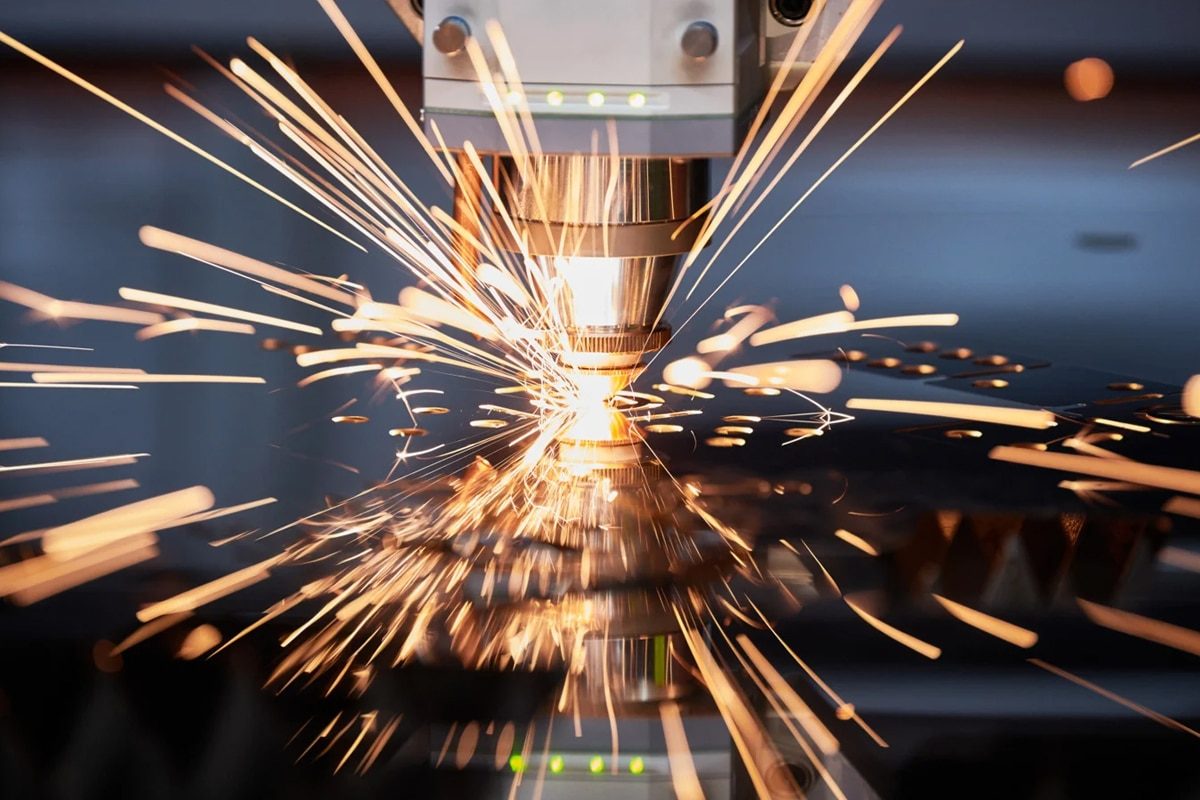
What Are The Three Main Types of Laser Cutting?
Laser cutting has become an integral part of modern manufacturing due to its precision, efficiency, and versatility. As a technology that uses concentrated, high-power laser beams to cut or engrave materials, it has reshaped how industries approach fabrication. The three main types of laser cutting—Fusion Cutting, Flame Cutting, and Sublimation Cutting—each brings distinct advantages and is suited for different materials and applications. Fusion Cutting excels in producing clean, oxide-free edges using inert gases, making it ideal for metals like stainless steel and aluminum. Flame Cutting, leveraging oxygen to produce an exothermic reaction, efficiently handles thicker carbon steel sections. Meanwhile, Sublimation Cutting, which vaporizes the material, offers exceptional precision for intricate designs in thin materials and non-metals. By understanding these three cutting processes, manufacturers can optimize their production strategies, ensuring top-tier results in quality and efficiency across various applications.
Table of Contents
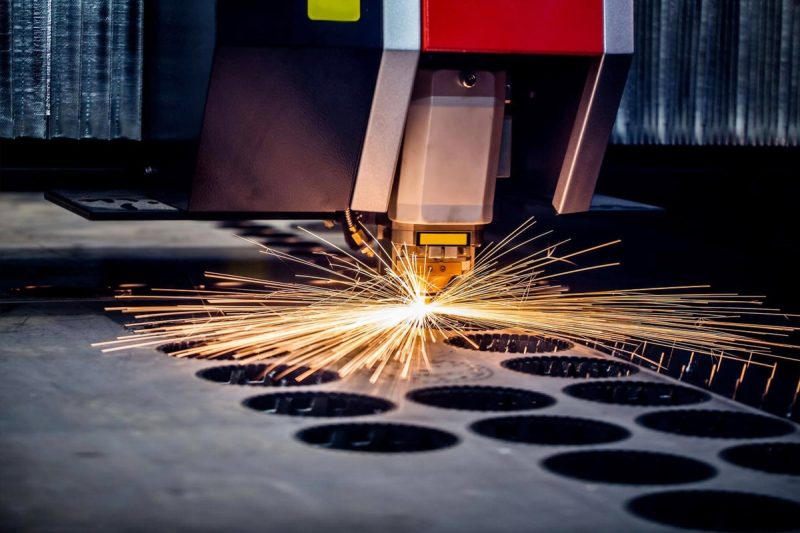
Overview of Laser Cutting
Laser cutting has revolutionized manufacturing, offering a precise, efficient, and versatile method for material processing across various industries. It involves the use of a high-power laser beam focused through optics and guided by CNC (Computer Numerical Control) systems to cut, engrave, or shape materials.
How Laser Cutting Works
Laser cutting is a thermal-based, non-contact process that uses a focused laser beam to melt, burn, or vaporize material, resulting in a clean and precise cut edge. Here’s a step-by-step breakdown of the process:
- Laser Source: A laser beam is generated by stimulating a lasing medium, typically CO2, fiber, or YAG, within a sealed chamber.
- Beam Delivery: The laser beam is directed through mirrors or fiber optics and focused onto the material using a lens, resulting in a highly concentrated heat source.
- Focusing and Cutting Head: The laser beam is directed through a cutting head, which also contains a nozzle that emits an assist gas (inert or reactive) to aid in cutting and material removal.
- CNC Control: The movement of the laser head and material is controlled by a CNC system, which precisely guides the laser path according to a programmed design.
- Cutting Process: The focused beam interacts with the material, either melting, burning, or vaporizing it while the assist gas blows away debris and molten material from the cutting zone.
Advantages of Laser Cutting
- High Precision and Accuracy: Laser cutting allows for intricate and complex shapes to be cut with tight tolerances, reducing the need for secondary processing.
- Versatility: It can cut a wide range of materials, including metals, plastics, wood, ceramics, and more, making it highly adaptable across industries.
- Minimal Material Waste: The narrow laser kerf (cut width) ensures minimal material waste, optimizing yield and reducing costs.
- Clean Cuts and Reduced Finishing: Laser cutting produces clean edges with minimal burrs, often eliminating or reducing the need for post-processing.
- High-Speed Processing: Compared to traditional methods, laser cutting can complete tasks faster, enhancing productivity and reducing lead times.
- Contactless Process: Since the laser beam does not physically touch the material, there is less risk of deformation, particularly for thin or delicate materials.
- Automation Compatibility: Laser cutting systems can be easily integrated with automated solutions, improving production efficiency and consistency.
Laser cutting continues to push the boundaries of what is possible in manufacturing, providing unparalleled precision, speed, and versatility to meet the demands of modern industries. By understanding the basics of how laser cutting works and its numerous advantages, manufacturers can harness this technology to optimize production processes and achieve exceptional results.
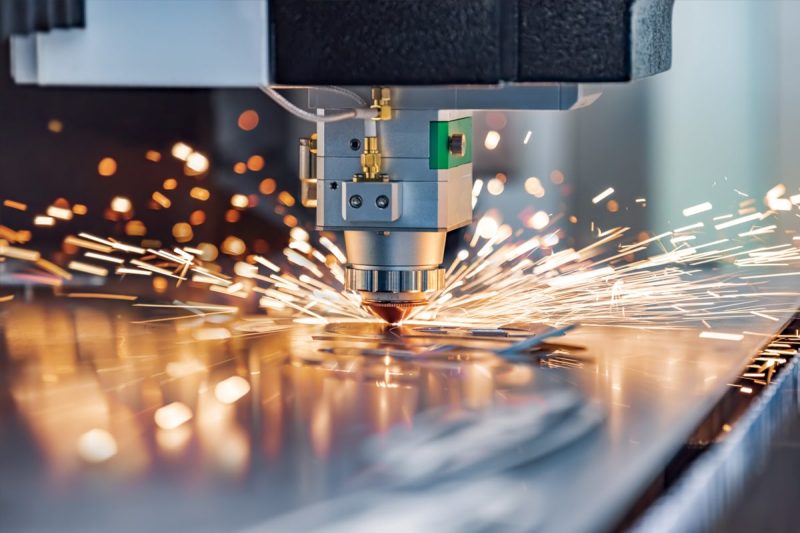
The Three Main Types of Laser Cutting
Laser-cutting technology encompasses several methods, each tailored to specific materials and desired outcomes. The three main types are Fusion Cutting (also known as Melt and Blow), Flame Cutting (Reactive Fusion Cutting), and Sublimation Cutting (Vaporization Cutting). Understanding the nuances of each process allows for the selection of the appropriate technology for a given application.
Fusion Cutting (Melt and Blow)
Explanation of the Process
Fusion cutting involves melting the material using a high-powered laser beam and then using an inert assist gas to blow the molten material out of the cut kerf. The assist gas, typically nitrogen or argon, does not chemically react with the material. Instead, it provides a high-pressure stream that efficiently removes molten metal from the cutting area, resulting in clean and precise cuts without oxidation.
The key steps in fusion cutting are:
- Melting: The laser beam focuses intense energy on a small area, rapidly heating and melting the material.
- Material Ejection: The inert assist gas blows the molten material away from the cut, preventing re-solidification and ensuring a smooth edge.
- Continuous Cutting: As the laser moves along the designated path, this process repeats, creating a continuous cut.
Materials Suitable for Fusion Cutting
Fusion cutting is ideal for materials that require high-quality, oxidation-free edges. Suitable materials include:
- Stainless Steel: Commonly cut using nitrogen to prevent oxide formation.
- Aluminum and Its Alloys: Requires higher laser power due to high reflectivity and thermal conductivity.
- Titanium and Nickel Alloys: Beneficial for aerospace and medical applications where material integrity is critical.
- Non-Ferrous Metals: Such as brass and copper, though they may need specialized lasers due to reflectivity.
Advantages of Fusion Cutting
- Oxide-Free Edges: The use of inert gas prevents oxidation, eliminating the need for post-cutting oxide removal.
- High Precision and Quality: Produces smooth, clean cuts with minimal thermal distortion.
- Minimal Post-Processing: Reduces the need for secondary finishing operations.
- Suitable for Complex Geometries: Can accurately cut intricate shapes and fine details.
Applications of Fusion Cutting
- Aerospace Industry: Manufacturing components that require precision and high-quality finishes.
- Medical Device Fabrication: Producing surgical instruments and implants with strict hygienic standards.
- Electronics: Cutting parts for electronic devices where precision is paramount.
- Automotive Industry: Fabrication of parts that require high-quality edges for assembly and aesthetics.
Technical Considerations
- Laser Power: Adequate power is necessary to melt the material efficiently, especially for thicker sections.
- Assist Gas Pressure: High-pressure inert gas is essential for the effective removal of molten material.
- Focus Position: Precise focusing ensures optimal energy concentration and cutting efficiency.
- Nozzle Design: Proper nozzle selection can enhance gas flow and improve cut quality.
- Material Reflectivity: Highly reflective materials like aluminum may require specialized lasers or coatings to prevent beam reflection.
Flame Cutting (Reactive Fusion Cutting)
Explanation of the Process
Flame cutting, also known as reactive fusion cutting or laser oxygen cutting, combines the laser’s heat with a chemical reaction to enhance the cutting process. In this method, oxygen is used as the assist gas. The laser heats the material to its ignition temperature, and the oxygen reacts exothermically with the metal (usually steel), releasing additional energy that assists in cutting.
Key steps in flame cutting:
- Heating: The laser beam heats the material to its kindling temperature.
- Exothermic Reaction: Oxygen reacts with the heated metal, combusting it and generating extra heat.
- Material Removal: The molten oxide is blown away by the oxygen stream, creating the cut.
Materials Suitable for Flame Cutting
Flame cutting is most effective on ferrous metals that can oxidize, such as:
- Carbon Steel: The primary material for flame cutting due to its reactive nature with oxygen.
- Low Alloy Steels: Steels with a small percentage of alloying elements.
- Mild Steel: Commonly used in construction and fabrication.
Advantages of Flame Cutting
- Cutting Thickness: Capable of cutting thicker materials compared to fusion cutting with the same laser power.
- Reduced Laser Power Requirement: The exothermic reaction supplements the laser, allowing for efficient cutting with lower power.
- Increased Cutting Speed: Especially effective on thick sections of steel.
- Cost-Effective: Oxygen is less expensive than inert gases like nitrogen or argon.
Applications of Flame Cutting
- Heavy Fabrication: Manufacturing of structural components like beams and plates.
- Shipbuilding: Cutting large steel sections for hulls and other structures.
- Construction Machinery: Fabrication of heavy equipment parts.
- Steel Service Centers: Processing of steel sheets and plates for various industries.
Technical Considerations
- Oxidation of Cut Edges: The process results in oxidized edges, which may require post-processing like grinding or sandblasting if a clean edge is necessary.
- Heat-Affected Zone (HAZ): Larger HAZ compared to other cutting methods, which can affect the mechanical properties of the material near the cut.
- Assist Gas Purity: High-purity oxygen improves the consistency and quality of the cut.
- Laser Focus and Alignment: Critical for initiating and maintaining the exothermic reaction.
- Material Thickness: Best suited for thicker materials where the exothermic reaction provides the most benefit.
Sublimation Cutting (Vaporization Cutting)
Explanation of the Process
Sublimation cutting, also known as vaporization cutting, involves converting the material directly from a solid to a gas phase without passing through a liquid state. The laser beam heats the material to its vaporization temperature, causing it to evaporate. An assist gas, often an inert gas like nitrogen, is used to remove the vaporized material from the cut kerf.
Key steps in sublimation cutting:
- Vaporization: The laser beam rapidly heats the material to its boiling point, causing it to vaporize.
- Material Ejection: The assist gas expels the vaporized material from the cutting area.
- Precision Cutting: The absence of molten material results in precise cuts with minimal thermal effects.
Materials Suitable for Sublimation Cutting
Sublimation cutting is ideal for materials that have low melting points or tend to burn or melt poorly. Suitable materials include:
- Wood and Paper Products: For engraving and precise cuts.
- Plastics and Polymers: Such as acrylics, polycarbonate, and other thermoplastics.
- Textiles and Fabrics: Cutting without fraying or damage to the material.
- Ceramics and Composites: Materials that are brittle or have high melting points.
- Thin Metals: When extreme precision is required.
Advantages of Sublimation Cutting
- High Precision and Detail: Ideal for intricate designs and fine details due to the minimal kerf width.
- Clean Cuts: Produces smooth edges without burrs or molten residues.
- Minimal Thermal Damage: Reduced heat input minimizes the heat-affected zone.
- Versatility: Capable of processing a wide range of non-metallic materials.
- Non-Contact Process: Eliminates mechanical stresses on delicate materials.
Applications of Sublimation Cutting
- Electronics Industry: Cutting and drilling of printed circuit boards (PCBs).
- Signage and Displays: Precise cutting of acrylics and plastics for high-quality displays.
- Medical Devices: Manufacturing components that require exact dimensions and clean edges.
- Fashion and Textiles: Cutting fabrics for clothing and accessories without edge fraying.
- Art and Crafts: Creating detailed designs in wood, paper, and other materials.
Technical Considerations
- Laser Power Density: High power density is required to achieve vaporization, especially for materials with high vaporization temperatures.
- Material Thickness: Best suited for thin materials; thick materials require significantly more energy.
- Assist Gas Selection: Inert gases prevent unwanted chemical reactions and help remove vaporized material.
- Ventilation Requirements: Vaporization produces fumes that may require proper extraction and filtration systems.
- Material Properties: Understanding the thermal properties of the material is crucial to prevent burning or charring.
By comprehensively understanding these three main types of laser cutting—Fusion Cutting, Flame Cutting, and Sublimation Cutting—manufacturers and engineers can select the most appropriate method for their specific applications. Each technique offers unique benefits and is suited to particular materials and requirements, making laser cutting a versatile tool in modern fabrication processes.
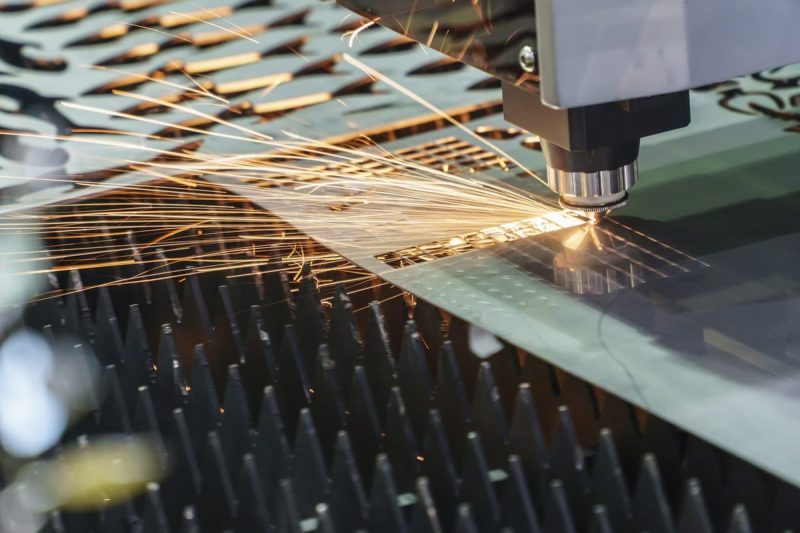
Comparison of the Three Cutting Methods
When considering the three main types of laser cutting—Fusion Cutting (Melt and Blow), Flame Cutting (Reactive Fusion Cutting), and Sublimation Cutting (Vaporization Cutting)—each method offers unique benefits and is suited to specific applications.
Process Mechanism
- Fusion Cutting (Melt and Blow): This method involves melting the material using a laser and blowing away the molten metal with an inert assist gas (e.g., nitrogen or argon). It produces clean, oxide-free edges and is ideal for precision cutting.
- Flame Cutting (Reactive Fusion Cutting): Flame cutting uses oxygen as the assist gas, which reacts with the heated material to create an exothermic reaction that adds heat to the process, enabling efficient cutting of thick materials like carbon steel. However, it leaves an oxidized edge.
- Sublimation Cutting (Vaporization Cutting): This process vaporizes the material directly using the laser beam’s heat, with an inert gas used to expel the vaporized material. It is well-suited for precise cuts on thin and non-metallic materials.
Material Compatibility
- Fusion Cutting: Suitable for a wide range of materials, particularly metals such as stainless steel, aluminum, and non-ferrous metals. It provides high-quality, oxidation-free cuts.
- Flame Cutting: Primarily used for cutting ferrous metals such as carbon steel and low alloy steels due to its reliance on an oxidizing reaction.
- Sublimation Cutting: Best for thin materials, including wood, plastics, textiles, ceramics, and certain metals, where precise, intricate cuts are required.
Edge Quality
- Fusion Cutting: Delivers clean, smooth edges with minimal burrs and no oxidation, reducing the need for post-processing.
- Flame Cutting: Results in oxidized edges that may require additional finishing, such as grinding, to remove the oxide layer if a clean surface is desired.
- Sublimation Cutting: Produces exceptionally clean edges, with minimal thermal distortion or burrs, making it ideal for applications where edge quality is paramount.
Cutting Speed and Thickness Capability
- Fusion Cutting: Effective for thin to medium-thickness materials with high precision, but its cutting speed decreases as material thickness increases.
- Flame Cutting: Offers high cutting speeds for thick materials due to the exothermic reaction with oxygen, making it efficient for heavy fabrication and structural components.
- Sublimation Cutting: Best suited for thin materials due to the high energy required for vaporization. While it provides high precision, it may not be efficient for thicker sections.
Assist Gas Usage
- Fusion Cutting: Inert gases like nitrogen or argon are used to prevent oxidation and produce a clean-cut edge.
- Flame Cutting: This relies on oxygen, which reacts with the metal to enhance the cutting process through an exothermic reaction.
- Sublimation Cutting: Often uses an inert gas or no gas, depending on the material, to expel vaporized material.
Heat-Affected Zone (HAZ)
- Fusion Cutting: Produces a relatively small heat-affected zone due to its focus on melting without additional reactions.
- Flame Cutting: This creates a larger heat-affected zone because of the exothermic reaction, which can alter material properties near the cut edge.
- Sublimation Cutting: Minimizes the heat-affected zone due to rapid vaporization, preserving the integrity of the surrounding material.
Applications
- Fusion Cutting: Ideal for applications where high precision and oxidation-free edges are critical, such as in the aerospace, medical, and electronics industries.
- Flame Cutting: Commonly used in heavy fabrication, construction, shipbuilding, and other applications requiring the cutting of thick steel sections.
- Sublimation Cutting: Best for detailed work on thin or delicate materials, such as in the electronics, textiles, and art and design industries.
Cost and Efficiency Considerations
- Fusion Cutting: Requires higher power and more expensive inert gases but offers superior edge quality and precision.
- Flame Cutting: More cost-effective for cutting thick carbon steel due to the use of oxygen, but post-processing may add costs.
- Sublimation Cutting: Energy-intensive for thicker materials, making it more suitable for specialized applications with thin materials.
Summary Table
Feature | Fusion Cutting | Flame Cutting | Sublimation Cutting |
Process Mechanism | Melts material, inert gas removes melt | Uses oxygen for exothermic reaction | Vaporizes material |
Materials | Metals like stainless steel, aluminum | Carbon steel, low alloy steels | Thin metals, non-metals, plastics |
Edge Quality | Clean, oxide-free | Oxidized, may need finishing | Clean, precise |
Cutting Thickness | Thin to medium | Thick materials | Thin materials |
Assist Gas | Inert gas (e.g., nitrogen, argon) | Oxygen | Inert gas or none |
HAZ | Small | Large | Minimal |
Applications | Aerospace, electronics, medical | Structural components, heavy fabrication | Electronics, textiles, art |
Cost Efficiency | Higher cost, high precision | Cost-effective for thick cuts | High precision, thin materials |
Each of these laser-cutting methods serves a specific purpose in modern manufacturing. By understanding the strengths and limitations of Fusion Cutting, Flame Cutting, and Sublimation Cutting, manufacturers can select the most appropriate process for their materials and desired outcomes, optimizing both cost and performance.
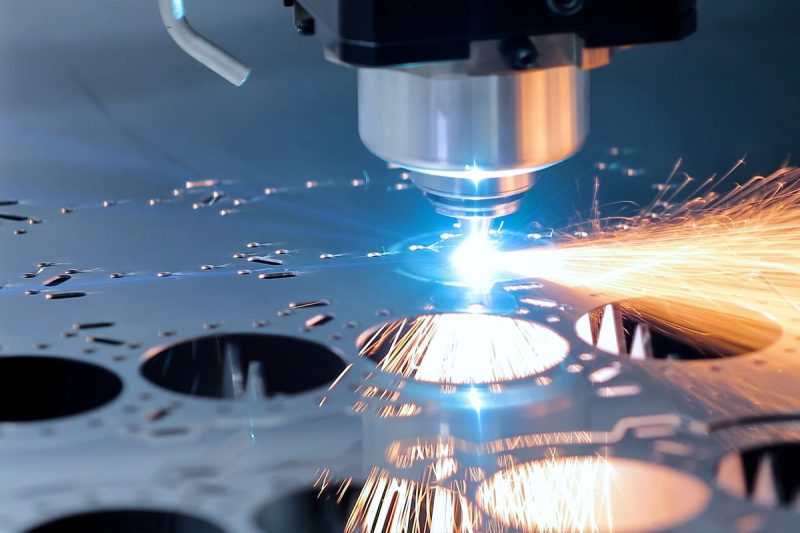
Choosing the Right Type of Cutting Method
Selecting the appropriate laser-cutting method is critical to achieving optimal results in terms of quality, efficiency, and cost-effectiveness. When choosing between the three main types of laser cutting—Fusion Cutting (Melt and Blow), Flame Cutting (Reactive Fusion Cutting), and Sublimation Cutting (Vaporization Cutting)—several factors must be considered, including material properties, desired edge quality, thickness, speed, and production requirements.
Material Type and Properties
- Metallic Materials: For metals such as stainless steel, aluminum, and other non-ferrous metals that require clean, oxide-free edges, Fusion Cutting is often the best option. The use of inert gases prevents oxidation, resulting in high-quality, precise cuts.
- Ferrous Metals: If you are cutting carbon steel or other ferrous materials, Flame Cutting offers excellent performance due to its use of oxygen to create an exothermic reaction. This method enables efficient cutting of thick materials but may result in oxidized edges.
- Non-Metallic and Thin Materials: Sublimation Cutting is ideal for non-metallic materials like plastics, wood, ceramics, and textiles. It is best suited for intricate designs and precise cuts, particularly for thin materials.
Desired Edge Quality
- Clean, Oxide-Free Edges: If a high-quality, clean edge without oxidation is crucial for your application, Fusion Cutting is preferred due to the use of inert gases that prevent oxidation during the cutting process.
- Oxidized Edges: In cases where a strong exothermic reaction is needed, and oxidized edges are acceptable or can be post-processed, Flame Cutting is a suitable option.
- High Precision and Smooth Edges: For applications that demand extreme precision and smooth edges with minimal thermal distortion, such as electronics and fine art, Sublimation Cutting is the right choice.
Material Thickness
- Thin to Medium Thickness: Fusion Cutting excels in thin to medium-thickness materials, providing precision and high-quality edges.
- Thick Materials: Flame Cutting is better suited for thicker materials, as the exothermic reaction allows efficient cutting with lower laser power requirements.
- Very Thin Materials: Sublimation Cutting is ideal for very thin materials and offers high precision for intricate patterns and shapes.
Cutting Speed and Efficiency
- High-Speed Production: If speed is a priority, particularly for cutting thick steel plates, Flame Cutting is highly efficient due to its oxygen-based exothermic reaction.
- Precision Over Speed: For applications where precision is more important than speed, Fusion Cutting and Sublimation Cutting provide superior results.
- Batch Production vs. Custom Work: Consider the nature of your production. Fusion Cutting is suited for high-precision batch processing, while Sublimation Cutting is ideal for custom work requiring intricate details.
Cost Considerations
- Assist Gas Costs: Fusion Cutting uses inert gases such as nitrogen or argon, which can be more expensive than oxygen used in Flame Cutting. However, it provides superior edge quality.
- Power Consumption: Sublimation Cutting can be energy-intensive for thick materials but is efficient for thin sections. Flame Cutting requires lower laser power due to the heat generated by the oxygen reaction, making it cost-effective for thick cuts.
- Post-Processing Requirements: The need for post-processing (e.g., oxide removal in Flame Cutting) can add to overall costs, which should be factored into the decision.
Application Requirements
- Precision-Critical Applications: For industries like aerospace, electronics, and medical device manufacturing where precision and clean edges are critical, Fusion Cutting and Sublimation Cutting are preferred.
- Heavy-Duty Fabrication: Flame Cutting is ideal for structural components, heavy machinery, and other applications requiring thick metal cutting.
- Intricate Designs: If fine details and intricate cuts are needed, especially for non-metallic materials, Sublimation Cutting is the best option.
Equipment and Setup Considerations
- Laser Power and Type: Ensure that the laser system you choose has adequate power and is compatible with the selected cutting method. For instance, highly reflective metals may require specialized laser sources in Fusion Cutting.
- Assist Gas Availability: Consider the availability and cost of assist gases. Flame Cutting typically uses oxygen, while Fusion Cutting requires inert gases.
- Automation and Integration: If you aim to integrate laser cutting into an automated production line, Fusion Cutting and Sublimation Cutting often offer better compatibility due to their precision capabilities.
Choosing the right type of laser cutting method depends on your material properties, desired cut quality, thickness, cost constraints, and specific application requirements. Fusion Cutting is ideal for high-precision, oxidation-free cuts on thin to medium-thickness metals. Flame Cutting excels in cutting thick ferrous materials efficiently, while Sublimation Cutting offers superior precision for thin materials and intricate designs. By carefully evaluating these factors, you can optimize your laser cutting process for maximum efficiency and quality, ensuring the best outcomes for your production needs.
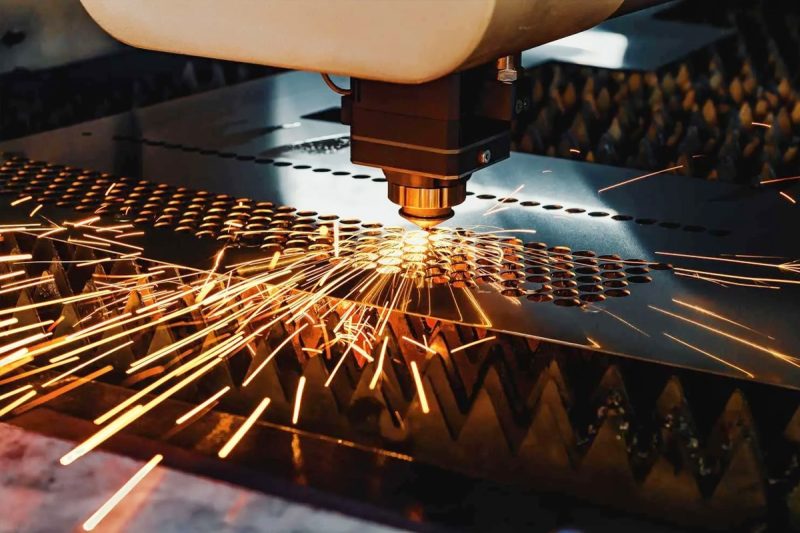
Summary
Laser cutting has become an essential technology in modern manufacturing, offering precision, versatility, and efficiency across a wide range of applications. The three main types of laser cutting—Fusion Cutting, Flame Cutting, and Sublimation Cutting—each serve distinct purposes. Fusion Cutting, using inert gases, delivers high-quality, oxide-free edges, making it ideal for metals such as stainless steel and aluminum. Flame Cutting employs oxygen to create an exothermic reaction, enabling efficient cutting of thick ferrous materials, which is particularly useful for heavy-duty fabrication. Sublimation Cutting vaporizes the material directly, providing exceptional precision for intricate designs and thin materials, including non-metals and specialized metal components. By understanding the capabilities and applications of each cutting method, manufacturers can optimize their processes for superior quality and cost-effectiveness, leveraging laser cutting to meet diverse industrial demands.
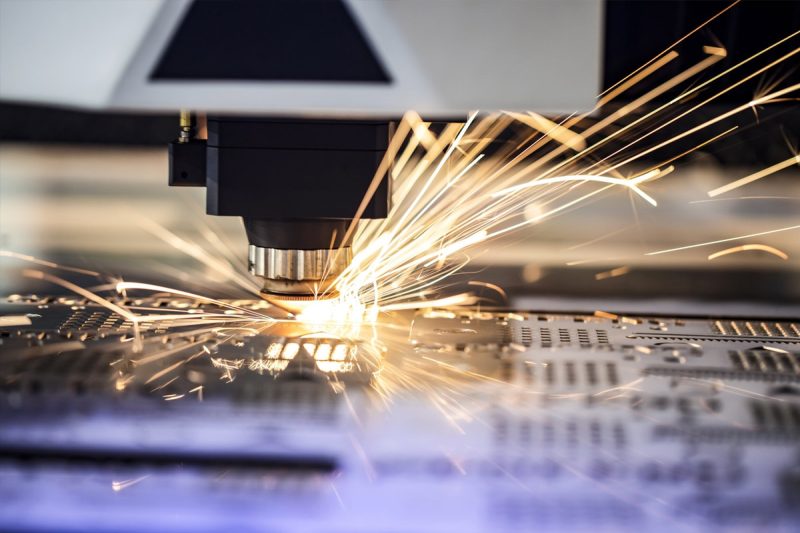
Get Laser Cutting Solutions
Choosing the right laser-cutting method is essential for achieving optimal precision, efficiency, and productivity in your manufacturing operations. Whether you need clean, oxidation-free cuts for metals, efficient processing of thick materials, or intricate designs on non-metallic substrates, AccTek Laser provides tailored laser cutting solutions to meet your exact needs. With expertise in Fusion Cutting, Flame Cutting, and Sublimation Cutting technologies, our laser cutting machines offer superior performance across diverse applications and industries. Our advanced systems are designed for high precision, minimal material waste, and maximum operational efficiency, ensuring the best results for your production goals.
AccTek Laser’s cutting solutions come with comprehensive support, including pre-sales consultation, custom configuration options, and reliable after-sales service. Whether you’re looking to enhance production capabilities or optimize your existing processes, AccTek Laser is here to provide state-of-the-art laser technology and expert guidance. Contact us today to find the perfect laser-cutting solution for your business.
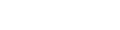
Contact information
- [email protected]
- [email protected]
- +86-19963414011
- No. 3 Zone A, Lunzhen Industrial Zone,Yucheng City , Shandong Province.
Get Laser Solutions