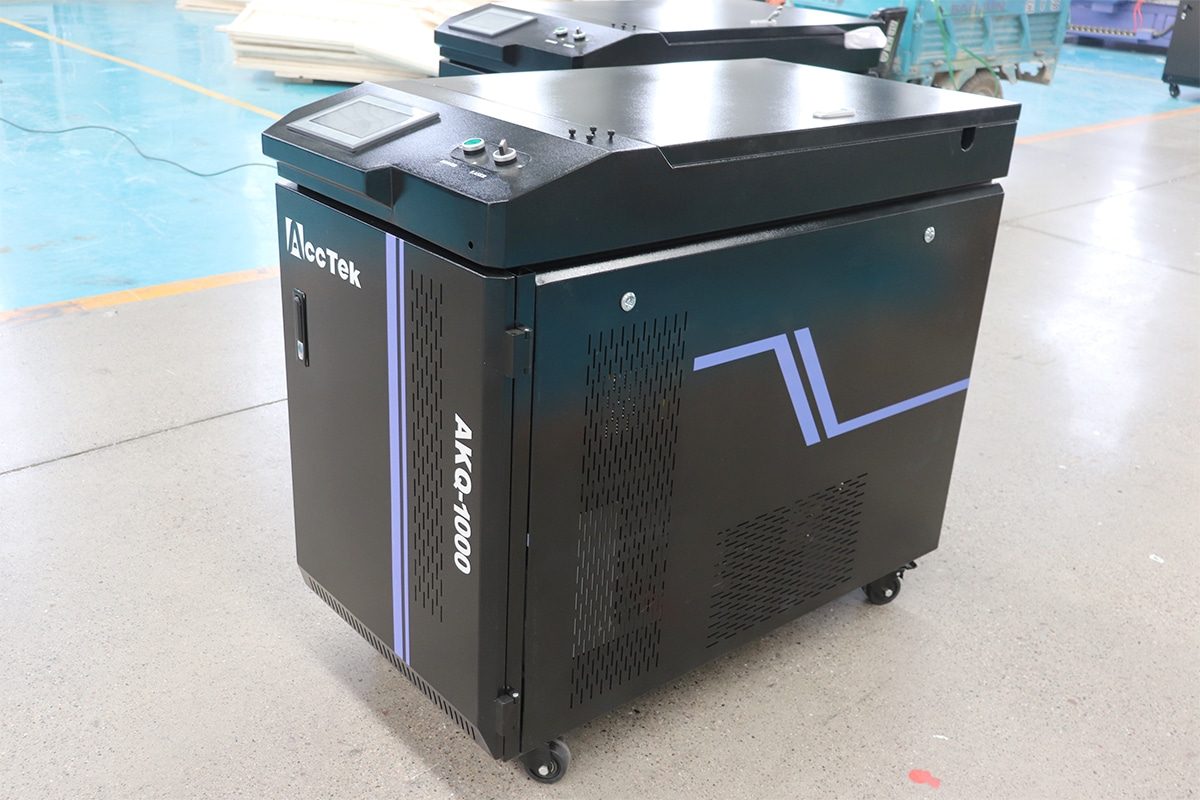
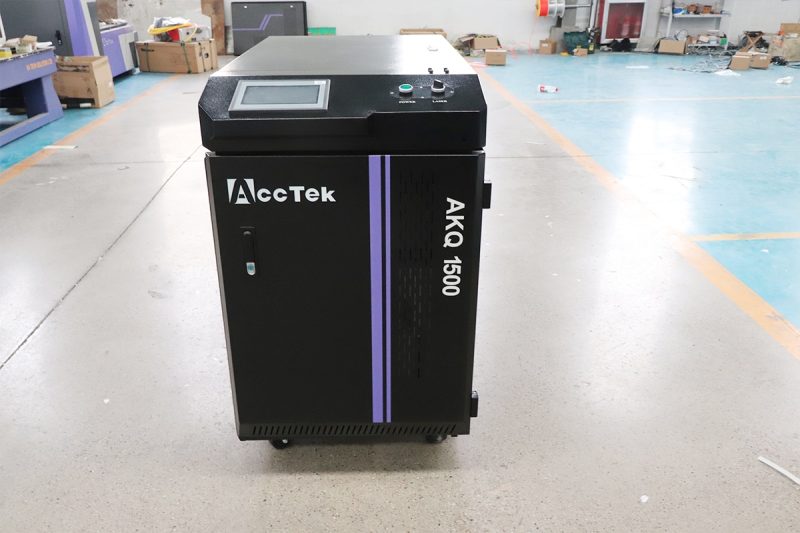
Laser Parameters
Wavelength
Pulse Duration
Pulse Repetition Rate
Energy Density (Flux)
Beam Profile and Focus
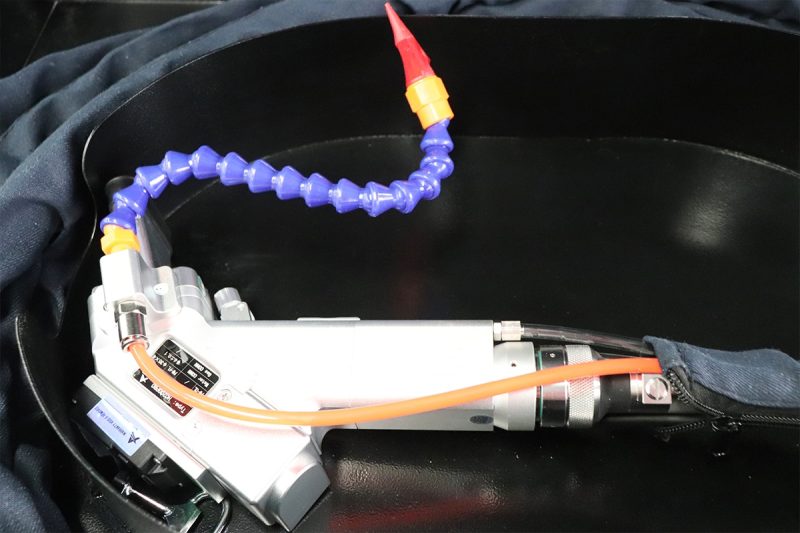
Material Properties
Absorption Properties
The absorption properties of the materials involved play a key role in determining the effectiveness of laser cleaning. Absorption properties refer to how well a material absorbs laser energy at a given wavelength. Different materials absorb laser energy differently depending on their atomic and molecular structure:
- Substrate Absorption: The ability of a substrate to absorb laser energy affects the amount of heat generated within the material. Materials with high absorption coefficients at the laser wavelength will heat up faster, which can either aid the cleaning process or potentially damage the substrate if not properly controlled.
- Contaminant Absorption: Effective laser cleaning requires that the contaminant absorbs the laser energy more readily than the substrate. This differential absorption ensures that the contaminant is ablated without significantly affecting the substrate. For example, rust (iron oxide) absorbs infrared laser energy effectively and is, more easily removed from metal surfaces using infrared lasers.
Thermal Properties
The thermal properties of both the substrate and the contaminant affect how heat is managed during laser cleaning. Key thermal properties include thermal conductivity, specific heat, and melting point:
- Thermal conductivity: Materials with high thermal conductivity, such as metals, can dissipate heat quickly, reducing the risk of local overheating and damage. Conversely, materials with low thermal conductivity, such as certain polymers, can retain heat, increasing the risk of thermal damage during the cleaning process.
- Specific heat: The specific heat of a material represents the amount of energy required to raise its temperature. Materials with high specific heat can absorb more energy without significantly raising their temperature, making them more resistant to thermal damage during laser cleaning.
- Melting and boiling points: The melting and boiling points of the substrate and contaminants affect their response to laser heating. The goal is usually to evaporate or sublimate the contaminant without reaching the melting point of the substrate. Understanding these thresholds helps select the appropriate laser parameters for effective cleaning.
Mechanical properties
The mechanical properties of the substrate and contaminants, including hardness, brittleness, and ductility, can affect the laser cleaning process:
- Hardness: Harder materials may be resistant to ablation and require higher energy densities for effective cleaning. The hardness of the substrate relative to the contaminant affects how easily the contaminant can be removed without damaging the substrate.
- Brittleness: Brittle materials, such as some ceramics or glasses, are more susceptible to cracking or breaking under the stress induced by the laser pulse. Laser parameters must be carefully controlled to avoid damaging brittle substrates.
- Ductile: Ductile materials, such as many metals, deform plastically under laser-induced stress. While this is sometimes beneficial for absorbing energy and preventing damage, excessive ductility can lead to undesirable surface modifications in precision cleaning applications.
Contaminant Properties
The nature of the contaminant is a key factor in determining the effectiveness of laser cleaning. Contaminants can vary widely in their chemical composition, physical state, thickness, and adhesion to the substrate.
- Chemical composition: Different contaminants react differently to laser energy. For example, organic contaminants, such as oil and grease, may evaporate or decompose under laser exposure, while inorganic contaminants, such as rust or scale, may require higher energy densities for effective removal. Chemical composition also affects the contaminant’s absorption characteristics and thermal response.
- Thickness: The thickness of a contaminant layer affects the energy required for removal. Thicker layers typically require more energy and multiple laser exposures to completely ablate. On the other hand, thin layers may be easier to remove but require precise control to avoid damaging the substrate.
- Physical state: Contaminants can be solid, liquid, or gaseous. Solid contaminants, such as rust or paint, generally require more energy to remove than liquids or vapors. The physical state also affects the interaction between the laser and the contaminant, which affects the efficiency of the cleaning process.
- Substrate adhesion: The strength of the bond between the contaminant and the substrate affects the ease of removal. Loosely attached contaminants can be removed with lower energy densities, while strongly attached contaminants may require higher energy levels or different laser parameters to break the bond and achieve effective cleaning.
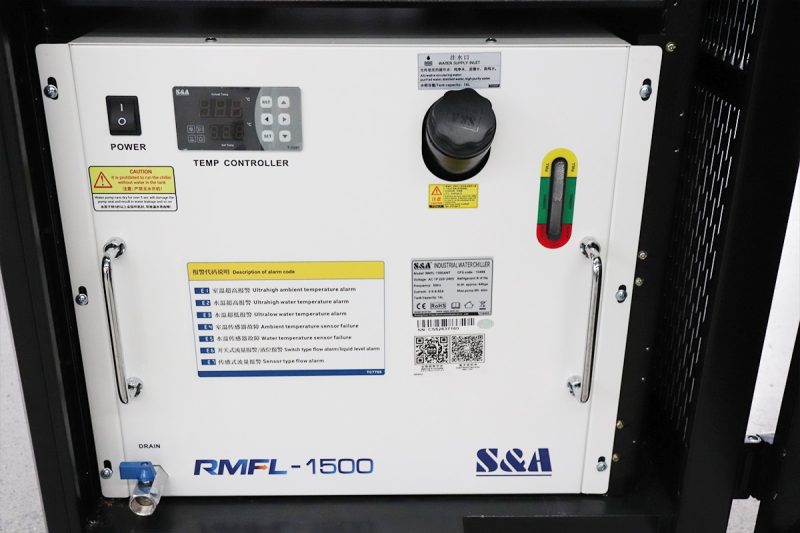
Surface Contaminants
Contaminant Composition
The chemical composition of surface contaminants determines how they interact with laser energy. Different materials have different absorption characteristics and thermal responses, which can affect how effectively they are ablated by the laser.
- Organic Contaminants: This includes oils, greases, and biological residues. Organic materials typically absorb laser energy differently than inorganic materials. For example, hydrocarbons may decompose or vaporize under laser irradiation, while biological contaminants may char or vaporize. Knowing the specific organic compounds present can help select the appropriate laser wavelength and parameters.
- Inorganic Contaminants: This includes rust, oxides, and mineral deposits. Due to their higher melting points and thermal stability, inorganic materials typically require higher energy densities for effective removal. The composition of these contaminants can influence the selection of laser parameters, such as wavelength and energy density, to ensure efficient ablation.
- Mixed Contaminants: Surfaces often contain a combination of organic and inorganic contaminants. In such cases, a multi-step or combined approach may be required, with laser parameters adjusted to effectively remove each type of contaminant without damaging the substrate.
Contaminant Thickness
The thickness of the contaminant layer is a critical factor in laser cleaning. It affects the energy required and the effective removal strategy.
- Thin Layers: Thin contaminant layers, such as light dust or fine oxide layers, can generally be removed with lower energy densities and fewer laser passes. The challenge with thin layers is to ensure complete removal without overexposing the substrate to the laser energy, which can cause damage.
- Thick Layers: Thicker contaminant layers require more energy and may require multiple laser passes to be completely removed. The challenge with thick layers is to ensure that each pass removes the desired amount of material without overheating or damaging the substrate. Adjusting the laser’s energy density and repetition rate can help manage the removal process for thicker layers.
Adhesion
The adhesion between the contaminant and the substrate affects how easily the contaminant can be removed by laser.
- Weak Adhesion: Contaminants that are loosely attached to the surface, such as loose dust or surface dirt, can be removed relatively easily with lower energy densities. The laser energy breaks weak bonds, causing the contaminant to be ablated or blown away by the resulting plume.
- Strongly Adherent: Strongly adherent contaminants, such as stubborn rust or strongly bonded coatings, require higher energy densities and more precise laser parameters to break bonds and effectively remove the contaminant. In some cases, pretreatment or a multi-step laser cleaning process may be required to weaken adhesion before complete removal.
Layer Composition
The composition and structure of contaminant layers can vary greatly, affecting laser-material interaction.
- Homogeneous Layers: Homogeneous contaminant layers composed of a single material type generally respond predictably to laser cleaning. The uniformity allows for a more straightforward optimization of laser parameters for efficient cleaning.
- Heterogeneous Layers: Many real-world contaminants are heterogeneous, composed of multiple materials with different properties. For example, a layer may be composed of a mixture of organic oil and inorganic dust particles. These layers require a more nuanced approach, as different components may react differently to laser energy. Adjusting laser wavelength, energy density, and pulse duration can help resolve different properties within a layer.
- Multi-Layered Contaminants: Multi-layered contaminants, such as a combination of paint, rust, and dirt, require a more complex approach. Each layer may have different absorption characteristics, thermal properties, and adhesion strength. It may be necessary to adjust laser parameters sequentially or use different wavelengths to effectively remove each layer without damaging the substrate.
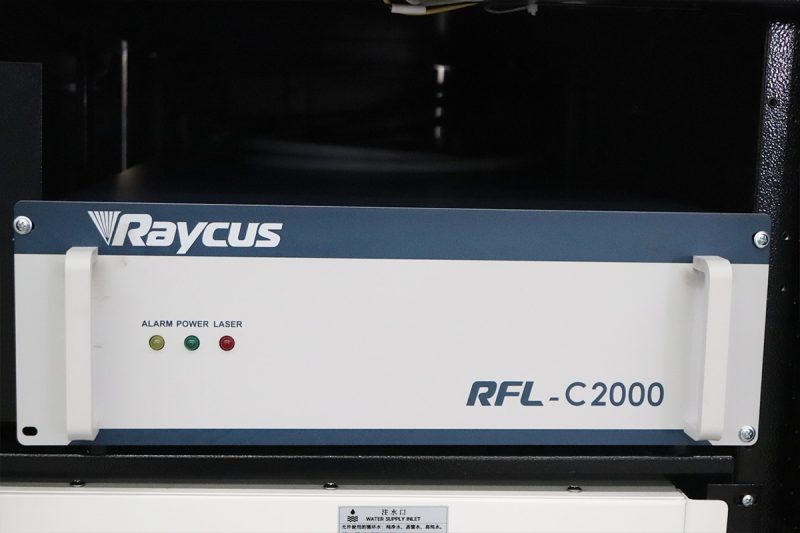
Environmental Conditions
Ambient Temperature
Ambient temperature plays a critical role in laser cleaning and can affect both substrates and contaminants.
- Substrate Response: The temperature of the substrate affects its thermal properties, such as thermal conductivity and specific heat. Higher ambient temperatures cause the substrate to heat up more quickly during the laser cleaning process, which can increase the risk of thermal damage. Conversely, lower ambient temperatures may reduce the substrate’s sensitivity to heat buildup, but can also make some materials more brittle and more susceptible to cracking.
- Laser Efficiency: The efficiency of the laser system itself can be affected by ambient temperature. Laser components, especially those in high-power systems, are sensitive to temperature changes, which can affect their performance and stability. Maintaining a stable ambient temperature helps stabilize laser output and effective cleaning.
- Contaminant Behavior: The behavior of contaminants under laser irradiation can also vary with ambient temperature. For example, some contaminants may become more volatile or reactive at higher temperatures, while others may become more viscous or adhere more firmly to the substrate. Controlling the ambient temperature helps ensure predictable and efficient contaminant removal.
Humidity
The humidity level in the environment can significantly affect the laser cleaning process.
- Condensation and absorption: High humidity can cause moisture to condense on the substrate surface, especially when the substrate is cooler than the surrounding air. This moisture layer can affect the absorption of laser energy, which can reduce the efficiency of contaminant removal. In addition, absorbed moisture can cause contaminants to swell or change their properties, complicating the cleaning process.
- Static charge: Low humidity levels increase the risk of static buildup on the substrate and contaminants. Static charges attract dust and other airborne particles, causing recontamination after cleaning. They can also interfere with the laser beam, causing uneven energy distribution and inconsistent cleaning results.
- Material interaction: Humidity can change the interaction between the laser and certain materials. For example, organic contaminants may absorb moisture and become more difficult to remove, while inorganic contaminants may form hydrates, changing their ablation properties. Maintaining optimal humidity levels ensures stable and predictable cleaning results.
Air contaminants
Air contaminants in the environment can adversely affect the laser cleaning process.
- Beam interference: Particles suspended in the air can scatter or absorb the laser beam before it reaches the material surface. This interference reduces the energy density of the laser, leading to reduced cleaning effectiveness and inconsistent results. Ensuring a clean work environment with a proper air filtration system can minimize beam interference.
- Optics: Airborne contaminants can deposit on the optical components of a laser system, such as lenses and mirrors, reducing their clarity and efficiency. Contaminated optics can reduce the quality of the laser beam, cause distortions, and reduce the overall efficiency of the cleaning process. Regular maintenance and cleaning of optics is necessary to prevent such issues.
- Workplace Safety: Airborne contaminants such as ablation particles, fumes, and gases generated during the laser cleaning process can pose a risk to the health and safety of operators. Implementing proper ventilation and filtration systems is essential to capture and remove these contaminants, thereby ensuring a safe work environment. Personal protective equipment (PPE) such as masks and goggles should also be used to protect operators from exposure.
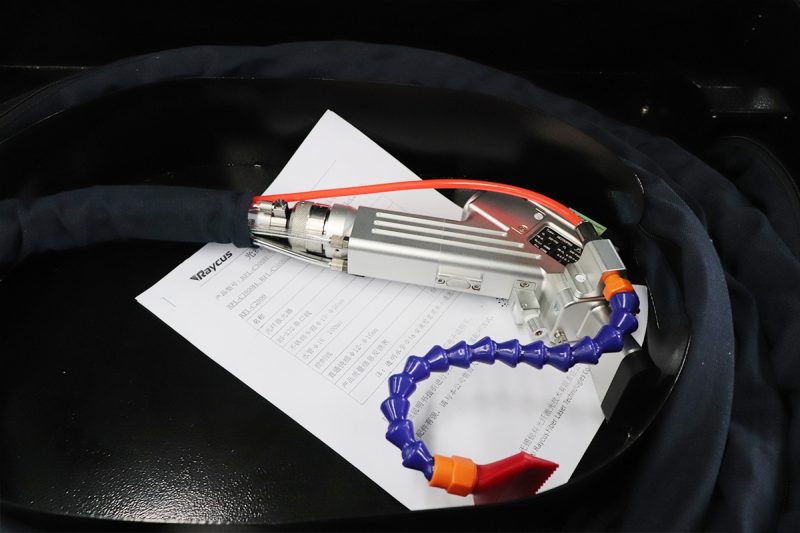
Operational Considerations
Scanning Speed
Scanning speed refers to the rate at which the laser beam moves across the surface being cleaned. It is a key factor affecting the amount of time the material is exposed to the laser energy.
- Impact on Cleaning Efficiency: Faster scan speeds can reduce the risk of thermal damage by limiting heat buildup in any single area. However, if the speed is too high, the laser may not stay on each point long enough to effectively ablate the contaminant, resulting in incomplete cleaning.
- Balance and Optimization: Slower scan speeds allow for longer exposures, which can enhance contaminant removal but increase the risk of overheating and potential substrate damage. Finding the optimal scan speed requires balancing the need for effective contaminant removal with the risk of thermal effects. This balance is often determined experimentally based on the specific material and contaminant characteristics.
Pulse Overlap
The degree of overlap between consecutive laser pulses affects the uniformity and thoroughness of the cleaning process.
- Consistent Energy Delivery: Proper overlap ensures that every area of the surface receives consistent laser energy. This helps achieve uniform cleaning results, which is important because insufficient overlap can leave uncleaned areas, while excessive overlap can lead to increased heat buildup and potential damage.
- Pulse Repetition Rate and Scan Speed: Overlap is affected by pulse repetition rate and scan speed. Higher repetition rates and slower scan speeds increase overlap, which improves the thoroughness of cleaning, but also increases thermal loading on the substrate. Conversely, lower repetition rates and faster scan speeds reduce overlap, which may require multiple scans to achieve complete cleaning.
- Adjusting Overlap: Adjusting the degree of overlap requires careful coordination of pulse repetition rate, scan speed, and laser energy. The goal is to ensure thorough cleaning without causing thermal damage or leaving behind residual contaminants.
Laser-to-Surface Distance
The distance between the laser source and the material surface, also known as the standoff distance, is a critical factor in laser cleaning.
- Focus and Energy Density: Standoff distance affects the focus and energy density of the laser beam on the target surface. Maintaining the optimal distance ensures that the laser beam is properly focused, maximizing energy delivery to contaminants and increasing ablation efficiency.
- Distance Variation: Standoff distance variations can lead to inconsistent cleaning results. If the distance is too large, the laser beam may be out of focus, which reduces energy density and cleaning effectiveness. If the distance is too short, the risk of damaging the substrate increases due to over-concentration of energy.
- Maintaining the Optimal Distance: Using precision positioning systems and feedback mechanisms can help maintain the optimal spacing during the cleaning process. This ensures consistent focus and energy delivery for uniform and effective cleaning.
Angle of Incident
The angle at which the laser beam strikes the surface is called the angle of incidence, which can significantly affect the absorption and effectiveness of the cleaning process.
- Energy Absorption and Reflection: The angle of incidence affects the absorption and reflection of laser energy by the surface. The optimal angle of incidence maximizes energy absorption by the contaminants, which enhances the ablation process. Typically, a perpendicular angle (90 degrees) ensures the most effective energy delivery.
- Surface Geometry: The geometry of the surface being cleaned may require adjustment of the angle of incidence. For example, complex or curved surfaces may require different angles to ensure that all areas are effectively cleaned. Using an adjustable laser head or robotic system can help maintain the optimal angle for different surface geometries.
- Reflection Safety: Managing the angle of incidence also has safety implications. Properly controlling the angle helps minimize unwanted reflections, which can be hazardous to operators and equipment. Safety measures such as protective barriers and controlled environments can mitigate these risks.

Summary
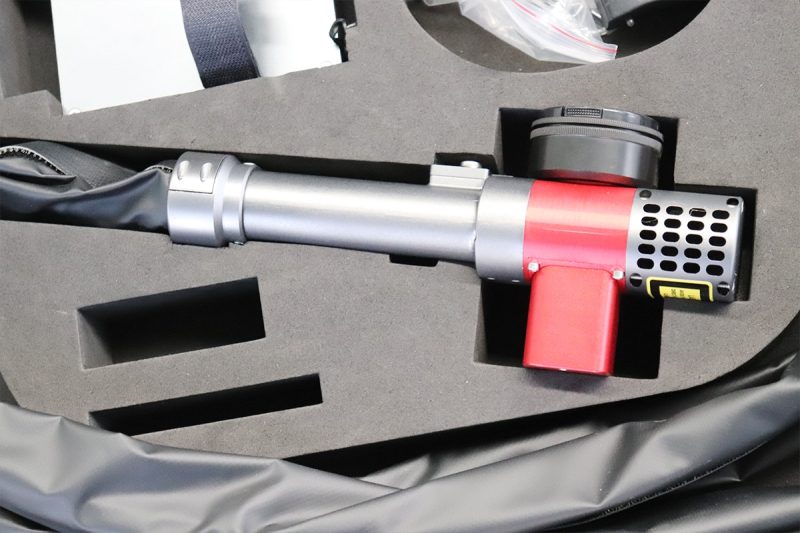
Get Laser Cleaning Solutions
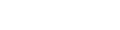
- [email protected]
- [email protected]
- +86-19963414011
- No. 3 Zone A, Lunzhen Industrial Zone,Yucheng City , Shandong Province.