
What Causes Laser Welding Spatter?
As one of the important joining technologies in modern manufacturing, laser welding has been widely used in automotive, aerospace, electronics, and other fields due to its high precision, high efficiency, and adaptability to a variety of materials. However, any processing method, including laser welding, can produce defects or inferior products, and spatter is one of the common defects in laser welding. If you regularly use laser welding to weld various metals in your job, you need to understand why your laser welding machine produces spatter during the welding process and find out the best way to control the effects of spatter. This article will discuss in detail how to solve this situation.
Table of Contents
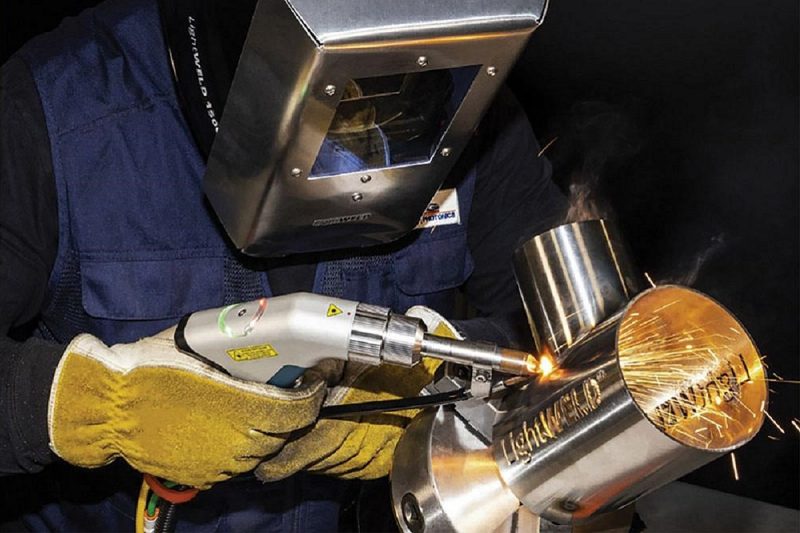
Phenomena and Effects of Laser Welding Spatter
Weld spatter is a common defect in laser welding. Laser welding spatter means that during the welding process, the molten metal in the welding pool is quickly sprayed out of the molten pool. After the metal material is heated to the melting temperature, it changes from a solid state to a liquid state continues to heat up, and transforms into a gaseous state. As the laser beam heats up, the solid metal becomes liquid and forms a molten pool. The liquid metal in the molten pool is then heated to “boil” again. Finally, the material again absorbs heat and vaporizes, and the boiling changes the internal pressure to form tiny droplets that carry the surrounding liquid metal and then land on the area around the weld, eventually creating a “splash”.
In addition, spatter may also cause problems such as pollution and failure inside the laser welding equipment, reducing the reliability of the equipment. These spatters may not only contaminate the weld seam and affect the welding quality but may also pose a threat to the health of welding workers. Therefore, corresponding control measures need to be taken to reduce or avoid the occurrence of spatter.
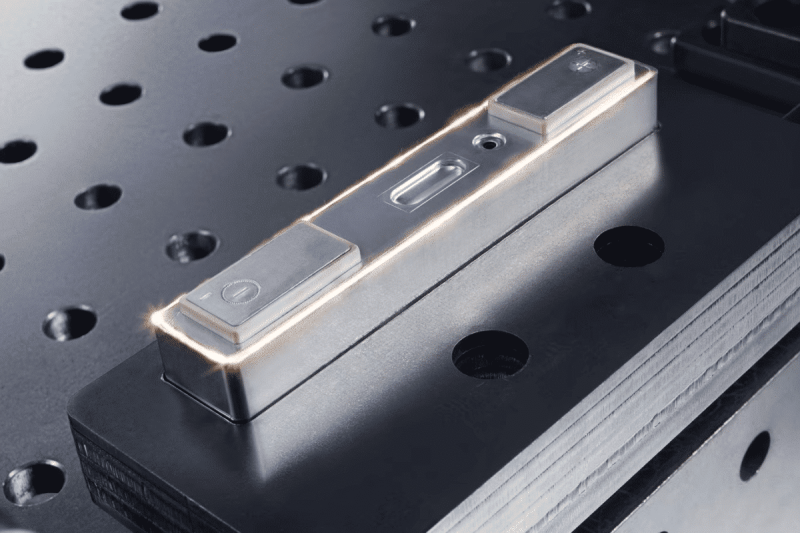
What Causes Laser Welding Spatter?
The cause of spatter in laser welding is the combined effect of many factors, involving material properties, welding parameters, weld design, and equipment conditions. Here are some common main causes of spatter in laser welding:
Material properties
The physical and chemical properties of materials are important factors affecting spatter in laser welding. Some materials are prone to gasification at high temperatures, producing gases that, when trapped in the weld pool, can cause jets and splashes of liquid metal as the bubbles expand and collapse. In addition, the surface coating and oxide layer of the material may also affect the stability of the weld pool and increase the probability of a spatter.
Welding parameters
The parameter settings of laser welding also affect the generation of spatter. For example, unreasonable settings of parameters such as laser power, scanning speed, and focal length may cause the temperature of the welding pool to be too high or unstable, thereby increasing the probability of a spatter.
Weld Design
Unreasonable weld seam design may also cause laser welding spatter. Factors such as weld shape, width, angle, etc. all affect the stability of the weld pool, which in turn affects the generation of spatter.
Equipment status
The state of the laser welding equipment can also affect the spatter. Problems such as the optical path of the equipment, the quality of the beam, and the stability of the welding head may cause the instability of the welding pool, resulting in a spatter.
Welding environment
Improper atmosphere control can lead to oxidation and other adverse reactions, increasing spatter generation.
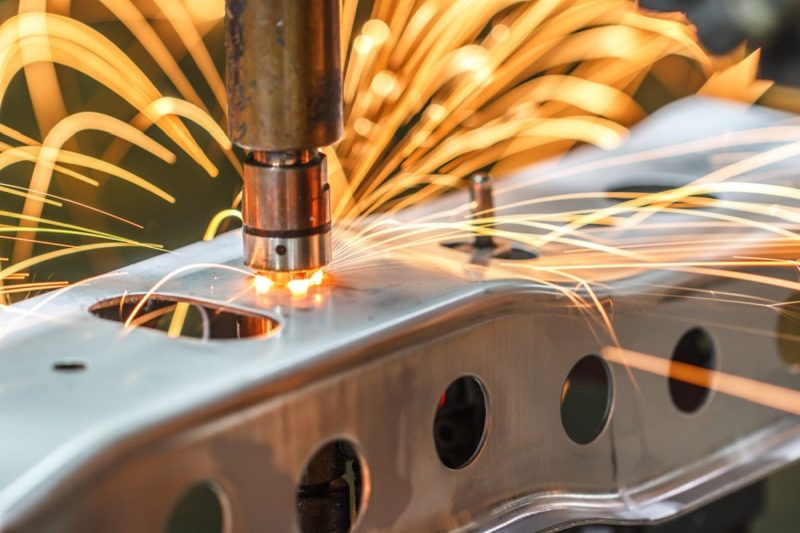
What are the hazards of laser welding spatter
Laser welding spatter can cause multiple adverse effects, involving welding quality, equipment stability, and personnel health. Here are some of the main hazards that laser welding spatter can create:
Impaired welding quality
Spatter may adhere to the surrounding areas of the weld pool, such as the weld pool and workpiece surfaces, creating an undesirable weld finish. This can lead to poor-quality welds and reduced weld strength, which can affect product performance and reliability.
Equipment contamination and failure
Spatter can be deposited on the optical path, welding head, and other critical components of laser welding machine. This may lead to equipment pollution and wear, leading to equipment performance degradation, and even triggering equipment failure, affecting the stable operation and life of the equipment.
Human health risk
Splashes may contain harmful substances such as molten metal particles, aerosols, etc. Workers may inhale these substances, causing respiratory and health damage. Especially in the case of long-term exposure, it may also cause respiratory problems, skin allergies, and other health problems.
Production efficiency decline
Spattering can lead to weld pool instability requiring weld pool correction or re-welding, which can reduce welding efficiency and productivity.
Subsequent processing difficulties
The spatter attached to the surface of the weld may make the subsequent surface treatment and coating process more difficult, increasing the cost and time of subsequent treatment.
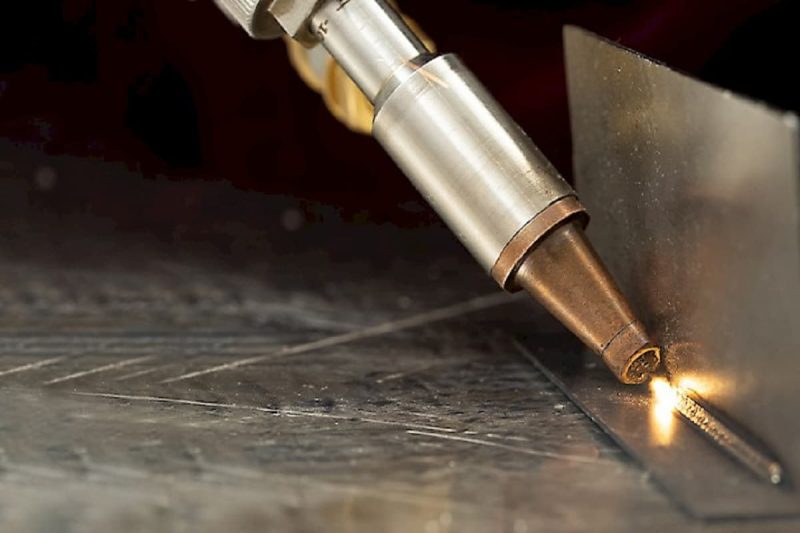
Methods of Controlling Spatter in Laser Welding
To control laser welding spatter, a variety of methods can be adopted, covering material selection, welding parameter optimization, weld design improvement, equipment maintenance, gas control, and other aspects. Here are some common methods of spatter control in laser welding:
Optimal material selection
During laser welding, materials with a lower gasification tendency can be selected to avoid the generation of air bubbles and reduce the probability of a spatter.
The reasonable setting of welding parameters
According to different materials and welding requirements, reasonably set the laser power, scanning speed, focal length, and other parameters to ensure that the temperature of the welding pool is stable within an appropriate range and reduce the occurrence of spatter.
Optimized weld design
In the welding design stage, factors such as weld shape, width, and angle are considered to make the weld pool more stable, avoid overly large or undersized welds, and reduce the possibility of spatter.
Equipment Maintenance and Calibration
Regular maintenance and calibration of laser welding equipment to ensure a smooth optical path, good beam quality, and a stable welding head can help reduce fluctuations in the welding pool, thereby reducing spatter.
Auxiliary gas control
Introduce a suitable shielding gas during the welding process. When high-purity, high-pressure argon is used as the shielding gas, many small bubbles will appear on the surface of the weld, which can suppress the generation of spatter to a certain extent. It can effectively reduce the generation of oxidation and gas in the welding pool, thereby reducing the probability of a spatter.
Reduce weld pool size
By controlling the welding parameters and weld seam design, the size of the weld pool is kept as small as possible to reduce the instability of the weld pool and the occurrence of spatter.
Use splash suppressant
Some special spatter inhibitors can be added during the welding process to help control the jet of liquid metal and reduce the occurrence of spatter
Welding Technology Training
Provide professional laser welding technology training for operators to understand the causes of spatter and control methods, which will help improve operating skills and reduce unnecessary spatter.
Summarize
Laser welding spatter is one of the important factors affecting welding quality and equipment stability. Its generation involves many factors such as material properties, welding parameters, weld design, and equipment conditions. By optimizing material selection, rationally setting welding parameters, optimizing weld seam design, equipment maintenance and calibration, and auxiliary gas control, the generation of laser welding spatter can be effectively reduced, welding quality and equipment reliability can be improved, and the further development of laser welding technology can be promoted.
AccTek Laser can meet all your specific needs. With our advanced equipment and experienced technicians, we are able to provide high-quality and precise welding solutions for your machined parts. Just contact us to start a new project!
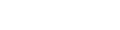
Contact information
- [email protected]
- [email protected]
- +86-19963414011
- No. 3 Zone A, Lunzhen Industrial Zone,Yucheng City , Shandong Province.
Get Laser Solutions