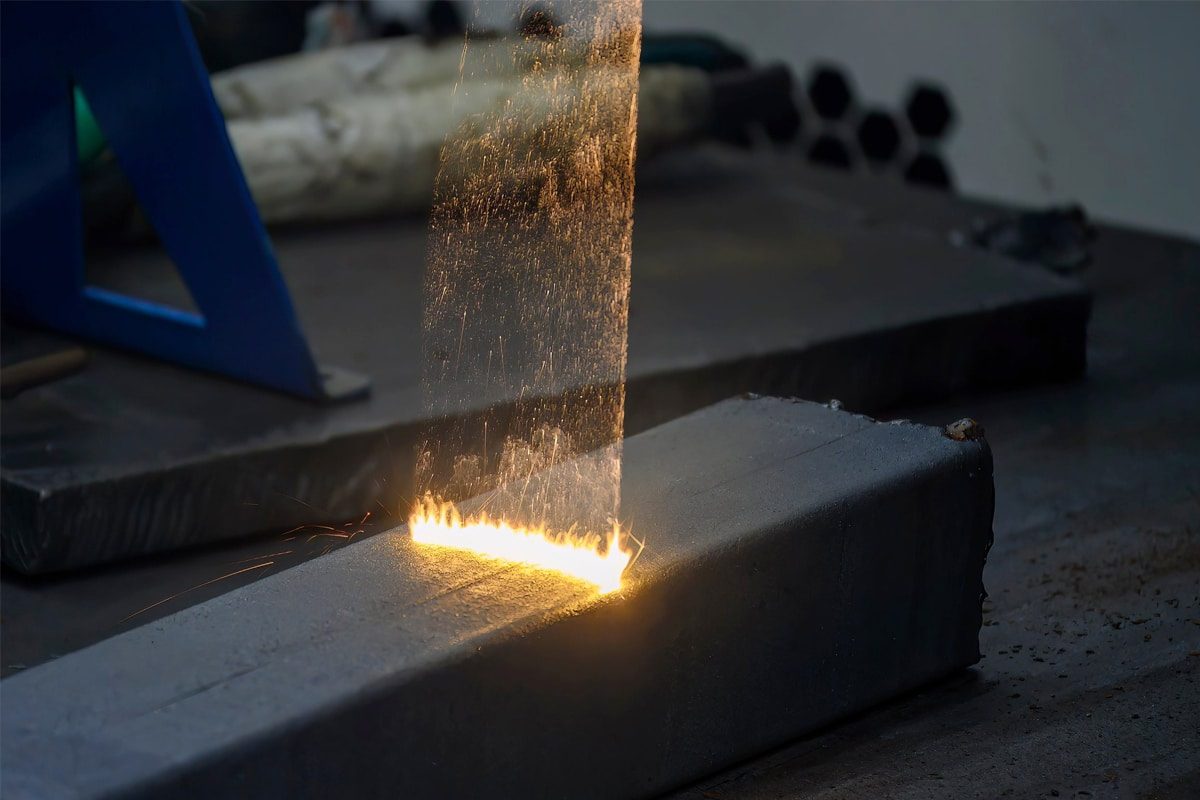
What Are The Applications of Laser Cleaning Machines?
In today’s rapidly advancing industrial landscape, the demand for efficient, precise, and environmentally friendly cleaning solutions is at an all-time high. Traditional cleaning methods often involve abrasive techniques or harmful chemicals that can damage surfaces and pose environmental risks. Enter laser cleaning machines—a cutting-edge technology that offers a non-contact, eco-friendly alternative for removing contaminants, rust, paint, and other unwanted materials from a variety of surfaces. This article delves into the diverse applications of laser cleaning machines, highlighting how they are revolutionizing industries by improving efficiency, reducing costs, and promoting sustainability.
Table of Contents
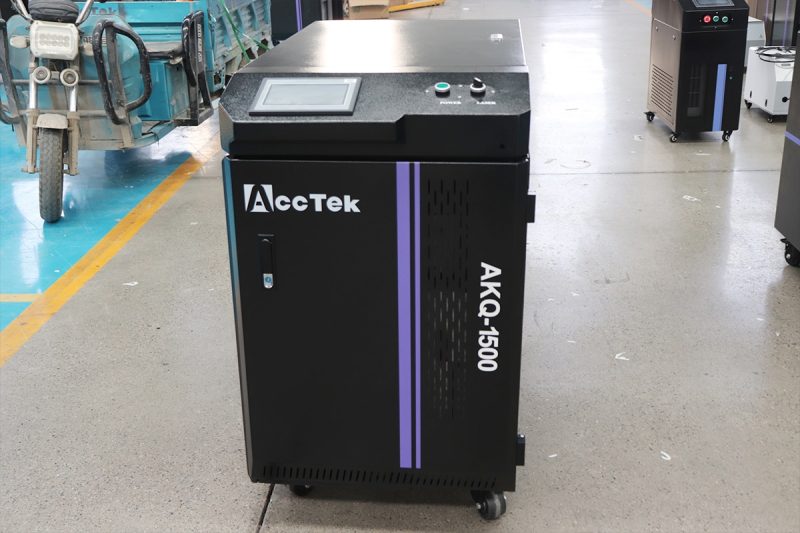
How Laser Cleaning Machines Work
Basic Principles of Laser Cleaning
Laser cleaning is a non-contact and non-abrasive process that uses laser beams to remove contaminants from surfaces without damaging the underlying material. The process works by focusing a high-energy laser beam on the surface to be cleaned. When the laser hits the contaminant layer, it rapidly heats it, causing the material to vaporize, sublimate, or break down into smaller particles, which can then be blown away or extracted. This selective process ensures that only the unwanted material is removed while preserving the base surface, making it ideal for delicate and sensitive applications.
One of the key benefits of laser cleaning is its precision and control. Operators can adjust laser settings such as wavelength, pulse duration, and intensity to target specific contaminants. This makes it suitable for a wide range of applications, from rust removal on industrial machinery to paint stripping on aircraft, and even the delicate cleaning of historical artifacts.
Types of Lasers Used
Two primary types of lasers are used in laser cleaning machines: pulse lasers and continuous lasers, each offering distinct advantages depending on the application.
Pulse Lasers
Pulse lasers emit laser beams in short bursts or pulses, with high peak energy during each pulse. This high-energy pulse vaporizes the contaminants quickly while minimizing heat transfer to the underlying material. As a result, pulse lasers are particularly useful for cleaning sensitive surfaces, such as removing rust or oxides from delicate components in electronics or aerospace applications. The precision of pulse laser cleaning machines also makes them ideal for applications where surface integrity is critical, such as heritage restoration or fine metal cleaning.
Continuous Lasers
Continuous lasers emit a steady, uninterrupted beam of laser energy. These lasers are typically used in applications where higher cleaning speeds are required, and the substrate material can handle more heat. Continuous laser cleaning machines are often used for heavy-duty industrial applications like large-scale rust removal, cleaning welding surfaces, or preparing metal parts for coating. They offer greater cleaning efficiency for tasks that require significant material removal or for treating larger surface areas.
Both pulse and continuous lasers offer distinct advantages depending on the application, making laser cleaning machines highly versatile for a variety of industries.
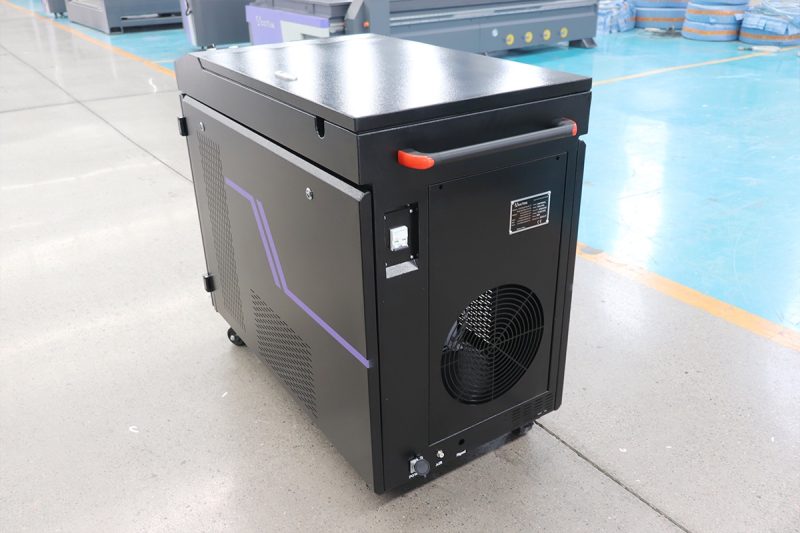
Applications of Laser Cleaning Machines
Rust Removal
Rust is a common issue in industries such as automotive, marine, and construction, where metal components are exposed to moisture and oxygen. Laser cleaning machines provide an effective solution for rust removal, offering precision and efficiency without damaging the base material. The laser targets the rust layer, heating and vaporizing it while preserving the integrity of the underlying metal. This process is particularly beneficial in industries where maintaining the structural integrity of components is crucial, such as in shipbuilding or automotive maintenance.
Paint Removal
Laser cleaning is also widely used for paint removal in industries like aerospace, automotive, and manufacturing. Traditional paint removal methods often involve harsh chemicals or abrasive techniques that can damage the surface. Laser cleaning machines, however, allow for controlled, non-invasive paint removal. The laser selectively removes the paint layer without affecting the substrate material, making it ideal for removing coatings from sensitive surfaces such as aircraft or delicate machinery parts. Additionally, laser cleaning offers a more eco-friendly alternative by eliminating the need for chemical solvents.
Surface Preparation
Proper surface preparation is essential for processes such as welding, coating, or bonding. Contaminants like rust, oxides, oil, and dirt can weaken the strength of welds or adhesive bonds. Laser cleaning machines are highly effective for surface preparation, as they remove these impurities without introducing new contaminants or damaging the surface. By creating a clean and even surface, laser cleaning enhances the quality and durability of welds, coatings, and adhesives, making it indispensable in industries like manufacturing, automotive, and aerospace.
Cleaning of Molds
Mold cleanliness is a critical factor in the quality of products in the plastics and rubber industries. Residues like release agents and build-up from production processes can accumulate in molds, affecting product quality and increasing maintenance downtime. Laser cleaning machines offer a fast and effective method for cleaning molds without the need for abrasive tools or chemicals. This not only improves the quality of the finished product but also extends the lifespan of the molds by reducing wear and tear. Laser cleaning can be used on a variety of mold types, including those used in injection molding, die casting, and extrusion processes.
Oil and Grease Removal
Heavy machinery and industrial equipment often accumulate oil, grease, and other lubricants, which can lead to reduced efficiency or failure over time. Laser cleaning machines provide a non-contact and chemical-free method of removing oil and grease from mechanical parts. The laser targets the contaminant, breaking it down and evaporating it from the surface, without causing any damage to the component. This application is especially useful in industries such as manufacturing, aerospace, and automotive, where cleanliness and maintenance are critical for optimal performance.
Oxide Layer Removal
In metal processing and manufacturing, oxide layers often form on the surface of components during welding, casting, or exposure to air. These layers can interfere with electrical conductivity, adhesion, or surface quality. Laser cleaning machines are highly effective at removing oxide layers without damaging the underlying metal. This application is particularly important in industries like electronics, where clean metal surfaces are essential for high-quality electrical connections, and in manufacturing processes that require pristine surfaces for coating or bonding.
Nuclear Decontamination
Laser cleaning has become a valuable tool in the nuclear industry for decontaminating radioactive surfaces. Radioactive particles can accumulate on surfaces within nuclear power plants and other facilities, posing significant safety and environmental risks. Laser cleaning machines can safely and efficiently remove radioactive contaminants without generating additional hazardous waste. The precision of laser cleaning allows for selective decontamination, targeting only the contaminated layers while leaving the base material intact. This application is critical for maintaining safety and compliance in the nuclear industry, where minimal waste and precision are essential.
Each of these applications showcases the versatility and efficiency of laser cleaning machines, making them a valuable tool across various industries. Whether it’s rust removal, surface preparation, or nuclear decontamination, laser cleaning provides a precise, eco-friendly, and cost-effective solution to meet the demands of modern industrial processes.
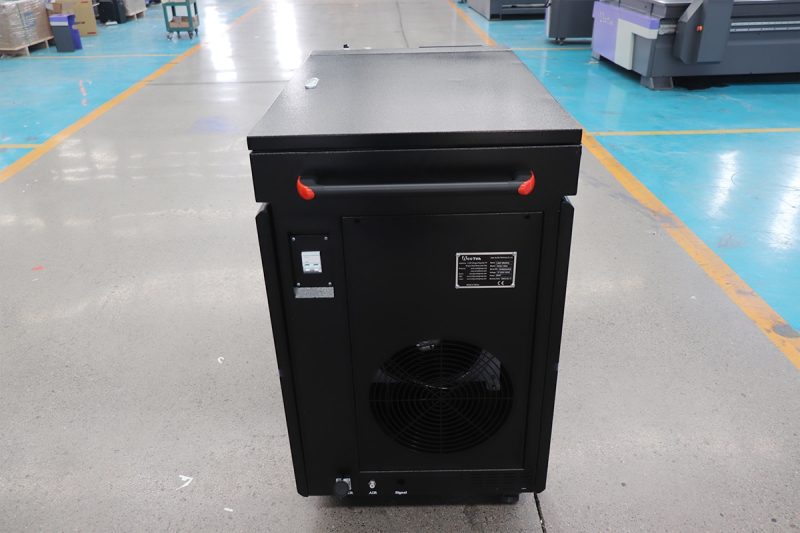
Application Industries of Laser Cleaning Machines
Automotive Industry
The automotive industry uses laser cleaning machines to remove rust, grease, and paint from metal components during maintenance and repair operations. These machines prepare surfaces for welding and coating, ensuring optimal adhesion and high-quality welds. Laser cleaning’s precision makes it suitable for delicate tasks such as cleaning engine parts, transmission systems, or brake components without causing damage, which is essential for maintaining safety and performance standards.
Aerospace Industry
In the aerospace sector, laser cleaning plays a vital role in paint removal, surface preparation, and part maintenance. It enables precise removal of coatings from aircraft without damaging the lightweight metals or composites used in construction. Laser technology is also used to remove contaminants and oxides from critical parts, such as turbine blades and fuselage sections, enhancing component performance and extending their lifespan while ensuring compliance with strict safety regulations.
Manufacturing and Metal Processing
Manufacturing industries utilize laser cleaning to remove oxides, oils, and residues from metal surfaces before processes such as welding, coating, or bonding. Laser cleaning ensures consistent surface preparation, improving product quality and reducing failure rates. In metal processing, it helps clean molds, tools, and machinery components, extending equipment life and minimizing downtime. The versatility of laser cleaning makes it suitable for both large-scale production environments and precision applications.
Cultural Heritage and Conservation
Laser cleaning is widely employed in the restoration of cultural artifacts, monuments, and historical buildings. The non-contact nature of laser technology allows for the gentle removal of dirt, grime, biological growth, and aged coatings without damaging the underlying material. Conservation specialists use laser cleaning to restore the original appearance of statues, paintings, and metalworks, preserving their historical integrity while maintaining strict control over the cleaning process.
Electronics and Semiconductor Industry
In the electronics and semiconductor industries, laser cleaning is used to remove oxide layers, dust, and other microscopic contaminants from components. Precision cleaning is essential in these sectors, as even tiny particles can affect the functionality of circuits and semiconductors. Laser cleaning ensures that surfaces remain pristine for subsequent processes, such as soldering or coating, contributing to the reliability and performance of electronic devices.
Nuclear Industry Applications
The nuclear industry relies on laser cleaning machines for decontamination tasks, where radioactive particles accumulate on equipment and surfaces. Laser technology allows for the safe and efficient removal of these contaminants, minimizing waste and environmental risks. The ability to precisely target only the contaminated areas ensures that the underlying materials remain intact, improving safety and compliance while reducing the complexity of waste disposal.
Shipbuilding and Marine Industry
In shipbuilding and marine applications, laser cleaning is used to remove rust, corrosion, and old paint from ship hulls, decks, and components. The harsh marine environment accelerates corrosion, making maintenance a constant challenge. Laser cleaning provides an efficient way to prepare surfaces for repainting or repair, ensuring the structural integrity of vessels and preventing long-term damage caused by rust and saltwater exposure.
Tire and Rubber Industry
In the tire and rubber industry, molds accumulate residues from sulfur, rubber, and release agents, affecting product quality and efficiency. Laser cleaning offers a quick and effective solution for cleaning molds without using abrasive tools or chemicals. This helps maintain high production standards, extend mold life, and reduce downtime. The non-contact nature of laser cleaning ensures that molds retain their precise dimensions and performance over extended use.
Precision Engineering and Micro-Mechanical Applications
Precision engineering industries, such as watchmaking and micro-mechanics, require extremely accurate cleaning methods for small, intricate components. Laser cleaning is ideal for these applications, as it removes contaminants without causing mechanical damage or altering surface geometry. It is used to clean gears, springs, and other tiny components, ensuring optimal performance and extending product life. Additionally, laser cleaning is valuable in medical device manufacturing, ensuring surgical instruments are free from contaminants.
From large-scale industrial applications to delicate restoration work, laser cleaning technology helps businesses achieve better results with lower environmental impact, improved efficiency, and longer equipment lifespans.
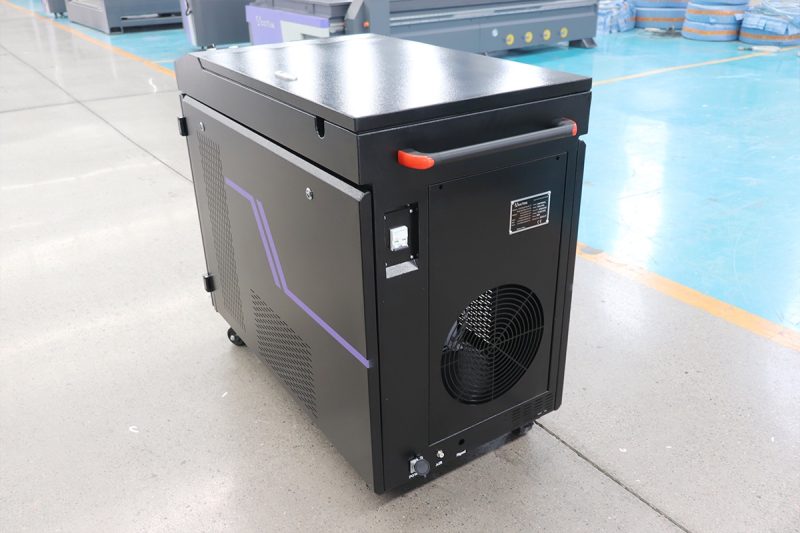
Advantages of Using Laser Cleaning Machines
Non-Contact Process
Laser cleaning is a non-contact technology, meaning the laser beam interacts only with the surface contaminants, leaving the underlying material untouched. This prevents mechanical stress, scratches, or wear on the surface, making it ideal for cleaning delicate components or intricate parts. The absence of physical contact also ensures consistent results, reduces maintenance, and extends the lifespan of tools and equipment.
Environmentally Friendly
Traditional cleaning methods often rely on chemicals, abrasive materials, or solvents, which can create hazardous waste and pollute the environment. In contrast, laser cleaning is an eco-friendly solution that eliminates the need for such materials. The process produces minimal waste, often only in the form of vaporized contaminants, and significantly reduces the environmental footprint. This makes laser cleaning particularly attractive for industries aiming to meet strict environmental regulations.
Precision and Control
Laser cleaning machines provide unparalleled precision, allowing operators to adjust parameters such as laser intensity, wavelength, and pulse duration. This high level of control ensures that only the contaminant is removed, making it ideal for applications that require delicate cleaning, such as restoration work or cleaning small electronic components. The precision also allows for selective cleaning of complex surfaces, edges, and corners, which may be difficult to reach using traditional methods.
Minimal Substrate Damage
One of the key advantages of laser cleaning is its ability to remove contaminants without damaging the substrate. Since laser energy is absorbed primarily by the surface material to be removed, the base material remains intact. This is particularly important for industries such as aerospace and electronics, where maintaining the integrity of the surface is critical for safety and functionality.
Cost-Effectiveness Over Time
While the initial investment in a laser cleaning machine can be higher than traditional cleaning equipment, the long-term savings are significant. Laser cleaning machines reduce ongoing costs by eliminating the need for consumables like chemicals, abrasives, and cleaning agents. They also reduce maintenance and downtime, improving overall productivity. Additionally, the efficiency and precision of laser cleaning often lead to fewer defects, which lowers the cost of rework and quality control.
Safety and User-Friendliness
Laser cleaning machines are designed with safety and ease of use in mind. Many machines come equipped with features such as interlock systems, emergency stop buttons, and safety enclosures to protect operators. Since laser cleaning reduces the need for hazardous chemicals, it also minimizes health risks associated with chemical exposure. Furthermore, user-friendly interfaces and automated functions make the machines easy to operate, requiring minimal training and ensuring consistent results across multiple applications.
With these advantages, laser cleaning machines are becoming the go-to solution for industries seeking precise, efficient, and sustainable cleaning methods.
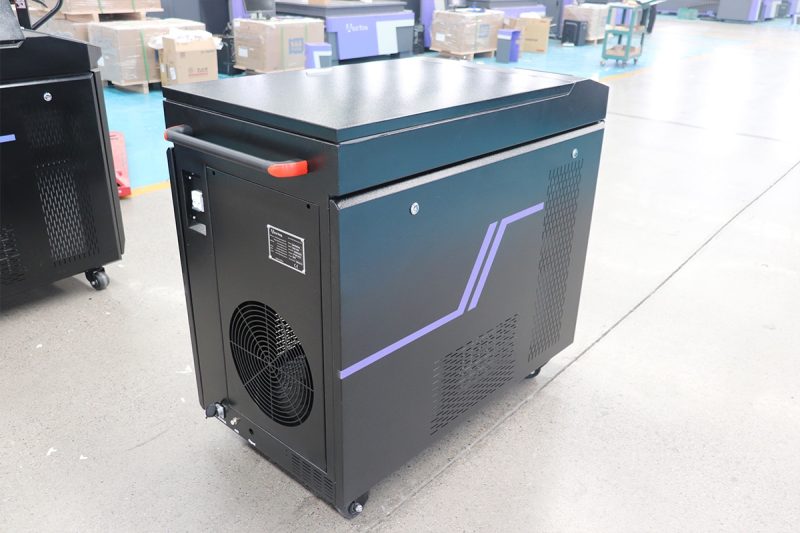
Challenges and Considerations
Initial Investment Costs
Laser cleaning machines typically require a higher upfront investment compared to traditional cleaning methods like abrasive blasting or chemical solvents. However, the long-term savings through reduced maintenance, consumables, and operational downtime often offset this initial cost. Companies must conduct a cost-benefit analysis to determine the return on investment (ROI) and assess whether laser cleaning aligns with their budget and operational needs.
Training Requirements
Operating laser cleaning machines requires proper training to ensure safe and effective use. Operators need to understand how to adjust laser parameters such as power, wavelength, and pulse duration for different materials and contaminants. Furthermore, safety protocols must be followed to prevent laser exposure risks. Businesses must invest in employee training programs to maximize the benefits of the technology.
Material Compatibility
Although laser cleaning is versatile, not all materials respond equally well to laser-based processes. Highly reflective materials, such as certain polished metals, can reflect laser energy, reducing cleaning efficiency. Some materials may require special configurations, such as different wavelengths or additional surface treatment, to achieve optimal results. Understanding the limitations and testing compatibility are essential steps before full-scale implementation.
Laser Safety Considerations
The use of high-powered lasers poses potential safety risks, such as eye and skin exposure. Laser cleaning machines must be operated in compliance with safety regulations, and proper protective equipment (PPE) must be used. Many modern laser cleaning systems come with interlock systems, enclosures, and emergency stop buttons to minimize risks, but maintaining operator awareness and compliance with safety standards remains critical.
Operating Environment Requirements
Laser cleaning machines require a controlled environment for optimal performance. Dust, humidity, or temperature fluctuations in the operating area can affect cleaning precision and efficiency. Some laser systems may also require ventilation or extraction systems to manage fumes generated during the cleaning process, especially when working with certain coatings, paints, or contaminants.
Maintenance and Downtime
While laser cleaning machines typically require less maintenance than abrasive or chemical systems, they still need periodic calibration and component replacement to maintain peak performance. Downtime during maintenance can disrupt production schedules, so businesses must plan and schedule maintenance activities to minimize interruptions.
Application-Specific Constraints
Some industries may encounter unique challenges when adopting laser cleaning. For example, cleaning very large surfaces, such as ship hulls or industrial tanks, may require specialized systems or automation to maintain efficiency. In other cases, complex geometries or hard-to-reach areas may demand customized solutions. Businesses must assess whether laser cleaning can fully meet their specific requirements or if supplementary cleaning methods are needed.
By addressing these challenges and considerations, businesses can better leverage the benefits of laser cleaning machines while ensuring safe, efficient, and cost-effective operations.
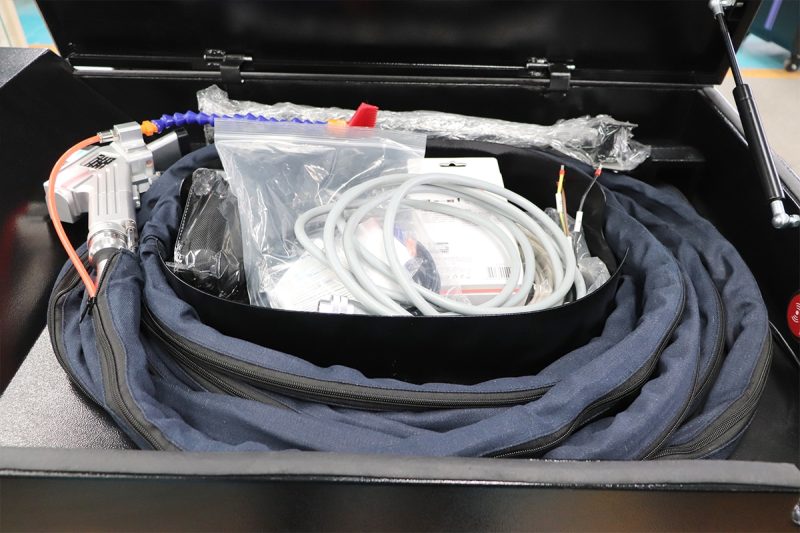
Summary
Laser cleaning machines have revolutionized surface cleaning and preparation by offering a non-contact, eco-friendly, and precise alternative to traditional methods. These machines utilize high-intensity laser beams to remove rust, paint, oil, oxides, and other contaminants without damaging the underlying surface, making them essential for industries requiring precision and cleanliness. Key applications include rust removal in the automotive and marine sectors, paint stripping for aerospace maintenance, and surface preparation for welding and coating in manufacturing. Laser cleaning also plays a crucial role in mold cleaning, nuclear decontamination, and delicate restoration work in cultural heritage conservation.
With advantages such as environmental friendliness, minimal substrate damage, precision, and long-term cost savings, laser cleaning machines are becoming increasingly popular across various industries. However, businesses must also consider factors like the initial investment, material compatibility, and safety requirements.
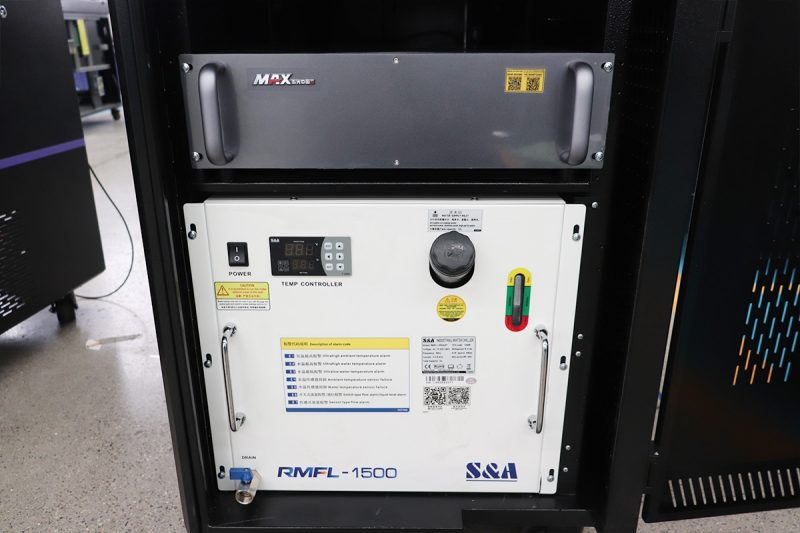
Get Laser Cleaning Solutions
If your business needs efficient, precise, and eco-friendly surface cleaning technology, AccTek Laser offers cutting-edge laser cleaning solutions tailored to meet your specific requirements. As a professional manufacturer of laser cutting machines, laser welding machines, laser cleaning machines, and laser marking machines, AccTek Laser provides a comprehensive range of cleaning systems for various industries. Whether you need to remove rust from automotive parts, strip paint in aerospace applications, clean molds for manufacturing, or safely perform nuclear decontamination, AccTek’s laser cleaning machines deliver exceptional results.
AccTek Laser’s solutions are designed with user-friendliness, safety, and efficiency in mind. With options for both continuous and pulse laser configurations, our machines ensure precise cleaning without damaging the underlying material. We also offer expert consultation, training, and after-sales technical support to help you seamlessly integrate laser cleaning technology into your operations. Trust AccTek Laser to provide advanced, reliable, and sustainable cleaning solutions that enhance your business’s productivity and environmental responsibility.
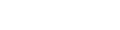
Contact information
- [email protected]
- [email protected]
- +86-19963414011
- No. 3 Zone A, Lunzhen Industrial Zone,Yucheng City , Shandong Province.
Get Laser Solutions