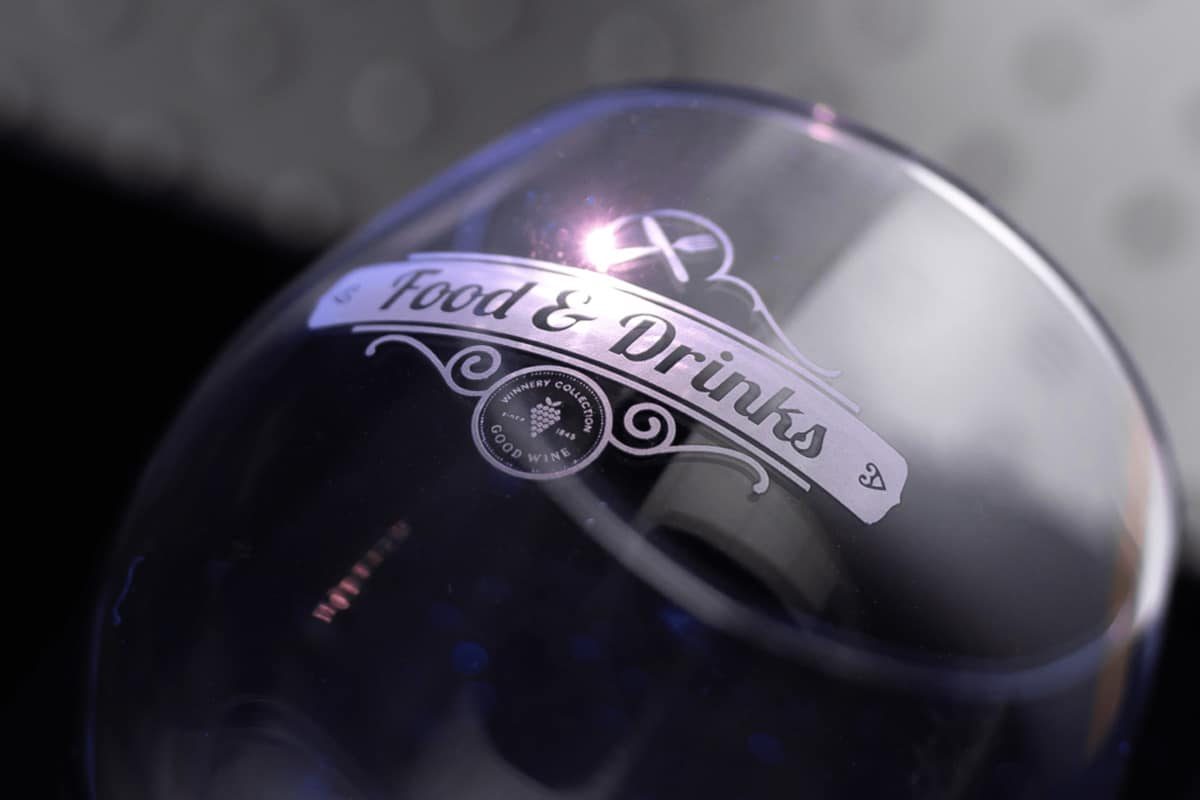
What Are the Common Defects in Laser Marking?
Laser marking is a technology that uses high-energy-density laser beams to perform non-contact processing on the surface of materials. Through the focused laser beam, the surface of the material is rapidly heated or evaporated, forming a permanent mark. This marking method is known for its high accuracy, flexibility and versatile applicability, with the ability to handle a wide range of materials, including metals, plastics, ceramics and glass. Compared with traditional marking machines, laser marking machines require no consumables and the marking effect is more precise and stable.
Table of Contents
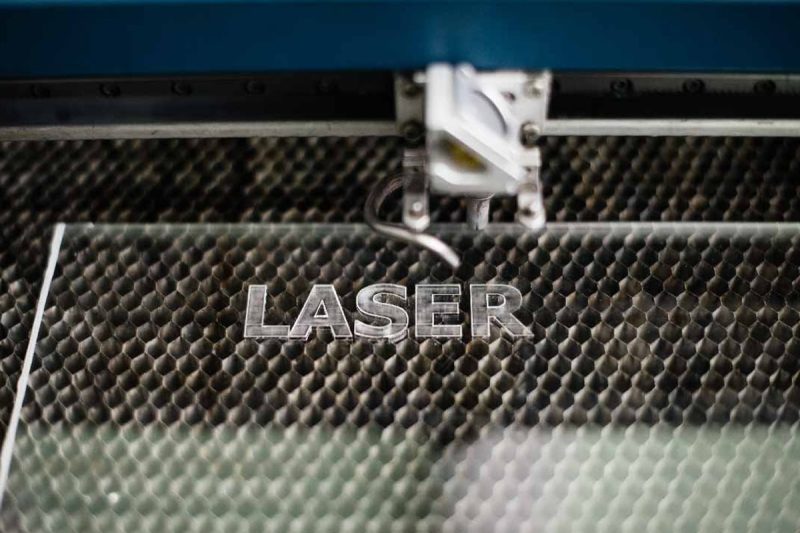
Laser Marking System Overview
The core of laser marking technology lies in different types of laser generators, and the appropriate laser system is selected according to material properties and processing requirements. Common laser types include fiber lasers and CO2 lasers, which have significant differences in application fields and performance.
The Main Differences Between Fiber Laser and CO2 Laser
Fiber Laser
- Laser type: Fiber laser generator excites laser through optical fiber, with high beam quality and high energy conversion efficiency.
- Wavelength: The wavelength of a fiber laser is generally 1.06 microns, which is suitable for processing metals and some hard materials.
Advantages
- High energy conversion efficiency and low energy loss.
- The laser beam has good quality and a strong focusing effect, which is suitable for precision processing.
- Suitable for marking and cutting metal materials (such as stainless steel, aluminum, copper, etc.) and some plastics and ceramics.
CO2 Laser
- Laser type: The CO2 laser generator uses carbon dioxide gas to excite the laser, with a longer wavelength, usually 10.6 microns.
- Wavelength: Compared with fiber laser, CO2 laser has a longer wavelength and is suitable for processing non-metallic materials.
Advantages
- It can produce strong absorption on organic materials and is suitable for processing non-metallic materials.
- The system is relatively mature and widely used in various production environments.
Fiber laser and CO2 laser have their advantages in laser marking. Fiber laser is suitable for metal and high-precision marking, while CO2 laser has advantages in non-metallic materials and large-scale processing. Choosing the right laser system according to processing requirements and material type can improve production efficiency and product quality.
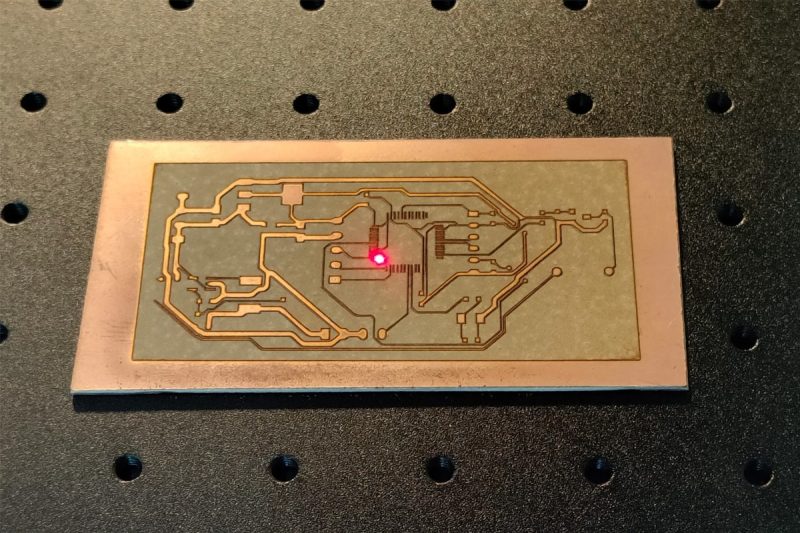
Common Materials for Laser Marking
Common laser marking materials include metals, plastics, ceramics, glass and composite materials. Understanding the characteristics of each material and the appropriate laser technology can not only help improve the marking quality, but also optimize production efficiency.
Laser Marking Characteristics of Metal Materials
Laser marking is widely used in metal materials, especially in common metal materials such as stainless steel, aluminum, copper, titanium, etc., and can achieve fine and lasting marking.
Laser Marking Effect of Plastic Materials
The application of laser marking on plastics is relatively complex. Due to the large differences in thermal reactivity and absorbance of different plastic materials, the marking effect will also be different. Common plastic materials include polycarbonate (PC), polyoxymethylene (POM), acrylic acid (PMMA), etc.
Ceramics and Glass
Ceramics and glass are fragile materials that need special attention to avoid material breakage during laser marking. Although these materials have low laser absorption, very high-quality marking can still be achieved by precisely controlling the power, frequency, and pulse width of the laser.
Composite Materials: Special Requirements for Complex Materials
Composite materials are made of two or more different materials and are commonly used in high-end manufacturing industries such as aerospace, automotive, construction, etc. Laser marking of composite materials requires precise adjustment of laser parameters according to the characteristics of each material to avoid uneven marking caused by thermal expansion or chemical reactions of different materials.
The application of laser marking technology on different materials is extensive and complex. Understanding the marking characteristics and requirements of each material is crucial to selecting the appropriate laser system. By optimizing laser parameters and selecting the appropriate laser type, more efficient, accurate, and lasting marking effects can be achieved to meet the marking quality and accuracy requirements of various industries.
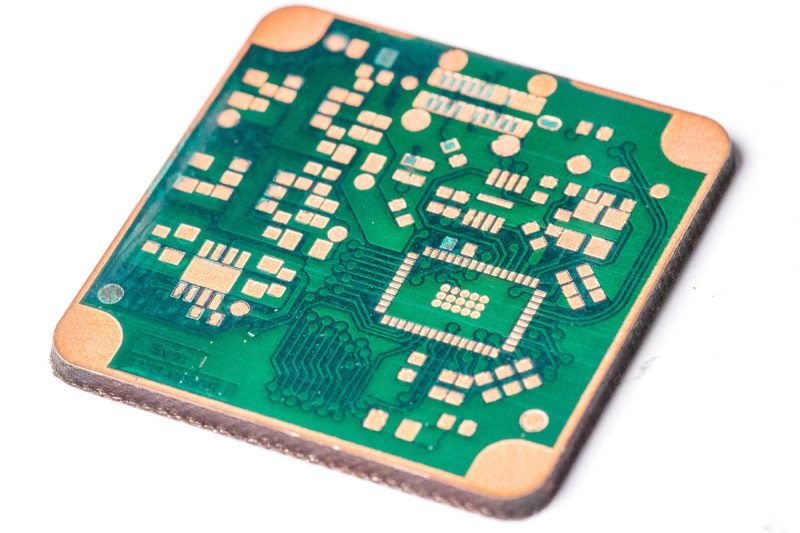
Laser Marking Defects Overview
Laser marking defects mainly come from equipment problems, improper parameter settings, and insufficient material selection and preparation. Equipment problems such as unstable laser power and misaligned beam mode can affect the marking quality. Regular calibration of equipment, cleaning of optical components, and replacement of aging parts can prevent these problems. Improper parameter settings such as too high power or too slow speed can lead to uneven marking. Parameters need to be optimized according to material and process requirements. The absorption rate and surface state of the material also affect the marking effect. Choosing materials compatible with the laser wavelength and ensuring the surface is clean can avoid defects.
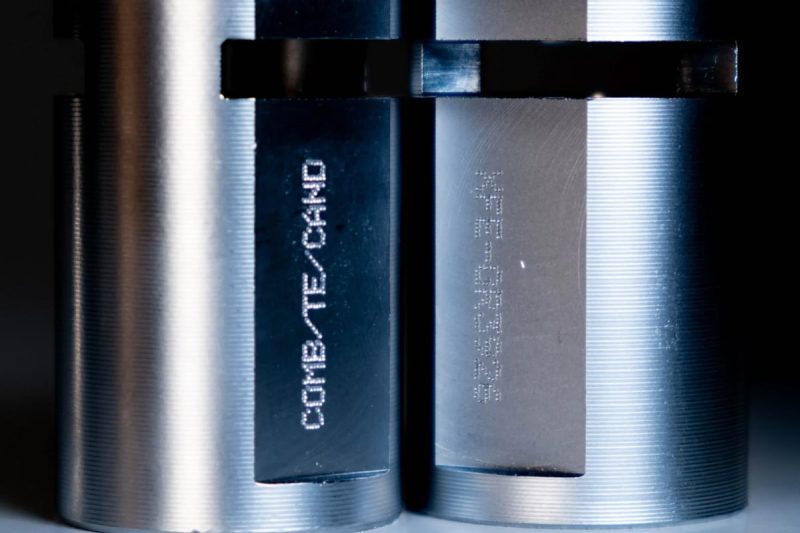
Common Laser Marking Defects and Solutions
Laser marking technology is widely used in many industries due to its high precision and efficiency. However, in actual operation, some common marking defects may occur due to the influence of equipment, parameter settings, material preparation, etc. These defects not only affect the marking effect, but may also have a negative impact on product quality and customer satisfaction. Understanding the root causes of these defects and applying appropriate solutions can significantly improve mark quality.
Burn Marks
Defect description: Burn marks usually appear under high power or improper focus conditions, especially on metals, plastics, and some ceramic materials. These marks usually appear as charred surfaces or overheated areas, which not only affect the appearance but may also affect the structure of the material.
Reason
- The laser power is too high, causing the material surface to overheat.
- Improper focus setting causes the laser beam to be too concentrated or dispersed, causing excessive heat accumulation at a certain point.
Solution
- Adjust power and speed: Reduce laser power or increase scanning speed to reduce heat buildup.
- Adjust focus: Make sure the laser focus is on the surface of the material and avoid over-focusing. Using the appropriate focus setting for the material can avoid overheating.
Incomplete Mark
Defect description: Incomplete marking is usually caused by inaccurate beam alignment or inappropriate laser scanning speed setting. This will make the mark appear uneven or partially missing, affecting the integrity and readability of the mark.
Reason
- The beam is not aligned correctly, resulting in the laser not being able to accurately illuminate the intended location.
- The laser scanning speed is too fast or too slow, resulting in an incomplete or uneven marking area.
Solution
- Calibrate beam alignment: Regularly check and calibrate the alignment of the laser generator to ensure that the laser beam is accurately focused on the marking area.
- Adjust scanning speed: According to the material and marking requirements, adjust the scanning speed of the laser appropriately to avoid too fast or too slow speed affecting the marking effect.
- Optimize process path: When marking complex graphics or text, choose appropriate path planning to ensure that each area is fully covered.
Color Change and Poor Contrast
Defect description: Discoloration and poor contrast are common problems during laser marking, especially on plastic or coated metal surfaces. These defects make the mark unclear and even difficult to identify.
Reason
- Contamination or oil on the surface of the material affects the reflection of the laser, causing the mark to be blurred or discolored.
- Improper laser parameter settings (such as too low power or too fast speed) result in insufficient contrast of the mark, making it difficult to identify.
Solution
- Material surface cleaning: Before marking, make sure that the material surface is free of oil, dust, or other contaminants to ensure that the laser beam can effectively act on the material surface.
- Optimize laser parameters: Adjust laser power, scanning speed, focal length, and other parameters according to the properties of the material to ensure the contrast and clarity of the mark.
- Use coatings or enhancers: For some plastic materials, specific laser marking coatings can be used to improve contrast and marking effects.
Surface Damage and Heat Affected Zone
Defect description: When processing heat-sensitive materials (such as plastics, wood, etc.), excessive laser heat can cause surface damage or heat-affected zones (HAZ). Such defects usually appear as scorching, discoloration or deformation.
Reason
- The laser power is too high or the scanning speed is too slow, resulting in excessive heating.
- Heat-sensitive materials undergo physical or chemical changes when heated.
Solution
- Adjust laser power and scanning speed: Use lower power and higher speed to reduce heat accumulation and avoid overheating of heat-sensitive materials.
- Select the right material: When selecting materials, give priority to those with good thermal stability suitable for laser marking, or use pre-treated materials.
- Heating control system: Use airflow or cooling system to control the heat generated during laser marking and reduce the expansion of the heat-affected zone.
Ghosting, Shadows and Marking Depth Inconsistency
Defect description: Ghosting and shadowing are usually caused by the divergence of the laser beam or errors in the optical system of the equipment. Inconsistent marking depth may also be caused by changes in the focal length of the laser generator, beam divergence, or uneven energy output.
Reason
- Divergence or instability of the laser beam, resulting in ghosting or shadowing of the mark.
- The optical system of the laser generator is not properly calibrated, resulting in an unfocused laser beam, affecting the uniformity of the mark.
- Uneven laser energy output, resulting in inconsistent mark depth.
Solution
- Calibrate the laser generator regularly: Ensure that the optical system and focal length of the laser generator are regularly checked and calibrated to avoid beam instability.
- Adjust the optical system settings: Adjust the focal length and energy output of the laser according to the characteristics of the material and the marking requirements.
- Use a high-precision laser generator: Choose a laser generator with high stability and precision to ensure the marking depth and pattern clarity.
By understanding the common defects in laser marking and their causes, we can take targeted measures to optimize the marking process and improve the quality of the mark. Regular inspection and adjustment of laser equipment, optimization of parameter settings, selection of appropriate materials, and surface preparation methods are all key to ensuring the quality of marking. Through fine adjustment and control, defects can be minimized, production efficiency can be improved and customer satisfaction can be ensured.
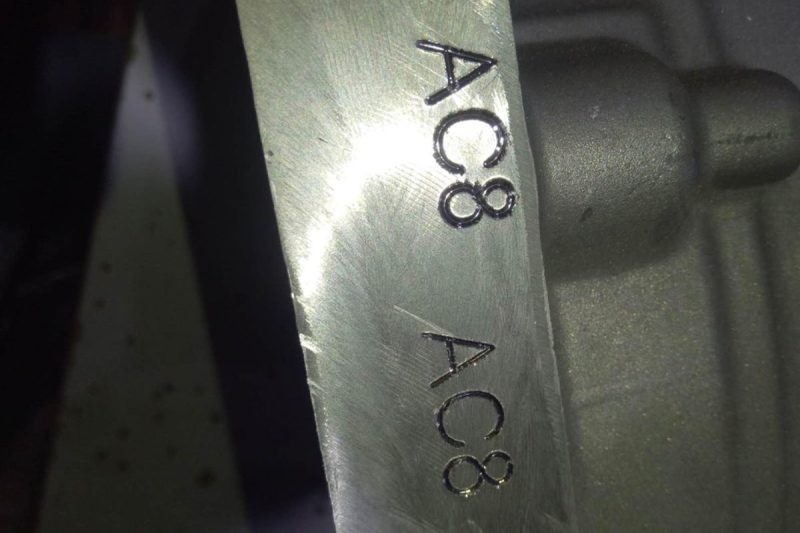
Preventive Measures and Optimization Suggestions
Parameter optimization
Power Settings
- Too high a power may cause the material to overheat, resulting in defects such as burns or deformation.
- Too low a power may result in unclear marking or even no effective marking.
Speed Settings
- Too slow a speed will cause the heat-affected zone to expand, increasing the risk of thermal damage.
- Too fast a speed may result in incomplete marking or uneven surface.
Focus Adjustment
- Accurate setting of the focal length ensures that the laser beam is focused, avoiding over-spreading or over-focusing, thus improving the clarity and consistency of marking.
Optimization Suggestions
- Adjust the power and speed regularly to set the optimal parameters according to different materials and application scenarios.
- Use multiple tests and experimental data to find the best combination of laser power and speed to ensure stable and accurate marking.
Material Preparation
Surface Cleaning
- Before marking, the material surface must be completely cleaned to remove oil, dust, and other contaminants that could affect the precise action of the laser beam.
- Use appropriate cleaning methods such as chemical cleaning, brushing, or blowing to ensure that the surface is free of any obstructions.
Material Compatibility
- Different materials have different laser absorption rates, so make sure you choose a material that is compatible with the laser wavelength. Highly reflective materials such as aluminum and copper require special attention to power and focus settings.
- Be especially careful with brittle materials (such as ceramics and glass), as excessive laser power may cause cracking or damage.
Optimization Suggestions
- Perform material testing before starting marking to ensure that the material can withstand the energy of the laser and avoid defects due to material incompatibility.
- Use materials with good laser compatibility and avoid materials with complex or unstable surfaces.
Equipment Maintenance
Regular Calibration
- The optical system of the laser equipment needs to be calibrated regularly to ensure the accuracy and consistency of the beam. Especially in areas such as focal length, beam collimation, and power output, regular calibration can significantly reduce errors.
- Use professional equipment and tools for calibration to avoid incomplete or blurry marks caused by beam deviation.
Component Inspection and Cleaning
- Optical components such as laser lenses, reflectors, and focusing lenses need to be kept clean to prevent dust or contaminants from affecting laser transmission and marking effects.
- Regularly check the operating status of the laser equipment to ensure there is no mechanical wear or other failures.
Regular Calibration
- Perform a comprehensive inspection of the laser equipment every month or quarter to ensure that all parts of the equipment are in optimal working condition.
- During the use of the equipment, keep the equipment clean and clean the optical components regularly.
Operator Training
Skills Improvement
- Operators should have a solid foundation of laser marking knowledge, and understand the working principle of lasers, material properties, and solutions to various common problems.
- Through simulation training or actual operation, operators’ fault diagnosis capabilities can be improved to ensure quick response to problems in production.
Operational Standardization
- Establish clear operating procedures and standard operating procedures (SOPs) to help operators follow consistency and standardization in their work.
- Operators should review the operating manual regularly and maintain continuous learning of equipment operation.
Optimization Suggestions
- Regular training and skills improvement courses are organized to ensure that operators master the latest laser marking technology and operating skills.
- Introducing an operator qualification certification system to ensure that each operator undergoes a rigorous skills assessment.
Environmental control
Temperature and Humidity Control
- Too high or too low ambient temperature will affect the stability of the laser and thus the marking effect. Excessive humidity may cause equipment failure or damage to the material surface.
- The laser marking studio should maintain stable temperature and humidity to ensure that the laser generator and material are in ideal working condition.
Keep It Clean
- The working environment should be kept clean and tidy to prevent dust, oil, or debris from entering the equipment. Clean the workshop regularly, especially the area where the optical components are located, to ensure that there are no pollutants that affect the marking quality.
Optimization Suggestions
- Install a temperature and humidity control system in the workshop, regularly check environmental conditions, and keep the temperature and humidity within the recommended range.
- Keep the workshop air fresh, and regularly clean and maintain the workspace to avoid dust accumulation.
Laser marking quality is affected by many factors. By optimizing parameters, accurately preparing materials, regular equipment maintenance, operator training and strict environmental control, defects can be reduced, production efficiency and customer satisfaction can be improved. These optimization measures can ensure high accuracy and long-term stability of the marking process, helping companies stand out from the competition.
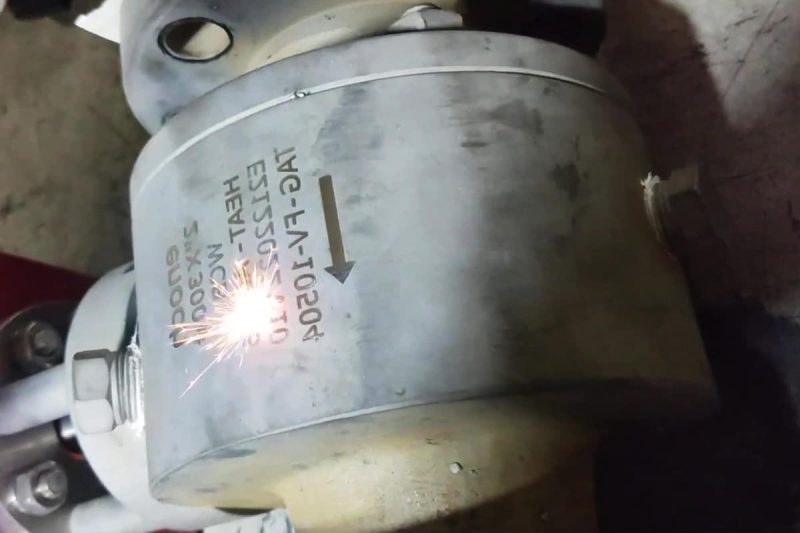
Summarize
Laser marking technology plays an important role in modern manufacturing, but in actual application, some defects are often encountered, such as burn marks, incomplete markings, and surface damage. These problems can be effectively reduced by optimizing the selection of laser equipment, adjusting parameter settings, regular maintenance, and professional training of operators. Reasonable equipment selection and precise parameter settings can not only avoid common defects, but also improve the quality of marking, ensure that the appearance and logo of each product are clear and consistent, and thus enhance the brand image and market competitiveness.
Through these optimization measures, not only can the quality of laser marking be improved, the appearance of products can be enhanced, but also customer satisfaction can be effectively improved. High-quality laser marking not only makes products more attractive but also strengthens customers’ brand loyalty, thus helping enterprises stand out in the fierce market competition and win more customers and market share.
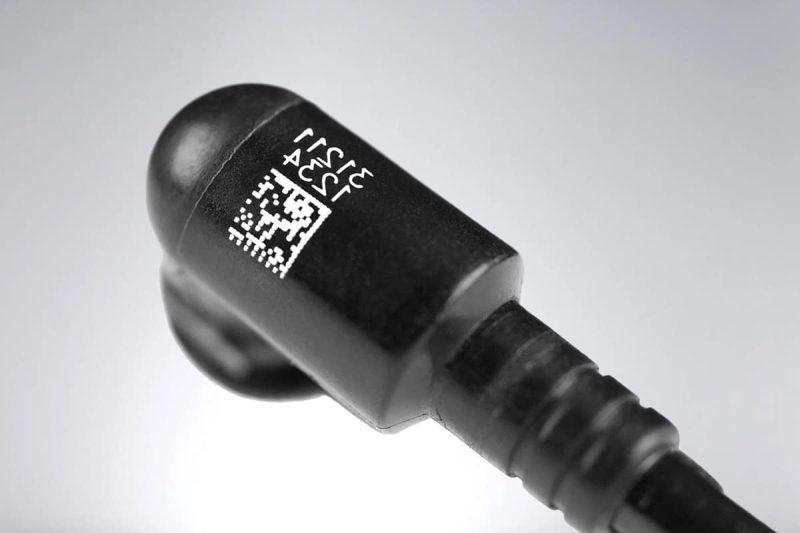
Get Laser Solutions
If you are looking for efficient laser solutions, AccTek Laser provides professional laser technology consulting and customized services to meet your unique needs. Whether it is equipment selection, parameter optimization, or reference for specific application cases, our team of experts can provide you with in-depth guidance to help you achieve the best processing results.
Contact us today to learn more about laser marking, laser welding, and other laser applications. With our consulting services, you will receive personalized solutions to ensure your business remains competitive in the application of laser technology.
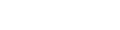
Contact information
- [email protected]
- [email protected]
- +86-19963414011
- No. 3 Zone A, Lunzhen Industrial Zone,Yucheng City , Shandong Province.
Get Laser Solutions