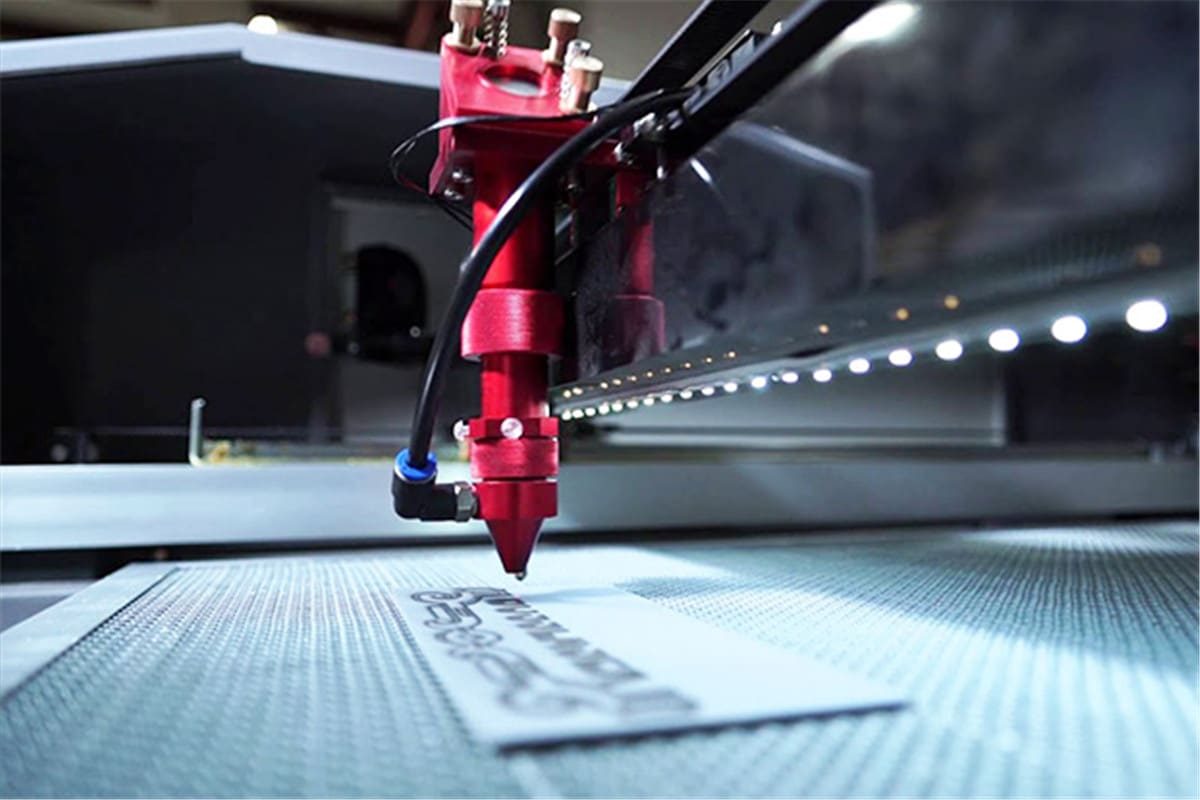
What Are The Factors That Affect The Edge Quality of CO2 Laser Cutting?
CO2 laser cutting has emerged as a versatile and precise method for shaping various materials, ranging from metals to plastics. The success of any laser cutting operation is heavily reliant on achieving high-quality edges, characterized by smooth finishes and minimal distortions. However, achieving optimal edge quality is a persistent challenge that manufacturers often face. In this article, we explore the myriad factors that significantly influence the edge quality of the final product. Through these discussions, we provide you with various techniques and strategies to improve the edge quality of CO2 laser cutting processes to ensure excellent results in your manufacturing process.
Table of Contents
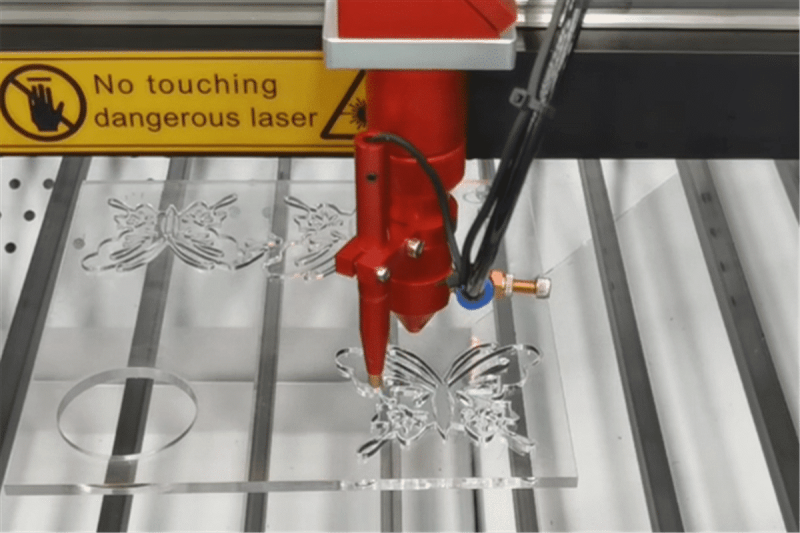
Understanding CO2 laser cutting technology
CO2 laser cutting machine has revolutionized the manufacturing industry with its precision and efficiency. Before delving into the factors affecting edge quality, it’s essential to understand the fundamentals, composition, and application materials of CO2 laser cutting machine.
How CO2 laser cutting system works?
CO2 laser generators operate by emitting a concentrated beam of light, generated by exciting carbon dioxide gas. This intense beam is then focused onto the material’s surface, causing localized heating and vaporization, resulting in precise and clean cuts. For non-metallic materials, such as wood or acrylic, the laser beam typically melts and vaporizes the material. For metallic materials, the laser can cut through by melting the material and blowing away the molten metal with an assist gas (e.g., oxygen or nitrogen).
CO2 laser cutting machines are equipped with a computer numerical control (CNC) system. A computer program guides the CNC system, controlling the movement of the laser beam along the specified cutting path. Computer-aided design (CAD) files are often used to program the CNC system for precise and complex cuts.
Composition of CO2 laser cutting system
- Laser Generator/CO2 Laser Tube: The CO2 laser tube is the core component that generates the laser beam. It typically contains a mixture of gases, including carbon dioxide, nitrogen, and helium. Electrical energy is applied to this gas mixture, resulting in the amplification of the laser light through a process known as stimulated emission.
- Laser Cutting Head: The laser cutting head contains the focusing lens and is responsible for positioning the focused laser beam onto the material being processed. It can move in multiple axes to follow the programmed cutting path.
- Controller: A sophisticated controller manages and regulates various parameters such as laser power, cutting speed, and focal length. Advanced controllers offer real-time adjustments for optimal cutting performance.
- Worktable: The worktable is the surface on which the material to be cut or engraved is placed. It provides support for the material and may have features such as a grid pattern or slats to allow for efficient exhaust and removal of debris.
- Assist Gas System: An assist gas, such as oxygen or nitrogen, may be used to improve the cutting process, especially for metal materials. The assist gas can help blow away molten metal and enhance the combustion process.
- Cooling System: CO2 laser tubes generate heat during operation. A cooling system, often using water or other coolants, is employed to maintain optimal operating temperatures and prevent overheating of the laser components.
What materials can CO2 laser cutting be used for?
- Non-metallic materials: Wood, acrylic, plastics, leather, fabric, felt, paper, stone, etc.
- Metal materials: stainless steel and carbon steel. It should be noted that the CO2 laser generator is limited to cutting thinner metals.
While CO2 laser generators are versatile, they may not be suitable for cutting or engraving certain materials, especially those with highly reflective surfaces or those that do not absorb the CO2 laser wavelength effectively.
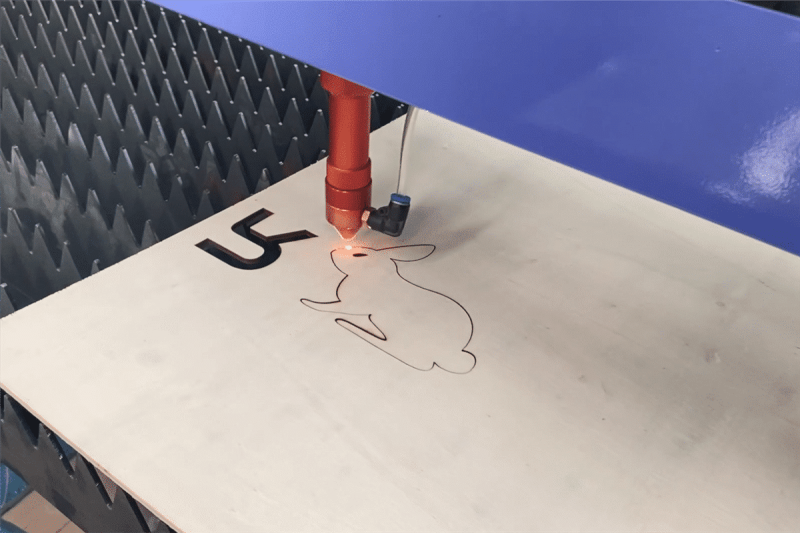
How does the focus size of a CO2 laser affect cutting results?
The focus size of a CO2 laser plays an important role in determining the cutting results in laser cutting applications. The focus size refers to the diameter of the laser beam at the focal point, where the laser energy is most concentrated. The focal point is where the laser beam is focused to achieve maximum intensity. The following is the effect of focus size on cutting results:
Cutting Precision
A smaller focus size results in a smaller spot size on the material. This allows for higher precision in cutting intricate patterns, fine details, and smaller features.
Cutting Speed
Generally, a smaller focus size allows for a higher power density at the focal point. This increased power density can lead to faster cutting speeds, as it provides more energy to vaporize or melt the material.
Material Thickness
For thinner materials, a smaller focus size is usually chosen, which allows for finer detail and greater accuracy during cutting. For thicker materials, in order to obtain greater penetration, a larger focus size is usually selected, but this results in reduced accuracy, making it difficult to achieve precise details in cutting.
Material Interaction
Different materials have varying responses to laser energy. The focus size can be adjusted to optimize the interaction between the laser beam and the material. For example, materials with high absorption of laser energy might benefit from a smaller focus size to concentrate the energy more efficiently.
Heat-Affected Zone (HAZ)
The size of the focus also affects the heat-affected zone in the material. A smaller focus size can result in a smaller HAZ, which is desirable in applications where minimal heat transfer to the surrounding material is important.
Beam Divergence
The focus size is related to the beam divergence, which is the spreading of the laser beam as it travels away from the focal point. Smaller focus sizes often correspond to lower beam divergence, contributing to better cutting accuracy over longer distances.
The optimal focus size depends on various factors, including the material being cut, its thickness, and the desired cutting quality. Laser operators often perform tests and adjustments to find the ideal focus size for a specific application. Additionally, some laser cutting systems allow for dynamic focus control, enabling the operator to adapt the focus size during the cutting process for improved results.
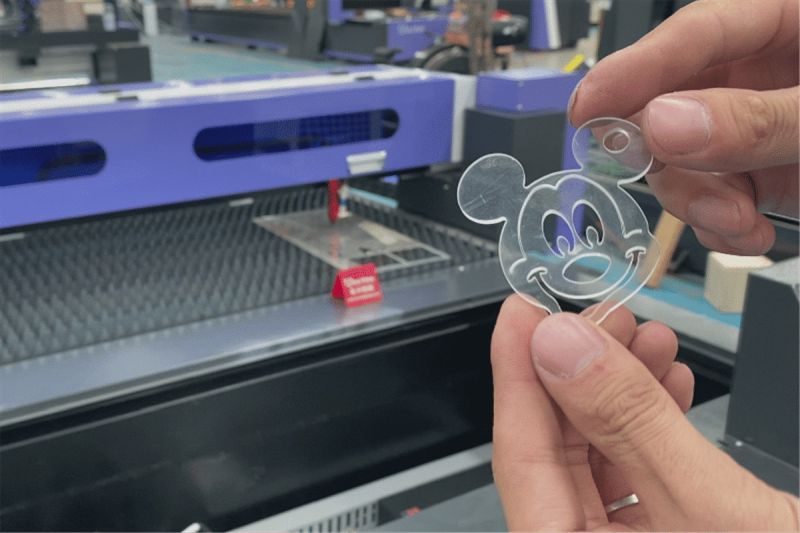
Other factors affecting CO2 laser cutting results
The size of the focus of the CO2 laser generator has a greater impact on the cutting results, but in addition, other factors also have a certain impact on the edge quality of the workpiece. Understanding them can better improve the quality of CO2 laser cutting.
Material Properties
The type of material being cut significantly affects edge quality. Different materials absorb and reflect laser energy differently. Metals, for instance, require higher power levels due to their high reflectivity, while non-metals like plastics and wood may exhibit different responses. Material thickness also influences the cutting process, with thicker materials requiring adjustments in power and speed settings.
Laser Power
Laser power is a fundamental parameter affecting edge quality. The power level determines the intensity of the laser beam, impacting the depth of material penetration and the overall cut quality. Higher power levels are often necessary for thicker or denser materials, but excessive power can lead to overheating and adversely affect the edge quality.
Assist Gases
Assist gases, such as oxygen, nitrogen, or air, play a significant role in CO2 laser cutting. They assist in removing molten material from the cutting area and preventing excessive heat buildup. The choice of assist gas depends on the material being cut and can impact the chemical composition of the cut edge. For instance, using oxygen with ferrous metals can enhance the cutting speed but may result in an oxidized edge.
Pre-processing and Post-processing Parameters
Pre-processing steps, such as material cleaning, surface preparation, and proper fixturing, can significantly impact edge quality. Additionally, post-processing techniques, including deburring, sanding, or coating, may be employed to enhance the final product’s appearance and functionality.
Summarize
CO2 laser cutting has revolutionized the manufacturing industry by providing a precise and efficient method for shaping a wide range of materials. Achieving high-quality edges is a complex interplay of various factors, including material properties, laser parameters, auxiliary gases, etc. Among them, the focus size of the CO2 laser generator plays a significant effect on the cutting results. Understanding and optimizing these factors can help improve consistency and achieve superior edge quality in CO2 laser cutting applications.
At AccTek Laser, we not only provide users with high-quality machines but also provide users with fast-response after-sales service. Whether it is the installation steps after you receive the machine, the technical optimization you want to achieve when using the machine, or the machine failure that needs to be solved, the AccTek technical team will provide you with free technical guidance and troubleshooting. When you need help, Acctek will be your faithful companion.
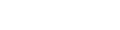
Contact information
- [email protected]
- [email protected]
- +86-19963414011
- No. 3 Zone A, Lunzhen Industrial Zone,Yucheng City , Shandong Province.
Get Laser Solutions