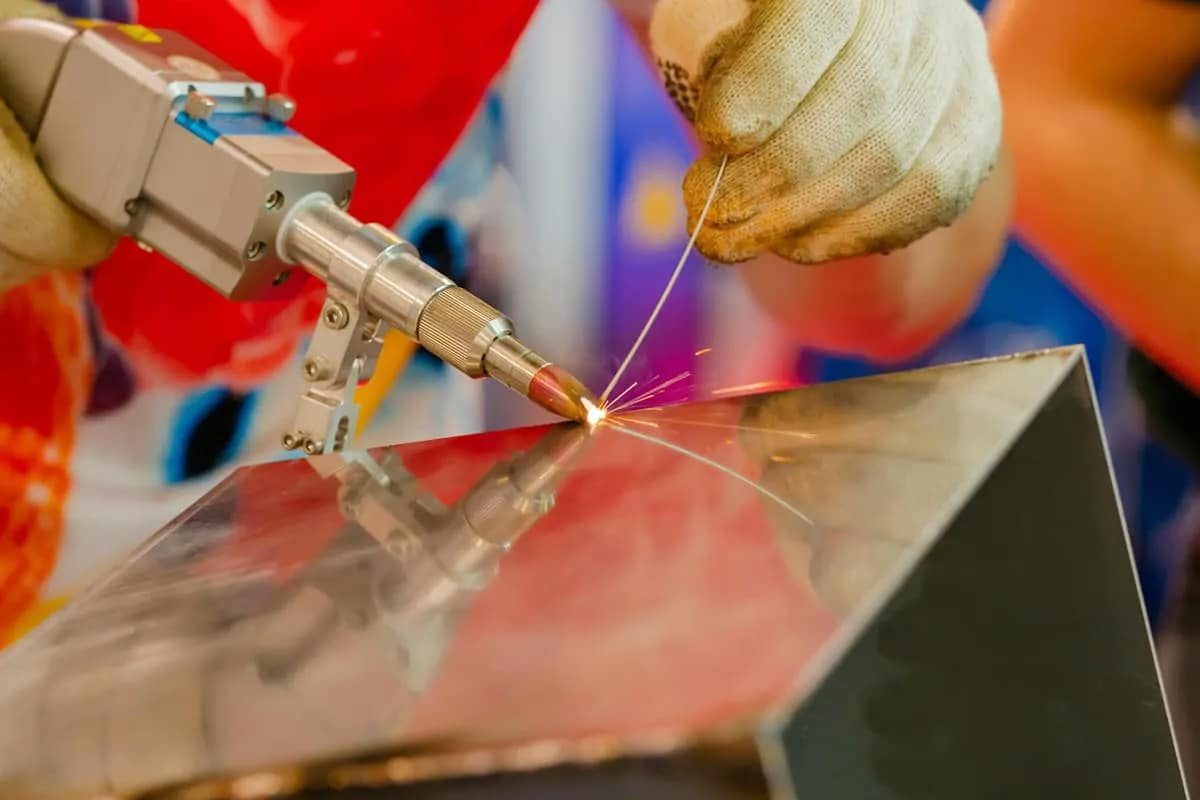
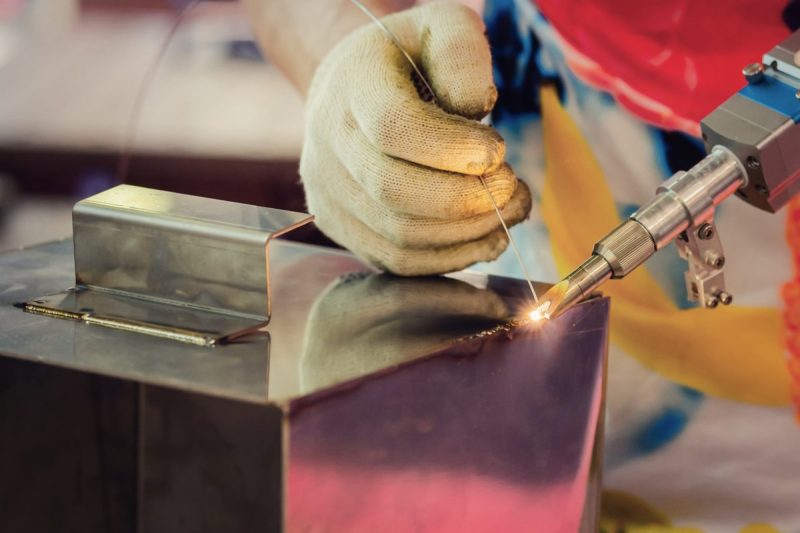
Laser Parameters
Laser Power
Laser power is a fundamental parameter in laser welding and determines the amount of energy delivered to the weld area. The power setting affects welding speed and penetration depth.
- High Power: Using high laser power increases welding speed and penetration depth, enabling the welding of thicker materials. It is particularly useful for applications that require deep welds or high productivity. However, too high a power can lead to overheating, excessive melting, and defects such as spatter and porosity.
- Low Power: Lower laser powers are suitable for thinner materials and applications that require high precision, such as micro welding. However, insufficient power can result in weak welds due to incomplete fusion or insufficient penetration.
- Optimization: Achieving optimal laser power requires balancing penetration and speed needs with defect risks. This requires careful calibration based on material type, thickness, and specific welding requirements.
Wavelength
The wavelength of a laser affects how well the material being welded absorbs the laser energy. Different materials have different absorption characteristics at different wavelengths.
- Common Wavelengths: Typical wavelengths used in laser welding include infrared (IR), visible light, and ultraviolet (UV). Each wavelength has its advantages, depending on the material and application.
- Infrared (IR) Lasers: IR lasers, such as CO2 and fiber lasers, are commonly used to weld metals and are effective on materials with high absorption in the infrared spectrum.
- Visible and UV Lasers: These wavelengths are more easily absorbed by nonmetals and some reflective metals, making them useful for applications involving plastics and ceramics.
- Material-Specific Considerations: Materials such as aluminum and copper that are highly reflective in the infrared range may require lasers with wavelengths that are more easily absorbed by these metals. Special coatings or laser sources with specific wavelengths can enhance absorption and welding efficiency.
Pulse Duration and Frequency
Pulse duration and frequency are critical parameters in pulsed laser welding, where the laser operates in short pulses rather than a continuous wave.
- Pulse Duration: The length of each laser pulse can significantly affect the thermal characteristics of the weld. Shorter pulses deliver energy in brief, intense bursts, minimizing the heat-affected zone (HAZ) and reducing thermal deformation. Longer pulse durations deliver more energy but can increase the HAZ and risk of thermal damage.
- Pulse Frequency: The frequency of the pulses, or the number of pulses per second, affects overall energy delivery and weld speed. Higher frequencies can increase weld speeds but can also increase the risk of cumulative heat buildup, which can cause defects.
- Optimization: The combination of pulse duration and frequency must be optimized based on material properties and desired weld characteristics. Fine-tuning these parameters helps achieve a balance between weld speed, penetration, and thermal effect.
Beam Quality
The quality of a laser beam is defined by parameters such as mode structure and beam profile, which directly impact welding efficiency.
- Beam Mode: The mode of a laser beam (e.g. TEM00) determines its intensity distribution. A high-quality mode structure ensures concentrated and uniform energy delivery, resulting in consistent and precise welding.
- Beam Profile: A uniform and well-defined beam profile minimizes energy losses and ensures maximum energy delivery to the weld area. Poor beam quality (characterized by a distorted or irregular profile) results in uneven heating and weld defects.
- Feasibility: High beam quality enables better focussing, enabling the laser to achieve smaller spot sizes for applications requiring high precision and fine detail.
Focal Position
The position of the laser focal point relative to the material surface is a critical parameter that affects welding efficiency and quality.
- Correct Focus: Correctly focusing the laser beam on the weld area ensures maximum energy density and efficient melting of the material. The optimal focal position depends on the material thickness and the desired weld characteristics. For deep penetration welding, the focal point is usually set slightly below the material surface.
- Focal Length: The focal length of the laser optics determines the focal depth and focal size. Short focal lengths produce smaller spot sizes and higher energy densities for fine welding tasks. Longer focal lengths provide greater focal depths, which are beneficial for welding thicker materials.
- Focus Tolerance: Maintaining a consistent focal position can help achieve uniform weld quality. Variations in the focal position can result in inconsistent penetration, incomplete fusion, and defects. Automated systems with real-time focus adjustment can help maintain optimal focus during the welding process.
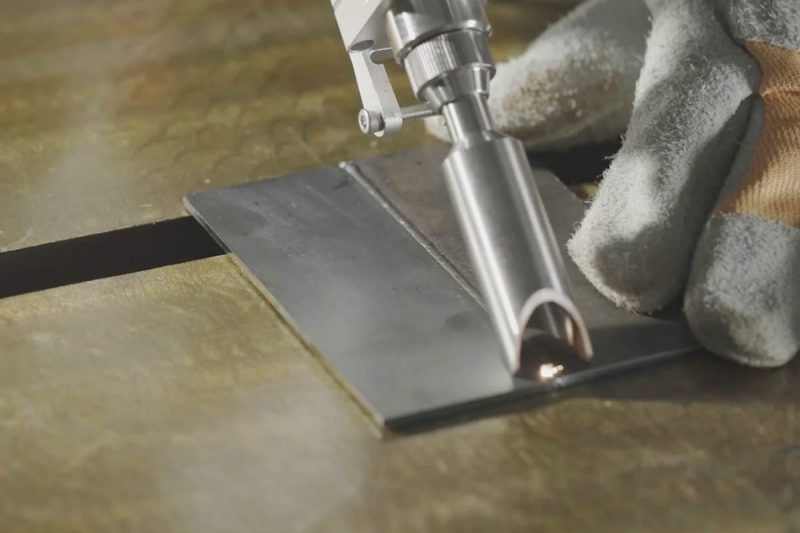
Material Properties
Material Type
The type of material being welded is the primary factor in determining laser welding efficiency. Different materials absorb and conduct laser energy in different ways, affecting weld quality and process parameters.
- Metals: Commonly welded metals include steel, aluminum, titanium, and copper. Each metal has different properties:
- Steel: It can generally be welded well with a laser due to its good absorption of laser energy. Various grades of steel, including carbon steel, stainless steel, and alloy steel, may require different laser settings.
- Aluminum: Aluminum is known for its high reflectivity and thermal conductivity, and welding aluminum with a laser can be challenging. Special wavelengths or coatings can improve absorbance.
- Titanium: Titanium can be welded effectively with a laser due to its moderate reflectivity and thermal properties. It is widely used in aerospace and medical applications.
- Copper: Copper’s high reflectivity and thermal conductivity make it difficult to weld with a traditional laser setup. Fiber lasers with specific wavelengths are often used to improve efficiency.
- Nonmetals: Materials such as plastics, ceramics, and composites can also be laser welded. Each nonmetal requires specific laser parameters for efficient welding:
- Plastics: Plastics generally absorb laser energy well, but their thermal properties require careful control of welding parameters to avoid burning or melting.
- Ceramics: Ceramics are brittle and can crack under thermal stress. Laser welding ceramics generally requires preheating and using lasers with specific wavelengths to reduce stress.
- Composites: Composites combine different materials and require careful adjustment of parameters to ensure uniform weld quality across different components.
Thickness
The thickness of the material is a key factor affecting the efficiency of laser welding. It affects the required laser power, welding speed, and overall process stability.
- Thin Materials: Thin materials require lower laser power and higher welding speeds to prevent burn-through and excessive heat input. Precise control of laser parameters allows for clean, defect-free welds.
- Thick Materials: Welding thick materials requires higher laser power and slower welding speeds to ensure adequate penetration and fusion. Advanced techniques such as multi-pass welding or hybrid welding (combining laser and arc welding) can be used to achieve full penetration.
- Transition Zone: When welding materials of different thicknesses, the laser parameters need to be dynamically adjusted to accommodate differences in heat absorption and conduction.
Surface Condition
The surface condition of a material can affect laser absorption, heat transfer, and overall weld quality. Proper surface preparation helps achieve efficient laser welding.
- Cleanliness: Contaminants such as oil, grease, dirt, and oxide layers can interfere with laser absorption and cause defects in the weld. Thoroughly cleaning the surface before welding is necessary to ensure optimal results.
- Surface Roughness: The roughness of a material’s surface can affect laser beam interaction. Smoother surfaces generally result in better laser absorption and more consistent welds. Surface treatments such as polishing or grit blasting can be used to improve surface conditions.
- Coatings and Treatments: Some materials may have coatings or treatments that affect laser welding. For example, galvanized steel has a zinc coating that requires specific laser settings to prevent evaporation and porosity. Understanding the effects of these coatings can help adjust welding parameters accordingly.
Thermal Properties
The thermal properties of a material, including thermal conductivity, specific heat capacity, and melting point, affect how the material interacts with laser energy.
- Thermal Conductivity: Materials with high thermal conductivity, such as copper and aluminum, dissipate heat quickly and require higher laser powers to achieve proper fusion. Materials with low thermal conductivity, such as stainless steel, retain heat longer, so heat input needs to be carefully controlled to avoid excessive melting.
- Specific Heat Capacity: The specific heat capacity of a material determines the amount of energy required to raise its temperature. Materials with high specific heat capacities require more energy to weld, which affects the choice of laser power and welding speed.
- Melting Point: The melting point of a material determines the amount of energy required to initiate melting and fusion. High melting point materials, such as titanium and certain alloys, require higher laser powers and precise control of welding parameters to achieve efficient welding.
Metallurgical Properties
The metallurgical properties of a material, including its composition, microstructure, and phase transformations, play a critical role in the laser welding process.
- Composition: The chemical composition of a material affects its weldability. Alloying elements affect the material’s absorption of laser energy, melting behavior, and susceptibility to defects such as cracking and porosity. Understanding the composition helps select appropriate laser parameters and shielding gas.
- Microstructure: The microstructure of a material, including grain size and phase distribution, affects its mechanical properties and response to welding. Fine-grained materials generally weld better than coarse-grained materials, which may require special attention to avoid cracking and deformation.
- Phase Transformations: Some materials undergo phase transformations during welding, which can affect the final weld properties. For example, some steels transform from austenite to martensite as they cool, resulting in a hard and brittle weld. Controlling cooling rates and post-weld heat treatment can help control these transformations and improve weld quality.
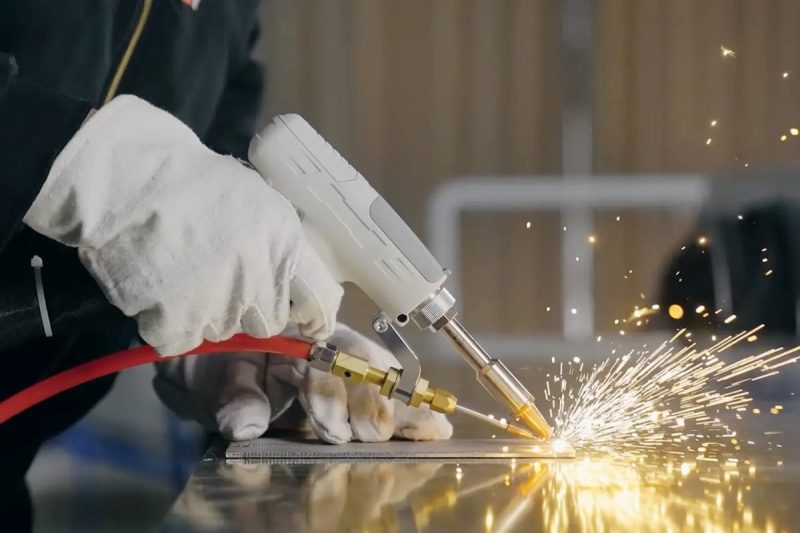
Joint Design
Joint Configuration
Joint configuration has a significant impact on the laser welding process. Different joint types offer varying degrees of accessibility, ease of welding, and mechanical strength.
- Butt Joint: In a butt joint, two pieces of material are placed edge to edge. This configuration is common in laser welding because it is simple and enables deep penetration. However, only precise alignment and minimal gaps can ensure a high-quality weld.
- Lap Joint: In a lap joint, one piece of material overlaps another. This configuration is often used to weld thin materials and is easy to assemble. However, it requires careful control of laser parameters to avoid excessive melting and ensure that the two layers are properly fused.
- T-Joint: T-joints are formed by welding one piece of material perpendicular to another. This configuration is often used in structural applications. The challenge with T-joints is to achieve uniform penetration and avoid defects at the intersection.
- Corner Joint: Corner joints are used to join two pieces of material at right angles. They are frequently used in box-like structures and frames. Ensuring proper fusion at corners requires precise control of laser parameters and joint preparation.
- Edge Joint: Edge joints involve welding along the edge of one or both pieces of material. This configuration is suitable for thin materials and applications where minimal overlap is required. Achieving consistent welds in edge joints requires precise alignment and gap control.
Joint Preparation
Proper joint preparation helps achieve high-quality welds. The condition of the joint surface directly affects laser absorption, heat transfer, and overall weld integrity.
- Cleanliness: The joint surface must be free of contaminants such as oil, grease, dirt, and oxides. Contaminants can interfere with laser absorption and cause defects such as porosity and incomplete fusion. Cleaning methods such as degreasing, wire brushing, and chemical cleaning can be used, depending on the material and contaminants present.
- Surface Treatment: Surface treatments such as sandblasting, grinding, or machining can improve the surface condition and enhance laser absorption. These treatments help create a smooth, uniform surface with reduced risk of defects.
- Edge Preparation: Proper edge preparation ensures a good fit and minimizes gaps. Techniques such as beveling, chamfering, and edge rounding can improve joint fit and promote better fusion.
Gap Tolerance
Maintaining tight gap tolerances can help achieve consistent and high-quality laser welds. Gaps between joint surfaces can result in incomplete fusion, weak welds, and defects.
- Minimum Gap: Ideally, joint surfaces should have a minimum gap to ensure complete fusion and a strong weld. Small gaps can be bridged by molten material, but excessive gaps can result in incomplete fusion and a weak joint.
- Allowable Tolerance: The allowable gap tolerance depends on the material, joint configuration, and welding parameters. In general, high-precision applications and thin materials require tighter tolerances, while thicker materials can tolerate slightly larger gaps.
- Adjustments: If gaps exist, adjusting the laser power, welding speed, and focus position can help compensate and ensure adequate fusion. However, excessive gaps should be avoided as they can affect weld quality and strength.
Fixtures and Clamping
Effective fixtures and clamping devices can ensure the stability and alignment of the joint during the laser welding process. Proper fixtures and clamping devices prevent movement, deformation, and misalignment, thereby improving welding efficiency and quality.
- Stability: The fixture must firmly hold the material in place to prevent any movement during the welding process. Even slight movement can cause misalignment, defects, and changes in weld quality.
- Alignment: The clamping system should ensure that the joint surfaces are accurately aligned. Misalignment can lead to poor fusion and weak welds. Adjustable fixtures and precision clamping tools can help achieve precise alignment.
- Heat Management: The fixtures and clamps should also manage the heat generated during the welding process. Excessive heat can cause the joint to deform and move. Using materials with good thermal conductivity for the fixture or integrated cooling systems can help manage heat and maintain stability.
- Accessibility: The design of the fixture and clamping system should allow the laser beam to easily reach the welding area. Complex geometries and tight spaces require custom fixtures to ensure proper laser access and optimal welding conditions.
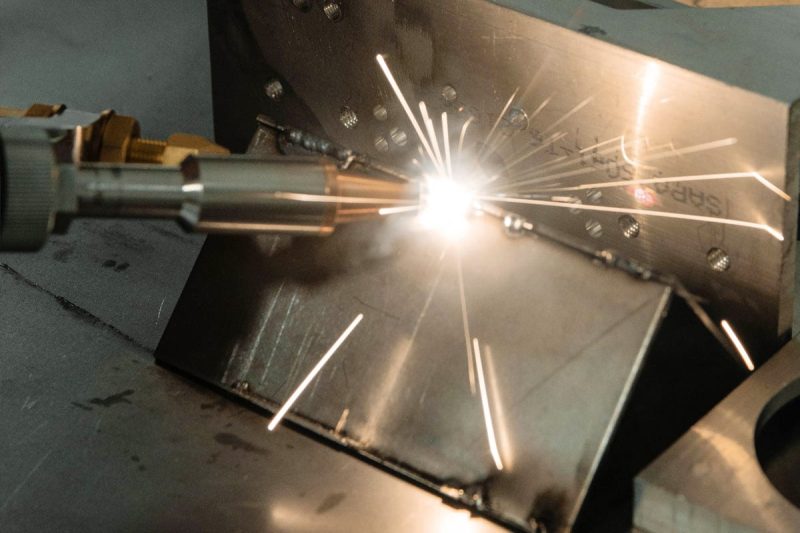
Environmental Conditions
Ambient Temperature
Ambient temperature can affect the laser welding process in several ways. Maintaining a controlled temperature environment ensures consistent weld quality and prevents equipment issues.
- Consistent Welding Performance: Extreme temperatures, either too high or too low, can affect the thermal characteristics of the materials being welded. High ambient temperatures can result in excessive heat input and increased thermal deformation, while low temperatures can cause rapid cooling and potential cracking.
- Equipment Stability: Laser welding equipment, including the laser source and cooling system, operates best within a specific temperature range:
- High Temperature: Excessive heat can cause thermal expansion of the weld material, leading to misalignment and deformation. It can also affect the cooling rate of the weld, affecting the microstructure and mechanical properties of the joint.
- Low Temperature: Extremely cold environments can cause condensation on the laser optics and material surfaces, interfering with laser absorption and potentially causing defects. Low temperatures can also affect the thermal conductivity and melting behavior of the material.
- Control Measures: Implementing a climate control system in the welding environment can help maintain a stable ambient temperature. This ensures consistency in material behavior and equipment performance, resulting in a more efficient and reliable welding process.
Humidity
Humidity levels in the welding environment can affect both the laser equipment and the materials being welded.
- Condensation: High humidity can cause condensation to form on the laser optics and material surfaces. This can scatter the laser beam, reducing its intensity and precision, and can also introduce contaminants into the weld.
- Oxidation and Corrosion: Materials susceptible to oxidation and corrosion are affected by high humidity. The presence of moisture can accelerate these processes, leading to surface contamination and weld defects.
- Material Behavior: Some materials, especially those that are sensitive to moisture, can exhibit changes in properties due to humidity. This can affect their weldability and the quality of the final weld.
- Control Measures: Using a dehumidifier and ensuring proper ventilation can help control humidity levels. Keeping the welding area dry and free of moisture can maintain optimal welding conditions.
Shielding Gas
The use of shielding gas can help achieve successful laser welding by protecting the weld area from atmospheric contaminants and improving weld quality.
- Types of Shielding Gases: Common shielding gases used in laser welding include argon, helium, nitrogen, and mixtures of these gases. The choice of shielding gas depends on the weld material and the weld characteristics required.
- Argon: Argon is widely used because of its inertness and provides excellent protection against oxidation and contamination. It is suitable for welding a variety of metals, including steel, aluminum, and titanium.
- Helium: Helium can increase weld penetration and reduce porosity, making it ideal for deep welds and high thermal conductivity materials such as copper and aluminum.
- Nitrogen: Nitrogen is often used in combination with other gases to improve weld quality on some materials, but must be used with caution due to its potential reactivity with some metals.
- Flow and Coverage: The flow and coverage of the shielding gas must be carefully controlled to ensure adequate protection of the weld area. Insufficient gas flow can lead to contamination and defects, while excessive flow can cause turbulence and cooling issues.
- Nozzle Design: The design and positioning of the shielding gas nozzle can help achieve effective gas coverage. Proper nozzle design ensures a continuous and even flow of gas over the weld area, improving weld quality and efficiency.
Ventilation
Proper ventilation of the welding area helps maintain a safe and efficient welding environment.
- Fume Extraction: Laser welding produces fumes and gases that are harmful to the operator and can affect the welding process. An effective fume extraction system removes these contaminants from the work area, ensuring a clean and safe environment.
- Airflow Control: Controlled airflow helps maintain a stable welding environment by preventing fume accumulation and maintaining consistent gas coverage of the welding area. Uncontrolled airflow or turbulence can disrupt the shielding gas and affect weld quality.
- Heat Management: Ventilation helps manage the heat generated during the welding process. Proper airflow prevents overheating of materials and equipment, reducing the risk of thermal distortion and equipment failure.
- Air Quality: Maintaining good air quality in the welding environment prevents the accumulation of dust and other particulates that can interfere with the laser beam and welding process. Clean air ensures consistent beam quality and reduces the risk of defects.
- Safety Measures: Ensuring proper ventilation reduces the risk of exposure to hazardous fumes and improves overall workplace safety. It also helps maintain the integrity of laser optics and other sensitive components by preventing contamination and particle accumulation.
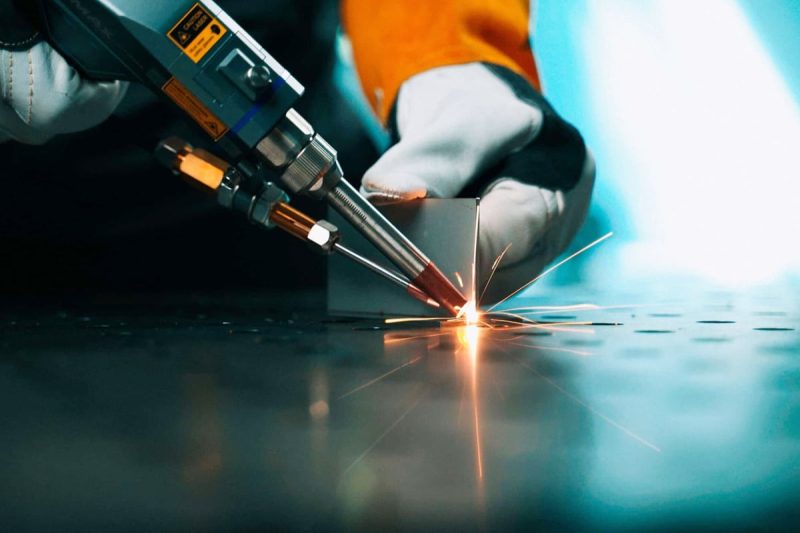
Welding Speed
Optimal Welding Speed
Achieving the optimal welding speed is a delicate balance between weld quality and productivity. The right speed ensures that the materials are fully fused without causing defects.
- Complete Fusion: At the optimal welding speed, the laser delivers enough energy to completely melt and fuse the materials. This produces a strong, defect-free weld with good mechanical properties.
- Consistent Quality: Consistent welding speeds ensure uniform heat input along the weld, resulting in consistent weld quality. Speed variations can cause irregularities that affect the strength and appearance of the weld.
Effects of High Welding Speeds
High welding speeds can improve productivity, but they come with specific challenges and potential drawbacks.
- Increased Productivity: Higher welding speeds reduce cycle time, allowing more welds to be completed in a given time. This is particularly beneficial in high-volume manufacturing environments.
- Potential Defects: Welding at too fast a speed can result in insufficient heat input, which can lead to incomplete fusion, weak welds, and potential cracks. Rapid movement may not allow enough time for the materials to melt and properly bond.
- Surface Irregularities: At very high speeds, the molten pool may not have enough time to settle, resulting in surface irregularities such as ripples and spatter.
Effects of Low Welding Speeds
While slower welding speeds can improve weld quality, there are certain limitations and considerations.
- Improved Penetration: Slower welding speeds increase heat input per unit length of weld, which improves penetration and ensures complete fusion of thicker materials.
- Increased Heat-Affected Zone (HAZ): Slower speeds result in excessive heat input, which results in a larger HAZ. This can cause thermal distortion, reduced mechanical properties, and possible warping of the welded component.
- Reduced Productivity: Slower welding speeds reduce productivity and increase the total time required to complete a welding task. In a high-volume production environment, this can be a significant disadvantage.
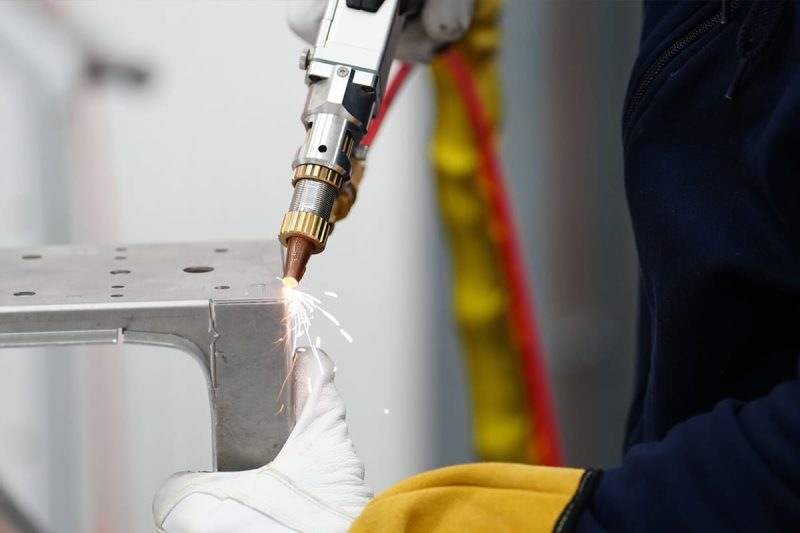
Operator Skills and Experience
Importance of Operator Skills and Experience
Operator proficiency is critical for several reasons, including proper setup of welding equipment, accurate parameter adjustments, and the ability to quickly identify and resolve issues that may arise during the welding process.
- Setup and Calibration: Skilled operators are adept at setting up and calibrating laser welding equipment. This includes aligning the laser, adjusting focus, setting the appropriate laser power, and configuring shielding gas flow. Proper setup ensures that the welding process starts with the right foundation, minimizing the risk of defects and inefficiencies.
- Parameter Adjustment: Experienced operators have a deep understanding of the relationship between welding parameters and weld quality. They can make precise adjustments to parameters such as welding speed, laser power, and pulse frequency to optimize the welding process for different materials and joint configurations.
- Troubleshooting and Problem Solving: During the welding process, a variety of issues may occur, such as misalignment, poor penetration, or the formation of defects such as porosity and cracks. Skilled operators can quickly diagnose these issues and implement corrective actions, ensuring minimal downtime and consistent weld quality.
- Process Adaptability: Different materials, joint configurations, and welding tasks require specific adjustments. Experienced operators can adjust process parameters to suit different conditions, ensuring consistent weld quality across applications.
Training and Certification
Proper training and certification help develop and maintain a high level of operator skills. The comprehensive training program should cover:
- Theoretical Knowledge: It is critical to understand the principles of laser welding, including the interaction between laser energy and materials. Operators should be well-versed in the science behind the process to make informed decisions.
- Hands-On Experience: Hands-on training with laser welding equipment allows operators to gain experience setting up, calibrating, and operating the machine. Hands-on experience helps build confidence and competence in the real world.
- Safety Protocols: Laser welding involves potential hazards, including intense light, fumes, and heat. Training should emphasize safety protocols to protect operators and ensure a safe work environment.
- Certification Programs: Certification programs validate operators’ skills and knowledge, formally recognizing their expertise. Certified operators are generally more capable of handling complex welding tasks and effectively troubleshooting problems.
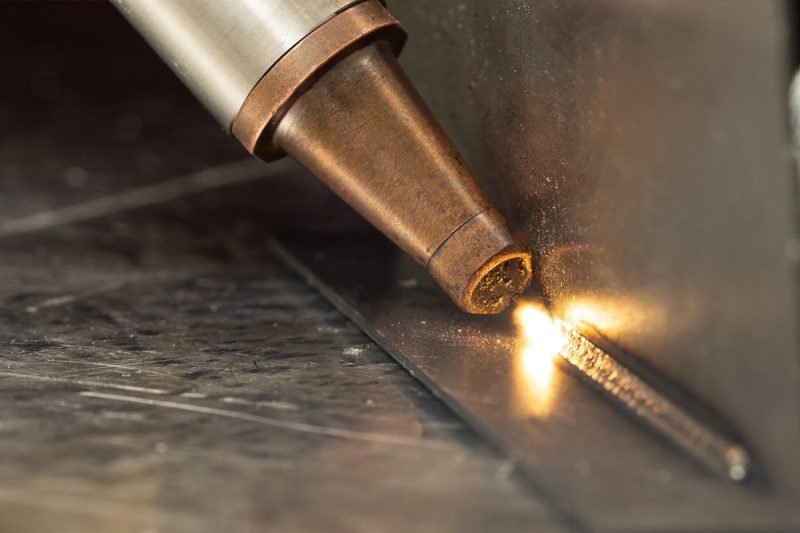
Equipment and Maintenance
Laser Source
The laser source is the heart of a fiber laser welding system, producing the high-intensity beam required for welding.
- Fiber Lasers: Known for their high efficiency, excellent beam quality, and ruggedness, fiber lasers are ideal for welding a wide range of materials, including reflective metals such as aluminum and copper.
- Maintenance: Regularly monitor power output to ensure consistent performance, clean optics to prevent contamination, and check alignment to maintain beam accuracy.
Optics
Optics direct and focus the laser beam to the weld area, ensuring precise energy delivery.
- Beam Delivery System: Includes optical fiber and collimator to deliver the laser beam with minimal losses.
- Focusing Optics: Lenses or focusing heads that concentrate the laser beam to a small spot size, thereby increasing energy density.
- Maintenance: Regular cleaning of lenses, mirrors, and protective windows, inspection for damage, and alignment checks can help maintain optimal beam quality.
Motion System
The motion system controls the motion of the laser beam and workpiece, ensuring precise positioning and smooth operation.
- Types: Cartesian systems for three-axis linear motion, robotic arms for multi-axis motion, and gantry systems for large-scale applications.
- Maintenance: Regular lubrication of moving parts, regular calibration for precise motion, and checking for wear or misalignment help ensure reliable operation.
Cooling System
The cooling system prevents the laser source and other key components from overheating and maintains stable operation.
- Water Cooling: It is often used in high-power fiber laser generators due to its good heat dissipation effect.
- Components: Pumps, heat exchangers, and coolant reservoirs are key elements of the cooling system.
- Maintenance: Regularly check for leaks and blockages, monitor coolant quality, and replace filters as needed to ensure efficient cooling.
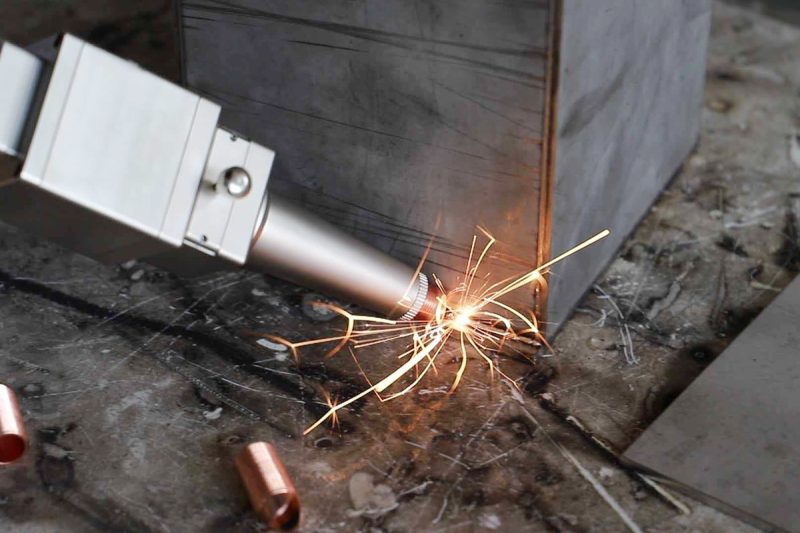
Automation and Control Systems
Real-time Monitoring
Real-time monitoring systems provide continuous feedback on the welding process, allowing adjustments to be made immediately to ensure optimal performance.
- Weld Quality Monitoring: Sensors and cameras monitor the weld pool, detecting defects such as porosity, cracks, and misalignment in real time. This enables the operator to adjust the laser power, speed, and focus in real time.
- Laser Power Monitoring: The system continuously tracks the laser power output to ensure it remains within the desired range. This helps maintain consistent energy delivery and weld penetration.
Adaptive Control
Adaptive control systems dynamically adjust welding parameters based on real-time data to optimize the process for varying conditions.
- Parameter Adjustment: These systems automatically adjust laser power, welding speed, and focus position based on changes in material properties, thickness, and joint configuration. This ensures uniform and consistent weld quality across different parts of the workpiece.
- Feedback Loops: Incorporating feedback loops allows the system to learn from previous welds, improving accuracy and efficiency over time.
Integration with Robotic Systems
Integrating fiber laser welding with robotic systems enhances automation, flexibility, and repeatability.
- Multi-Axis Motion: The robotic arm provides multi-axis motion for precise welding of complex geometries and hard-to-reach areas.
- Constant Quality: The robot ensures consistent weld quality by precisely controlling the weld path, speed, and angle, reducing the variations associated with manual welding.
- Increase Throughput: Robotic automation increases throughput by enabling continuous operation and reducing cycle times, resulting in significant productivity gains.
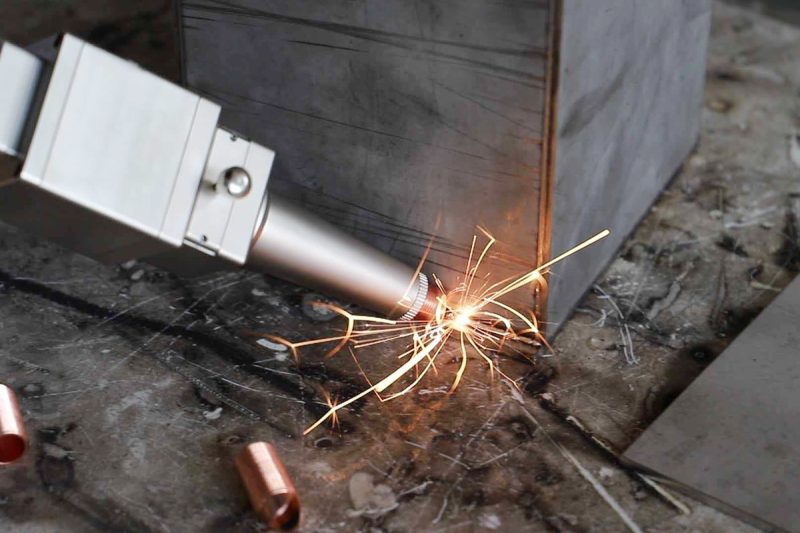
Application-Specific Considerations
Material Combinations
Different materials react uniquely to laser welding, and their combinations can present specific challenges.
- Dissimilar Materials: Welding dissimilar materials, such as aluminum to steel, can be challenging due to differences in melting points, thermal conductivities, and laser absorption rates. Fiber lasers are effective in welding these combinations but require precise control over parameters to manage the heat input and avoid defects.
- Reflective Materials: Materials like copper and aluminum reflect a significant portion of laser energy, which can reduce welding efficiency. Fiber lasers, particularly with shorter wavelengths, are better suited for these materials, but optimizing the laser parameters is essential to ensure effective energy absorption.
- Alloys and Composites: Each alloy or composite material may require specific settings for optimal welding. Understanding the material properties and adjusting the laser power, speed, and focus accordingly is key to achieving high-quality welds.
Welding Geometry
The geometry of the weld joint affects the welding process and must be carefully considered to ensure efficiency.
- Complex Geometries: Welding complex geometries, such as curved or intricate shapes, requires precise control of the laser beam and motion system. Fiber lasers can effectively handle these geometries when integrated with advanced motion systems and robotic arms.
- Thin VS Thick Sections: Welding thin sections requires lower power and higher precision to avoid burn-through, while thick sections require higher power and lower speeds to fully penetrate. Adjusting laser parameters to specific geometries can achieve efficient welding.
- Edge Preparation: Proper edge preparation, such as beveling or cleaning, ensures better fit and fusion. Maintaining consistent edge quality can help achieve uniform welds.
Production Volume
Production volume affects the choice of laser welding equipment and process parameters.
- Small-Batch or Custom Production: For small-batch or custom production, flexibility and adaptability are key. The versatility of fiber lasers allows for quick adjustment of welding parameters and configurations, making them suitable for a variety of specialized welding tasks.
- High-Volume Production: High-volume production requires consistency, speed, and automation. Fiber laser systems integrated with automated control systems and robotic arms provide the required precision and repeatability, significantly increasing production and efficiency.
- Cycle Time Optimization: In a production environment, minimizing cycle time can improve efficiency. Fiber laser systems equipped with real-time monitoring and adaptive control can reduce setup time and ensure optimal welding speeds, thereby increasing overall productivity.
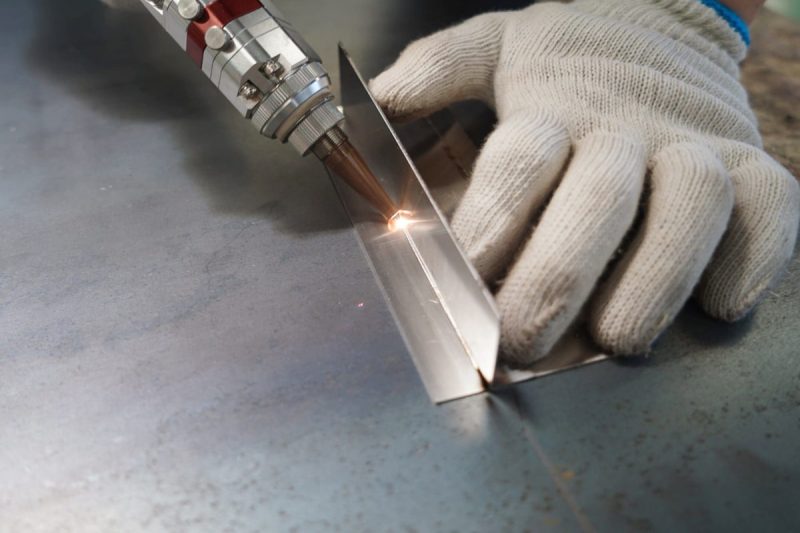
Summary
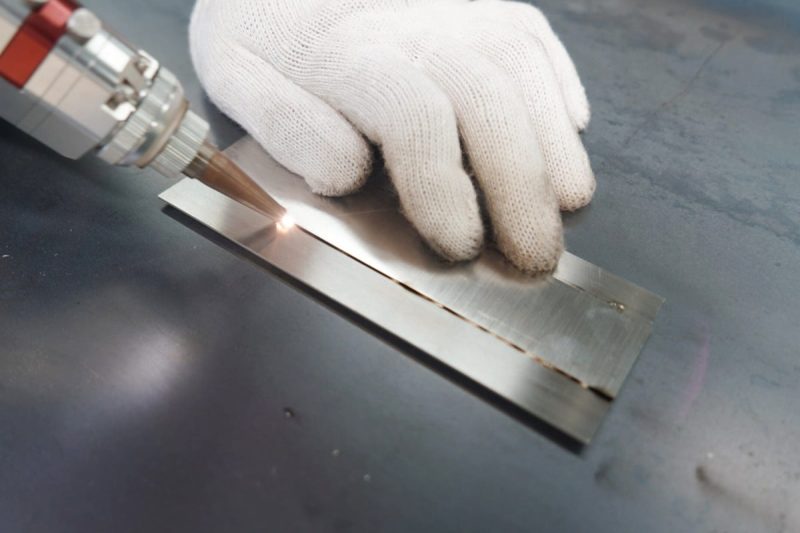
Get Laser Welding Solutions
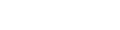
- [email protected]
- [email protected]
- +86-19963414011
- No. 3 Zone A, Lunzhen Industrial Zone,Yucheng City , Shandong Province.