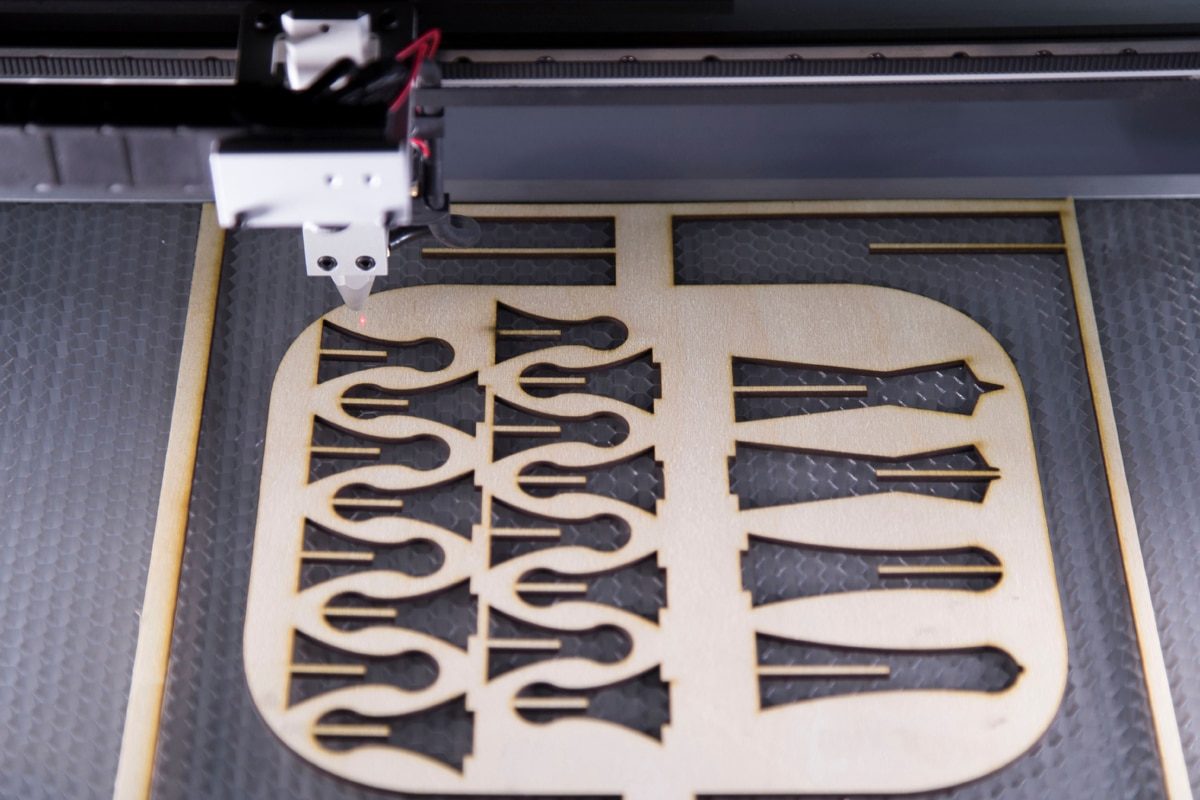
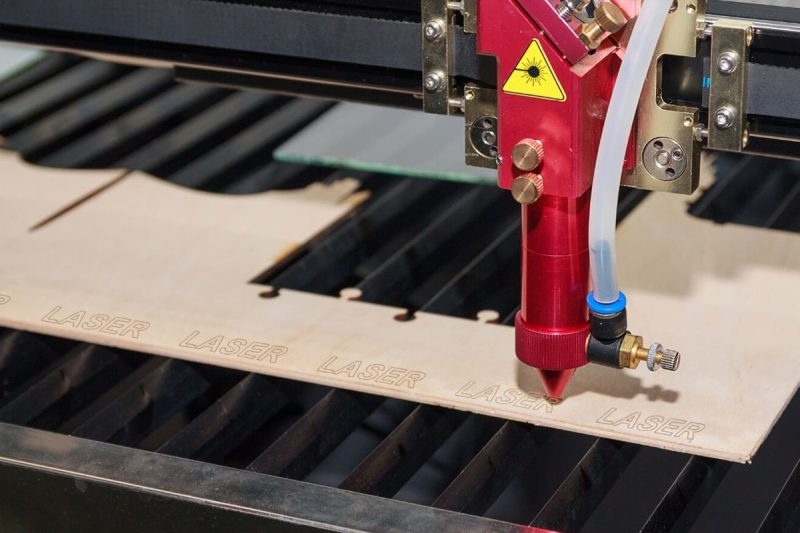
Fundamentals of CO2 Laser Cutting
Principles of Operation
Common Applications
CO2 laser cutting is known for its versatility and adaptability, making it a valuable tool across diverse industries. Some of its primary applications include:
- Automotive Industry: CO2 lasers are used to cut interior and exterior non-metal components, including dashboards, upholstery, and seals. The precision and speed of CO2 lasers also make them ideal for cutting complex shapes in automotive plastics and composites.
- Aerospace and Electronics: The high precision of CO2 lasers allows manufacturers to create intricate components for aerospace and electronic products. Thin materials like polyimide films, used in flexible electronics, and aerospace composites are frequently processed with CO2 laser cutting.
- Textiles and Apparel: CO2 laser cutting has gained popularity for cutting fabrics, leather, and other textile materials. The non-contact nature of the laser beam allows for intricate patterns without fraying or distortion, an essential requirement in the fashion and garment industries.
- Signage and Advertising: CO2 lasers excel at cutting materials such as acrylic, wood, and certain plastics, commonly used in signage production. They allow for detailed designs, complex shapes, and clean edges, producing high-quality and visually appealing signage.
- Packaging: In packaging, CO2 lasers cut cardboard, paper, and thin plastic films with precision, offering a versatile solution for packaging designs, die cuts, and intricate shapes.
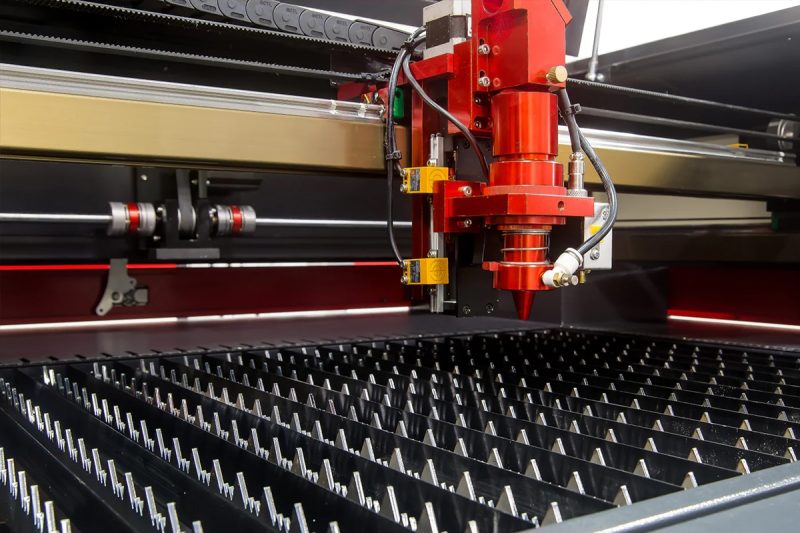
Key Factors Influencing Cutting Speed
The cutting speed of CO2 laser cutting machines depends on various interconnected factors. Optimizing these factors is essential for achieving efficient, precise, and high-quality cuts.
Laser Power
Material Type and Thickness
Assist Gas Type and Pressure
Assist gases play an important role in the cutting process by expelling molten material, cooling the cut zone, and sometimes facilitating oxidation reactions that enhance cutting speed. The type and pressure of the assist gas influence how efficiently the cutting process occurs:
- Oxygen (O2): Oxygen is commonly used for cutting carbon-based materials, as it reacts with the material to produce additional heat (oxidation), speeding up the cutting process. It is particularly effective for thick materials but may lead to oxidation on the cut edges.
- Nitrogen (N2): Nitrogen is often used for cutting stainless steel and aluminum, as it prevents oxidation and produces cleaner cuts. It does not contribute to the cutting heat, so it generally results in slower cutting speeds compared to oxygen.
- Air: In some applications, compressed air is used as an economical assist gas. While it can be effective for thin materials and non-metallics, it generally does not provide the same cutting quality as oxygen or nitrogen for metals.
Beam Quality
Focus Position
Cutting Speed Settings
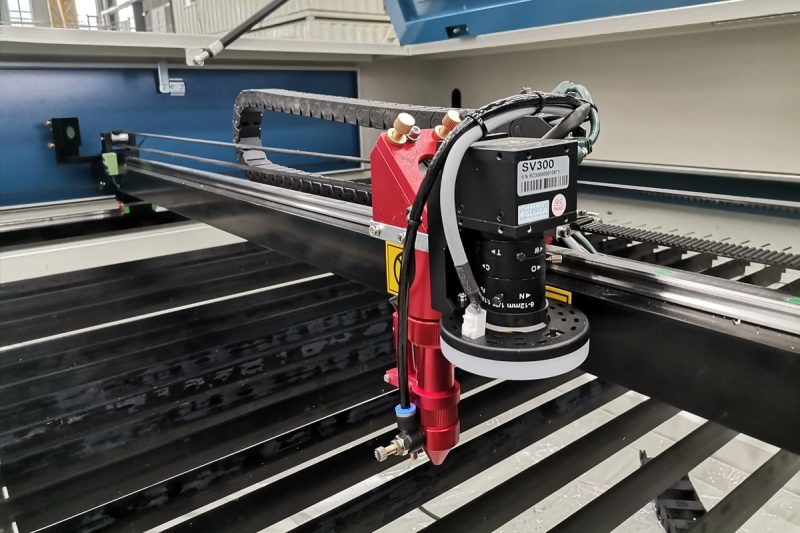
Key Factors Influencing Cutting Accuracy
Machine Precision and Stability
Beam Focus and Spot Size
Nozzle Design and Condition
Material Properties
Environmental Conditions
Operator Skill and Experience
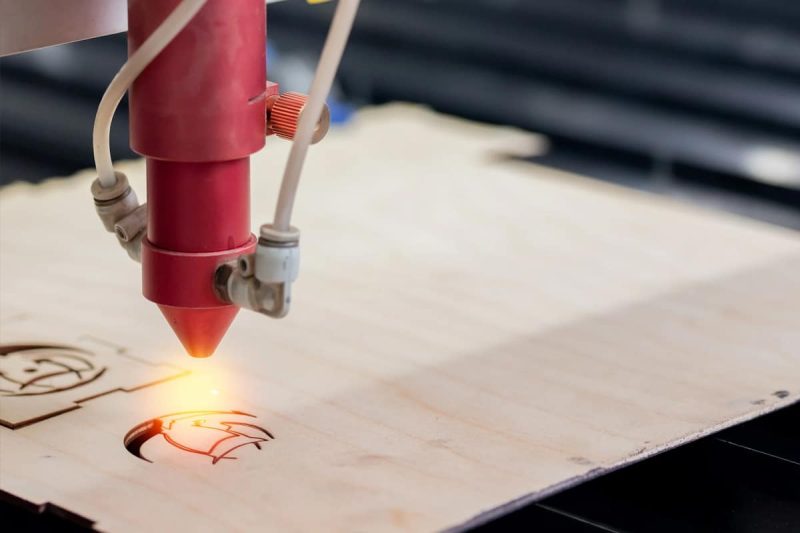
Optimization Strategies
Parameter Selection
Selecting the correct parameters is one of the most effective ways to optimize the speed and accuracy of CO2 laser cutting. Key parameters include laser power, cutting speed, assist gas type and pressure, and focus position. Fine-tuning these parameters for each material and thickness ensures optimal cutting performance.
- Laser Power: Adjusting the laser power based on the material type and thickness ensures precise cuts without excessive heat buildup or thermal distortion. Higher power is suitable for thick materials but may require slower speeds to maintain accuracy.
- Cutting Speed: Balancing cutting speed with laser power is critical. Excessively fast speeds can reduce edge quality, while slower speeds can enhance accuracy but decrease productivity. The ideal speed depends on material properties and the desired cut quality.
- Assist Gas: Selecting the appropriate assist gas (oxygen, nitrogen, or air) and adjusting its pressure optimizes material removal, improves edge quality, and can speed up the cutting process.
- Focus Position: Proper focus positioning ensures that the laser beam is concentrated at the correct point on the material, maximizing energy transfer and precision. Adjusting the focus based on material thickness and type is essential for achieving consistent results.
Maintenance Practices
Regular maintenance is vital to keep the CO2 laser-cutting machine operating at peak performance. A well-maintained machine produces more accurate cuts, operates more efficiently, and experiences fewer breakdowns. Key maintenance practices include:
- Optical Component Cleaning: Mirrors, lenses, and other optical components should be cleaned regularly to prevent dirt and debris from reducing beam quality and accuracy.
- Nozzle Maintenance: Inspecting and cleaning the nozzle ensures consistent assist gas flow, which is critical for accurate and efficient cutting.
- Alignment Checks: Periodic checks and alignment of optical components help maintain consistent beam focus and energy distribution.
- Lubrication: Regular lubrication of moving parts reduces wear and ensures smooth motion, improving both speed and precision.
- Calibration: Routine calibration of the laser cutter’s motion system and other components helps maintain accuracy and prevent mechanical drift.
Software and Control Systems
Advanced software and control systems play a crucial role in optimizing CO2 laser cutting performance. The right software can enhance cutting speed, improve precision, and enable complex geometries. Key features to focus on include:
- Path Optimization: Software that optimizes the cutting path minimizes unnecessary movements and reduces cycle times, increasing productivity without compromising accuracy.
- Real-Time Monitoring: Real-time feedback and monitoring systems enable operators to make adjustments on the fly, ensuring consistent cutting performance.
- Automation: Integrating automation features, such as automated loading/unloading or process parameter adjustments, reduces human error and increases operational efficiency.
- User-Friendly Interfaces: Intuitive software interfaces allow operators to easily set and adjust parameters, monitor performance, and troubleshoot issues, enhancing overall productivity and cutting accuracy.
Training and Skill Development
The skill and expertise of the machine operator can significantly impact the performance of a CO2 laser-cutting machine. Investing in operator training and skill development is essential for optimizing speed and accuracy. Effective strategies include:
- Training Programs: Comprehensive training programs that cover machine operation, parameter optimization, and maintenance practices ensure that operators can make informed decisions to maximize cutting performance.
- Hands-On Experience: Encouraging operators to gain hands-on experience with various materials and cutting scenarios allows them to develop practical skills and identify potential challenges quickly.
- Continuous Learning: Providing opportunities for ongoing education on the latest technologies, software features, and cutting techniques keeps operators up-to-date and capable of optimizing machine performance.
- Troubleshooting Skills: Equipping operators with the skills to diagnose and resolve issues ensures minimal downtime and consistent performance, enhancing both speed and accuracy.
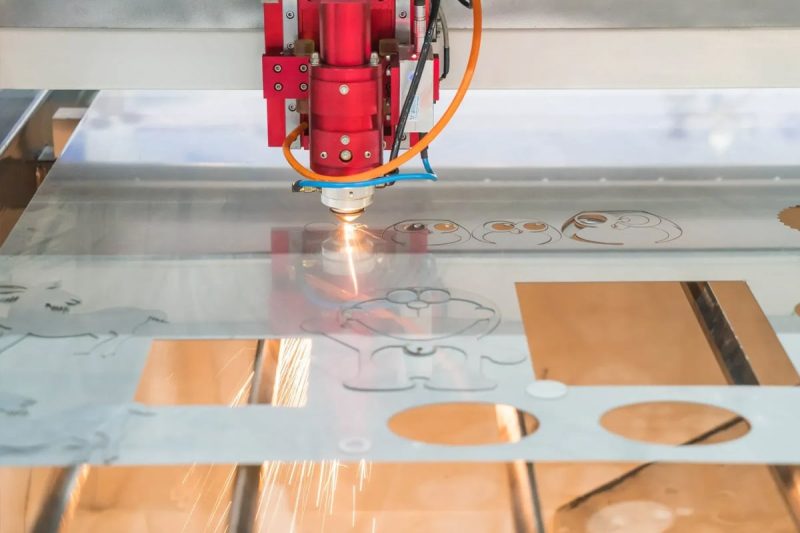
Summary
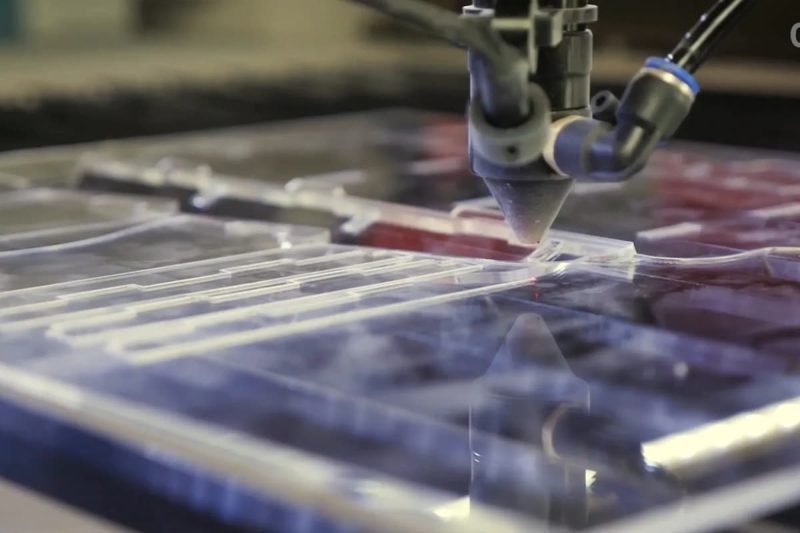
Get Laser Cutting Solutions
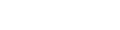
- [email protected]
- [email protected]
- +86-19963414011
- No. 3 Zone A, Lunzhen Industrial Zone,Yucheng City , Shandong Province.