
What Are The Types of Laser Marking Machines?
Laser marking has become an essential technology in various industries due to its precision, speed, and versatility. Unlike traditional marking methods, laser marking creates permanent, high-contrast, and highly legible marks on a wide range of materials with minimal wear and tear. This non-contact process ensures consistent, durable marks that withstand harsh environments, making it ideal for traceability, branding, and customization.
The rise of laser marking technology has led to the development of different types of laser marking machines, each designed to meet specific material and application needs. From engraving intricate patterns on metal components to marking sensitive electronics and packaging, laser marking offers unmatched precision and adaptability. By understanding the different types of laser marking machines, businesses can select the optimal solution for their needs, enhancing product quality, efficiency, and compliance. This article explores the main types, their applications, and their distinct benefits and considerations.
Table of Contents
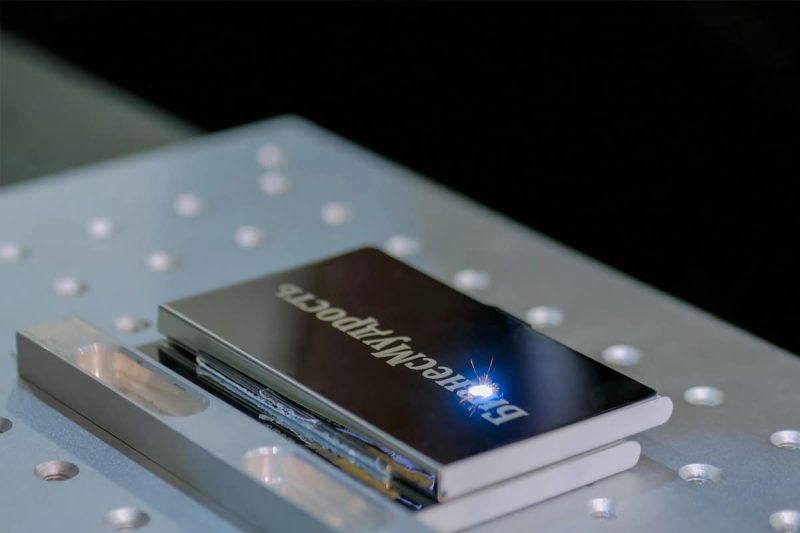
Understanding Laser Marking
Laser marking is a process in which a highly focused beam of light, known as a laser, alters the surface of a material to create permanent marks. This can include text, barcodes, serial numbers, logos, or intricate designs. Unlike traditional marking methods, laser marking does not rely on physical contact with the material, ensuring precise, high-contrast, and durable marks that can withstand harsh environments. The non-contact nature of the process minimizes wear and tear and allows for consistent marking on various materials such as metals, plastics, ceramics, and more.
How Does Laser Marking Work?
The process involves directing a laser beam onto the surface of a material with high precision. The laser’s energy interacts with the surface to induce physical or chemical changes, depending on the marking process used. The process is controlled by specialized software and a galvanometer scanning system, which accurately positions the laser beam to produce detailed, precise markings. The key variables in laser marking include laser power, speed, focus, and frequency, which are optimized based on the material and marking requirements.
Laser Marking Processes
- Annealing: Annealing is a heat-based marking process primarily used on metals. The laser heats the material, causing a change in its surface color without material removal. This results in a smooth, high-contrast mark that retains the material’s integrity. Annealing is commonly used for medical devices, automotive parts, and other components where corrosion resistance is critical.
- Engraving: Laser engraving removes material from the surface to create a deep mark. This process vaporizes material layer by layer, forming cavities visible to the naked eye. Engraving provides durable, permanent marks and is used for industrial components, jewelry, nameplates, and other items requiring lasting marks.
- Etching: Laser etching is a shallower marking process than engraving and involves melting the material’s surface to create a raised mark. It is faster than engraving, but the depth of the mark is less pronounced. Laser etching is suitable for marking metals, plastics, and other materials and is widely used in electronics, automotive, and consumer products.
- Foaming: Foaming involves creating gas bubbles within the material through laser-induced heating. This process alters the material’s color by producing raised, light-colored marks, especially on plastics. It provides high-contrast marks and is ideal for items such as medical instruments and packaging.
- Carbon Migration: Carbon migration occurs when a laser heats the surface of a material, causing carbon molecules to migrate to the surface, resulting in a dark mark. This process is commonly used for metal marking and provides excellent contrast. Carbon migration is particularly suitable for applications in aerospace, medical devices, and automotive components, where legibility and durability are essential.
Benefits of Laser Marking
Laser marking offers numerous benefits, making it a preferred solution for industrial marking and product identification:
- Permanence: The marks are resistant to wear, corrosion, heat, and other environmental factors.
- Precision and Consistency: Laser marking can produce highly detailed and repeatable marks, ensuring consistency across products.
- Non-Contact Process: Eliminates physical tool wear and reduces maintenance needs.
- Versatility: Works on a wide range of materials, including metals, plastics, glass, ceramics, and more.
- Speed and Efficiency: Delivers rapid marking without compromising quality, making it suitable for mass production.
- Eco-Friendly: No need for inks or chemicals, reducing waste and environmental impact.
By leveraging these different processes, laser marking machines provide unmatched flexibility, precision, and durability, meeting the diverse needs of industries worldwide.
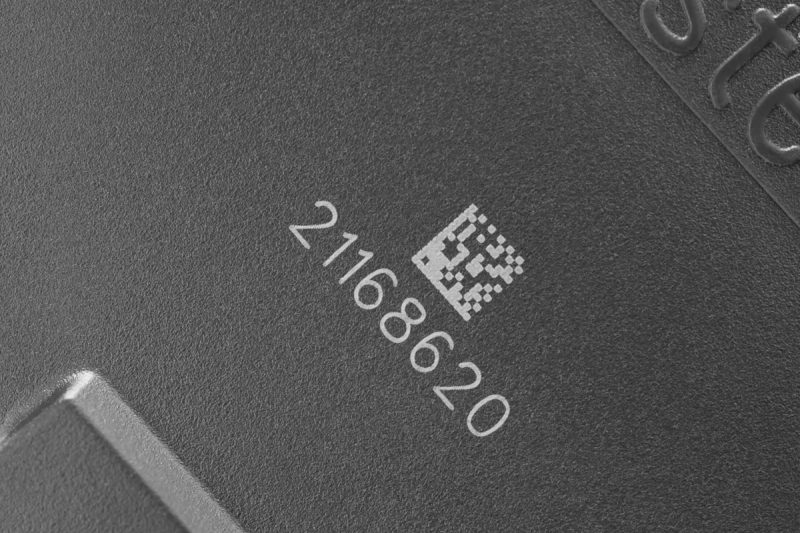
Types of Laser Marking Machines
Laser marking technology offers a range of machines, each designed to meet specific application needs, material compatibility, and marking requirements. Here’s a comprehensive overview of the primary types of laser marking machines, including their principles of operation, applications, advantages, disadvantages, and technical specifications.
Fiber Laser Marking Machines
Fiber laser marking machines operate using a fiber optic medium doped with rare-earth elements like ytterbium. The fiber acts as a gain medium, amplifying the laser beam at a wavelength of 1064 nm. This wavelength is particularly effective for marking metals and certain plastics due to its ability to achieve high energy density and precision.
Applications
Fiber laser marking machines are widely used across industries such as automotive, aerospace, electronics, medical, jewelry, and defense. Typical applications include marking barcodes, serial numbers, QR codes, logos, and text on metals, plastics, and some ceramics.
Advantages
- High Beam Quality: Produces precise, detailed, and permanent marks with a small focus spot size.
- Long Lifespan: Reliable performance with a lifespan of over 100,000 hours.
- Minimal Maintenance: Solid-state design with no moving parts.
- High Efficiency: Low power consumption and high electrical-to-optical conversion efficiency.
- Environmental Resistance: Robust against vibrations, dust, and temperature changes.
Disadvantages
- Material Limitations: Not as effective on transparent or organic materials.
- Cooling Requirements: High-powered versions require proper cooling systems.
- Initial Cost: Higher cost compared to some traditional marking systems.
Technical Specifications
- Power Range: Typically between 20W and 100W or higher.
- Marking Speed: Up to 7,000 mm/s.
- Repeatability: ±0.002 mm.
- Cooling Method: Air-cooled for lower powers, water-cooled for higher powers.
CO2 laser marking machine
CO2 laser marking machines generate a laser beam by electrically stimulating a gas mixture of carbon dioxide, nitrogen, and helium. The emitted wavelength is 10.6 μm, making it ideal for marking and cutting non-metallic materials such as wood, glass, leather, textiles, and certain plastics.
Applications
These machines are used in packaging, woodworking, textiles, glass etching, and other industries for marking, engraving, and cutting applications.
Advantages
- Versatility: Works on a wide range of non-metals.
- High Power Output: Suitable for both marking and cutting applications.
- Cost-Effective Operation: Low operating costs for non-metal applications.
- Large Format Capability: Can handle larger workpieces.
Disadvantages
- Limited Metal Processing: Generally ineffective on uncoated metals.
- Maintenance: Requires periodic replacement of gas tubes.
- Cooling Needs: Often water-cooled, adding complexity to the system.
Technical Specifications
- Power Range: From 10W to 150W or more.
- Beam Quality: Lower compared to fiber lasers.
- Marking Speed: Up to 5,000 mm/s.
- Cooling Method: Typically water-cooled.
UV Laser Marking Machines
UV laser marking machines operate at a wavelength of 355 nm by using frequency-tripled technology from infrared lasers. The shorter wavelength allows for “cold marking,” reducing thermal stress on materials and enabling high-precision marking.
Applications
UV lasers are ideal for applications that require high precision and minimal heat impact, such as marking on pharmaceuticals, cosmetics, plastics, electronics, and glass.
Advantages
- Minimal Thermal Impact: Reduces risk of deformation.
- High Absorption: Excellent for marking on a wide range of materials.
- Fine Marking: Capable of creating extremely precise and small marks.
- Clean Process: Minimal debris and fumes.
Disadvantages
- Lower Efficiency: Lower electrical efficiency compared to fiber lasers.
- Higher Cost: High initial investment due to complex technology.
- Limited Power Output: Typically not suitable for deep engraving.
Technical Specifications
- Power Range: From 3W to 15W.
- Spot Size: Can be as small as 10 micrometers.
- Marking Speed: Up to 3,000 mm/s.
- Cooling Method: Air-cooled for lower power levels.
Green Laser Marking Machines
Green lasers, with a wavelength of 532 nm, are achieved by frequency-doubling a 1064 nm laser source. This makes them highly effective for marking materials like copper, gold, and reflective surfaces.
Applications
Green lasers are widely used in the electronics industry, solar cell production, marking on glass and ceramics, and precision marking on precious metals.
Advantages
- High Absorption: Effective on materials that reflect longer wavelengths.
- Precision: Small spot sizes allow for detailed markings.
- Minimal Heat-Affected Zone: Reduces thermal impact on surrounding areas.
Disadvantages
- Higher Initial Cost: Advanced technology leads to a higher price point.
- Limited Power: Primarily for applications not requiring high output power.
- Niche Applications: Less commonly used than fiber or CO2 lasers.
Technical Specifications
- Power Range: Typically between 5W and 20W.
- Beam Quality: Excellent for fine detail.
- Marking Speed: Up to 3,000 mm/s.
- Cooling Method: Usually air-cooled.
MOPA Laser Marking Machines
MOPA lasers use a master oscillator and a power amplifier configuration, allowing adjustable pulse durations and frequencies. This flexibility makes them ideal for specialized marking needs.
Applications
Common applications include color marking on stainless steel, high-contrast black markings on anodized aluminum, and fine marking on plastics.
Advantages
- Adjustable Pulse Width: Greater control over marking results.
- High Contrast Marks: Ideal for creating bright or dark marks.
- Versatile: Suitable for both surface marking and deep engraving.
Disadvantages
- Complex Operation: Requires expertise to utilize fully.
- Higher Cost: More expensive than standard fiber lasers.
- Limited Awareness: Less common compared to other types.
Technical Specifications
- Power Range: From 20W to 350W.
- Pulse Duration: Adjustable from nanoseconds to microseconds.
- Marking Speed: Up to 7,000 mm/s.
- Cooling Method: Air-cooled for lower powers, water-cooled for higher powers.
3D Laser Marking Machines
3D laser marking machines use advanced galvanometer scanners and software to control the laser’s focus dynamically. This ensures consistent marking on complex 3D surfaces.
Applications
Used for marking on curved, inclined, or complex 3D surfaces in industries such as automotive, electronics, and consumer goods.
Advantages
- Dynamic Focusing: Consistent marking across varying heights.
- Improved Efficiency: Eliminates mechanical adjustments.
- Versatile: Capable of marking cylinders, spheres, and other 3D shapes.
Disadvantages
- Technical Complexity: Requires sophisticated software and hardware integration.
- Higher Cost: More expensive due to advanced components.
- Operator Training: Users need to be trained for full utilization.
Technical Specifications
- Power Range: Depends on the laser source (fiber, CO₂, etc.).
- Scanning Range: Larger Z-axis movement.
- Software: Advanced 3D design and control.
- Cooling Method: Varies by laser source.
Deep Laser Engraving Machines
Deep laser engraving uses high-powered lasers to remove significant layers of material, creating deeply etched marks. This requires precise control of laser parameters to achieve uniform depth.
Applications
Used in mold making, weaponry, tool manufacturing, and coin production, where deep, durable marks are essential.
Advantages
- Durable Marks: Resistant to wear and harsh conditions.
- High Precision: Creates detailed engravings with smooth surfaces.
- Material Versatility: Effective on a range of metals and alloys.
Disadvantages
- Slow Process: Requires multiple passes.
- High Energy Consumption: Deep engraving needs more power.
- Potential Thermal Effects: This may cause heat-affected zones.
Technical Specifications
- Power Range: Often above 100W.
- Depth Capability: Several millimeters.
- Cooling Method: Typically water-cooled due to high power.
By understanding the unique principles, applications, and benefits of each type of laser marking machine, businesses can select the most suitable solution for their specific needs, maximizing production efficiency and ensuring consistent, high-quality marks.
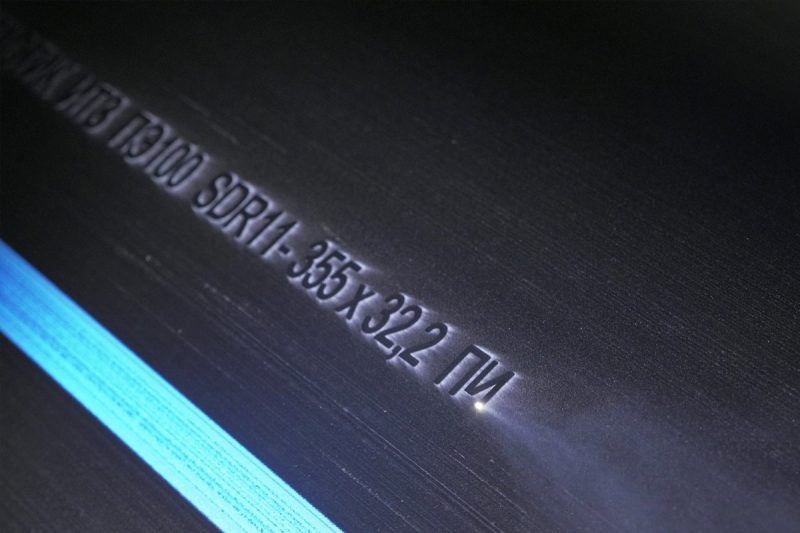
Comparison of Different Types of Laser Marking Machines
Selecting the right laser marking machine depends on various factors such as material compatibility, marking speed, precision, cost, maintenance needs, and overall versatility.
Material Compatibility
- Fiber Lasers: Best for metals like steel, aluminum, brass, and some plastics. Limited effectiveness on transparent materials.
- CO2 Lasers: Primarily for non-metals, including wood, leather, glass, textiles, and certain plastics. Limited use on metals unless they’re coated or treated.
- UV Lasers: Highly effective on sensitive materials like plastics, glass, and some metals, offering minimal thermal impact.
- Green Lasers: Well-suited for reflective materials such as copper, gold, and other metals; also works effectively on ceramics and glass.
- MOPA Lasers: Versatile across metals and certain plastics, especially good for color marking on metals and high-contrast markings on anodized aluminum.
- 3D Lasers: Compatible with a range of materials depending on the laser source, ideal for marking complex shapes.
- Deep Engraving Lasers: Primarily used for metals, especially in applications requiring long-lasting and highly durable marks.
Fiber lasers excel on metals, while CO2 lasers are best for non-metals. UV and Green lasers offer flexibility with sensitive or reflective materials, respectively. MOPA and 3D lasers are adaptable to diverse applications, and deep engraving lasers are designed for metals.
Marking Speed
- Fiber Lasers: High-speed marking, often up to 7,000 mm/s, making them suitable for high-volume production.
- CO2 Lasers: Moderate to high speed, generally up to 5,000 mm/s, but often slightly slower than fiber lasers.
- UV Lasers: Slower than fiber lasers, typically around 3,000 mm/s, as they’re designed for precision rather than speed.
- Green Lasers: Medium speed, typically around 3,000 mm/s, suitable for applications where high precision is needed over speed.
- MOPA Lasers: Comparable to fiber lasers in speed, reaching up to 7,000 mm/s, and allow for fast, high-quality marking.
- 3D Lasers: Speed varies depending on material and complexity, but dynamic focusing systems allow consistent marking without slowing down.
- Deep Engraving Lasers: Slower due to the need for multiple passes to achieve depth, which can impact productivity.
Fiber, MOPA, and CO2 lasers offer the highest speeds, making them ideal for fast production. UV, Green, and Deep Engraving lasers prioritize precision over speed.
Precision
- Fiber Lasers: Highly precise and suitable for intricate designs, especially on metal surfaces.
- CO2 Lasers: Moderate precision, generally sufficient for larger marks or non-metals but less detailed than fiber lasers.
- UV Lasers: Excellent precision due to minimal thermal impact, ideal for small, intricate markings on sensitive materials.
- Green Lasers: High precision, particularly effective for delicate materials and reflective metals.
- MOPA Lasers: High precision with adjustable pulse widths for customized fine marks, useful for color and high-contrast marking.
- 3D Lasers: Maintains precision on uneven or complex surfaces, allowing clear, consistent marks on three-dimensional objects.
- Deep Engraving Lasers: Precise for engraving deeper marks, especially suited for industries requiring permanent identification of metals.
UV, Green, MOPA, and Fiber lasers offer the highest precision, with 3D lasers adding the ability to maintain this precision on complex surfaces.
Cost
- Fiber Lasers: Moderate to high initial cost but offer good ROI due to durability and low operating costs.
- CO2 Lasers: Typically lower in cost than fiber lasers, especially for non-metal applications.
- UV Lasers: Higher initial cost due to advanced technology, generally more expensive than fiber and CO2 lasers.
- Green Lasers: Among the higher-priced options, suitable for specific applications, leading to higher initial investment.
- MOPA Lasers: Higher initial investment than standard fiber lasers, given their advanced pulse adjustment capabilities.
- 3D Lasers: Expensive due to advanced software and dynamic focusing systems for 3D marking.
- Deep Engraving Lasers: High initial cost, especially if high-powered, given the need for precision and multiple passes.
CO2 lasers tend to be the most cost-effective, while UV, Green, MOPA, and 3D lasers generally require a higher investment. Fiber lasers balance cost with durability and low operating expenses.
Maintenance
- Fiber Lasers: Low maintenance requirements due to solid-state design, making them a reliable choice.
- CO2 Lasers: Moderate maintenance, with regular replacement of gas tubes and optical components needed.
- UV Lasers: Higher maintenance needs, as components are sensitive and must be kept clean and free of dust.
- Green Lasers: Similar to UV lasers, requiring careful maintenance for optimal performance.
- MOPA Lasers: Low maintenance, similar to fiber lasers, but requires expertise for pulse adjustment and parameter setup.
- 3D Lasers: Higher maintenance due to complex scanning systems and software requirements.
- Deep Engraving Lasers: Moderate maintenance, with attention to the laser’s optical alignment and cooling systems due to high energy output.
Fiber and MOPA lasers are the most maintenance-friendly, while UV, Green, and 3D lasers require more attention due to complex components and sensitivity.
Versatility
- Fiber Lasers: Highly versatile for metal applications, including marking, engraving, and annealing.
- CO2 Lasers: Flexible for non-metal marking and cutting, especially with organic and softer materials.
- UV Lasers: Suitable for sensitive materials, including marking plastics, glass, and electronic components.
- Green Lasers: Good for reflective materials and specialized applications, though somewhat limited in material range.
- MOPA Lasers: Highly versatile, with adjustable pulse width enabling a wide range of applications, including color marking.
- 3D Lasers: Extremely versatile for marking complex 3D shapes and uneven surfaces.
- Deep Engraving Lasers: Limited to applications that require deep, durable marks, primarily on metals.
MOPA and 3D lasers offer the highest versatility across applications, followed by fiber and CO₂ lasers for their flexibility with metals and non-metals, respectively.
Summary Table
Feature | Fiber Laser | CO2 Laser | UV Laser | Green Laser | MOPA Laser | 3D Laser | Deep Engraving Laser |
Material Compatibility | Metals, some plastics | Non-metals | Sensitive materials | Reflective materials, glass | Metals, certain plastics | Complex 3D surfaces | Primarily metals |
Marking Speed | High | Moderate | Moderate | Moderate | High | Variable | Low |
Precision | High | Moderate | Very High | High | High | High | High |
Cost | Moderate | Low | High | High | High | Very High | High |
Maintenance | Low | Moderate | High | High | Low | High | Moderate |
Versatility | High | High (non-metals) | High for sensitive materials | Limited | Very High | Very High | Limited to deep marks |
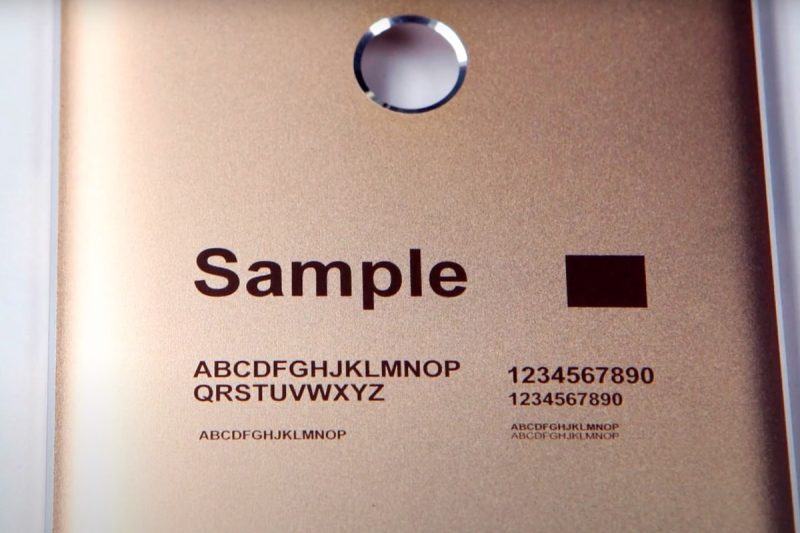
How to Choose the Right Laser Marking Machine
Selecting the optimal laser marking machine for your business involves more than simply choosing the most powerful or advanced option. It requires a careful evaluation of your specific needs, production goals, and budget constraints.
Assessing Material Compatibility
The type of material you need to mark plays a critical role in determining the suitable laser marking machine:
- Metals: For marking metals like steel, aluminum, brass, and titanium, fiber and MOPA lasers are excellent choices due to their high energy density and precision.
- Non-Metals: CO2 lasers are effective for marking on non-metal materials such as wood, glass, leather, paper, plastics, and textiles.
- Sensitive Materials: UV lasers are ideal for marking delicate and heat-sensitive materials, such as certain plastics, glass, and electronic components, due to their “cold marking” capabilities.
- Reflective Materials: For reflective surfaces such as gold, copper, or highly polished metals, green lasers are often preferred due to their shorter wavelength, which minimizes reflections and ensures clear marks.
Choosing the right laser for your material ensures optimal marking quality, speed, and durability.
Defining Application Requirements
Clearly defining your marking needs and objectives will help you choose the most suitable machine:
- Marking Type: Consider whether you need surface marking, deep engraving, or high-contrast color marking. Fiber lasers are versatile for metal applications, while MOPA lasers are suited for color marking.
- Production Volume: For high-speed, mass production environments, fiber or CO2 lasers offer fast marking speeds. If precision and detail are more critical, UV or green lasers may be more appropriate.
- Complexity of Marks: If your products have intricate designs, or fine details, or require consistent marking on uneven surfaces, a 3D laser marking machine may be necessary.
- Durability Requirements: Applications demanding long-lasting and abrasion-resistant marks, such as those in the automotive, aerospace, or medical device sectors, may benefit from deep engraving machines.
Tailoring your choice to specific application needs maximizes efficiency and ensures consistent results.
Evaluating Technical Specifications
Understanding the technical specifications of different laser marking machines is crucial for finding the right match:
- Laser Power: Higher power levels generally enable faster marking speeds and greater depth but may be excessive for certain delicate materials.
- Beam Quality: Precision and marking detail often depend on beam quality. Machines with high beam quality create smaller focus spots, resulting in more precise marks.
- Marking Speed: Consider the maximum marking speed of the machine if you require high throughput.
- Spot Size and Resolution: Smaller spot sizes allow for intricate markings and fine details, especially important for applications like jewelry engraving or electronic components.
- Cooling System: Machines may be air-cooled or water-cooled, with the latter providing better heat management for high-power systems.
Choosing a machine with the right technical specifications ensures optimal performance and output quality.
Considering Operational Environment
The operational environment where the machine will be used should also influence your decision:
- Space Constraints: If you have limited floor space, consider compact machines or desktop models. Fiber lasers often have a smaller footprint compared to CO2 systems.
- Environmental Conditions: Dust, temperature, and humidity levels can impact machine performance. Industrial environments may require sealed or robust systems with added protections.
- Ease of Use: Consider whether the machine is user-friendly and requires minimal training or if it involves complex setup and parameter adjustments.
Selecting a machine tailored to your operational environment minimizes disruptions and maximizes productivity.
Supplier Evaluation
Choosing a reputable supplier is essential to ensure long-term success with your laser marking machine:
- Reputation and Experience: Established manufacturers like AccTek Laser offer industry expertise, reliable products, and proven customer satisfaction.
- Technical Support and Training: Check if the supplier offers comprehensive technical support, operator training, and maintenance services.
- Customization Options: Some suppliers provide tailor-made solutions to meet specific production needs, offering flexibility that can enhance your operations.
- Service and Maintenance Contracts: Ensure that after-sales support and maintenance agreements are available to keep the machine running optimally.
Evaluating your supplier carefully helps you build a lasting and productive relationship.
Budget Planning
Cost considerations are vital when choosing a laser marking machine:
- Initial Investment: Determine your budget for upfront costs. Fiber and MOPA lasers often have a higher initial cost than CO2 lasers but may offer better long-term value.
- Operating Costs: Consider energy consumption, maintenance needs, consumable costs, and potential downtime. Fiber lasers tend to have lower operating costs.
- Return on Investment (ROI): Evaluate how quickly the machine will pay for itself through productivity gains, enhanced product quality, and lower operational costs.
- Financing Options: Some suppliers may offer leasing or financing options, allowing you to spread out costs and improve cash flow management.
Balancing initial investment, long-term costs, and projected ROI ensures you make a financially sound choice.
By carefully considering these key factors (material compatibility, application requirements, technical specifications, operating environment, supplier reliability, and budget constraints) you can select the right laser marking machine that meets your business goals. This decision will improve product quality, streamline production processes, and ultimately maximize your profitability.
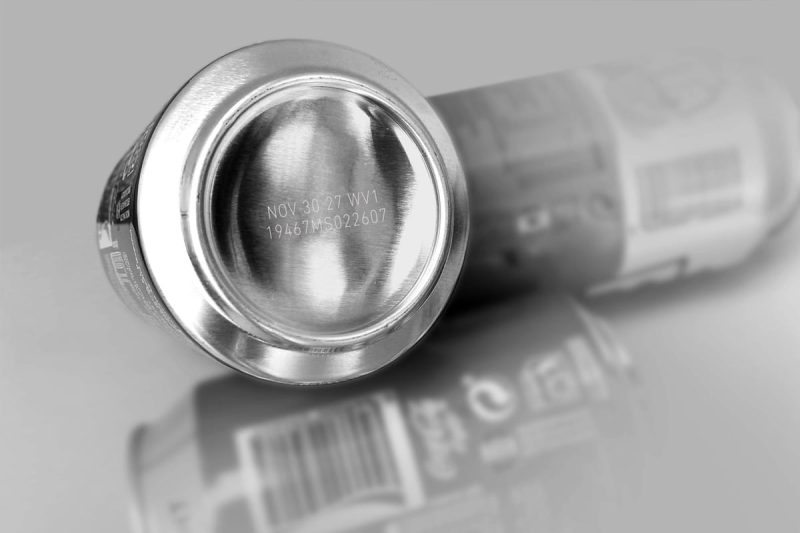
Summary
Laser marking technology offers a diverse range of machines tailored to meet specific industrial and application needs. Key types include fiber, CO2, UV, green, MOPA, 3D, and deep laser engraving machines. Each type provides unique advantages, such as fiber lasers excelling in marking metals with high speed and precision, while CO2 lasers are optimal for marking non-metallic materials like wood and glass. UV and green lasers offer precision on sensitive or reflective materials, and MOPA lasers provide unmatched flexibility for color and contrast marking. For complex geometries, 3D laser marking systems ensure precise marks on uneven surfaces, while deep engraving machines create durable, long-lasting marks.
Selecting the right laser marking machine depends on factors such as material compatibility, marking speed, precision, and application requirements. By understanding these distinct capabilities, businesses can enhance production efficiency, improve product traceability, and achieve high-quality marking results tailored to their needs.
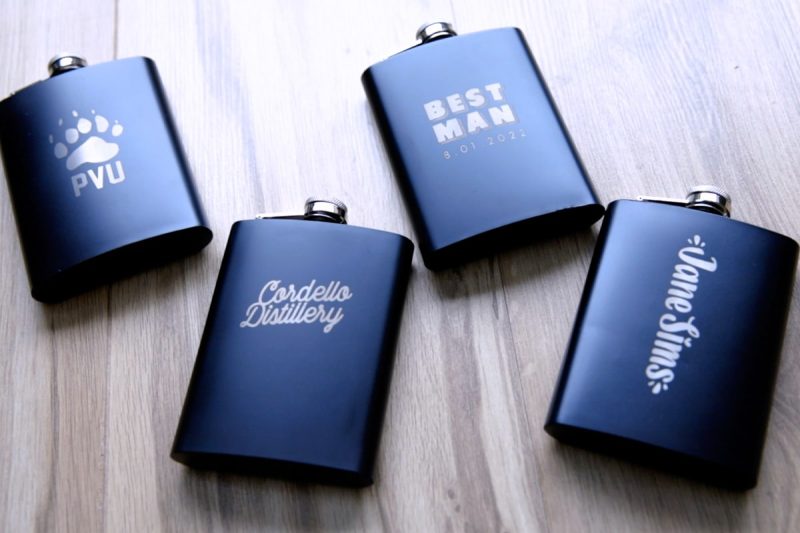
Get Laser Marking Solutions
Selecting the right laser marking machine is essential to achieve optimal marking performance, durability, and production efficiency. AccTek Laser offers a comprehensive range of laser marking solutions tailored to diverse industrial needs. Whether you require high-speed fiber lasers for precise metal marking, versatile CO2 lasers for non-metals, UV lasers for sensitive materials, or advanced MOPA and green lasers for specialized marking, AccTek Laser has you covered. Our machines are engineered for accuracy, consistency, and durability, ensuring high-quality, permanent marks on a wide range of materials.
With our extensive expertise, we provide personalized pre-sales consultation to understand your specific requirements and recommend the ideal solution. We also offer robust technical support, operator training, and customizable configurations to meet unique production needs. Trust AccTek Laser to deliver reliable, cutting-edge laser marking technology that enhances your operations and boosts product value and traceability. Contact us today to explore tailored laser marking solutions.
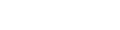
Contact information
- [email protected]
- [email protected]
- +86-19963414011
- No. 3 Zone A, Lunzhen Industrial Zone,Yucheng City , Shandong Province.
Get Laser Solutions