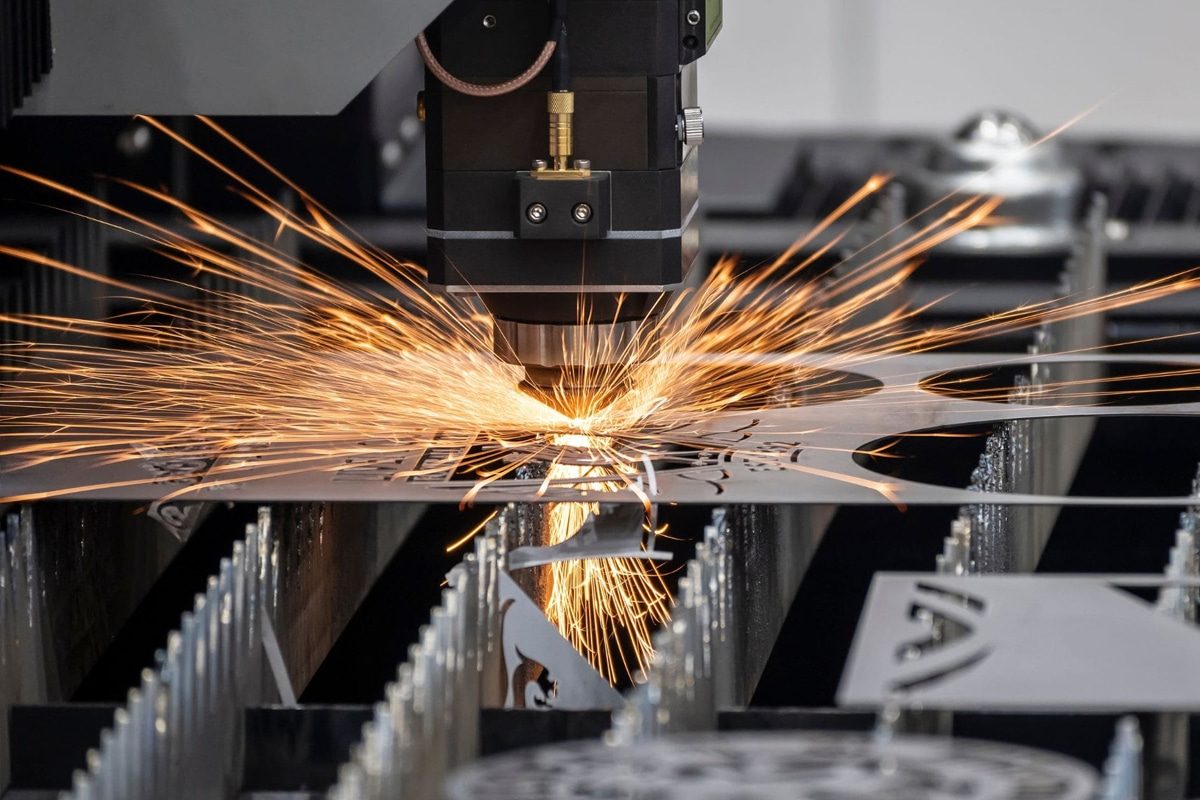
From high-speed fiber laser cutting machines for metal processing to versatile CO2 laser cutting machines for non-metal applications, each type of machine serves specific needs. Whether it’s cutting intricate designs into delicate materials or slicing through thick metal sheets, laser cutting machines deliver results that meet the demands of modern production.
Understanding the types of laser cutting machines available and their capabilities is vital for businesses seeking efficiency and precision in their operations. This article explores the various types of laser cutting machines, their features, applications, and how they revolutionize manufacturing processes worldwide.
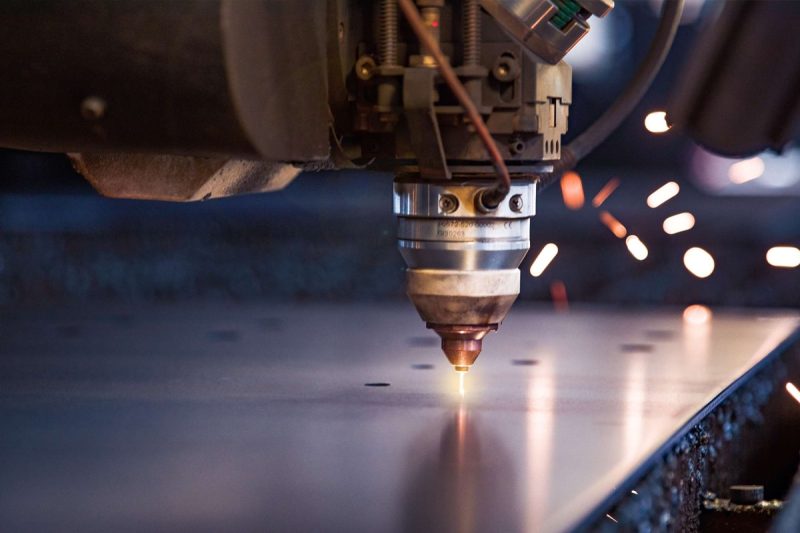
Overview of Laser Cutting Technology
Brief History
How Laser Cutting Works
Laser cutting involves using a high-powered, focused laser beam to melt, burn, or vaporize material in a precise pattern. The process typically includes:
- Laser Generation: The laser source (CO2, fiber, or Nd:YAG) generates a high-energy beam.
- Beam Delivery: The beam is directed to the cutting head using mirrors or fiber-optic cables.
- Focusing: Lenses or mirrors focus the beam into a fine point, increasing its intensity.
- Material Interaction: The focused laser beam interacts with the material, cutting through it by melting or vaporizing, often assisted by a gas like oxygen, nitrogen, or air.
- Motion Control: Computer-controlled systems guide the laser head or material to create intricate shapes and designs.
Advantages of Laser Cutting
Laser cutting stands out for its numerous benefits, making it a preferred choice for manufacturers worldwide:
- Precision and Accuracy: Laser cutting achieves tolerances as tight as ±0.1mm, making it ideal for intricate designs.
- Versatility: Capable of cutting a wide range of materials, including metals, plastics, wood, and composites.
- High Efficiency: Fast processing speeds and reduced material waste increase production efficiency.
- Clean Edges: The focused heat minimizes burrs and the need for post-processing.
- Non-Contact Process: No mechanical stress is applied to the material, preserving its integrity.
- Automation Friendly: Easily integrated with CNC systems for repeatable and consistent results.
- Minimal Maintenance: Fiber laser generators, in particular, offer long operational lifespans with low maintenance requirements.
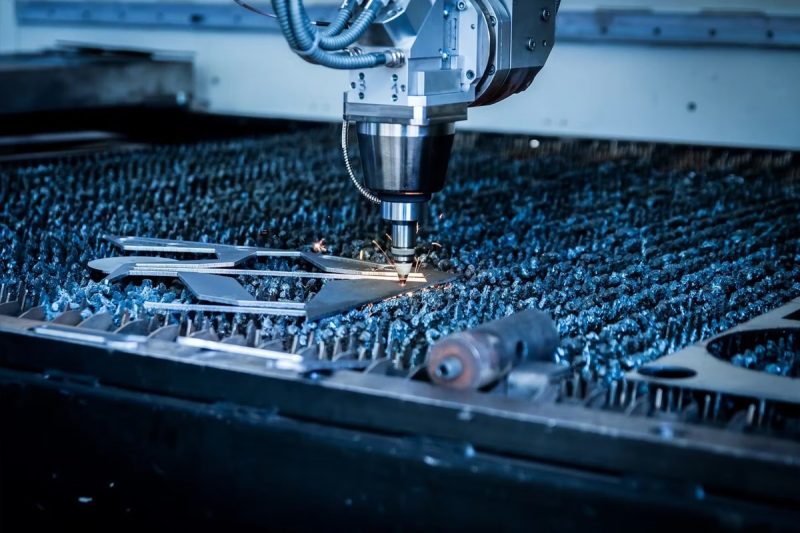
Classification of Laser Cutting Machines
Based on Laser Source
Fiber Laser Cutting Machines
Working Principles:
- Fiber lasers use optical fibers doped with rare-earth elements, such as ytterbium, to amplify light.
- The laser beam is generated and delivered directly through fiber-optic cables, eliminating the need for complex mirrors and lenses.
- Operating at a wavelength of approximately 1.06 micrometers, the concentrated laser beam achieves a high power density ideal for metal cutting.
Applications:
- Metal Processing: Stainless steel, carbon steel, aluminum, brass, copper, and titanium.
- Precision Industries: Aerospace, medical devices, electronics, and jewelry.
- High-Speed Production: Automotive and heavy machinery manufacturing.
Advantages:
- High Cutting Speeds: Faster processing than CO2 lasers, especially for metals.
- Energy Efficiency: Consumes significantly less power, lowering operational costs.
- Low Maintenance: Few moving parts and no mirror alignment required.
- Compact Design: Smaller footprint compared to CO2 systems.
- Durability: Longer operational lifespan, often exceeding 100,000 hours.
Disadvantages:
- Higher Initial Cost: Substantial upfront investment.
- Limited Non-Metal Applications: Ineffective for cutting materials like wood, glass, and acrylic.
- Reflective Material Challenges: Cutting reflective metals like copper requires specialized configurations.
CO2 Laser Cutting Machines
Working Principles:
- CO2 lasers generate a laser beam by electrically exciting a gas mixture of carbon dioxide, nitrogen, and helium.
- The laser emits infrared light at a wavelength of 10.6 micrometers, which is directed through a system of mirrors and lenses to the cutting surface.
- The intense heat generated melts, burns, or vaporizes the material to create clean, precise cuts.
Advantages:
- Wide Range of Materials: Excels in cutting and engraving non-metals.
- Smooth and Clean Edges: Minimal post-processing required.
- Proven Technology: Reliable, with extensive industry support and resources.
- Lower Cost: Initial investment is lower than other advanced laser systems.
Disadvantages:
- Limited Metal Cutting: Inefficient for cutting thick or reflective metals.
- Maintenance-Intensive: Requires regular cleaning, mirror alignment, and replacement of consumables.
- Energy-Intensive: Less efficient than newer technologies like fiber lasers.
- Slower Cutting Speed: Cannot match the high-speed capabilities of fiber lasers.
Nd:YAG Laser Cutting Machines
Working Principles:
- Nd:YAG lasers use a crystal rod doped with neodymium ions as the gain medium.
- Light amplification occurs within the crystal, generating a laser beam with a wavelength of 1.064 micrometers.
- The beam can be emitted in either continuous-wave or pulsed modes, offering flexibility for various applications.
Applications:
- High-Precision Cutting: Electronics manufacturing, medical device production, and jewelry.
- Metal Processing: Cutting and welding of steel, aluminum, and other metals.
- Micromachining: Creating small, intricate components.
Advantages:
- High Peak Power: Suitable for detailed work and thick material cutting.
- Versatility: Effective for cutting, welding, and drilling applications.
- Compact Design: Ideal for small-scale, high-precision production.
- Pulse Mode: Reduces heat-affected zones, preserving material properties.
Disadvantages:
- Energy Inefficiency: Consumes more energy compared to fiber lasers.
- High Maintenance Costs: Frequent replacement of flash lamps and careful cooling required.
- Limited Lifespan: Shorter operational life compared to fiber lasers.
Based on Material to Be Cut
Metal Laser Cutting Machines
Features:
- Equipped with fiber lasers for cutting metals of varying thicknesses.
- Assist gases (e.g., oxygen, nitrogen) enhance cutting speed and edge quality.
Applications:
- Thin and Thick Metals: Carbon steel, stainless steel, aluminum, brass, and titanium.
- Complex Shapes: Components for the automotive, aerospace, and construction industries.
Advantages:
- High precision with minimal material waste.
- Capable of cutting reflective and non-reflective metals.
Disadvantages:
- Higher operational and maintenance costs.
- Requires expertise in parameter setup for complex materials.
Non-Metal Laser Cutting Machines
Features:
- Adjustable cutting parameters for delicate materials.
- Excellent for heat-sensitive applications.
Applications:
- Organic Materials: Wood, acrylic, textiles, leather, and paper.
- Engraving: Artistic designs on ceramics, plastics, and glass.
Advantages:
- Clean and precise cuts with minimal damage.
- Ideal for artistic and decorative applications.
Disadvantages:
- Cannot cut metals effectively.
- Requires frequent maintenance for consistent performance.
Based on Application
Industrial Laser Cutting Machines
Applications:
- Mass production of metal parts and machinery components.
- Cutting large, complex workpieces with high accuracy.
Advantages:
- High throughput and repeatability.
- Capable of handling heavy workloads.
Disadvantages:
- High cost and large footprint.
- Requires skilled operators and advanced maintenance.
Hobbyist/Desktop Laser Cutting Machines
Applications:
- Prototyping, crafting, and engraving.
- Small-scale cutting of non-metals like wood, acrylic, and paper.
Advantages:
- Easy to use and transport.
- Cost-effective for small businesses and individuals.
Disadvantages:
- Limited power and functionality.
- Unsuitable for heavy-duty or high-volume tasks.
Based on Mode of Operation
2D Laser Cutting Machines
Operate on two axes (X and Y), suitable for cutting flat materials like sheet metal, wood, and textiles.
- Applications: Sheet metal fabrication, signage, and decorative panels.
3D Laser Cutting Machines
Multi-axis motion systems enable cutting complex geometries on three-dimensional surfaces.
- Applications: Automotive parts, formed metal sheets, and aerospace components.
5-Axis Laser Cutting Machines
Advanced machines offering flexibility to cut at various angles, producing intricate shapes.
- Applications: Turbine blades, medical implants, and high-precision aerospace parts.
Based on Functionality
Optimized for cutting flat sheets of materials like metal, acrylic, or wood.
- Applications: Panels, facades, and flat components.
Designed specifically for tubular materials, such as round, square, and rectangular pipes.
- Applications: Furniture frames, automotive pipes, and structural supports.
Combines both functionalities for cutting flat sheets and tubes, making it highly versatile.
- Applications: Mixed production tasks involving both flat and tubular materials.
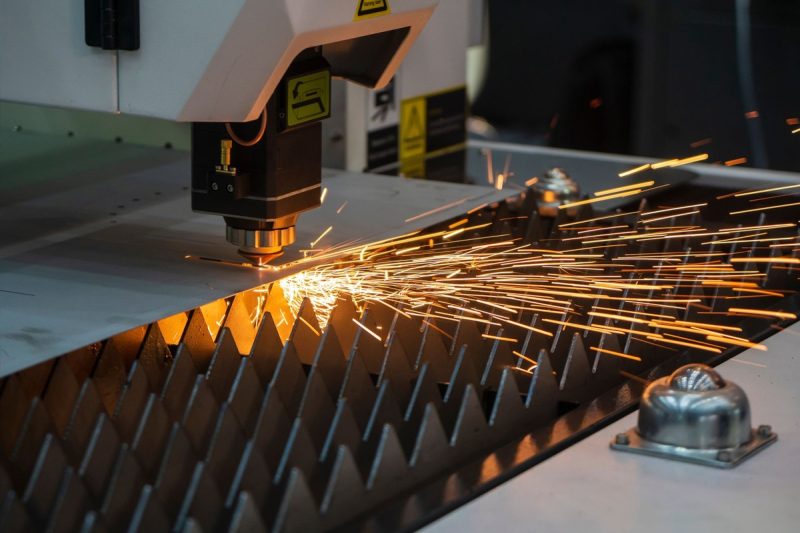
Key Factors to Consider When Choosing a Laser Cutting Machine
Material Compatibility
What to Consider:
- Metal Cutting: Fiber lasers excel at cutting metals like stainless steel, aluminum, brass, and copper due to their high energy density and efficiency.
- Non-Metals: CO2 lasers are better suited for cutting non-metal materials such as wood, acrylic, textiles, and glass.
- Material Thickness: Check the maximum cutting thickness the machine can handle, as different laser sources and power levels affect the range of materials that can be processed.
- Heat Sensitivity: Ensure the machine minimizes heat-affected zones for materials that are prone to warping or damage.
Power Requirements
What to Consider:
- Material Thickness: For cutting thick metals, a high-powered fiber laser (e.g., 6kW or more) is necessary, while lower power levels (e.g., 1-2kW) are sufficient for thinner materials.
- Cutting Speed vs. Power: Higher power not only allows for thicker cuts but also increases cutting speed, making it ideal for high-volume production.
- Energy Efficiency: Consider the operational power consumption to manage energy costs. Fiber lasers are generally more energy-efficient than CO2 lasers.
Cutting Speed Requirements
What to Consider:
- Material and Thickness: Cutting speed varies depending on the material and its thickness. For instance, fiber lasers cut thin metals faster than CO2 lasers.
- Production Volume: High-speed machines are essential for businesses with large-scale production requirements.
- Trade-offs: High-speed cutting may compromise edge quality, so ensure the machine meets both speed and quality expectations.
Precision and Accuracy Requirements
What to Consider:
- Tolerance Levels: Ensure the machine can meet the required tolerances, typically ranging from ±0.1mm to ±0.05mm, depending on the application.
- Beam Quality: High beam quality leads to cleaner cuts and reduces the need for post-processing.
- Motion Systems: Machines with advanced motion systems and linear guides offer better accuracy and smoother cuts.
Maintenance and Operational Costs
What to Consider:
- Consumables: CO2 lasers require more frequent replacement of mirrors and lenses, whereas fiber lasers have fewer consumable parts.
- Energy Costs: Fiber lasers consume less power compared to CO2 lasers, reducing energy bills.
- Downtime: Look for machines with minimal maintenance requirements to reduce downtime and ensure consistent productivity.
- Cooling Systems: Check if the machine requires a water or air-cooled system, as this can affect operational costs.
Software and Control Systems
What to Consider:
- Ease of Use: Look for machines with intuitive interfaces that simplify setup and operation.
- Nesting Software: Advanced nesting software optimizes material usage, minimizing waste.
- Integration: Ensure compatibility with existing CAD/CAM systems and the ability to handle complex designs.
- Automation Features: Machines with automated loading, unloading, and monitoring features streamline workflows.
Support and Service
What to Consider:
- Manufacturer Reputation: Work with reputable manufacturers like AccTek Laser that offer high-quality machines and comprehensive support.
- Technical Support: Ensure 24/7 access to technical assistance, especially for critical production environments.
- Training and Installation: Look for manufacturers that provide operator training and machine installation services.
- Spare Parts Availability: Check for the availability of spare parts and their delivery times to minimize downtime.
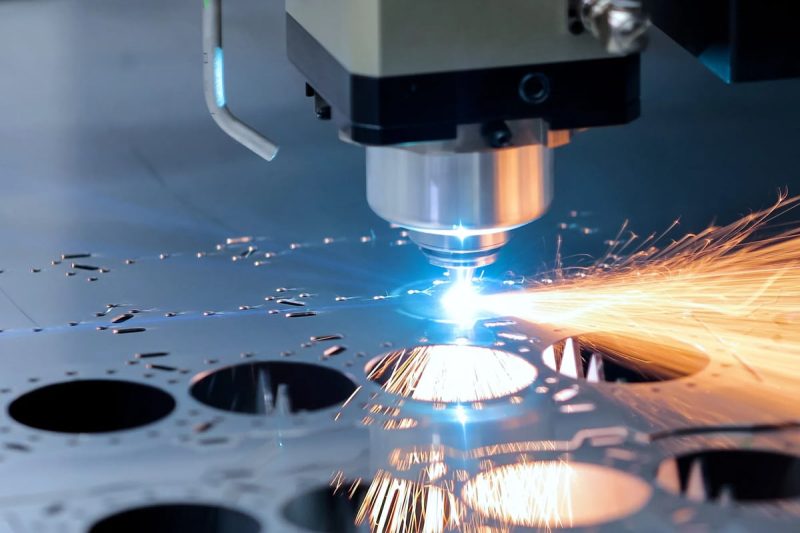
Summary
Additionally, machines can be specialized for cutting metals or non-metals, industrial-scale production, or small-scale, hobbyist applications. Advanced features like 2D, 3D, and 5-axis operations, as well as combinations of sheet and tube cutting capabilities, further expand their versatility.
Choosing the right machine involves considering factors like material, power, cutting speed, and support services. By understanding these classifications and aligning them with specific needs, businesses can unlock the full potential of laser-cutting technology.
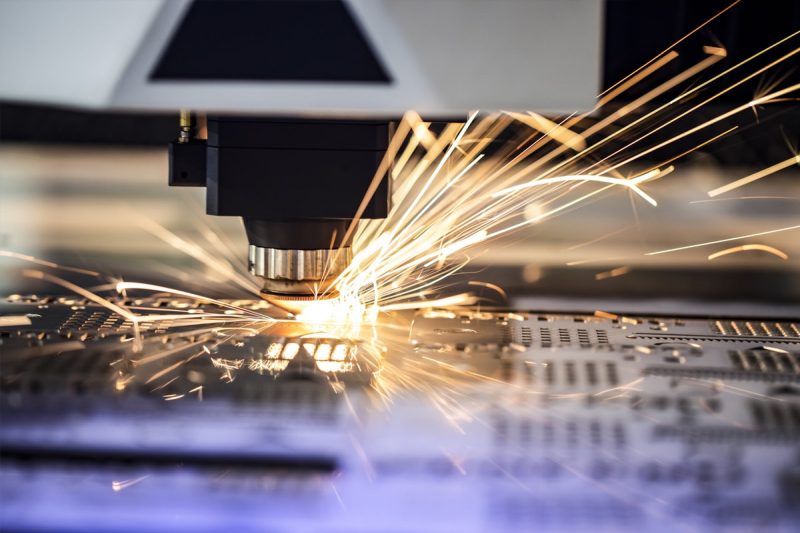
Get Laser Cutting Solutions
Our machines are designed with advanced features such as precise motion systems, user-friendly software, and energy-efficient operation to ensure seamless performance. With AccTek Laser’s expert team, you gain access to personalized consultations, professional installation, operator training, and 24/7 technical support.
Let AccTek Laser help you transform your production line with tailored solutions that align with your business goals. Discover the perfect laser cutting machine for your needs and elevate your manufacturing capabilities today.
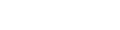
- manager@accteklaser.com
- manager@accteklaser.com
- +86-19963414011
- No. 3 Zone A, Lunzhen Industrial Zone,Yucheng City , Shandong Province.