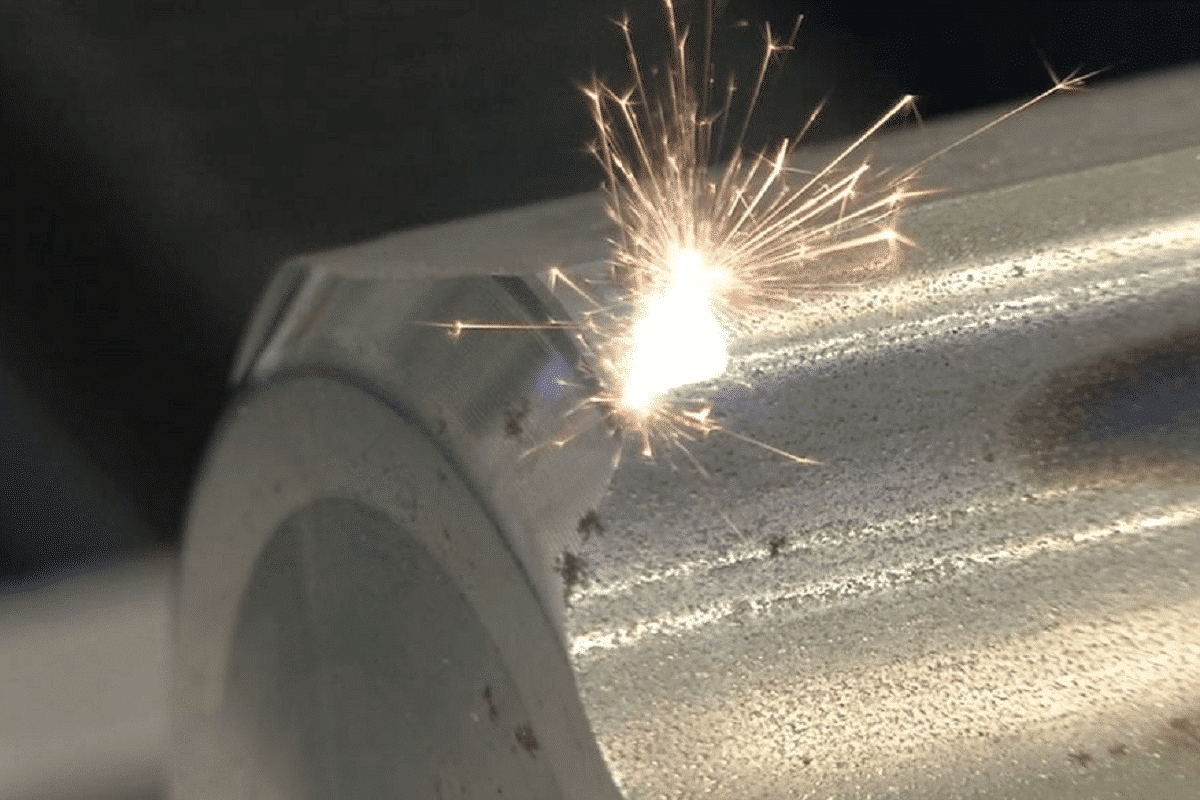
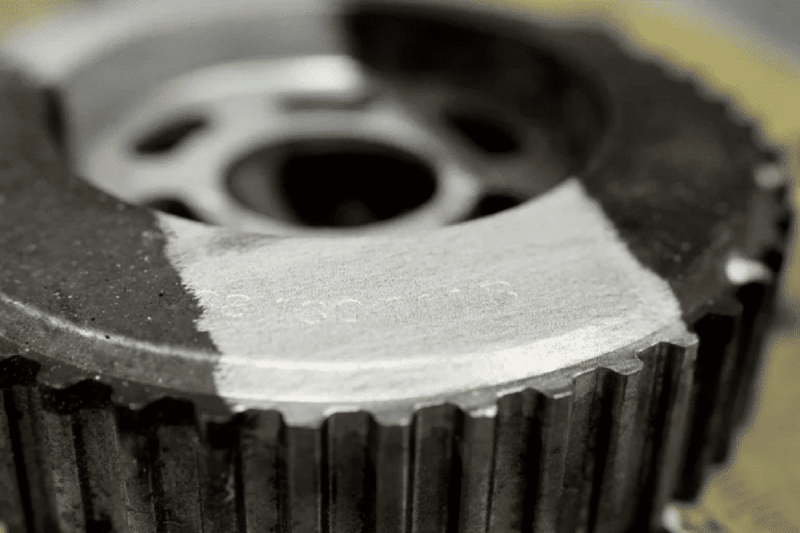
The working principle and advantages of laser cleaning
Laser cleaning is a high-tech surface cleaning technology that uses the high energy density of laser beams to directly evaporate or peel off harmful substances such as dirt, coatings, and grease attached to the surface by irradiating it, thereby cleaning the surface. the goal of. Compared with traditional cleaning methods, laser cleaning has unique advantages, making it widely used in many fields.
- No chemical cleaners required: Laser cleaning is a chemical-free cleaning method. Compared with traditional cleaning methods, laser cleaning does not require the use of chemical cleaning agents or solvents, thus avoiding the problem of chemical residues.
- High efficiency: The laser beam can focus on a small area with extremely high energy density, thereby completing the cleaning process in a short time.
- High precision: After focusing, the laser beam will be concentrated on a small area on the surface of the object. Therefore, using laser cleaning can clean every detail and corner of the surface of the object, and directly evaporate and peel off contaminants.
- Can be used on a variety of materials and surfaces: By adjusting the laser parameters, different materials can be cleaned without damaging the surface of the object. Laser cleaning can also effectively remove coatings and rust, providing a clean surface for subsequent painting or repair work.
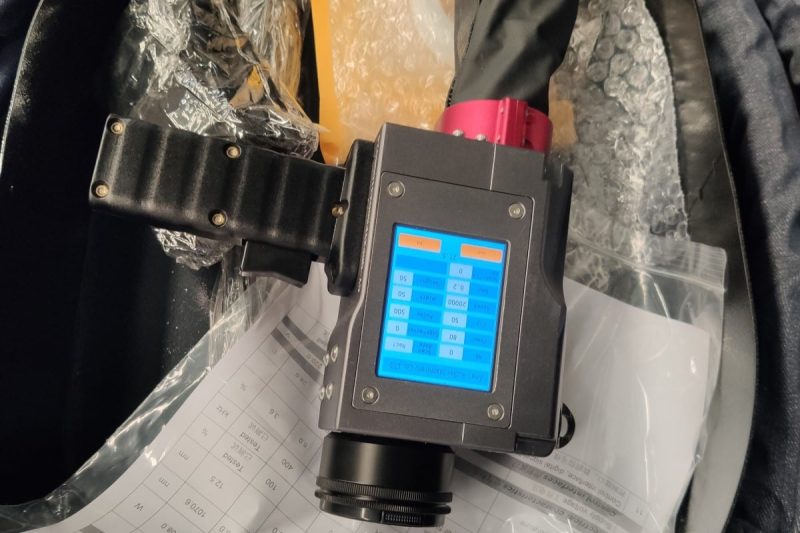
Limitations of laser cleaning
Limitations on surface properties of objects
Challenges of Energy Density Control
Laser beam propagation and focusing issues
Disposal of waste generated during cleaning
Cost and equipment complexity
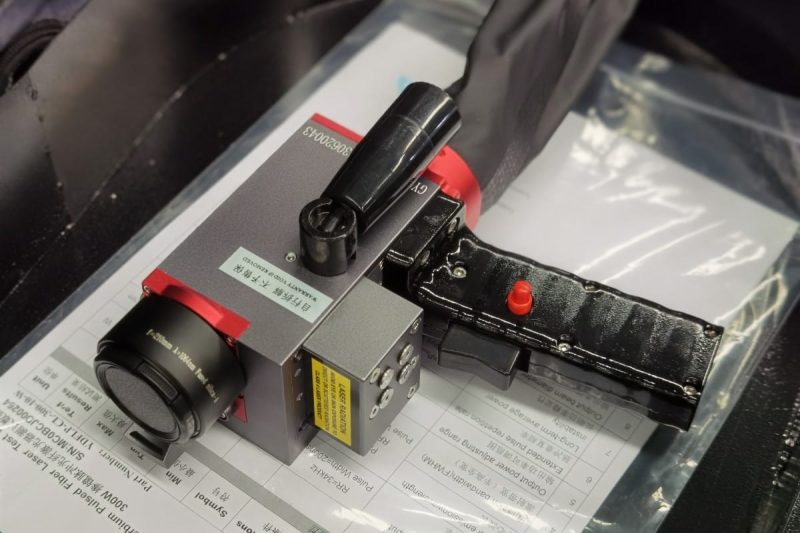
Limitations on the scope of laser cleaning
As an efficient, pollution-free surface treatment technology, laser cleaning still faces some limitations in its scope of application, which may become technical challenges for specific application scenarios. The following are the limitations of the applicable scope of laser cleaning:
- Highly reflective materials: The effect of laser cleaning is affected by the reflectivity of the surface of the object being cleaned. For materials with high reflectivity, the laser beam is easily reflected, resulting in a reduced cleaning effect.
- Special materials: For some special materials. For example, for materials that are easy to absorb moisture and easily oxidize, laser cleaning may cause undesirable chemical reactions and affect the performance of the material. In these situations, choosing the right cleaning method becomes crucial.
- Cleaning speed limit: Although laser cleaning is highly efficient in cleaning effects, the cleaning speed may be limited for large-area, high-volume cleaning tasks. This can be a challenge on production lines that require large-scale cleaning.
- Energy density requirements: Different object surfaces require lasers with different energy densities to achieve ideal cleaning results. Therefore, for some complex materials, more precise energy density control is required, which may increase the complexity and cost of the equipment.
- Safety considerations: High-energy-density laser beams may cause high temperatures during the cleaning process, and measures need to be taken to ensure the safety of operators. This may require special equipment and training, increasing the barriers to using laser cleaning technology.
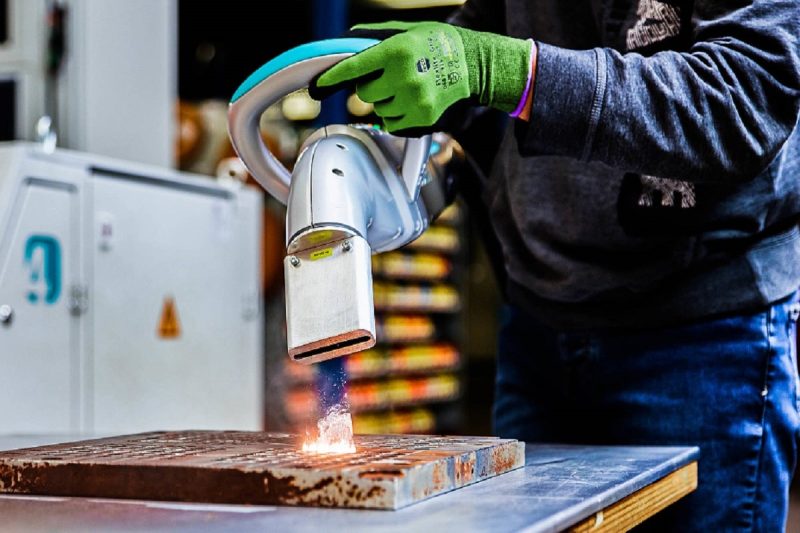
How to overcome the limitations of laser cleaning
Optimize laser parameters
Precise control of energy density
Innovative laser beam propagation and focusing technology
Development of multi-mode cleaning system
To deal with workpieces of different shapes and materials, the development of a multi-mode laser cleaning system can be considered. These systems can select appropriate laser modes according to specific needs, such as flying laser cleaning, handheld laser cleaning, etc., to adapt to different scenarios and workpiece cleaning needs.
Improve cleaning waste processing efficiency
Continue to reduce equipment costs and improve ease of use
Promote standardization and specification development
Summarize
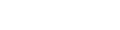
- [email protected]
- [email protected]
- +86-19963414011
- No. 3 Zone A, Lunzhen Industrial Zone,Yucheng City , Shandong Province.