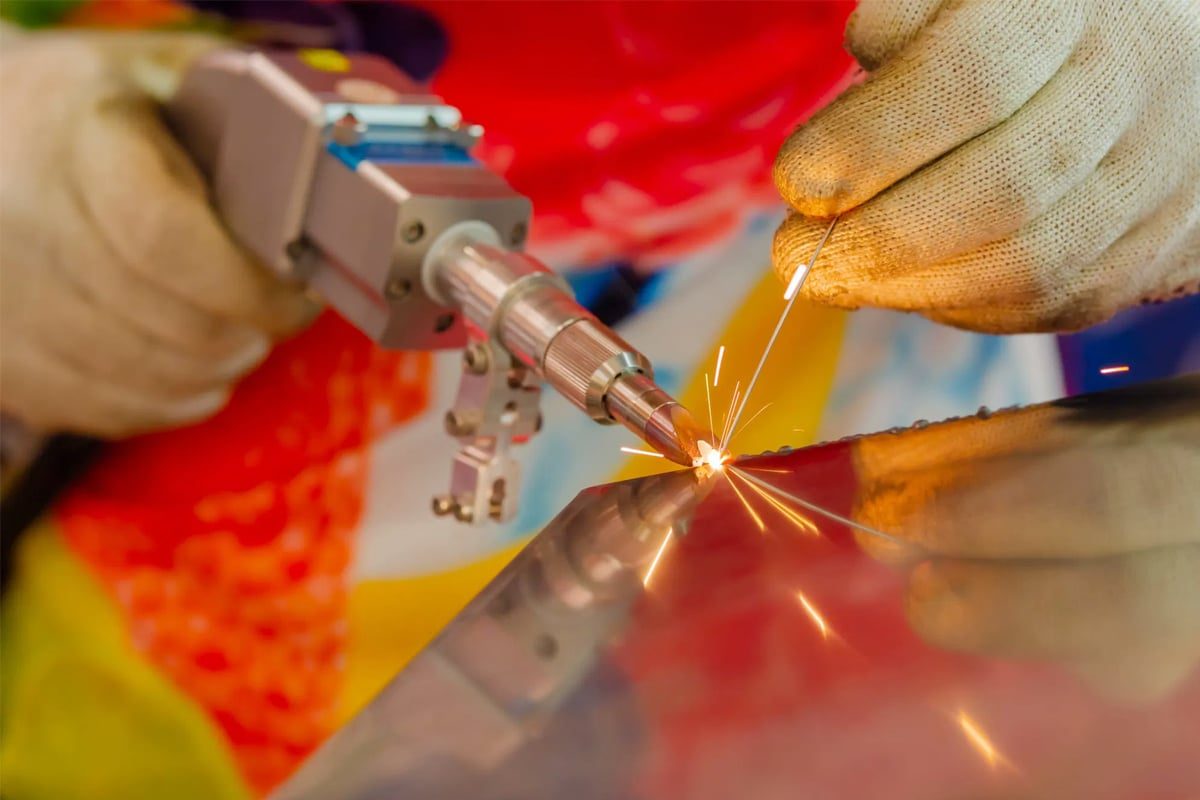
What Are The Factors That Affect The Thickness of Laser Welding
In laser welding, controlling weld thickness is essential for ensuring the strength, durability, and aesthetic quality of the joint. The thickness of a laser weld is influenced by a variety of factors, from laser settings like power, beam focus, and speed to the physical and chemical properties of the material being welded. Additionally, the design of the joint, the choice of shielding gas, and environmental conditions in the workspace play critical roles in determining how deeply the laser penetrates the material and the overall weld profile. By optimizing these factors, manufacturers can achieve precise weld thickness, which is especially important in industries where precision and consistency are crucial, such as automotive, aerospace, and electronics. This article explores the many variables that affect weld thickness in laser welding, offering insights into how adjustments in process parameters and materials can impact weld depth and quality.
Table of Contents
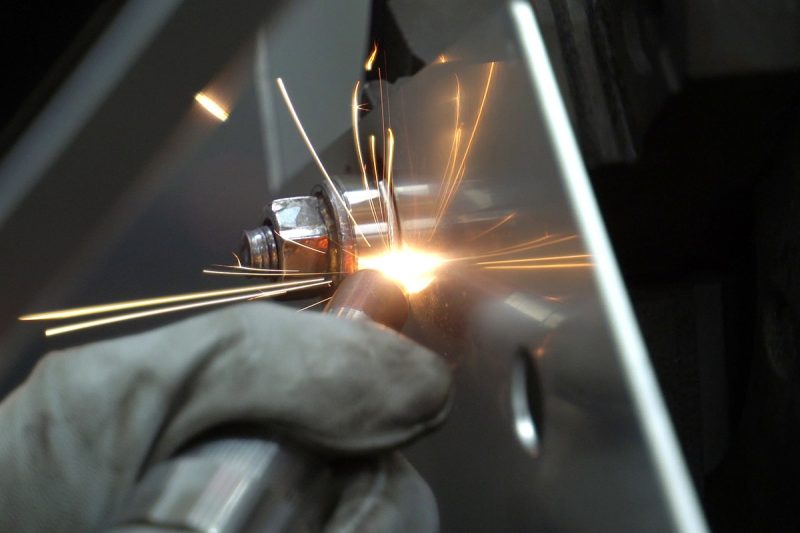
Understanding Laser Welding
Laser welding relies on a focused laser beam as an intense heat source to join materials, primarily metals. The laser beam, typically produced by a laser source like a fiber, CO2, or solid-state laser, is focused on the material’s surface. The intense energy from the laser rapidly heats and melts the target area, creating a molten pool that fuses the parts. As the laser moves along the joint, the molten pool solidifies, resulting in a continuous weld.
The high energy density of the laser enables precise and deep penetration with minimal heat-affected zones (HAZ), reducing thermal distortion in comparison to conventional welding methods. Laser welding can be performed in different environments, including vacuum chambers, inert gas atmospheres, or open air, depending on the specific application and material requirements. This versatility and precision make laser welding highly effective for complex geometries and materials with varying thermal properties.
Basics of the Laser Welding Process
The laser welding process typically involves three main stages: pre-weld preparation, laser-material interaction, and post-weld cooling and solidification.
- Pre-Weld Preparation: Before welding, the surfaces of the materials must be clean, free of contaminants, and properly aligned. Contaminants like oils, oxides, or debris can interfere with energy absorption and reduce weld quality.
- Laser-Material Interaction: During welding, the laser beam is focused onto the workpiece, where its energy is absorbed by the surface, leading to localized melting. There are two primary modes of laser-material interaction:
- Conduction Welding: This occurs when the laser power density is relatively low, causing surface melting without vaporization. The heat is conducted into the material, resulting in shallow and broad welds. This mode is often used for applications prioritizing aesthetics and low heat input.
- Keyhole Welding: When the laser power density is high enough to vaporize the material, it forms a keyhole or vapor cavity within the molten pool. The keyhole allows the laser energy to penetrate deeply, creating narrow and deep welds with a high aspect ratio. Keyhole welding is well-suited for thick materials and applications requiring strong joints.
- Post-Weld Cooling and Solidification: As the laser moves along the weld joint, the molten pool solidifies, forming a continuous bond between the materials. The proper cooling rate can prevent defects such as cracking or residual stresses and achieve the desired mechanical properties of the weld.
Laser welding offers high precision, minimal distortion, and the ability to produce clean and robust joints. However, factors such as laser power, beam focus, welding speed, and material characteristics must be carefully controlled to achieve the desired weld thickness and quality, making laser welding a complex and highly adaptable process for modern manufacturing.
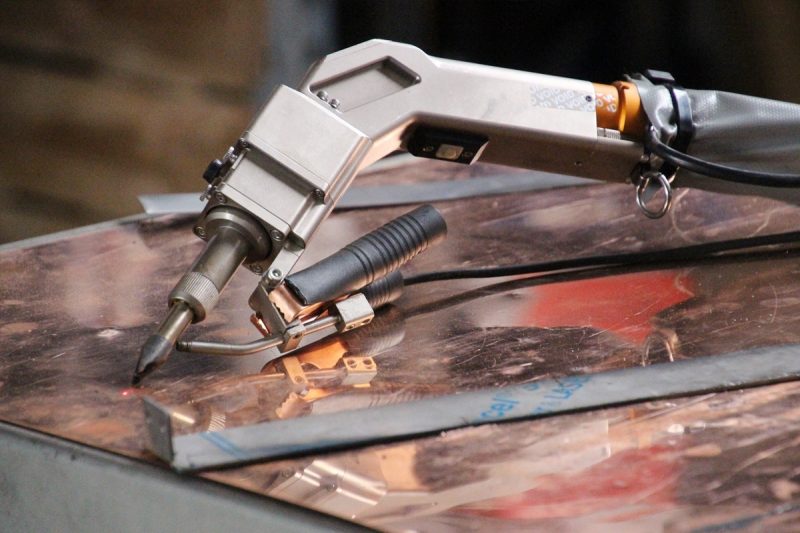
Applications of Laser Welding
Laser welding has become a cornerstone technology across numerous industries, owing to its precision, speed, and ability to produce high-quality, consistent welds with minimal thermal distortion. As manufacturing demands evolve, the versatility and adaptability of laser welding continue to make it an invaluable tool.
- Automotive Industry: In the automotive sector, laser welding is widely used for assembling car bodies, engine components, transmission gears, exhaust systems, and battery modules for electric vehicles. The process allows for strong, high-precision joints while minimizing the weight of components. Laser welding’s ability to join dissimilar materials, such as aluminum and steel, makes it especially useful for lightweight, energy-efficient vehicle designs.
- Aerospace Industry: Laser welding is vital in the aerospace industry due to its capacity to create precise and high-strength joints for critical components like turbine blades, structural frames, and fuel tanks. Its minimal heat-affected zone helps maintain the structural integrity of lightweight and heat-sensitive aerospace materials, such as titanium alloys and composites. Laser welding’s precision ensures compliance with stringent safety and performance standards.
- Energy and Power Generation: In the energy sector, laser welding is used for manufacturing components for wind turbines, solar panels, oil and gas equipment, and nuclear power plants. The ability to produce strong, defect-free welds ensures reliability and safety in high-pressure and high-temperature environments. Laser welding also supports the fabrication of heat exchangers, pipes, and high-pressure vessels.
- Shipbuilding and Marine Industry: The shipbuilding industry benefits from laser welding’s ability to produce strong, corrosion-resistant welds. It is used to join structural steel plates, hull components, and interior fittings. The process reduces the overall weight of marine vessels, increases fuel efficiency, and supports complex designs with high precision.
- Consumer Electronics and Appliances: Laser welding is employed in the assembly of consumer electronics, such as smartphones, tablets, and home appliances. It ensures reliable and aesthetically appealing joints in metal casings, connectors, and battery packs. The process supports automated high-speed production lines, enhancing productivity and consistency.
- Food and Beverage Industry: Laser welding is used in the food and beverage industry to produce stainless steel equipment, such as pipes, brewery equipment, and filling machines. The hygienic and seamless welds produced by laser welding prevent bacterial growth and simplify cleaning processes, making it ideal for food-grade applications.
- Construction and Architecture: Laser welding finds applications in the construction and architectural sectors for creating strong and aesthetically pleasing metal structures. It is used for fabricating structural beams, decorative elements, facades, and more. The process’s precision and speed enable the creation of custom designs and complex geometries.
- Agriculture and Heavy Machinery: The agricultural industry relies on laser welding for fabricating robust components for machinery and equipment, such as plows, tractors, and loaders. Laser-welded joints provide high strength and durability to withstand harsh operational conditions.
Laser welding’s diverse applications across industries highlight its role as a critical tool for modern manufacturing and engineering. The ability to control the thickness and quality of welds with precision ensures that laser welding meets the exacting demands of high-performance products, complex assemblies, and stringent regulatory standards.
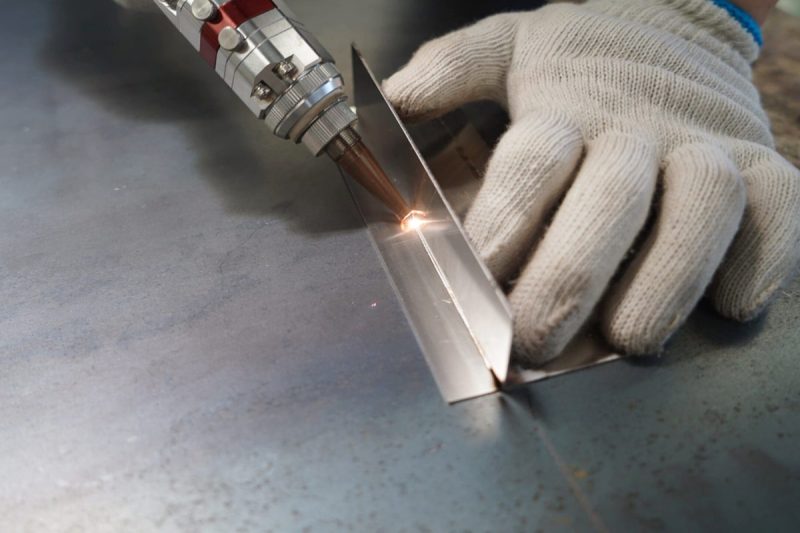
Factors Affecting the Thickness of Laser Welding
Achieving the desired thickness in laser welding is a complex process influenced by numerous factors. Each of these factors directly impacts the depth of penetration, quality, and integrity of the weld. Understanding these variables allows manufacturers to tailor the laser welding process for optimal thickness, strength, and precision.
Laser Power
- Impact on Weld Thickness: Laser power is one of the most critical factors in determining weld thickness. Higher laser power increases the energy input, allowing for deeper penetration and thicker welds. Conversely, lower power levels yield shallower welds, which may be more suitable for thin materials or applications where minimal heat input is required.
- Optimization: Adjusting laser power according to the material thickness and desired penetration depth ensures effective energy utilization. For thicker materials or deep welds, sufficient power must be applied to achieve the necessary penetration without causing excessive heat-affected zones (HAZ).
Welding Speed
- Impact on Weld Thickness: Welding speed, or the rate at which the laser moves along the joint, significantly influences weld thickness. A slower welding speed allows more laser energy to be absorbed by the material, resulting in thicker and deeper welds. Conversely, faster speeds reduce heat input, leading to shallower welds.
- Optimization: Balancing welding speed with laser power is essential for achieving the desired thickness. Excessively slow speeds may lead to overheating and defects, while high speeds can result in incomplete fusion or lack of penetration.
Focal Position
- Impact on Weld Thickness: The focal position of the laser beam affects where the energy is concentrated on the workpiece. Focusing the beam precisely on or slightly below the surface of the material can enhance penetration depth, resulting in thicker welds. Misalignment of the focal point can lead to inconsistent or insufficient penetration.
- Optimization: By adjusting the focal point according to material thickness and welding mode (conduction or keyhole), manufacturers can achieve more controlled weld thickness. Accurate focusing improves energy concentration and ensures consistent depth.
Beam Quality and Mode
- Impact on Weld Thickness: Beam quality and mode (TEM00, TEM01, etc.) affect how the laser energy is distributed across the work area. A high-quality, single-mode beam (TEM00) provides a more focused and intense spot, allowing for deeper penetration and thicker welds. Multi-mode beams, on the other hand, may lead to broader but shallower welds due to the spread of energy.
- Optimization: Selecting a laser with the appropriate beam quality and mode enhances control over weld thickness. For applications requiring deep, narrow welds, a high-quality, single-mode laser is ideal.
Material Properties
- Impact on Weld Thickness: Different materials respond to laser energy differently based on properties like thermal conductivity, melting point, and reflectivity. For example, metals with high thermal conductivity, such as aluminum and copper, dissipate heat quickly, requiring higher laser power to achieve desired penetration. Materials with high reflectivity may also reduce energy absorption, affecting thickness.
- Optimization: Understanding the specific material properties helps in adjusting laser parameters to achieve target thickness. For instance, reflective materials may benefit from surface treatments to improve absorption or require higher power for effective penetration.
Preheating
- Impact on Weld Thickness: Preheating the material before welding can reduce thermal gradients, allowing for smoother penetration and thicker welds. It also minimizes the risk of cracking in materials prone to thermal stress, such as high-carbon steels.
- Optimization: Preheating helps achieve consistent thickness, especially in thicker sections where rapid cooling could otherwise lead to defects. The degree of preheating should be controlled to prevent excessive thermal input.
Surface Condition
- Impact on Weld Thickness: The surface condition of the material, including cleanliness and oxidation, impacts energy absorption and penetration. Contaminants like oils, oxides, and dirt can reduce laser energy absorption, leading to inconsistent thickness and weaker welds.
- Optimization: Cleaning and preparing the surface before welding ensure that the laser energy is effectively absorbed, leading to controlled thickness. Surface treatments, such as grinding or sandblasting, can also improve weld quality.
Shielding Gas and Assisting Gas
- Impact on Weld Thickness: Shielding gas (such as argon, helium, or nitrogen) protects the weld pool from atmospheric contamination and can influence weld penetration and thickness. Different gases have varying thermal properties, which affect heat input and weld characteristics. Assist gases, often used in cutting, can also play a role in maintaining a stable weld pool.
- Optimization: Choosing the appropriate shielding gas enhances weld penetration. For instance, helium, with high thermal conductivity, can increase penetration, affecting weld thickness. Adjusting gas flow rates ensures sufficient shielding without introducing turbulence or defects.
Welding Mode (Conduction VS Keyhole)
- Impact on Weld Thickness: Laser welding can occur in conduction or keyhole mode, each of which affects the achievable weld thickness. Conduction welding produces broad and shallow welds, suitable for surface-level applications, while keyhole welding creates deep, narrow welds ideal for thicker materials.
- Optimization: Selecting the appropriate welding mode allows for precise control over thickness. Conduction mode is used when aesthetic surface welds are required, while keyhole mode is ideal for applications demanding greater penetration depth.
Joint Configuration
- Impact on Weld Thickness: The configuration of the joint, such as butt, lap, or T-joint, affects how the laser energy interacts with the materials and determines the achievable thickness. For instance, butt joints allow for full penetration welding, while lap joints may require more laser power for equivalent depth.
- Optimization: Choosing the correct joint configuration based on the material thickness and application requirements ensures effective energy distribution and weld thickness.
Laser Wavelength
- Impact on Weld Thickness: The wavelength of the laser impacts how effectively the material absorbs energy. For example, shorter wavelengths, such as those from fiber lasers, are absorbed better by metals than longer wavelengths from CO2 lasers, affecting penetration depth and weld thickness.
- Optimization: Selecting a laser with a wavelength that matches the material’s absorption characteristics ensures efficient energy use, allowing for optimal weld thickness.
Pre- and Post-Weld Processing
- Pre-Weld Processing: Surface preparation, cleaning, and alignment before welding improve the laser’s energy absorption, resulting in consistent thickness. Any contaminants or misalignments can cause defects or inconsistent penetration.
- Post-Weld Processing: Post-weld treatments, such as heat treatment or controlled cooling, influence weld structure and stability. Controlled cooling rates help maintain uniform thickness by preventing residual stress or warping.
- Optimization: Proper pre- and post-weld processing enhances weld quality, allowing for consistent weld thickness and mechanical properties.
Each of these factors plays a crucial role in determining the thickness and quality of laser welds. By carefully adjusting and optimizing each variable, manufacturers can achieve desired weld thicknesses, ensuring that laser welding meets the stringent requirements of various industrial applications.
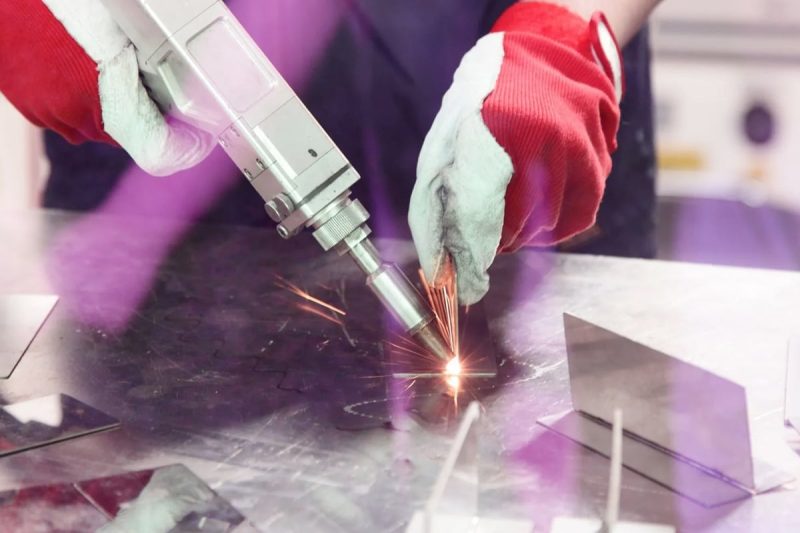
Optimizing Weld Thickness
Optimizing the thickness of laser welding involves carefully balancing multiple process parameters and employing strategies for precise control. Achieving the desired weld thickness is essential for ensuring weld strength, minimizing defects, and meeting design specifications.
Process Parameters Adjustment
Laser Power Adjustment
- Impact: Laser power directly affects the depth of penetration and weld thickness. Increasing power provides more energy to the weld pool, allowing for deeper and thicker welds, while reducing power results in shallower penetration.
- Optimization Strategy: To achieve optimal weld thickness, laser power should be carefully adjusted based on material properties, joint configuration, and thickness requirements. Excessive power can lead to defects like porosity or excessive melting, so it is crucial to find a balance that maximizes penetration while minimizing unwanted effects.
Welding Speed Control
- Impact: Welding speed determines the amount of time the laser interacts with the material. Slower speeds increase energy absorption, resulting in deeper and thicker welds, while faster speeds reduce heat input and yield thinner welds.
- Optimization Strategy: Adjusting the welding speed in conjunction with laser power ensures consistent thickness. Slower speeds can be used for thicker materials or deeper penetration, but they must be controlled to prevent overheating or excessive heat-affected zones.
Focal Position Adjustment
- Impact: The position of the laser focus relative to the material surface affects the concentration of energy. A focused beam at or slightly below the surface maximizes penetration and increases weld thickness, while an incorrectly aligned focal position can lead to inconsistent results.
- Optimization Strategy: Precise adjustment of the focal point ensures consistent energy delivery to the workpiece, enhancing weld thickness. Focal position adjustments may be needed for different materials or joint configurations to achieve desired results.
Beam Quality and Mode Optimization
- Impact: High-quality laser beams with a stable mode structure offer better energy concentration, leading to deeper and more controlled welds.
- Optimization Strategy: Ensuring the use of high-quality beams and selecting the appropriate beam mode helps in achieving precise and consistent weld thickness. Maintaining stable laser output and beam quality through regular equipment maintenance is key.
Shielding and Assist Gas Flow
- Impact: The type and flow rate of shielding gas influence the weld pool’s stability and penetration. Proper shielding protects against contamination and can enhance energy absorption, while assist gases help maintain a stable weld environment.
- Optimization Strategy: Selecting the appropriate shielding gas (e.g., argon, helium, or nitrogen) and adjusting flow rates to ensure optimal weld penetration and thickness. The shielding gas must be tailored to the material and welding conditions to maximize its effectiveness.
Preheating and Cooling Rates
- Impact: Preheating materials reduce thermal gradients, improving energy absorption and penetration. Cooling rates affect the solidification process and weld structure.
- Optimization Strategy: Implementing controlled preheating and post-weld cooling ensures uniform thickness and minimizes the risk of defects like cracking or warping.
Strategies for Control
Process Mapping and Simulation
Developing a process map that correlates laser parameters (e.g., power, speed, focal position) with weld thickness helps in identifying optimal settings for different materials and joint configurations. Welding simulation software can further assist in predicting the effects of parameter changes on weld thickness, reducing the need for costly trial-and-error.
Real-Time Monitoring and Feedback Systems
Implementing sensors and monitoring systems during laser welding provides real-time data on weld penetration, thickness, and quality. Automated feedback systems can adjust parameters in response to changes in the welding environment, ensuring consistent weld thickness.
Adaptive Control Systems
Advanced laser welding systems can automatically adjust laser power, speed, and other parameters based on real-time feedback. This capability minimizes variability and ensures uniform weld thickness across complex geometries or varying material conditions.
Surface Preparation and Material Conditioning
Proper surface preparation, including cleaning and conditioning, enhances energy absorption and weld consistency. Strategies such as grinding, sandblasting, or applying surface coatings improve laser energy interaction, resulting in more consistent thickness.
Optimization of Joint Design and Fit-Up
Minimizing gaps and ensuring precise alignment of components enhances energy transfer and consistency in weld thickness. Using appropriate clamping and fixturing techniques helps maintain optimal joint conditions during welding.
Process Validation and Testing
Conducting regular tests and validations of laser welding processes helps to identify optimal parameter settings for specific applications. Continuous process improvement ensures that weld thickness remains within desired tolerances.
By adjusting key process parameters and implementing effective control strategies, manufacturers can achieve optimal weld thickness, improve joint quality, and enhance the overall efficiency of their laser welding operations. These practices ensure that laser welding remains a reliable and versatile solution for diverse industrial applications.
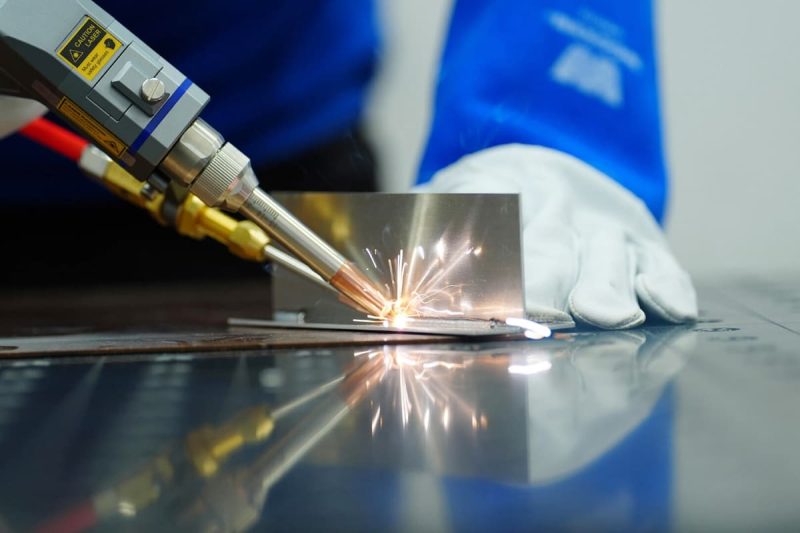
Challenges and Considerations
Optimizing the thickness of laser welding is not without its challenges. Various factors can impact the weld’s consistency, quality, and performance. By understanding common issues and implementing robust quality control measures, manufacturers can improve their processes and ensure reliable welds.
Common Issues
Inconsistent Penetration Depth
- Challenge: Variations in laser power, beam focus, material thickness, or joint alignment can lead to inconsistent penetration depths, affecting weld thickness. This inconsistency may result in weak joints, lack of fusion, or structural defects, compromising the weld’s integrity.
- Consideration: Regular calibration of the laser source, monitoring of beam focus, and precise control over welding parameters are essential for consistent penetration and weld thickness.
Heat-Affected Zones (HAZ)
- Challenge: Excessive heat input can create a large heat-affected zone, altering the material’s microstructure and reducing the mechanical properties near the weld. This can lead to warping, residual stress, or cracking, especially in materials sensitive to thermal stress.
- Consideration: Optimizing laser power and welding speed, as well as using appropriate shielding gases, can minimize heat-affected zones and maintain consistent weld thickness.
Porosity and Gas Entrapment
- Challenge: Entrapped gases within the weld pool can cause porosity, reducing the weld’s mechanical strength and leading to inconsistencies in weld thickness. Porosity may arise from contaminants, insufficient shielding gas, or improper process settings.
- Consideration: Cleaning the surface before welding, optimizing shielding gas flow, and reducing contaminants can minimize porosity. Real-time monitoring helps detect and address porosity issues early in the process.
Reflectivity of Materials
- Challenge: Highly reflective materials, such as aluminum and copper, reflect a significant portion of laser energy, leading to difficulties in achieving adequate penetration and consistent thickness. These materials may require special considerations to enhance energy absorption.
- Consideration: Surface treatments, such as coatings or texturing, and using lasers with shorter wavelengths can improve energy absorption and consistency for reflective materials.
Joint Misalignment and Gaps
- Challenge: Misaligned joints or gaps between components reduce the laser’s ability to achieve consistent penetration. This can lead to undercutting, incomplete fusion, and variable weld thickness.
- Consideration: Proper fixturing, alignment, and fit-up control ensure consistent joint conditions, reducing the likelihood of defects.
Thermal Distortion and Stress
- Challenge: Uneven heat distribution and rapid cooling can cause thermal distortion, residual stress, and warping, which may impact weld thickness and joint integrity.
- Consideration: Preheating, controlled cooling, and optimized welding speeds help reduce thermal stresses and maintain consistent weld dimensions.
Quality Control Measures
Real-Time Process Monitoring
- Measure: Implementing real-time monitoring systems provides feedback on key parameters, such as laser power, welding speed, and penetration depth. This enables immediate adjustments, reducing variations in weld thickness and improving overall consistency.
- Consideration: Optical sensors, temperature monitors, and laser feedback systems are examples of tools that can be used to maintain process stability.
Pre-Weld Surface Preparation
- Measure: Ensuring the workpiece surface is clean, free from contaminants, and properly prepared is critical to achieving consistent energy absorption and weld quality.
- Consideration: Surface treatments like grinding, degreasing, or applying coatings help minimize contaminants that could interfere with energy transfer.
Calibration and Maintenance of Equipment
- Measure: Regular calibration and maintenance of laser sources, optics, and other system components ensure stable beam quality, power output, and precision.
- Consideration: Periodic checks prevent performance degradation, which could impact weld thickness and overall quality.
Non-Destructive Testing (NDT)
- Measure: Techniques such as ultrasonic testing, radiography, and visual inspections help assess weld quality without damaging the part. NDT methods detect porosity, cracking, incomplete fusion, and other issues.
- Consideration: Implementing NDT procedures helps verify weld consistency and adherence to specifications, reducing the likelihood of product failures.
Use of Shielding Gas and Assist Gas
- Measure: Proper selection and flow control of shielding gases protect the weld pool from atmospheric contamination and influence weld penetration.
- Consideration: Adjusting the type and flow rate of shielding gases can minimize oxidation, porosity, and inconsistencies in weld thickness.
Welding Process Optimization
- Measure: Developing a process map that correlates laser parameters (e.g., power, speed, focal position) with weld thickness ensures optimal settings for different materials and joint configurations.
- Consideration: Continuous process improvement, backed by testing and simulation, enhances control over weld thickness and reduces variability.
Training and Skilled Operators
- Measure: Skilled operators with a deep understanding of laser welding parameters, materials, and techniques contribute significantly to maintaining weld consistency and quality.
- Consideration: Ongoing training and skill development enable operators to quickly identify and resolve issues, improving process control.
By addressing common challenges and implementing robust quality control measures, manufacturers can optimize laser welding processes for consistent weld thickness, high structural integrity, and superior quality.

Summary
The thickness of laser welding is a critical factor that influences the strength, precision, and overall performance of weld joints. Achieving optimal thickness requires a deep understanding of various factors, including laser power, welding speed, beam quality, focal position, material properties, and shielding gases. Adjusting these parameters ensures precise energy input and consistent penetration, resulting in high-quality, defect-free welds. Pre- and post-welding treatments, as well as joint configuration and surface conditions, further impact the welding outcome. By addressing common challenges such as inconsistent penetration, porosity, and thermal distortion, manufacturers can optimize weld thickness and enhance overall process reliability. Implementing robust quality control measures, including real-time monitoring, proper equipment calibration, and operator training, ensures consistent and dependable results. With these insights, laser welding remains an indispensable solution for industries demanding precision, strength, and high productivity.
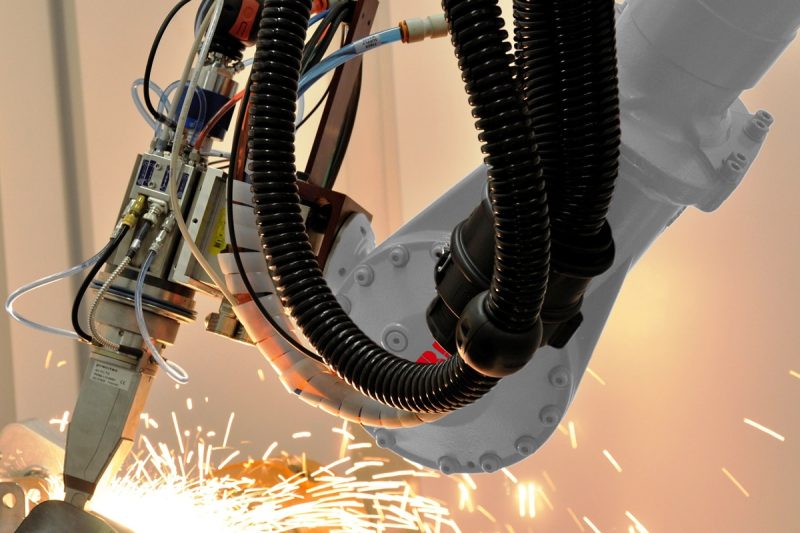
Get Laser Welding Solutions
Optimizing the thickness of laser welding is essential for achieving precise, strong, and reliable welds across various applications. At AccTek Laser, we provide advanced laser welding solutions tailored to meet the unique demands of your industry. Our state-of-the-art laser welding systems offer exceptional control over key parameters, such as laser power, beam focus, and welding speed, ensuring consistent penetration and high-quality results. Our expert team is dedicated to helping you select the right laser welding machine based on your material type, joint configuration, and specific application needs.
Whether you need to weld thin, delicate components or thick structural parts, AccTek Laser’s solutions deliver superior precision, minimal heat-affected zones, and unmatched efficiency. With our comprehensive support, including pre-sales consultation, system integration, training, and maintenance, you can optimize your welding process and achieve unparalleled performance. Contact us today to discover the perfect laser welding solution for your production requirements.
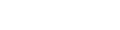
Contact information
- [email protected]
- [email protected]
- +86-19963414011
- No. 3 Zone A, Lunzhen Industrial Zone,Yucheng City , Shandong Province.
Get Laser Solutions