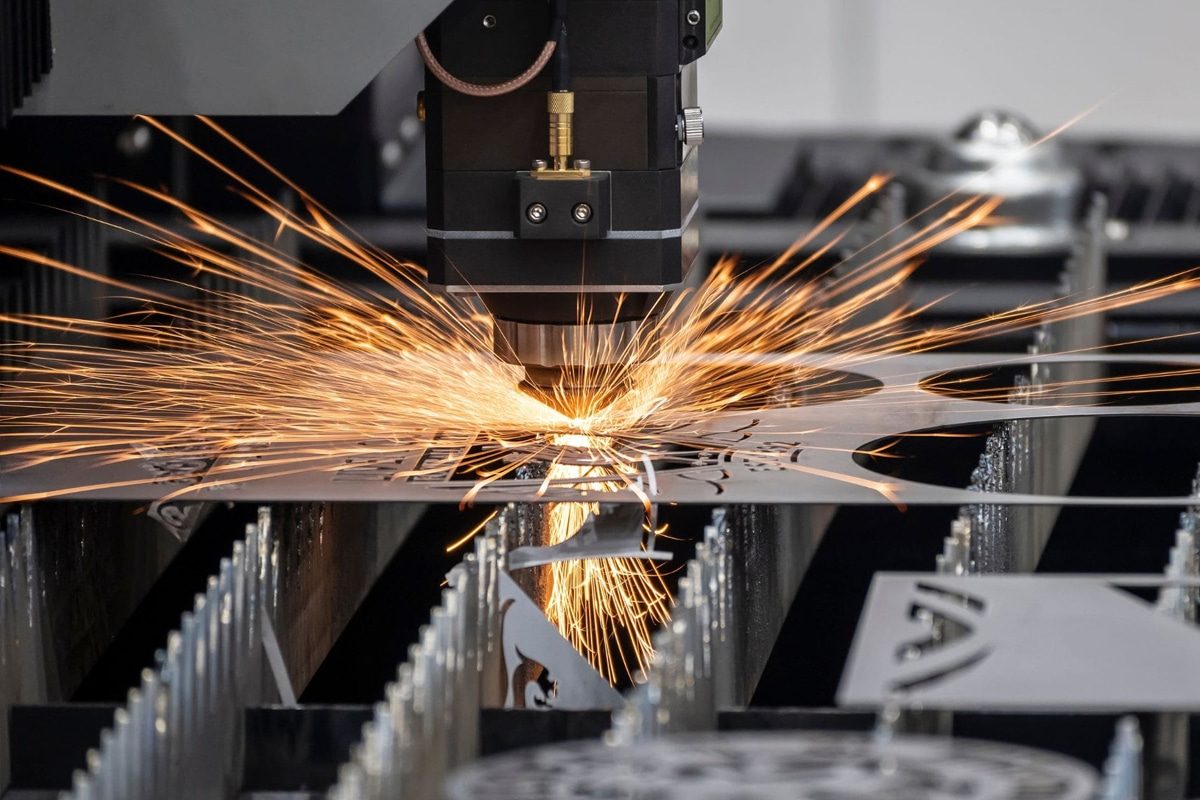
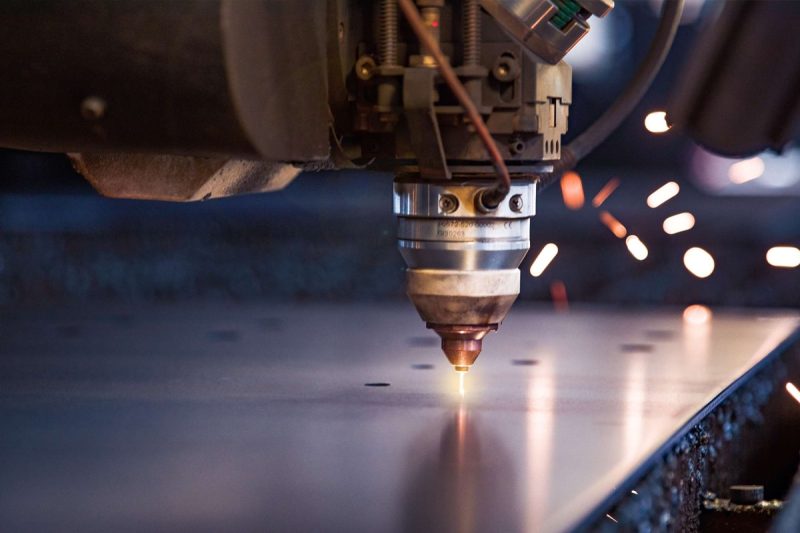
Overview of Laser Cutting Technology
Brief History
How Laser Cutting Works
Laser cutting involves using a high-powered, focused laser beam to melt, burn, or vaporize material in a precise pattern. The process typically includes:
- Laser Generation: The laser source (CO2, fiber, or Nd:YAG) generates a high-energy beam.
- Beam Delivery: The beam is directed to the cutting head using mirrors or fiber-optic cables.
- Focusing: Lenses or mirrors focus the beam into a fine point, increasing its intensity.
- Material Interaction: The focused laser beam interacts with the material, cutting through it by melting or vaporizing, often assisted by a gas like oxygen, nitrogen, or air.
- Motion Control: Computer-controlled systems guide the laser head or material to create intricate shapes and designs.
Advantages of Laser Cutting
Laser cutting stands out for its numerous benefits, making it a preferred choice for manufacturers worldwide:
- Precision and Accuracy: Laser cutting achieves tolerances as tight as ±0.1mm, making it ideal for intricate designs.
- Versatility: Capable of cutting a wide range of materials, including metals, plastics, wood, and composites.
- High Efficiency: Fast processing speeds and reduced material waste increase production efficiency.
- Clean Edges: The focused heat minimizes burrs and the need for post-processing.
- Non-Contact Process: No mechanical stress is applied to the material, preserving its integrity.
- Automation Friendly: Easily integrated with CNC systems for repeatable and consistent results.
- Minimal Maintenance: Fiber laser generators, in particular, offer long operational lifespans with low maintenance requirements.
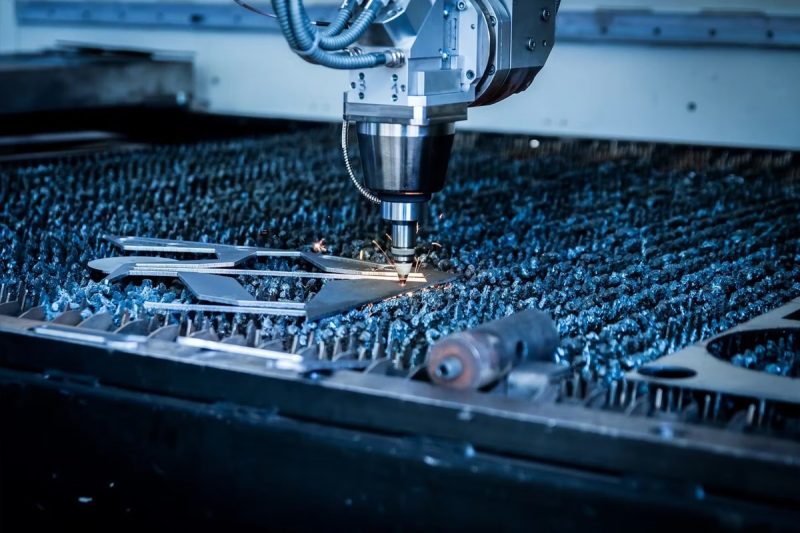
Classification of Laser Cutting Machines
Based on Laser Source
Fiber Laser Cutting Machines
Working Principles:
- Fiber lasers use optical fibers doped with rare-earth elements, such as ytterbium, to amplify light.
- The laser beam is generated and delivered directly through fiber-optic cables, eliminating the need for complex mirrors and lenses.
- Operating at a wavelength of approximately 1.06 micrometers, the concentrated laser beam achieves a high power density ideal for metal cutting.
Applications:
- Metal Processing: Stainless steel, carbon steel, aluminum, brass, copper, and titanium.
- Precision Industries: Aerospace, medical devices, electronics, and jewelry.
- High-Speed Production: Automotive and heavy machinery manufacturing.
Advantages:
- High Cutting Speeds: Faster processing than CO2 lasers, especially for metals.
- Energy Efficiency: Consumes significantly less power, lowering operational costs.
- Low Maintenance: Few moving parts and no mirror alignment required.
- Compact Design: Smaller footprint compared to CO2 systems.
- Durability: Longer operational lifespan, often exceeding 100,000 hours.
Disadvantages:
- Higher Initial Cost: Substantial upfront investment.
- Limited Non-Metal Applications: Ineffective for cutting materials like wood, glass, and acrylic.
- Reflective Material Challenges: Cutting reflective metals like copper requires specialized configurations.
CO2 Laser Cutting Machines
Working Principles:
- CO2 lasers generate a laser beam by electrically exciting a gas mixture of carbon dioxide, nitrogen, and helium.
- The laser emits infrared light at a wavelength of 10.6 micrometers, which is directed through a system of mirrors and lenses to the cutting surface.
- The intense heat generated melts, burns, or vaporizes the material to create clean, precise cuts.
Advantages:
- Wide Range of Materials: Excels in cutting and engraving non-metals.
- Smooth and Clean Edges: Minimal post-processing required.
- Proven Technology: Reliable, with extensive industry support and resources.
- Lower Cost: Initial investment is lower than other advanced laser systems.
Disadvantages:
- Limited Metal Cutting: Inefficient for cutting thick or reflective metals.
- Maintenance-Intensive: Requires regular cleaning, mirror alignment, and replacement of consumables.
- Energy-Intensive: Less efficient than newer technologies like fiber lasers.
- Slower Cutting Speed: Cannot match the high-speed capabilities of fiber lasers.
Nd:YAG Laser Cutting Machines
Working Principles:
- Nd:YAG lasers use a crystal rod doped with neodymium ions as the gain medium.
- Light amplification occurs within the crystal, generating a laser beam with a wavelength of 1.064 micrometers.
- The beam can be emitted in either continuous-wave or pulsed modes, offering flexibility for various applications.
Applications:
- High-Precision Cutting: Electronics manufacturing, medical device production, and jewelry.
- Metal Processing: Cutting and welding of steel, aluminum, and other metals.
- Micromachining: Creating small, intricate components.
Advantages:
- High Peak Power: Suitable for detailed work and thick material cutting.
- Versatility: Effective for cutting, welding, and drilling applications.
- Compact Design: Ideal for small-scale, high-precision production.
- Pulse Mode: Reduces heat-affected zones, preserving material properties.
Disadvantages:
- Energy Inefficiency: Consumes more energy compared to fiber lasers.
- High Maintenance Costs: Frequent replacement of flash lamps and careful cooling required.
- Limited Lifespan: Shorter operational life compared to fiber lasers.
Based on Material to Be Cut
Metal Laser Cutting Machines
Features:
- Equipped with fiber lasers for cutting metals of varying thicknesses.
- Assist gases (e.g., oxygen, nitrogen) enhance cutting speed and edge quality.
Applications:
- Thin and Thick Metals: Carbon steel, stainless steel, aluminum, brass, and titanium.
- Complex Shapes: Components for the automotive, aerospace, and construction industries.
Advantages:
- High precision with minimal material waste.
- Capable of cutting reflective and non-reflective metals.
Disadvantages:
- Higher operational and maintenance costs.
- Requires expertise in parameter setup for complex materials.
Non-Metal Laser Cutting Machines
Features:
- Adjustable cutting parameters for delicate materials.
- Excellent for heat-sensitive applications.
Applications:
- Organic Materials: Wood, acrylic, textiles, leather, and paper.
- Engraving: Artistic designs on ceramics, plastics, and glass.
Advantages:
- Clean and precise cuts with minimal damage.
- Ideal for artistic and decorative applications.
Disadvantages:
- Cannot cut metals effectively.
- Requires frequent maintenance for consistent performance.
Based on Application
Industrial Laser Cutting Machines
Applications:
- Mass production of metal parts and machinery components.
- Cutting large, complex workpieces with high accuracy.
Advantages:
- High throughput and repeatability.
- Capable of handling heavy workloads.
Disadvantages:
- High cost and large footprint.
- Requires skilled operators and advanced maintenance.
Hobbyist/Desktop Laser Cutting Machines
Applications:
- Prototyping, crafting, and engraving.
- Small-scale cutting of non-metals like wood, acrylic, and paper.
Advantages:
- Easy to use and transport.
- Cost-effective for small businesses and individuals.
Disadvantages:
- Limited power and functionality.
- Unsuitable for heavy-duty or high-volume tasks.
Based on Mode of Operation
2D Laser Cutting Machines
Operate on two axes (X and Y), suitable for cutting flat materials like sheet metal, wood, and textiles.
- Applications: Sheet metal fabrication, signage, and decorative panels.
3D Laser Cutting Machines
Multi-axis motion systems enable cutting complex geometries on three-dimensional surfaces.
- Applications: Automotive parts, formed metal sheets, and aerospace components.
5-Axis Laser Cutting Machines
Advanced machines offering flexibility to cut at various angles, producing intricate shapes.
- Applications: Turbine blades, medical implants, and high-precision aerospace parts.
Based on Functionality
Optimized for cutting flat sheets of materials like metal, acrylic, or wood.
- Applications: Panels, facades, and flat components.
Designed specifically for tubular materials, such as round, square, and rectangular pipes.
- Applications: Furniture frames, automotive pipes, and structural supports.
Combines both functionalities for cutting flat sheets and tubes, making it highly versatile.
- Applications: Mixed production tasks involving both flat and tubular materials.
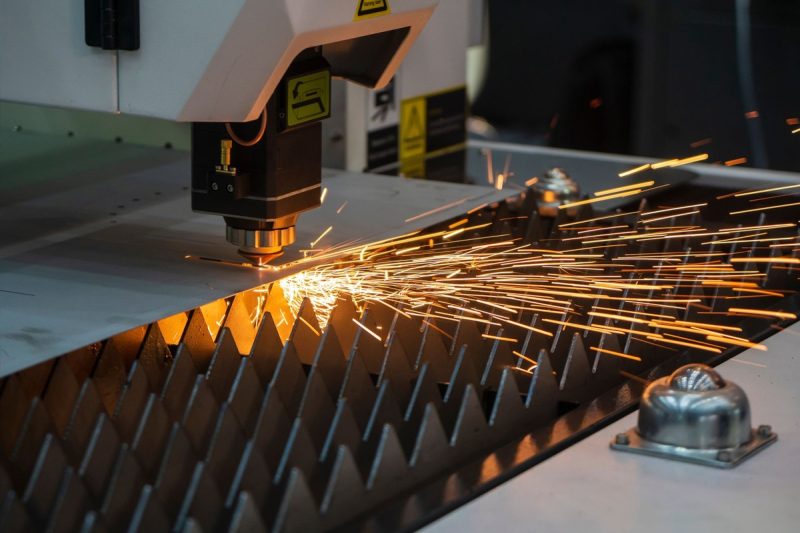
Key Factors to Consider When Choosing a Laser Cutting Machine
Material Compatibility
What to Consider:
- Metal Cutting: Fiber lasers excel at cutting metals like stainless steel, aluminum, brass, and copper due to their high energy density and efficiency.
- Non-Metals: CO2 lasers are better suited for cutting non-metal materials such as wood, acrylic, textiles, and glass.
- Material Thickness: Check the maximum cutting thickness the machine can handle, as different laser sources and power levels affect the range of materials that can be processed.
- Heat Sensitivity: Ensure the machine minimizes heat-affected zones for materials that are prone to warping or damage.
Power Requirements
What to Consider:
- Material Thickness: For cutting thick metals, a high-powered fiber laser (e.g., 6kW or more) is necessary, while lower power levels (e.g., 1-2kW) are sufficient for thinner materials.
- Cutting Speed vs. Power: Higher power not only allows for thicker cuts but also increases cutting speed, making it ideal for high-volume production.
- Energy Efficiency: Consider the operational power consumption to manage energy costs. Fiber lasers are generally more energy-efficient than CO2 lasers.
Cutting Speed Requirements
What to Consider:
- Material and Thickness: Cutting speed varies depending on the material and its thickness. For instance, fiber lasers cut thin metals faster than CO2 lasers.
- Production Volume: High-speed machines are essential for businesses with large-scale production requirements.
- Trade-offs: High-speed cutting may compromise edge quality, so ensure the machine meets both speed and quality expectations.
Precision and Accuracy Requirements
What to Consider:
- Tolerance Levels: Ensure the machine can meet the required tolerances, typically ranging from ±0.1mm to ±0.05mm, depending on the application.
- Beam Quality: High beam quality leads to cleaner cuts and reduces the need for post-processing.
- Motion Systems: Machines with advanced motion systems and linear guides offer better accuracy and smoother cuts.
Maintenance and Operational Costs
What to Consider:
- Consumables: CO2 lasers require more frequent replacement of mirrors and lenses, whereas fiber lasers have fewer consumable parts.
- Energy Costs: Fiber lasers consume less power compared to CO2 lasers, reducing energy bills.
- Downtime: Look for machines with minimal maintenance requirements to reduce downtime and ensure consistent productivity.
- Cooling Systems: Check if the machine requires a water or air-cooled system, as this can affect operational costs.
Software and Control Systems
What to Consider:
- Ease of Use: Look for machines with intuitive interfaces that simplify setup and operation.
- Nesting Software: Advanced nesting software optimizes material usage, minimizing waste.
- Integration: Ensure compatibility with existing CAD/CAM systems and the ability to handle complex designs.
- Automation Features: Machines with automated loading, unloading, and monitoring features streamline workflows.
Support and Service
What to Consider:
- Manufacturer Reputation: Work with reputable manufacturers like AccTek Laser that offer high-quality machines and comprehensive support.
- Technical Support: Ensure 24/7 access to technical assistance, especially for critical production environments.
- Training and Installation: Look for manufacturers that provide operator training and machine installation services.
- Spare Parts Availability: Check for the availability of spare parts and their delivery times to minimize downtime.
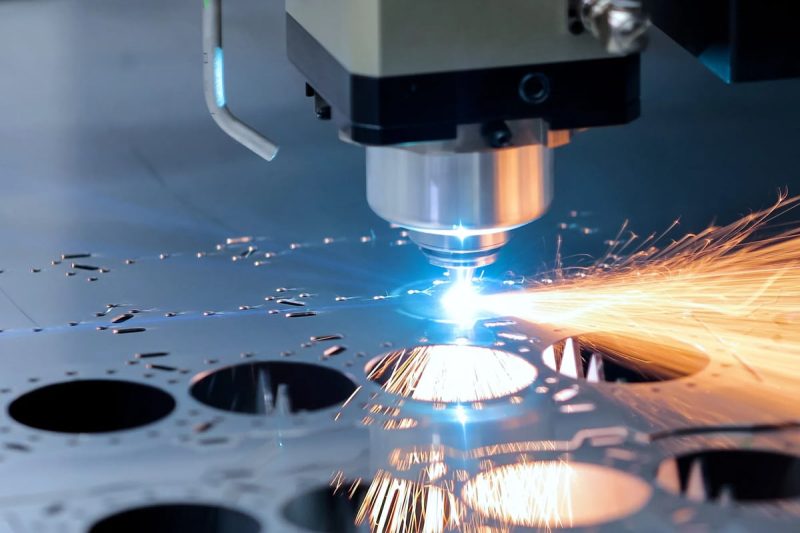
Summary
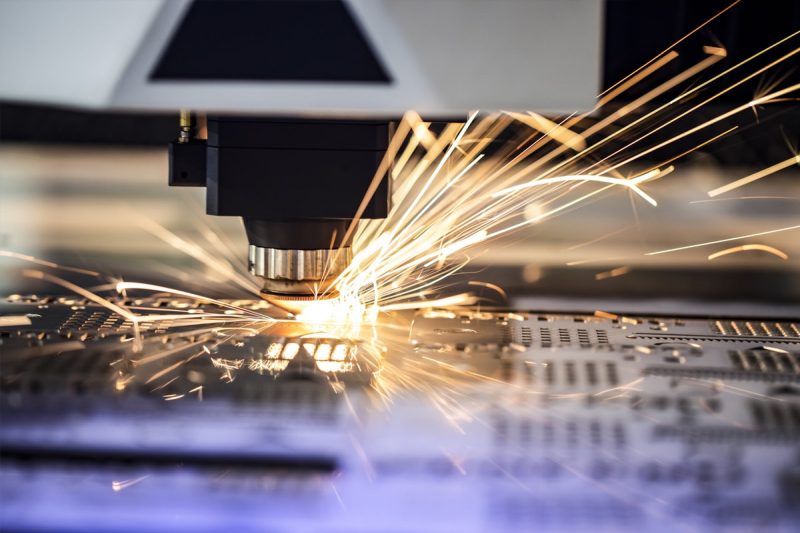
Get Laser Cutting Solutions
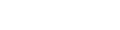
- [email protected]
- [email protected]
- +86-19963414011
- No. 3 Zone A, Lunzhen Industrial Zone,Yucheng City , Shandong Province.