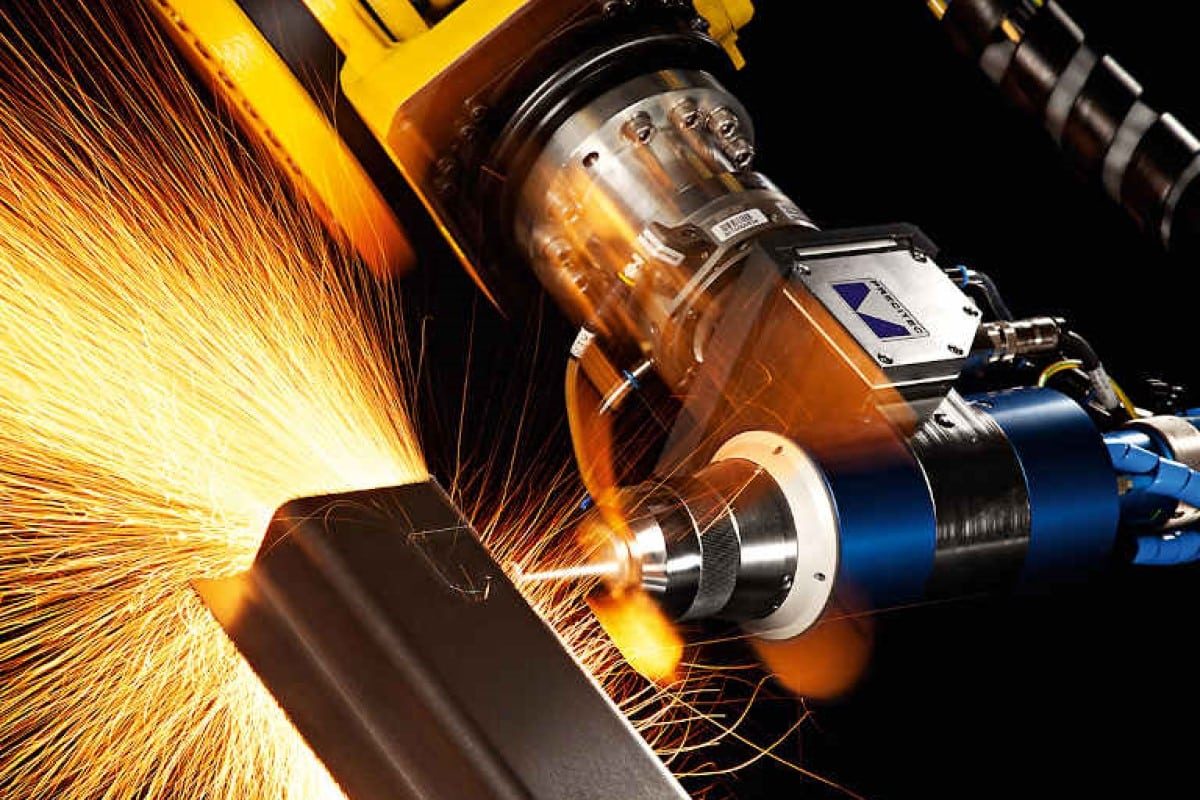
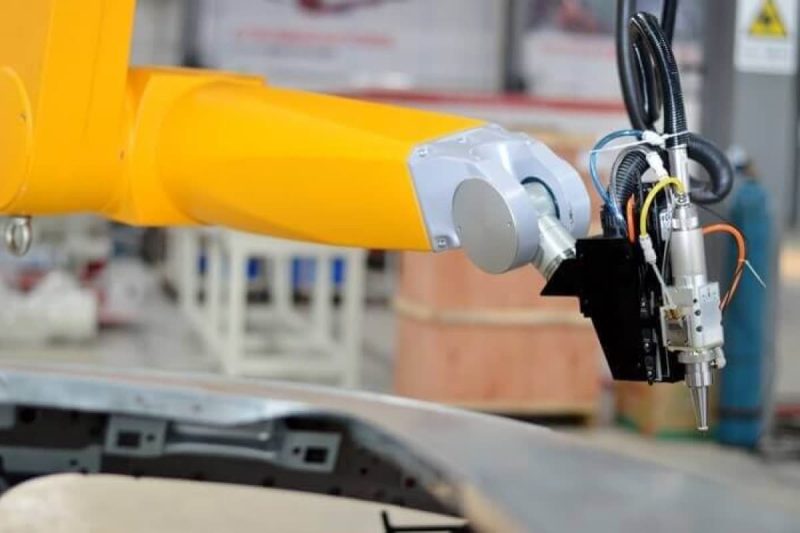
Working Principle of 3D Laser Cutting System
At its core, 3D laser cutting is a precision manufacturing process that utilizes the extraordinary properties of a highly focused laser beam to cut materials in three dimensions. This complex process unfolds through a series of carefully planned steps:
- Laser generator: It all starts with a high-power laser generator, typically using a carbon dioxide (CO2) or fiber laser generator. The choice of laser generator depends on the material being processed and the cutting characteristics required.
- Focusing optics: The laser beam then passes through a series of focusing optics that converge the beam into a highly concentrated laser beam. The quality of these optics plays a key role in determining the accuracy of the laser generator.
- Material interaction: A highly focused laser beam is directed to the surface of the material. When the laser comes into contact with a material, it heats up rapidly, causing the material to melt, evaporate, or be blown away. Results depend on material properties and laser parameter settings.
- Computer numerical control (CNC): Computer software systems often utilize computer numerical control (CNC) to coordinate the entire process. The software converts a 3D computer-aided design (CAD) model of an object into precise instructions for a laser cutting machine.
- Multi-axis movement: A defining feature of 3D laser cutting is its ability to operate in three dimensions (X, Y, and Z axes). This exceptional flexibility enables the laser to follow complex 3D paths, enabling the creation of complex shapes, contours, and complex geometries with unparalleled precision.
- Real-time adjustments: Throughout the laser cutting process, CNC software continuously monitors and fine-tunes the laser’s power, speed, and focus. This real-time adjustment ensures consistent and flawless results for even the most complex tasks.
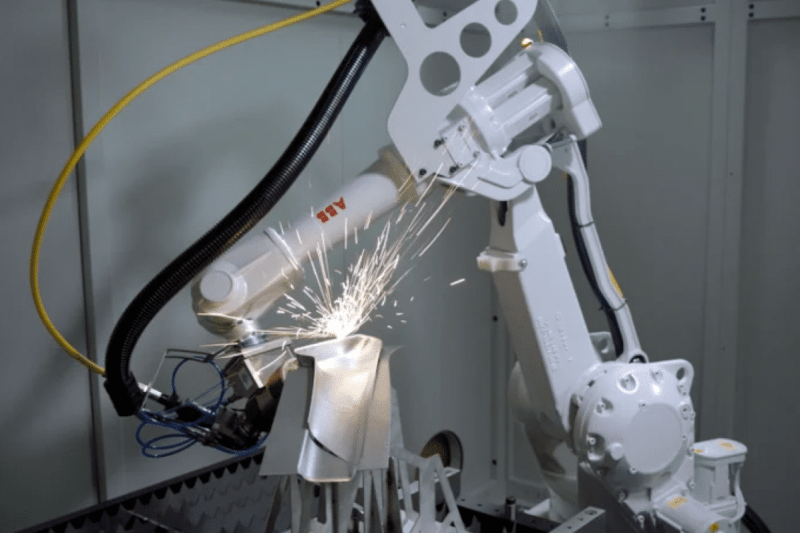
Basic Components of 3D Laser Cutting System
To fully understand 3D laser cutting, it is also necessary to be familiar with its core components:
- Laser generator: The core of the 3D laser cutting system, which can provide a high-intensity laser beam.
- Focusing optics: These optics, such as lenses and mirrors, focus the laser beam to a precise point to achieve the required precision.
- Material handling system: A mechanism that positions the material in place during the cutting process and makes adjustments as needed.
- CNC control system: A computer-based control system used to manage the entire cutting process from interpreting CAD designs to controlling laser movement and power adjustments.
- Laser head: The component that focuses the laser beam onto the surface of the material.
- Cooling system: Laser generators generate large amounts of heat, so a cooling system is required to maintain optimal performance.
- Exhaust system: This system can exhaust the smoke and debris generated during the laser cutting process to maintain a clean working environment.
- Safety measures: Basic safety measures include enclosure, smoke extraction, and operator protection.
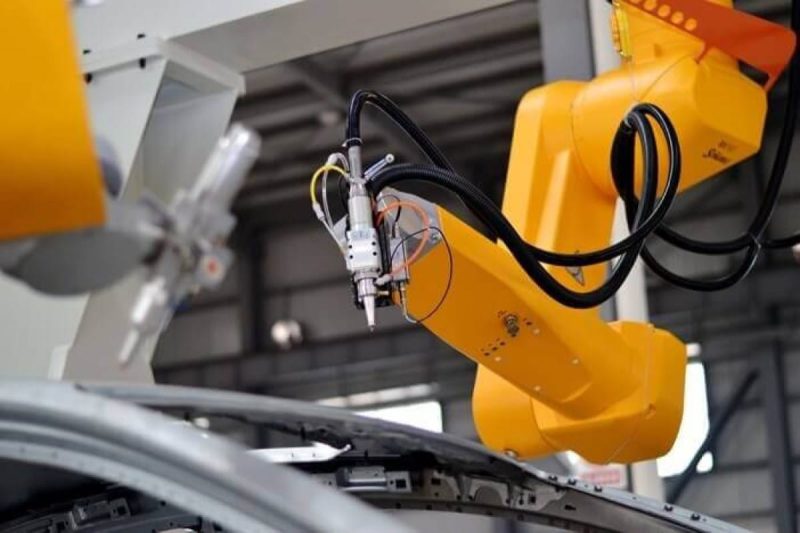
Advantages and Disadvantages of 3D Laser Cutting
Advantage
- Precision and accuracy: 3D laser cutting systems offer extremely high precision and accuracy, making them ideal for complex designs. It can cut with tolerances within millimeters, ensuring consistent quality. This is particularly valuable in industries where accuracy is critical, such as aerospace and medical device manufacturing.
- Versatility: 3D laser cutting systems can be used to cut a variety of materials, including metals, plastics, ceramics, composites, and more. This versatility makes it suitable for a variety of industries and applications.
- Speed and efficiency: Laser cutting is a fast cutting process, especially compared to traditional cutting methods. It can produce parts quickly and help improve overall production efficiency.
- No tool wear: Unlike traditional cutting methods that involve wear-and-tear tools, lasers have no physical tools that degrade over time. This results in consistent quality over a longer period of time and less maintenance requirements.
- Minimal material waste: The laser beam can be precisely controlled and laser cutting produces minimal material waste compared to other cutting methods. This can save costs, especially when working with expensive materials.
- Non-contact cutting: Laser cutting is a non-contact process, which means there is no physical contact between the tool and the material, reducing the risk of material deformation, contamination, or tool wear.
- Complex geometries: 3D laser cutting can easily create complex 3D shapes and contours that may be difficult or impossible to achieve with other cutting methods.
- Automation and Integration: 3D laser cutting systems can be integrated with CAD/CAM software to enable automated, computer-controlled cutting, thereby reducing labor costs and minimizing the possibility of human error.
- Minimal heat-affected zone (HAZ): Laser cutting produces a small heat-affected zone that minimizes deformation and metallographic changes of the material being cut. This is especially important for materials such as metals, as material properties are maintained.
- No mold costs: Unlike some traditional cutting methods, 3D laser cutting does not require expensive mold changes for different designs or materials, which reduces setup time and costs.
Disadvantages
- Initial cost: 3D laser cutting systems can be expensive to purchase and set up, which can make them prohibitive for small businesses or startups.
- Limited material thickness: Although suitable for a wide range of materials, there is a limit to the thickness of materials that can be cut with the laser. For thicker materials, other cutting methods such as plasma or waterjet cutting may be more suitable.
- Operating costs: Laser cutters have high operating costs due to energy consumption, maintenance, and the need for skilled operators.
- Safety issues: Laser cutting involves the use of high-powered laser beams, which can be dangerous to the operator if safety precautions are not followed. Proper safety precautions, including protective eyewear and safety interlocks, are essential.
- Material limitations: While 3D laser cutting can be used on a variety of materials, some materials, such as highly reflective metals, can present challenges due to their reflective properties. This type of material may require specialized equipment to cut effectively.
- Maintenance and downtime: Like all machinery, 3D laser cutting equipment requires regular maintenance to ensure it is operating at peak efficiency. Unexpected failures can cause production downtime. Additionally, maintenance costs may increase over time.
- Noise and smoke: Depending on the material being cut, the laser cutting process can produce noise and smoke, requiring adequate ventilation and noise control measures to ensure a safe working environment.
- Complex programming: Creating complex cutting paths and procedures can be time-consuming and may require a skilled operator with expertise in CAD/CAM software.
- Edge quality: While laser cutting generally produces clean, precise edges, some materials may have slight burrs or discoloration on the cut edges, which may require additional post-processing.
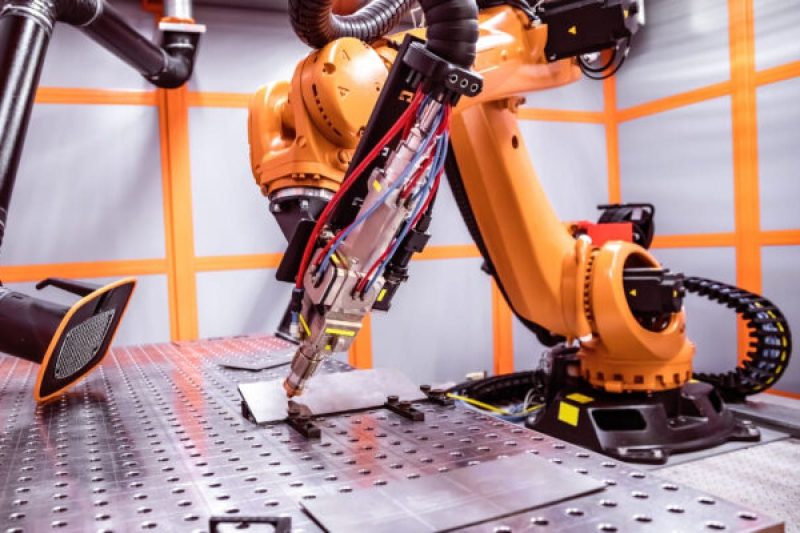
Applications of 3D Laser Cutting
3D laser cutting is a versatile manufacturing technology that finds applications in various industries due to its precision and ability to cut intricate and complex shapes. Here are some common applications of 3D laser cutting:
- Aerospace: 3D laser cutting is used in aerospace manufacturing to cut precise and lightweight components from materials like aluminum, titanium, and composite materials. It is essential for fabricating parts such as aircraft frames, turbine blades, and intricate engine components.
- Automotive: In the automotive industry, 3D laser cutting is employed to create precise components for vehicles, including chassis parts, exhaust systems, and complex body panels. It can also be used for cutting airbags, seatbelt components, and other safety features.
- Medical devices: 3D laser cutting is used to manufacture intricate medical devices and components, such as stents, catheters, surgical instruments, and orthopedic implants. Its precision is crucial in the medical field.
- Electronics: This technology is utilized for cutting and shaping delicate electronic components and circuit boards. It enables the production of intricate patterns and fine details required in electronics manufacturing.
- Architectural models: 3D laser cutting is used to create architectural models with precision and intricate detailing. It allows architects and designers to visualize and present their projects effectively.
- Jewelry manufacturing: In the jewelry industry, 3D laser cutting is used to cut and shape precious metals and gemstones to create intricate and customized jewelry pieces.
- Prototyping and rapid manufacturing: 3D laser cutting is valuable in rapid prototyping and small-batch production. It allows for quick design changes and the production of prototypes and custom parts.
- Art and sculpture: Artists and sculptors use 3D laser cutting to create intricate and detailed artworks and sculptures from various materials, including metal, wood, and acrylic.
- Packaging: This technology is used in the packaging industry to create custom-designed packaging materials, displays, and promotional items. It can also be used for cutting foam inserts for protective packaging.
- Textile and fashion: 3D laser cutting is employed in the textile and fashion industries for cutting intricate patterns in fabrics and leather. It enables the creation of unique and complex designs for clothing and accessories.
- Signage and advertising: In the signage and advertising industry, 3D laser cutting is used to cut materials like acrylic, wood, and metal to create eye-catching signs, displays, and promotional materials.
- Model making: Model makers use 3D laser cutting to create detailed scale models for architectural, engineering, and industrial purposes.
- Machinery and equipment: Manufacturers of heavy machinery and industrial equipment use 3D laser cutting to produce precise components, including gears, brackets, and housings.
- Agriculture: In agricultural machinery manufacturing, 3D laser cutting is used to fabricate parts for tractors, harvesters, and other equipment.
- Shipbuilding: Shipbuilders use 3D laser cutting to produce complex components for ships and boats, such as hull sections, structural components, and pipe fittings.
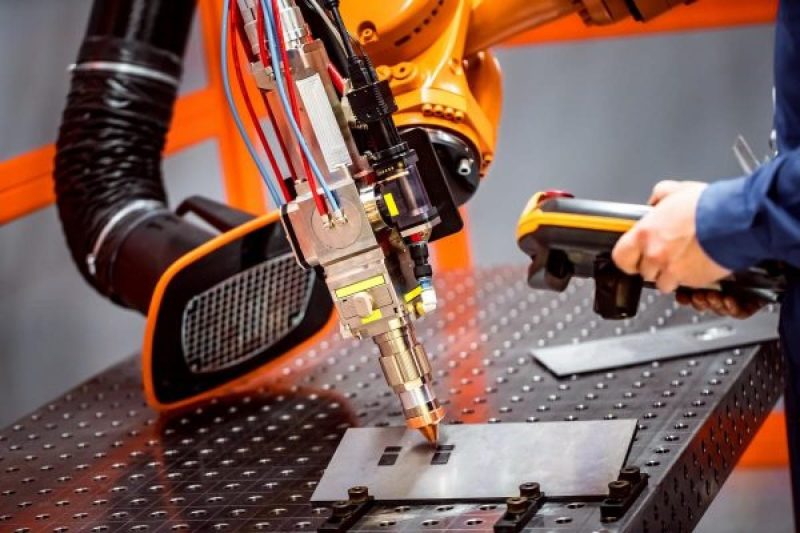
3D Laser Cutting Trends
3D laser cutting is a technology with huge potential for growth and innovation in various industries. Let’s take a look at some of the current trends and developments in 3D laser cutting technology:
- Improved precision and accuracy: One of the major trends in 3D laser cutting is the focus on improving precision and accuracy. Manufacturers are investing in better laser control systems, advanced optics, and more sophisticated software algorithms to ensure laser cutters can achieve tighter tolerances and cut complex 3D shapes with greater precision.
- Artificial intelligence (AI) integration: Artificial intelligence and machine learning will be incorporated into 3D laser cutting systems to optimize cutting paths, reduce errors, and improve overall efficiency. These AI-driven systems can analyze data in real-time to adapt to changing conditions and materials.
- Enhanced automation and robotics: Automation is an important trend in manufacturing, and 3D laser cutting systems are no exception. Robots and computer-controlled systems are used to load materials, position lasers, and remove finished parts. This not only increases productivity but also reduces the need for manual labor.
- Wider material range: 3D laser cutting is expanding beyond traditional materials such as metal. It is used to cut a wider range of materials, including composites, plastics, ceramics, and even organic materials such as fabrics.
- Environmental considerations: Sustainability is a growing concern as environmental concerns become more severe. Manufacturers are exploring ways to reduce energy consumption and waste during laser cutting, including innovations in beam delivery systems, cooling methods, and waste disposal.
- Faster processing speed: To increase productivity, manufacturers will continue to strive to increase the processing speed of 3D laser cutting systems. Improvements in laser technology, beam delivery systems, and motion control mechanisms allow for faster cuts without sacrificing quality.
- Reducing costs: As with many technologies, manufacturers are working to reduce the overall cost of 3D laser cutting systems, making them more accessible to a wider range of industries and applications. This involves not only making the machines cheaper but also reducing operating costs and maintenance requirements.
- Real-time monitoring and quality control: 3D laser cutting systems may add real-time monitoring systems and quality control measures to ensure cutting accuracy and consistency, which can help reduce material waste and improve overall efficiency.
- Enhanced user-friendly interface: Manufacturers are developing improved user interfaces and software tools to make 3D laser cutting systems more accessible to a wider range of users, including those without extensive technical expertise.
Summarize
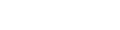
- [email protected]
- [email protected]
- +86-19963414011
- No. 3 Zone A, Lunzhen Industrial Zone,Yucheng City , Shandong Province.