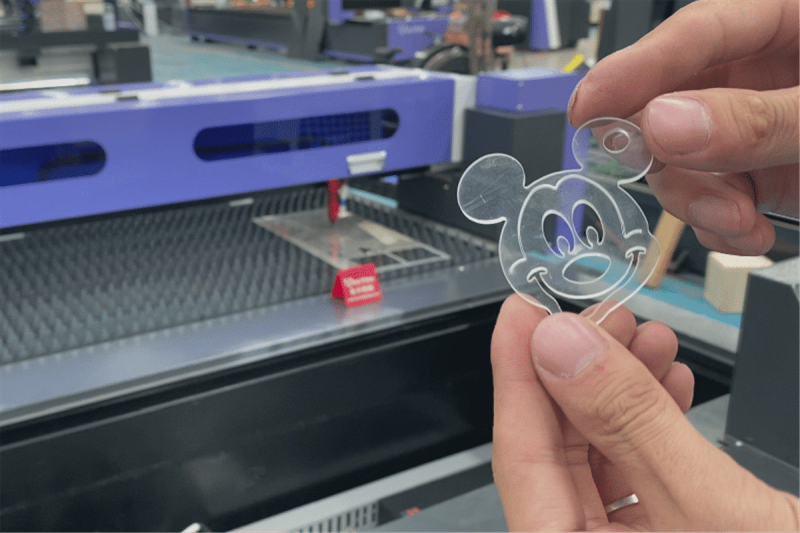
Advantages of CO2 Laser Cutting Machine
CO2 laser cutting machine offers several advantages that make them a popular choice for a variety of cutting and engraving applications. Here are some key advantages of using a CO2 laser cutting machine:
- Versatility: the CO2 laser cutting machine can cut a wide variety of materials including metals (ferrous and non-ferrous), plastics, acrylics, wood, textiles, leather, paper, glass, and more. This versatility allows for diverse cutting applications in various industries.
- PRECISION AND ACCURACY: CO2 laser generators can produce an extremely focused narrow beam, resulting in a high level of cutting precision and accuracy. This precision makes it ideal for intricate and detailed designs, fine carvings, and delicate work.
- Narrow kerf width: The diameter of the focused laser beam is very small, resulting in a narrow cut width (kerf width). This minimizes material loss and increases material utilization, effectively saving material, especially when cutting expensive or valuable materials.
- Non-contact cutting: CO2 laser cutting is a non-contact process. The laser beam does not physically contact the material being cut, reducing the risk of damage and contamination. This is especially beneficial for delicate materials or those with sensitive surfaces.
- No Tool Wear: Unlike traditional mechanical cutting methods, CO2 laser cutting machines have no physical tools to wear out over time. This reduces maintenance costs and downtime associated with tool changes.
- Speed and efficiency: CO2 laser cutting is a fast process, and the speed can be adjusted to balance cut quality and productivity. It can achieve high cutting speeds while maintaining good edge quality, which is especially beneficial for high-volume manufacturing processes.
- Minimal Heat Affected Zone (HAZ): CO2 laser generators generate a focused and controlled source of heat with minimal heat transfer to the surrounding area. This results in a smaller heat-affected zone (HAZ) in the material being cut, reducing the risk of warping, deforming, or damaging adjacent areas.
- Clean cuts and edges: CO2 laser cutting typically produces clean, smooth edges that require minimal or no additional finishing. This saves time and resources in post-processing steps such as deburring or grinding compared to traditional cutting methods.
- Complex Shapes and Designs: CO2 laser cutters can cut complex shapes that may be challenging or impossible with traditional cutting methods. This is especially useful for art and decorative applications.
- Design Flexibility: The precision and versatility of CO2 laser cutting allow for complex designs, allowing for quick adjustments and design changes without tooling changes. This makes them ideal for customization and small-scale production.
- Environmentally friendly: CO2 laser cutting machines produce minimal waste as the cut material evaporates or melts. This reduces waste and environmental impact compared to some other cutting methods.
- Automation and precise control: CO2 laser cutting machines can be easily integrated into automated manufacturing processes. Computer controls allow for high-speed, consistent production while allowing easy design adjustments.
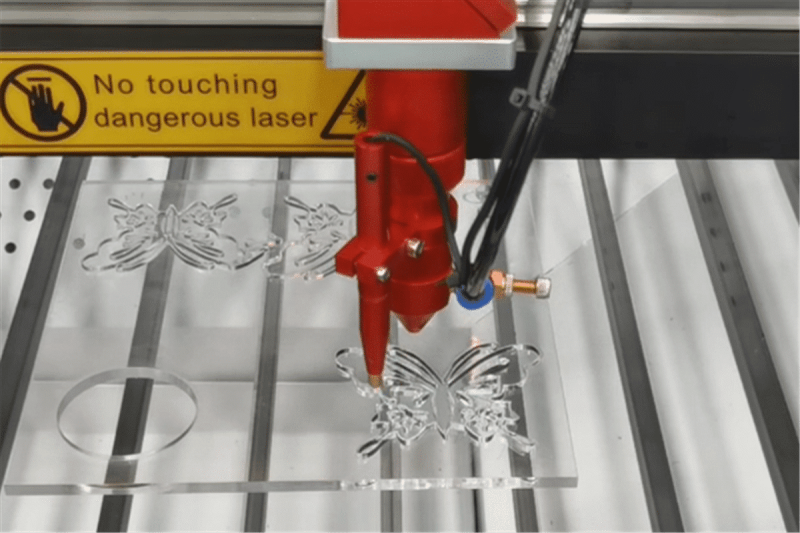
Which industries can CO2 laser cutting machines be applied in
CO2 laser cutting machine is used in most modern industries because they provide a low-cost, high-speed, high-precision cutting method. Some common industries that use CO2 laser-cutting machines are listed below.
- musical instrument industry. Instruments must be manufactured with high precision to achieve the high level of sound quality required by professionals. CO2 laser cutting is an ideal method for precision dimensional processing. Wood is a commonly used material in musical instruments. CO2 laser cutting machines can be used to cut the basic panels that make up musical instruments such as guitars and violins and can also engrave artistic patterns on the surface of finished musical instruments to increase the aesthetics and various style elements of the musical instrument.
- furniture industry. CO2 laser cutting machine can efficiently cut wood boards to assemble furniture. You can also create furniture items like doors, tables, and chairs with a CO2 laser cutter.
- Garment Industry. The CO2 laser cutting machine can cut the fabric with high precision without contact with the material, ensuring that the fabric has no burrs or abrasions during processing. This gives it a great advantage in cutting cloth. The CO2 laser cutting machine can effectively cut single or multi-layer fabric materials, and your work will be completed faster.
- Advertising industry. The application of CO2 laser-cutting machines in the advertising industry is very common. In the advertising industry, acrylic material is one of the most widely used raw materials. Acrylic sections cut with a CO2 laser beam are smooth and polished, so no further processing is required. If you’re engraving text or graphics on acrylic, you can get both matte and frosted finishes. This makes them look very distinctive.
- model production industry. CO2 laser cutting machines are widely used in companies that manufacture architectural models. They often need to cut complex shapes in thin sheet materials. Most of the models use acrylic sheets, which cut very well with CO2 laser cutting equipment.
- Leather processing industry. A CO2 laser cutter can cut and engrave patterns on leather used to make bags, belts, shoes, and more. Laser-cutting machine technology minimizes the possibility of material deformation during leather processing, resulting in perfect cut edges.
- art industry. It is common for beginners and even professionals to use a CO2 laser cutter to cut wood for assembly, engrave gifts, and carve intricate patterns into a piece of wood. Or use a CO2 laser cutter to cut acrylic to create some stunning artwork.
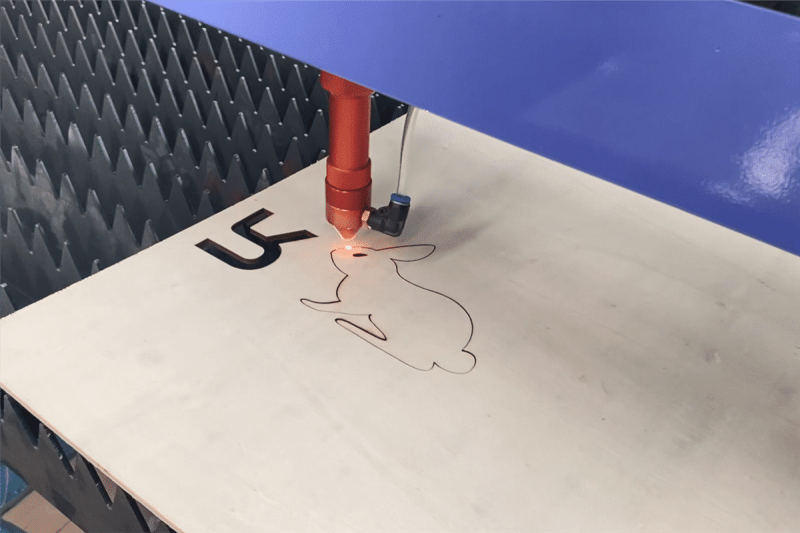
What should be paid attention to when using a CO2 laser cutting machine
Safety Specifications for CO2 Laser Cutting Machines
- Before using the CO2 laser cutting machine, the operator should read the user manual first to understand how to operate the machine safely.
- Make sure someone is watching while cutting and carving. Safety is very important, CO2 laser cutting machines are often used to cut wood and acrylic, these materials are very flammable. Therefore, when the CO2 laser cutting machine is cutting and engraving, it must be ensured that staff members are watching over the machine. Once an unexpected situation occurs during the operation of the machine, it is necessary to turn off the power immediately, which allows you to avoid losses.
- Before the laser cutting machine works, the laser tube must be filled with circulating water. The quality and temperature of the circulating water directly affect the service life of the laser tube. It is recommended to use pure water and keep the water temperature below 35°
- Laser safety glasses should be worn when operating a CO2 laser cutting machine. These lenses are tinted to absorb laser light and prevent it from damaging the operator’s eyes.
Routine maintenance of CO2 laser cleaning machine
- Laser lens cleaning. After the laser machine has been cutting for 8 hours a day, it is necessary to check the lens and clean it if necessary. The optics are located directly above the laser beam, which means they are exposed to a lot of dust, smoke, and debris. If the lens is dirty, the cutting speed of the laser machine will be reduced, and even the cutting will be uneven or the engraved image will be blurred. If it is not cleaned for a long time, the dirt may permanently damage the lens. Therefore, lens cleaning is very important.
- Clean the laser cutter fan. When machines cut and engrave acrylic, MDF, and wood, it is inevitable to generate fumes, dust, and debris. Regular maintenance of the fan unit is therefore essential as any buildup will impede its function (unless a smoke filter is fitted). To do this: disconnect the fan from the power supply, remove the suction hose, and clean the impeller fan and duct with a soft brush.
- Pay attention to the cooling of the laser tube. If your laser cutting machine uses a water tank for cooling, please pay attention to cleaning the water tank regularly. Specific method: First, turn off the power, remove the water inlet pipe, let the laser tube automatically enter the water tank, open the water tank, and pump water to remove the dirt on the water pump. Clean the water tank, replace the circulating water, return the water pump to the water tank, insert the connecting pipe into the water inlet of the water pump, and arrange the joints. Use the pump power alone and run for 2 to 3 minutes (the laser tube is filled with circulating water). If you are using a chiller to cool the laser tube, you will need to keep an eye on the chiller performance and monitor the temperature indication on the chiller display. Every few weeks, find the filter in the cooler and remove any built-up trash. Check for water contamination and replace as necessary.
Summarize
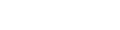
- [email protected]
- [email protected]
- +86-19963414011
- No. 3 Zone A, Lunzhen Industrial Zone,Yucheng City , Shandong Province.