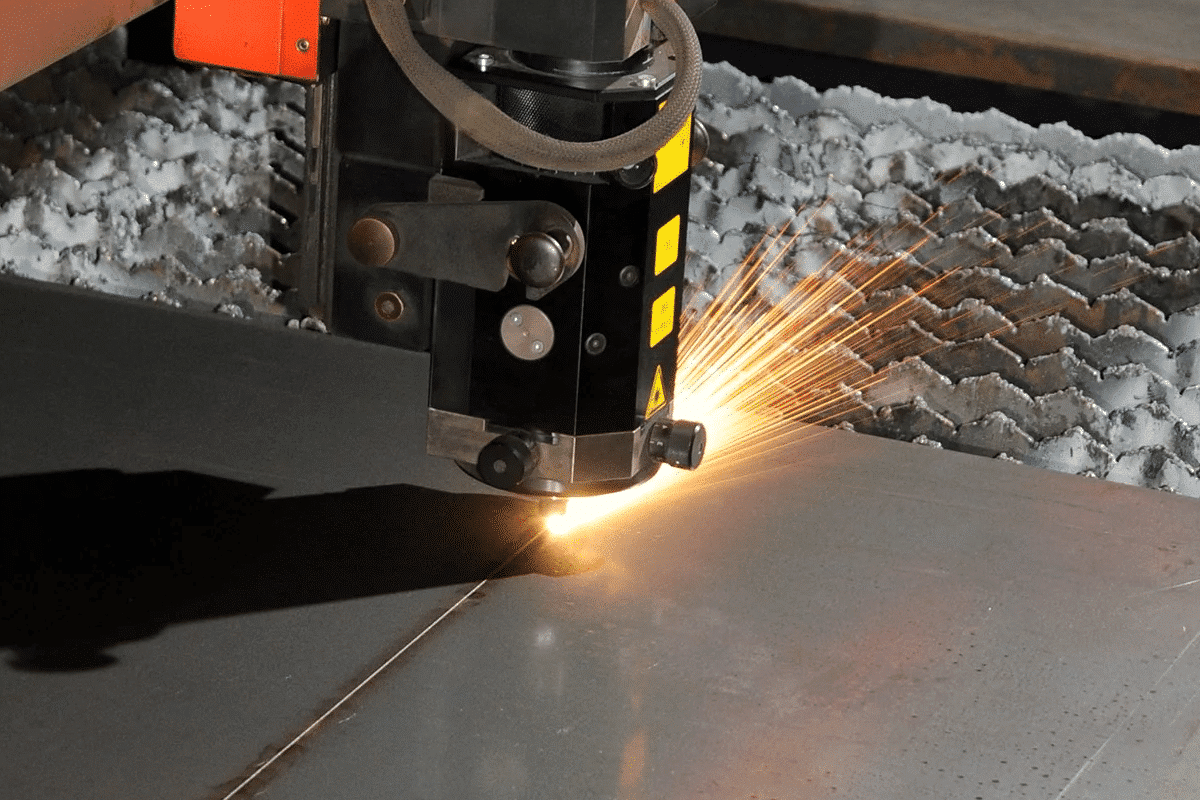
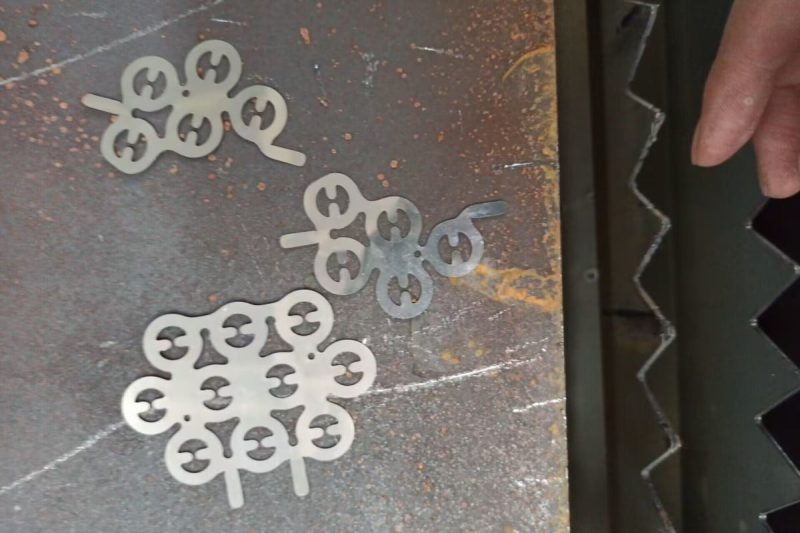
What are the defects caused by the improper cutting of the fiber laser cutting machine
Glitch
Slag
Uneven cut
Cutting Skew
Oxidized edges
The heat-affected zone is too large
Long-term cut quality change
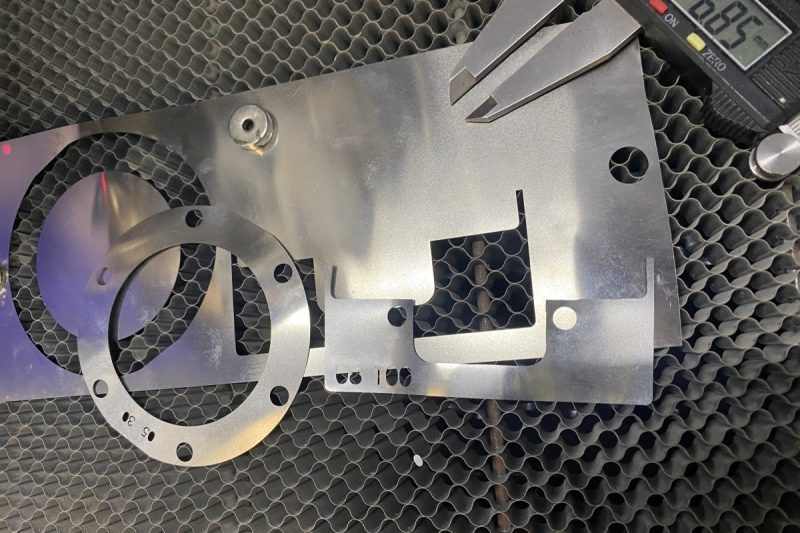
Reasons Affecting Fiber Laser Cutting Quality
Material Properties
Different materials have different optical properties and thermal conductivity, which affect laser absorption and heat transmission. Factors such as hardness, thickness, and thermal conductivity of the material will also affect the heat-affected zone and degree of deformation during cutting.
- Material Type: Metallic materials generally have higher laser absorption rates, while non-metallic materials (such as plastic, wood, etc.) have lower laser absorption rates. Therefore, it is necessary to increase and decrease the laser power and parameters appropriately according to the material type to ensure sufficient cutting energy.
- Material thickness: Too thick material will lead to too slow cutting speed, thus increasing the production cycle; while too thin material is prone to cutting instability or incomplete penetration. Adjust parameters for materials of different thicknesses to achieve the best cutting results.
- Material surface quality and optical properties: the poor surface of the material surface, such as oxidation, and oil stains will lead to cutting instability and slag and other defects; in addition, the optical properties of the material, including the absorption and scattering characteristics of the material to the laser, will directly affect the laser transmission efficiency and focus quality.
Laser parameters
Laser parameters are important factors affecting the quality of fiber laser cutting, including laser power, laser frequency, pulse width, and frequency, etc. Different laser parameters will have different effects on the cutting effect.
- Laser power: The laser power determines the energy density of the laser. Too high power may cause slag and scorch on the cutting edge, and too low power may cause incomplete cutting.
- Laser Frequency: Laser frequency affects the speed and quality of the cut. Higher frequencies increase cutting speed but may reduce cut quality. Proper frequency selection can strike a balance between high-speed cutting and high-quality cutting.
- Pulse width: The pulse width determines the laser’s action time on the material, too long pulse width may lead to excessive heat conduction and affect the cutting quality. Shorter pulse widths help reduce the heat-affected zone, resulting in smaller cut widths.
- Repetition frequency: The repetition frequency determines the frequency of the pulse. Too high a repetition frequency may cause excessive accumulated heat and affect the cutting quality. Lower repetition rates may affect cutting speed. Choosing an appropriate repetition rate will help optimize cutting results.
Optical system
The optical system is responsible for transmitting the laser light from the fiber to the workpiece and focusing the laser light at the proper focal point. The performance of the optical system directly affects the quality of fiber laser cutting, and the specific effects include:
- Beam quality: The laser beam quality of the laser generator, that is, the BPP value, is one of the important parameters to measure the quality of the laser generator. The smaller the BPP value, the better the beam quality, which means smoother sections and higher precision when processing sheet metal.
- Focusing quality: The focusing effect of the optical system determines the focal size and depth of focus of the laser. Appropriate focus size can achieve fine cutting, while improper focus may lead to unclear cutting edges and even reduced cutting quality.
- Focusing accuracy: The focusing accuracy of the optical system determines the position and stability of the laser focus. The inaccurate focus will lead to cutting line deviation or focus drift, affecting cutting quality and precision.
Auxiliary gas
The auxiliary gas mainly plays the role of cooling, cleaning, and combustion in fiber laser cutting. The impact on the quality of fiber laser cutting is mainly reflected in the following aspects:
- Cleaning effect: The auxiliary gas can blow impurities such as slag, oxides, and debris generated during the cutting process away from the cutting area to keep the cutting area clean. This helps to improve the absorption efficiency of laser energy and avoid secondary pollution during cutting.
- Gas flow: The flow of auxiliary gas determines the strength of the gas flow in the cutting area, too high or too low gas flow will affect the cutting quality. Proper gas flow keeps the cutting area stable and clean.
- Gas purity: The purity of the auxiliary gas is also an important factor affecting the cutting quality. High-purity gas can reduce the impact of impurities on cutting and ensure the purity of the cutting area.
Control system
The control system plays a vital role in fiber laser cutting. It involves the motion control and parameter adjustment of the cutting machine, which directly affects the cutting quality and accuracy. Specific impacts include:
- Stability of the motion control system: The motion control system of the fiber laser cutting machine is responsible for controlling the movement trajectory of the laser head on the workpiece. Stability is the key to ensuring cutting quality. If the motion control system is unstable, it may lead to changes in the laser focus position during the cutting process, resulting in skewed cutting lines or uneven cutting.
- Cutting speed and acceleration: The control system can adjust the cutting speed and acceleration. A cutting speed that is too fast may result in incomplete cutting, while a speed that is too slow may cause the heat-affected zone to be too large and affect the quality of the cutting edge.
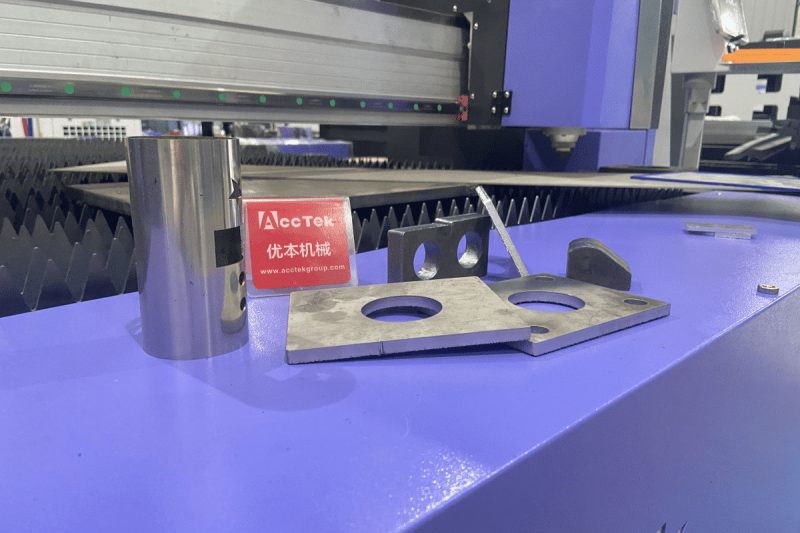
How to optimize the cutting defects of fiber laser cutting machines?
Slag and burrs
Cutting line skew
Uneven cutting
The heat-affected zone is too large
Oxidized edges
Charring and hole burning
Summarize
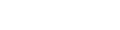
- [email protected]
- [email protected]
- +86-19963414011
- No. 3 Zone A, Lunzhen Industrial Zone,Yucheng City , Shandong Province.