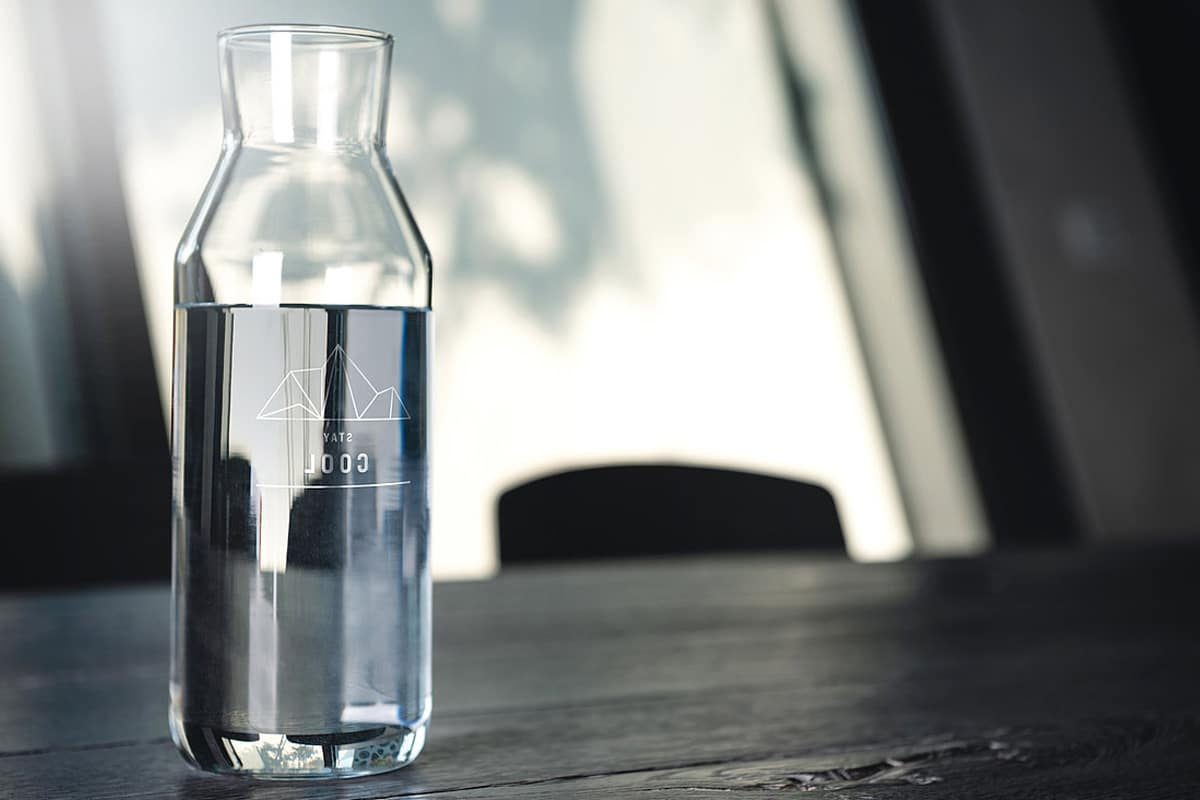
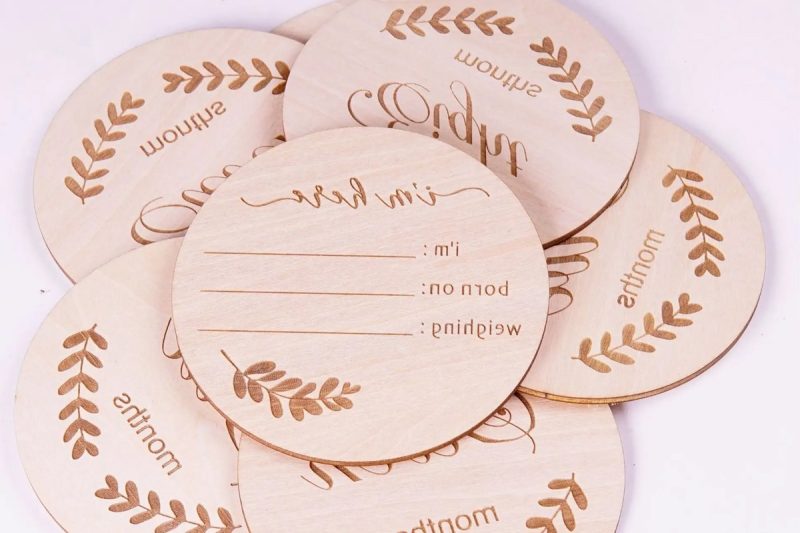
Laser Type and Source
- Fiber laser: With its high energy density and excellent focusing characteristics, fiber laser generators are very suitable for marking metal materials, especially materials such as steel, aluminum, and copper. Fiber laser marking can achieve extremely high precision and is often used in high-precision applications that require extremely fine patterns and text, such as marking electronic components, medical devices, and automotive parts. In addition, fiber lasers have low energy consumption and long service life, making them the first choice for metal marking.
- CO2 laser: CO2 lasers are mainly used for marking non-metallic materials, especially for materials such as wood, plastic, leather, and paper. With a wavelength of 10.6 microns, it can efficiently absorb the energy of non-metallic materials, so it has been widely used in industries such as packaging, clothing, and handicrafts. The cutting and engraving functions of CO2 laser marking also make it outstanding in advertising production, furniture decoration, and model manufacturing.
- Ultraviolet (UV) laser: UV lasers are called cold light sources due to their short wavelength (usually 355nm). Compared with other laser types, UV lasers have a very small heat-affected zone, which means that thermal deformation and damage to the material will be greatly reduced during the marking process. This makes it very suitable for fine marking, especially on heat-sensitive materials such as glass, plastic, and ceramics. UV laser marking is often used in high-precision industries such as electronic products, cosmetic packaging, and pharmaceutical labels, and can achieve extremely fine and clear marking effects.
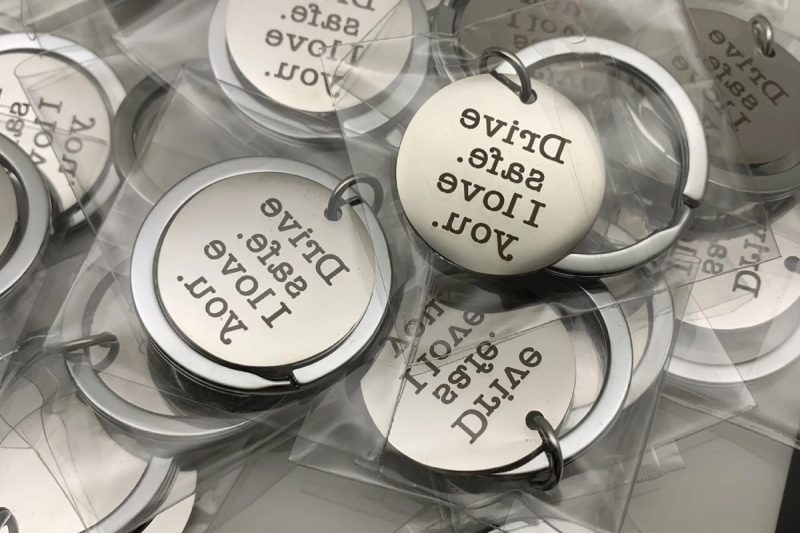
Influence of Material Properties
- Absorption and reflectivity: Materials have different absorption and reflection capabilities for lasers of different wavelengths. Materials with high absorption can better absorb laser energy and produce better marking effects, while materials with high reflectivity will reflect a large amount of laser light and reduce marking efficiency. For example, metal materials such as aluminum and copper have high reflectivity for fiber lasers, which may result in insufficient or unclear marking. For this reason, when marking these high-reflectivity materials, it is usually necessary to adjust the laser parameters or use lasers of specific wavelengths to enhance the absorption rate to obtain the ideal marking effect. In contrast, non-metallic materials such as plastics or glass have high absorption rates for CO2 and UV lasers, and the marking depth and contrast are easier to control.
- Thermal conductivity: The thermal conductivity of the material directly affects the heat distribution during the marking process. Materials with high thermal conductivity, such as copper, aluminum, and other metals, can quickly disperse the heat generated during the marking process, reduce local overheating, and avoid melting or burning of the material surface. Such materials usually require increased laser power or extended marking time during laser marking to ensure that sufficient energy is applied to the marking area. For materials with low thermal conductivity, such as plastic or wood, heat is difficult to diffuse quickly, and overheating is likely to occur during the marking process, resulting in deformation or damage. Therefore, when processing such materials, it is usually necessary to reduce the laser power or increase cooling measures to avoid overheating.
- Surface condition: The surface condition of the material can also have an important impact on the marking effect. A smooth, clean surface ensures that the laser acts evenly and produces a clear and consistent marking pattern. However, a rough or coated surface can cause an uneven distribution of laser energy, resulting in unclear marking or insufficient contrast. The thickness and uniformity of the coating are particularly important. If the coating is uneven, the laser may produce different effects in different areas, resulting in inconsistent marking. Proper surface preparation before marking, such as cleaning, grinding or coating, can significantly improve the marking effect.
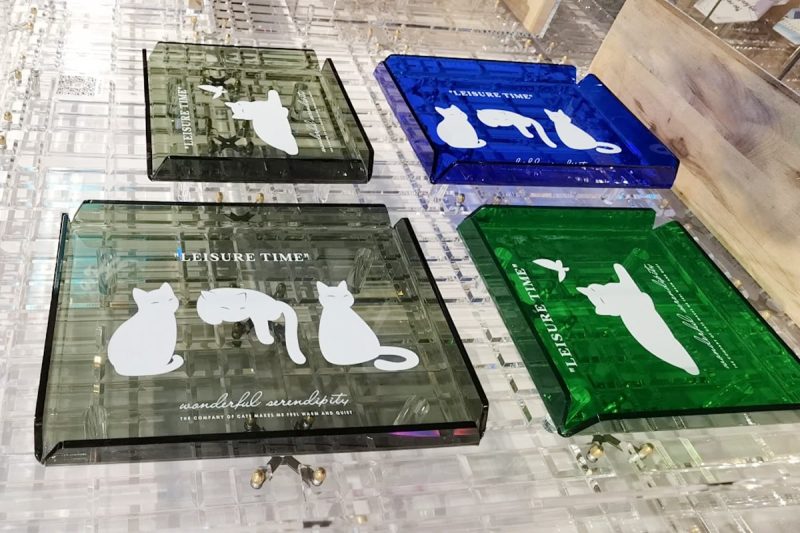
Influence of Laser Parameters
- Power setting: Laser power is an important factor affecting the depth and effect of marking. When the power setting is too high, the laser energy is too large, which can easily cause excessive ablation, melting, or deformation of the material surface, especially for heat-sensitive materials such as plastics or thin metals. Excessive power may also cause rough and uneven edges of the marking, affecting the overall appearance. When the power is too low, the laser energy is insufficient and cannot effectively act on the material surface, resulting in unclear or even difficult-to-identify markings. Therefore, the power setting needs to be precisely adjusted according to the characteristics of the material and the specific requirements of the marking to ensure that sufficient marking depth can be achieved without damaging the material surface.
- Pulse frequency: The pulse frequency refers to the number of pulses emitted by the laser generator per second, which has an important impact on the speed and surface quality of the marking. A higher pulse frequency means that the laser energy is more evenly distributed, which helps to produce a smoother marking surface and is suitable for applications requiring fine marking. However, too high a frequency may also cause the laser energy to be too dispersed, affecting the depth and contrast of the marking. A lower pulse frequency will make the laser energy more concentrated, which is suitable for scenes that require a larger marking depth, but may cause a slight roughness on the surface. Therefore, according to different materials and marking requirements, choosing the right pulse frequency can strike a balance between depth and surface finish.
- Marking speed: The marking speed refers to the speed at which the laser moves on the surface of the material, which has a direct impact on the depth, efficiency, and effect of the marking. Higher marking speeds can improve production efficiency and are suitable for large-scale processing needs. However, as the speed increases, the laser stays on the material for a shorter time, and the marking depth also decreases, which may affect the clarity and contrast of the marking. For applications that require deep marking or higher precision, it is usually necessary to reduce the marking speed to ensure that the laser has enough time to interact effectively with the material. The speed setting needs to comprehensively consider the marking requirements and the characteristics of the material to achieve a balance between efficiency and quality.
- Focal length adjustment: The accuracy of the laser focal length is critical to the quality of the marking. The focal length refers to the distance between the laser beam and the surface of the material. The laser energy at the optimal focal length is concentrated, which can produce clear and accurate marking effects on the surface of the material. If the focal length is not adjusted correctly, the energy of the laser beam will be dispersed, resulting in blurred and out-of-focus marking, and it is impossible to achieve clear patterns or text. Especially in fine marking, even a slight deviation in focal length will have a significant impact on the final effect. Regularly calibrating the focus of the equipment and confirming the accuracy of the focal length before marking are key steps to ensure the consistency of the marking effect.
In general, the correct setting of laser parameters is crucial to obtain high-quality laser marking results. By properly adjusting the power, pulse frequency, marking speed, and focal length, the clarity, depth, and contrast of the marking can be effectively improved, ensuring that the laser marking performs best in different materials and applications.
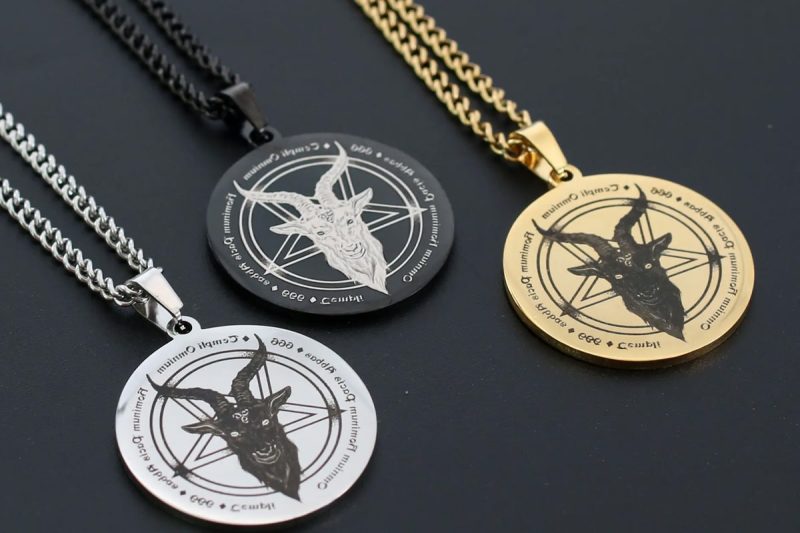
Influence of Environmental Conditions
- Temperature: The ambient temperature has a direct impact on the operating status of the laser marking machine. Excessive temperature may cause overheating inside the equipment, especially the laser source and electronic components. Overheating will reduce the working efficiency of the equipment and even cause failure or damage. In addition, the output power of the laser generator may become unstable in a high-temperature environment, resulting in fluctuations in the intensity of the laser beam during the marking process, and affecting the consistency and clarity of the marking. On the contrary, too low a temperature may also affect the startup and normal operation of the equipment, especially in cold areas or seasons, where the laser generator may take longer to warm up. Therefore, maintaining the ambient temperature of the equipment within the manufacturer’s recommended range (usually 15°C to 30°C) is the key to ensuring the stable operation of the laser marking machine.
- Humidity: Excessive humidity is another major hidden danger that affects the performance of laser marking equipment. A high humidity environment may cause the optical components of the laser marking machine to be damp, such as lenses, lenses, and other key components. If these optical components are damp, the laser beam will scatter and attenuate during transmission, resulting in unclear or blurred marking effects. In addition, high humidity may accelerate oxidation and corrosion inside the equipment and shorten the life of the equipment. To avoid humidity problems, the marking equipment should be installed in an environment with good humidity control, especially in rainy seasons or humid areas. It is recommended to use equipment such as dehumidifiers to keep the ambient humidity between 40%-60% to prevent the optical components and equipment from getting wet.
- Cleanliness: The cleanliness of the working environment has a significant impact on the accuracy and quality of laser marking. Particles such as dust, dirt, and oil stains may be deposited on the surface of the marking material or the optical components of the equipment, interfering with the transmission of the laser beam and the accuracy of the focal length, thereby reducing the clarity and contrast of the marking. In a production environment, especially in an industrial site, there are many dust particles in the air, which may affect the interaction between the laser beam and the surface of the material, resulting in uneven marking. To ensure the best marking effect, it is recommended to clean the equipment regularly, especially the lens and optical components, to keep the surface of the marking material clean and dust-free. During the cleaning process, use appropriate cleaning tools and methods to avoid scratching the optical components or damaging the surface of the material.
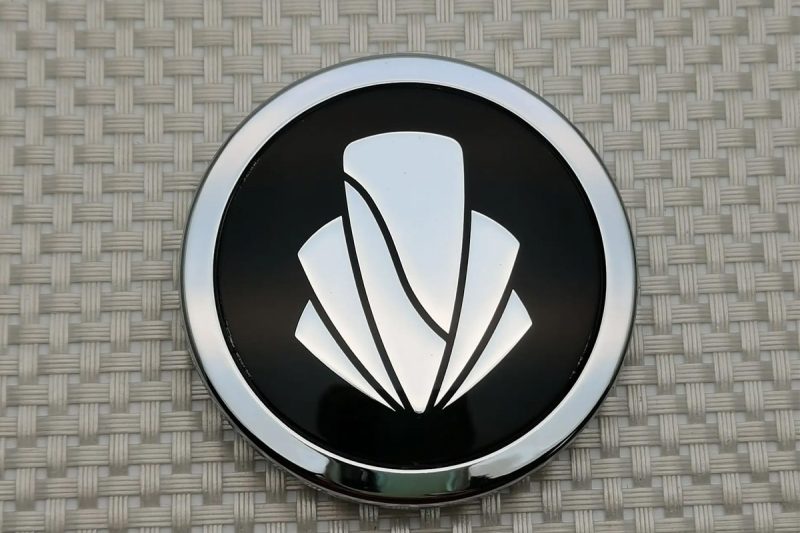
The Influence of Optical Components
- Lens quality: The lens is one of the most important optical components in the laser system. Its function is to focus the laser beam and project it accurately onto the surface of the material. If the lens quality is poor, such as scratches, dust, or insufficient optical performance on the lens surface, the laser beam will deviate or lose energy during the focusing process, which will affect the accuracy and clarity of the marking. Poor-quality lenses may cause blurred marking, out-of-focus, or uneven energy distribution, especially in occasions where fine processing is required, the marking effect will appear rough and uneven. Therefore, choosing high-quality optical lenses and regularly cleaning and maintaining them to ensure their stable optical performance is the key to ensuring marking accuracy.
- Beam transmission system: The beam transmission system is responsible for transmitting the laser from the laser source to the surface of the marking material. During this process, the energy of the laser must be transmitted efficiently without any energy loss or beam scattering. Any loss during the transmission process will affect the intensity and focusing effect of the laser, resulting in insufficient marking depth or reduced clarity. To ensure the efficiency of beam transmission, the various components of the transmission system, such as reflectors and transmission optical fibers, must be kept highly clean and intact. Any dust, dirt, or damage to the optical components will cause the beam to scatter and reflect poorly, thus affecting the marking results. An efficient and lossless beam transmission system can ensure the stability and consistency of the marking process, ensuring that the ideal effect can be achieved every time.
- Galvanometer scanner: The galvanometer scanner is a key component that controls the rapid movement and precise positioning of the laser beam, which directly determines the speed, accuracy, and consistency of the marking pattern. The galvanometer scanner adjusts the direction of the laser beam through a high-speed reflector to draw the required pattern or character on the surface of the material. Its scanning speed and accuracy are particularly important for the marking effect. High-precision galvanometer scanners can ensure the precise positioning of the laser beam in complex or tiny patterns to avoid deviations in lines or patterns. High-speed galvanometer scanners can improve marking efficiency and are suitable for mass production needs. However, too fast scanning speed may cause uneven energy distribution, affecting the depth and contrast of the marking. Therefore, while ensuring the speed, it is also necessary to ensure that the accuracy of the galvanometer remains within a reasonable range. The quality and performance of the galvanometer scanner are crucial to the stability of the marking effect. Therefore, a high-performance galvanometer system should be selected calibrated, and maintained regularly to ensure that it can maintain accurate marking effects even at high-speed scanning.
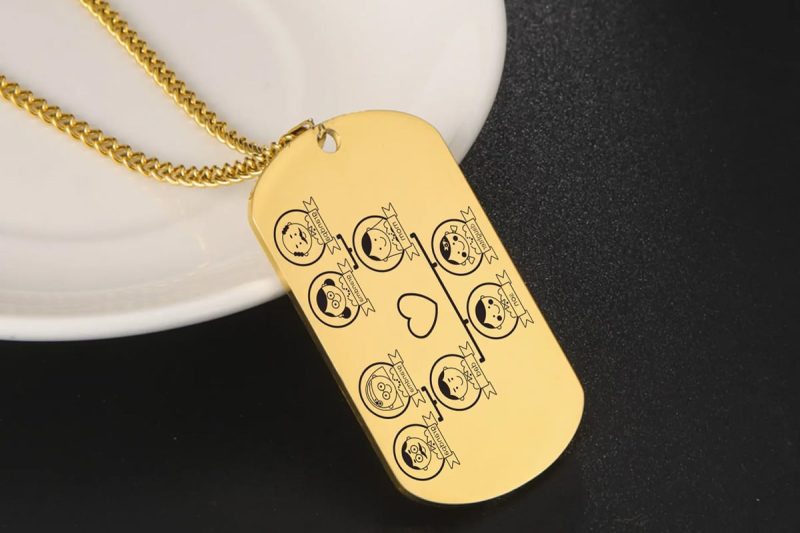
The Impact of Software and Control Systems
- Marking software: Marking software is an important tool for controlling laser marking equipment. It is responsible for setting and adjusting laser generator parameters, such as laser power, marking speed, pulse frequency, etc. High-quality software can not only accurately control these key parameters, but also provide rich marking functions, such as pattern design, font selection, barcode and QR code generation, etc. In addition, marking software can achieve multi-level marking and support various processing requirements of different materials, such as high-precision and different depth marking on metal, plastic, glass, and other materials. Advanced marking software usually has a user-friendly interface, simplifies the operation process, enables operators to quickly familiarize themselves with and master the system, reduces human operation errors, and thus improves production efficiency and marking quality. At the same time, the upgradeability of the software is also very important. With the development of technology and changes in market demand, marking software needs to be continuously updated and optimized to adapt to new marking requirements.
- Motion control system: The motion control system is the core component used in the laser marking machine to control the coordinated movement between the laser head and the workpiece. It ensures that during the marking process, the laser head and the workpiece to be processed can be accurately synchronized, so that the laser beam moves on the material surface according to the set trajectory. This synchronization is essential to achieve consistency and accuracy of the marking pattern. Motion control systems usually include hardware such as motors, sensors, and controllers, and cooperate with marking software for real-time monitoring and adjustment. In high-precision marking, especially when complex patterns need to be marked on large areas of materials, the accuracy and response speed of the motion control system is particularly important. If the motion control system is not sensitive enough, the laser marking head may deviate, resulting in problems such as pattern deformation and uneven lines. Therefore, a stable and efficient motion control system is one of the key factors to ensure the consistency and clarity of laser marking.
- Automation: A highly automated laser marking system can significantly improve production efficiency, reduce errors in human operation, and ensure that each batch of products can obtain consistent marking effects. By introducing an automated control system, laser marking equipment can be seamlessly connected to the production line to achieve batch and continuous marking operations. For example, the automated system can automatically identify and locate the workpiece, adjust the height and focal length of the laser marking head, and ensure that each marking is carried out under optimal conditions. The automated system can also automatically change the marking pattern and parameters of different batches without human intervention, greatly improving production flexibility. In addition, the automation system can be connected with other factory management systems to achieve real-time monitoring and analysis of production data, helping enterprises optimize production processes, improve product quality, and reduce costs. The automated marking system can also reduce operator involvement and reduce labor costs, especially in high-demand and high-volume production environments, where its advantages are particularly evident.
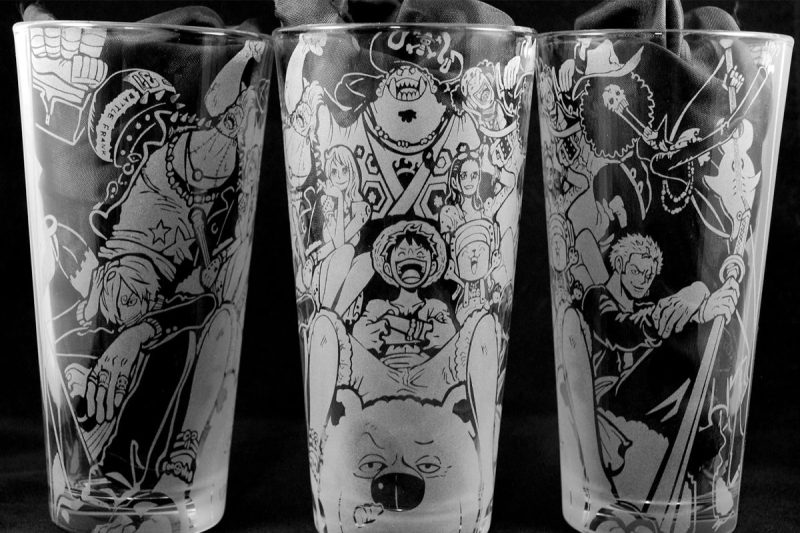
Effect of Cooling System
- Air cooling: Air cooling systems are often used for low-power laser equipment, such as some small fiber laser marking machines. This cooling method removes heat from the laser generator and other key components through air circulation devices such as fans. Due to the simple structure and low maintenance cost of the air cooling system, it is suitable for application scenarios with low heat dissipation requirements. The air cooling system has the advantages of a small footprint and compact design. It is usually integrated into the equipment without the need for external cooling equipment. Therefore, it is widely used in small laser marking machines with limited volume. However, the heat dissipation effect of air cooling is relatively weak and cannot cope with the large amount of heat generated by high-power laser generators. If high-power equipment is cooled by air, heat accumulation may occur, affecting the performance and life of the laser generator. Therefore, the air cooling system is mainly suitable for laser equipment with low power and low heat dissipation requirements.
- Water cooling system: Compared with air cooling, the water cooling system is suitable for high-power laser marking equipment, especially when long-term continuous operation is required, it can provide more effective heat dissipation. The water cooling system circulates the coolant (usually water or coolant) to the vicinity of the laser generator and other heat-generating components through a water pump and quickly removes the heat through the efficient heat transfer of water. Compared with air cooling, the water cooling system has higher heat capacity and conduction efficiency, which can ensure that the equipment can maintain stable operation in high-temperature environments or high-intensity working conditions, and avoid the power attenuation or marking quality degradation caused by overheating of the laser generator. In addition, the water cooling system can control temperature fluctuations and ensure that the laser generator always works within the optimal temperature range, thereby extending the service life of the equipment.
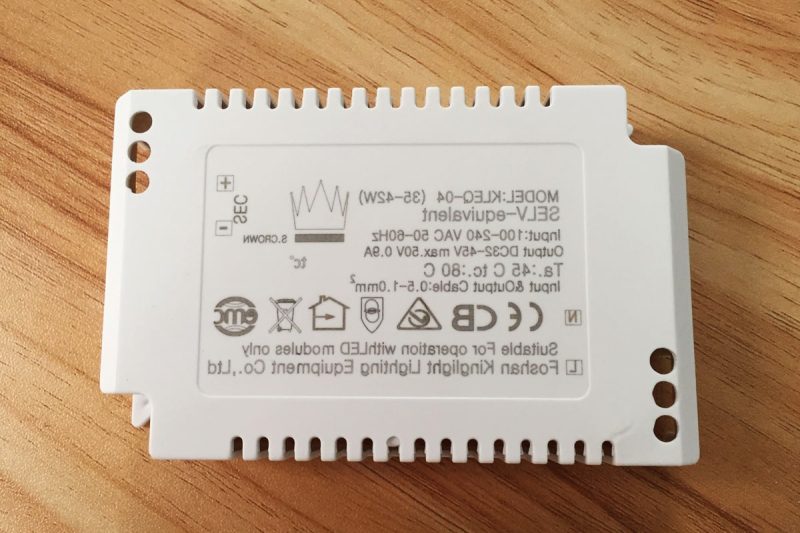
Operator Skills and Training
- Expertise: Laser marking operators need to have solid expertise, especially knowledge of different material properties and laser parameters. Different materials have different absorption rates, reflectivity, and thermal conductivity of lasers, so operators must reasonably adjust laser parameters such as laser power, marking speed, pulse frequency, etc. according to the characteristics of the materials. For example, metal materials usually require higher-power fiber laser generators, while non-metallic materials such as plastics or glass may be more suitable for UV lasers or CO2 laser generators. If the operator does not have enough knowledge of material properties and laser generator types, it may lead to unsatisfactory marking results, uneven depth, blur, and burning. Through systematic training, operators can master the marking requirements of different materials and ensure that each marking can achieve the best results.
- Calibration and maintenance: Laser marking equipment may experience wear or deviation of key components such as lenses, galvanometers, and beam transmission systems during long-term use. Therefore, regular equipment calibration and maintenance are essential to ensure that the equipment’s beam quality and marking accuracy are always in the best condition. Operators need to have the ability to perform daily inspections and simple troubleshooting of the equipment to detect and solve problems promptly. For example, the power attenuation of the laser generator, the reduced accuracy of the galvanometer scanning, and the contamination of the optical components will affect the marking effect. Well-trained operators can regularly calibrate the equipment to ensure the stable operation of the laser marking equipment and reduce production stagnation or quality degradation caused by equipment failure or parameter deviation. In addition, maintenance can not only extend the service life of the equipment but also avoid unexpected downtime or major failures and reduce repair costs.
- Operation proficiency and safety awareness: Although the operation of laser marking equipment has become simple, operators still need to have a certain level of proficiency to operate the equipment efficiently. Operators should master the operating procedures of various marking tasks at work, such as setting the marking path, adjusting the focal length, and selecting the appropriate marking speed and power. Skilled operators can quickly judge and adjust parameters to meet different marking needs, thereby improving production efficiency. In addition, operators must also have a certain level of safety awareness. Laser equipment may have certain safety hazards during operation, such as laser radiation and heat generation. Operators who have received professional training can effectively avoid safety problems caused by improper operation and ensure the safety of the production environment.
- Continuous learning and technology updates: Laser marking technology is constantly updated, and new marking equipment and software functions are also being launched. Therefore, operators need to continue to learn and adapt to new technologies, master the operation of new laser generators and marking software through training, and understand the latest process improvements. Continuous learning of operators can help companies maintain competitiveness, improve marking efficiency and product quality, and meet changing market demands.
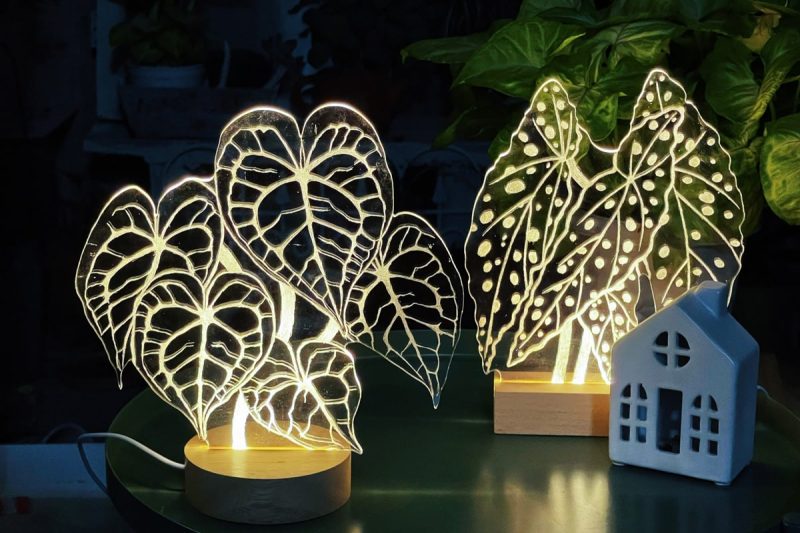
The Influence of Material Handling and Fixturing
Fixture
- Ensure workpiece stability: Precise clamping and fixation prevent the workpiece from moving slightly during the marking process, thereby ensuring accurate positioning and consistency of the marking pattern. This is especially important for high-precision marking tasks, such as marking tiny characters or complex patterns.
- Reduce errors: A stable fixture can effectively reduce marking errors caused by changes in the position of the workpiece, improving product consistency and quality. Especially in large-scale production, consistent fixture settings can ensure that each workpiece is marked under the same conditions.
- Adapt to different workpieces: The design of the fixture should take into account workpieces of different shapes and sizes so that it can be flexibly applied in various production tasks. The fixture should have a quick adjustment function to facilitate the operator to set it according to different workpiece requirements, thereby improving production efficiency.
Material Preparation
- Cleaning: Before marking, the cleanliness of the material surface is critical. Impurities such as dirt, grease, and dust can interfere with the transmission of the laser beam, resulting in blurred and uneven marking patterns. Using appropriate cleaning methods, such as ultrasonic cleaning or chemical cleaning, can effectively remove surface contamination and ensure the clarity and consistency of laser marking.
- Treatment: Some materials may require additional surface treatment, such as grinding, sandblasting, or chemical treatment, to improve their surface finish and laser adhesion. These treatment steps can reduce the unevenness of the material surface and enhance the marking effect, especially in application scenarios where high smoothness is required.
- Inspection: Before marking, the material surface should be inspected to ensure that it meets the marking requirements. Materials with obvious defects or uneven surfaces may require additional treatment to avoid negatively affecting the final marking effect.
Batch Processing
- Standardization: To maintain consistent marking results in mass production, standardized operating procedures, and fixture designs must be adopted. Standardization can reduce marking errors caused by operational differences or inconsistent workpiece positions.
- Automation: In mass production, the application of automation systems can significantly improve production efficiency and consistency. Automated systems can quickly and efficiently complete the task of marking large numbers of workpieces and ensure that each workpiece is processed under the same conditions, thereby reducing human error and fluctuations in production.
- Quality Control: When producing in bulk, strict quality control measures need to be implemented, including regular inspections and testing, to ensure that each batch of products meets quality standards. Real-time monitoring of the marking effect can promptly detect and correct potential problems to ensure product consistency and stability.
In summary, fixture design, material preparation, and batch processing are all important factors affecting the quality of laser marking. By optimizing the stability of the fixture, improving the cleanliness and consistency of the material surface, and implementing standardization and automation in batch production, companies can ensure high precision, high efficiency, and high quality of the marking process.
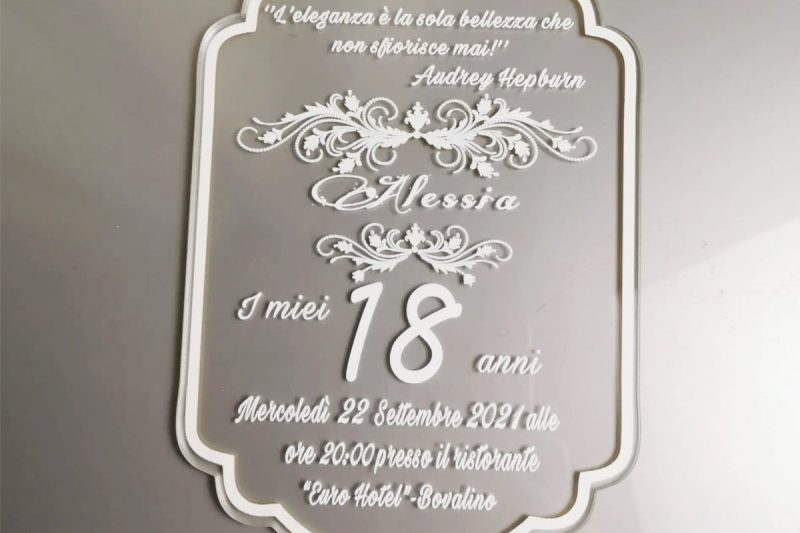
Impact of Application-Specific Factors
Marking Depth
- Depth requirements: In some specific applications, such as manufacturing and industrial parts, a deeper mark may be required to ensure that the mark is durable and remains readable over long-term use. For example, aerospace parts and tools often require a deeper mark to remain legible in high-friction and harsh environments. Deep marks not only help improve the durability of the mark but also enhance its resistance to wear.
- Surface marking: In contrast, for some applications that only require surface marking, such as consumer product labels or decorative markings, a shallower mark depth is sufficient. In this case, a shallower mark depth can reduce material loss and processing costs while meeting the readability requirements of the mark.
Marking Contrast
- QR codes and barcodes: High contrast is essential for machine-readable marks such as QR codes and barcodes. High-contrast marks ensure that scanning devices can accurately read information and avoid reading failures due to blurred marks or insufficient contrast. Using appropriate laser parameters and material processing technology, the contrast of the mark can be enhanced to ensure reliable transmission of information.
- Visual marking: High contrast is equally important in some applications that require manual identification, such as product numbers, brand logos, etc. Clear marking can improve recognition efficiency and accuracy and reduce the possibility of misidentification. In these cases, the marking machine needs to adjust parameters according to the characteristics of different materials to ensure the clarity and readability of the mark.
Marking Durability
- Harsh environments: In some industrial applications, the marking needs to withstand harsh environments such as high temperatures, chemical corrosion, and ultraviolet radiation. For example, automotive parts and mechanical equipment are exposed to various external factors during use, which requires the marking to have high durability and resistance to loss. Choosing the right laser type and material processing process can improve the durability of the marking and ensure that the marking remains clear and readable during long-term use.
- Long-term use: For some markings that need to be preserved for a long time, such as serial numbers on electronic components or logos on medical devices, durability is equally important. The laser marking machine needs to adjust the laser parameters to ensure that the marking will not fade, wear, or be lost in long-term use, to maintain its original state and function.
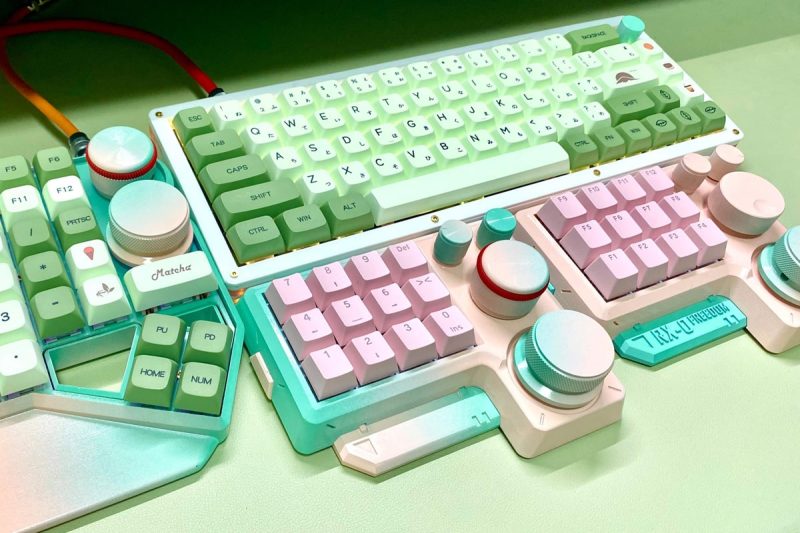
Summarize
- The choice of laser source directly determines the applicable materials and marking results. For example, fiber lasers are suitable for metal materials, CO2 lasers are suitable for non-metallic materials, and ultraviolet (UV) lasers are suitable for applications that require fine marking.
- Material properties such as absorption, reflectivity, and surface condition will affect the transmission of the laser beam and the final marking effect. Material handling and surface preparation also have a direct impact on the marking quality.
- Laser parameters include power settings, pulse frequency, marking speed, and focal length adjustment, which must be set accurately to ensure clear and compliant marking.
- Environmental conditions such as temperature, humidity, and cleanliness will affect the stability of the equipment and the quality of the laser beam.
- The performance of optical components such as lens quality, beam delivery system, and galvanometer scanner is also directly related to the accuracy and consistency of marking.
- The quality of software and control systems determines the accuracy of marking and the ease of operation. Excellent software and automation systems can improve marking efficiency and quality.
- The cooling system is crucial to the stable operation of laser equipment. An efficient cooling system can extend the life of the equipment and maintain equipment performance.
- Operator skills and training are the basis for ensuring marking quality. A professional operator can correctly set the equipment parameters and perform regular maintenance to ensure the best performance of the equipment.
- Material handling and fixture design are also important factors affecting the marking effect. Stable fixtures and proper material handling can improve the consistency and accuracy of marking.
- Application-specific factors such as marking depth, contrast, and durability, depending on the application requirements, the marking quality standards are also different.
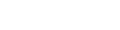
- [email protected]
- [email protected]
- +86-19963414011
- No. 3 Zone A, Lunzhen Industrial Zone,Yucheng City , Shandong Province.