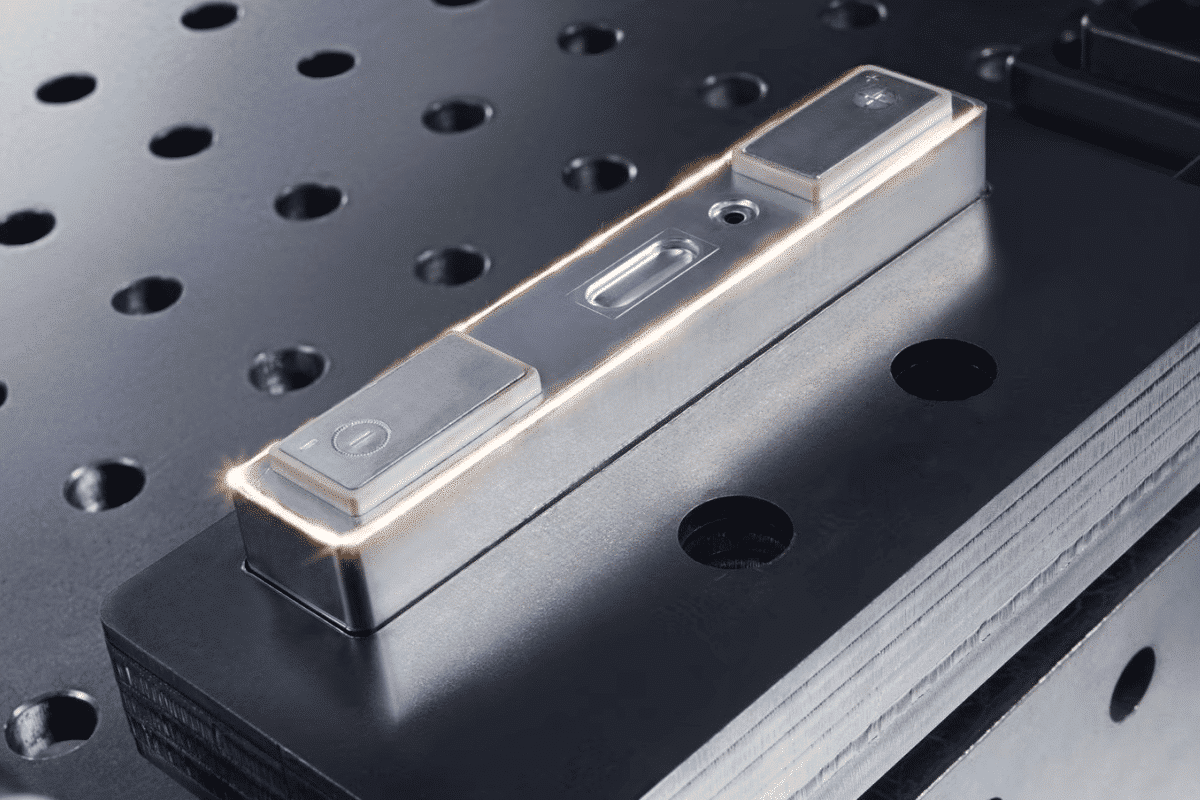
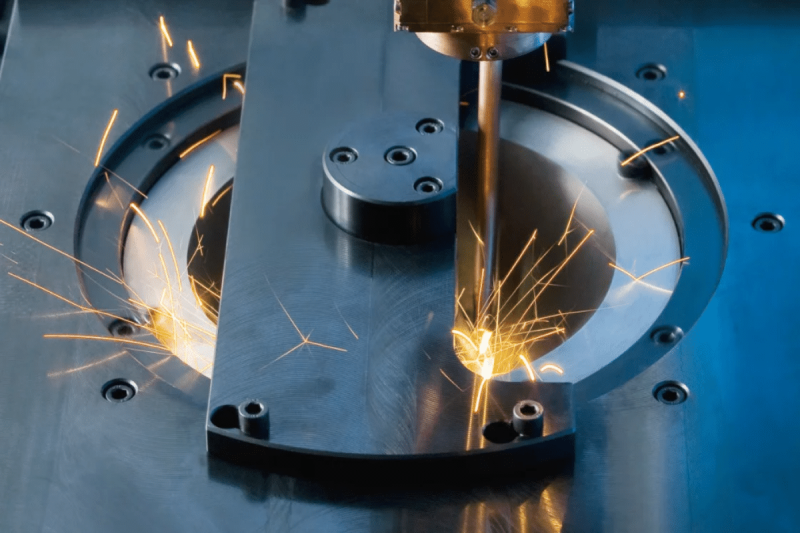
Why is gas needed for laser welding?
Protection of welding areas
Heat Control
Improved weld quality
Gas cooling
Gas protection of optical systems
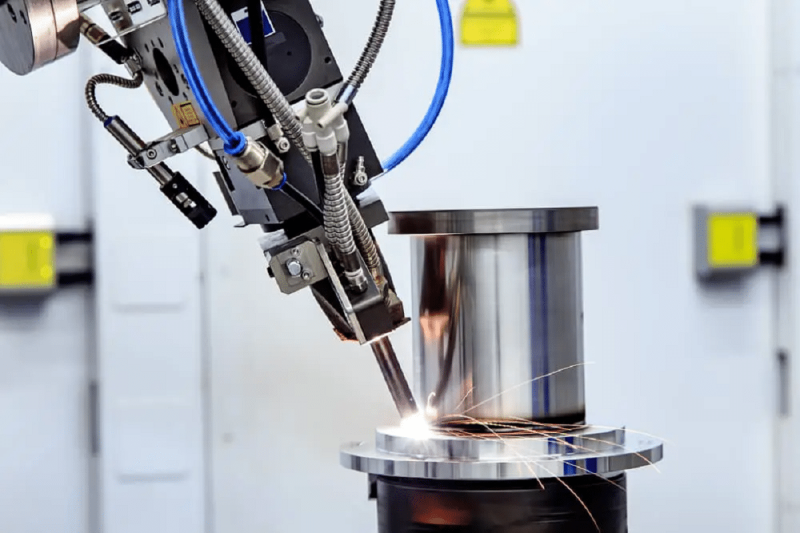
Which gases are used in laser welding?
Protective gas
Shielding gases, sometimes called “inert gases,” play an important role in the laser welding process. Laser welding processes often use inert gases to protect the weld pool. The commonly used protective gases in laser welding mainly include argon and neon. Their physical and chemical properties are different, so their effects on the weld are also different.
- Argon: Argon is one of the most commonly used inert gases. It has a high degree of ionization under the action of the laser, which is not conducive to controlling the formation of plasma clouds, which will have a certain impact on the effective use of lasers. The inert nature of argon keeps it out of the soldering process, while it also dissipates heat well, helping to control the temperature in the soldering area.
- Neon: Neon is often used as an inert gas, similar to argon, and is mainly used to protect the welding area from oxygen and other pollutants in the external environment. It is important to note that neon is not suitable for all laser welding applications. It is mainly used for some special welding tasks, such as welding thicker materials or when deeper weld seams are required.
Auxiliary gas
During the laser welding process, in addition to the main protective gas, auxiliary gases can also be used to improve welding performance and quality. The following are some common auxiliary gases used in laser welding:
- Oxygen: Oxygen is commonly used as an assist gas and can be used to increase heat and weld depth during welding. Adding oxygen can increase welding speed and penetration, but needs to be carefully controlled to avoid excess oxygen causing oxidation problems.
- Nitrogen: Nitrogen is also often used as an auxiliary gas in laser welding. The ionization energy of nitrogen is moderate, higher than argon and lower than hydrogen. The ionization degree is generally under the action of a laser. It can better reduce the formation of plasma clouds, provide higher quality welds and appearance, and reduce the impact of oxygen on the welds. Nitrogen can also be used to control the temperature of the welding area and reduce the formation of bubbles and pores.
- Hydrogen/Hydrogen Mixture: Hydrogen improves the quality of welds and reduces the formation of porosity. Mixtures of argon and hydrogen are used in some special applications, such as welding stainless steel. The hydrogen content of the mixture typically ranges from 2% to 15%.
- Helium: Helium is usually used for high-power laser welding because it has low thermal conductivity and is not easily ionized, allowing the laser to pass smoothly and the beam energy to reach the workpiece surface without any obstacles. Conducive to higher power welding. Helium can also be used to improve weld quality and control welding temperatures. This is the most effective shielding gas used in laser welding, but it is relatively expensive.
Cooling gas
Cooling gas is often used during laser welding to control the temperature of the welding area, prevent overheating, and maintain welding quality. The following are some commonly used cooling gases:
- Water: Water is a common cooling medium often used to cool laser generators and laser welding optical systems. Water cooling systems can help maintain a stable temperature of the laser generator and optical components to ensure laser beam stability and performance.
- Atmospheric gases: In some laser welding processes, ambient atmospheric gases can be used for cooling. For example, in the optical system of a laser generator, the surrounding atmosphere gas can provide a cooling effect.
- Inert gases: Inert gases such as argon and nitrogen can also be used as cooling gases. They have lower thermal conductivity and can be used to control the temperature of the welding area and reduce the heat-affected zone (HAZ).
- Liquid Nitrogen: Liquid nitrogen is an extremely low-temperature cooling medium that can be used for extremely high-power laser welding. It provides a very effective cooling effect and ensures temperature control in the welding area.
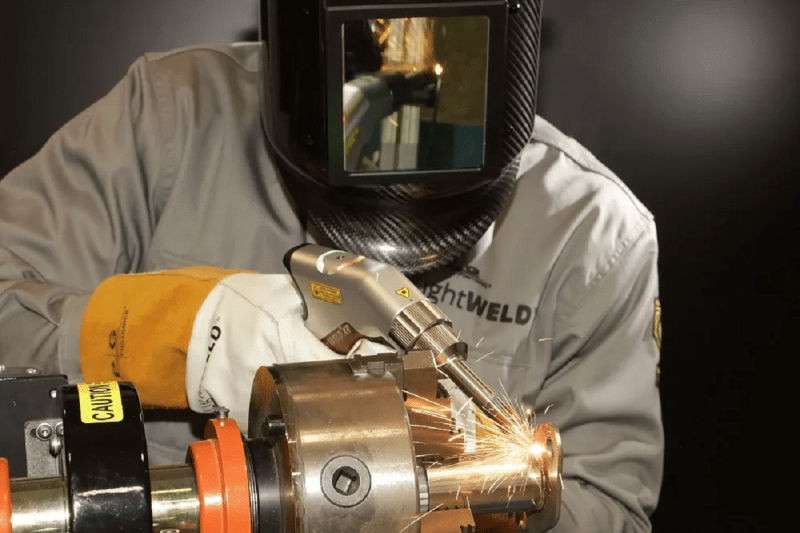
Gas selection in different applications
Type of welding material
Different materials require different gas combinations. Generally speaking:
- Stainless steel typically uses argon or an argon/hydrogen mixture.
- Aluminum and aluminum alloys often use pure argon.
- Titanium alloys often use nitrogen.
- High-carbon steels often use oxygen as an auxiliary gas.
Welding speed and penetration
Weld quality
Pore and Bubble Control
Control of Heat Affected Zone (HAZ)
Equipment and cost considerations
Summarize
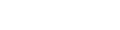
- [email protected]
- [email protected]
- +86-19963414011
- No. 3 Zone A, Lunzhen Industrial Zone,Yucheng City , Shandong Province.