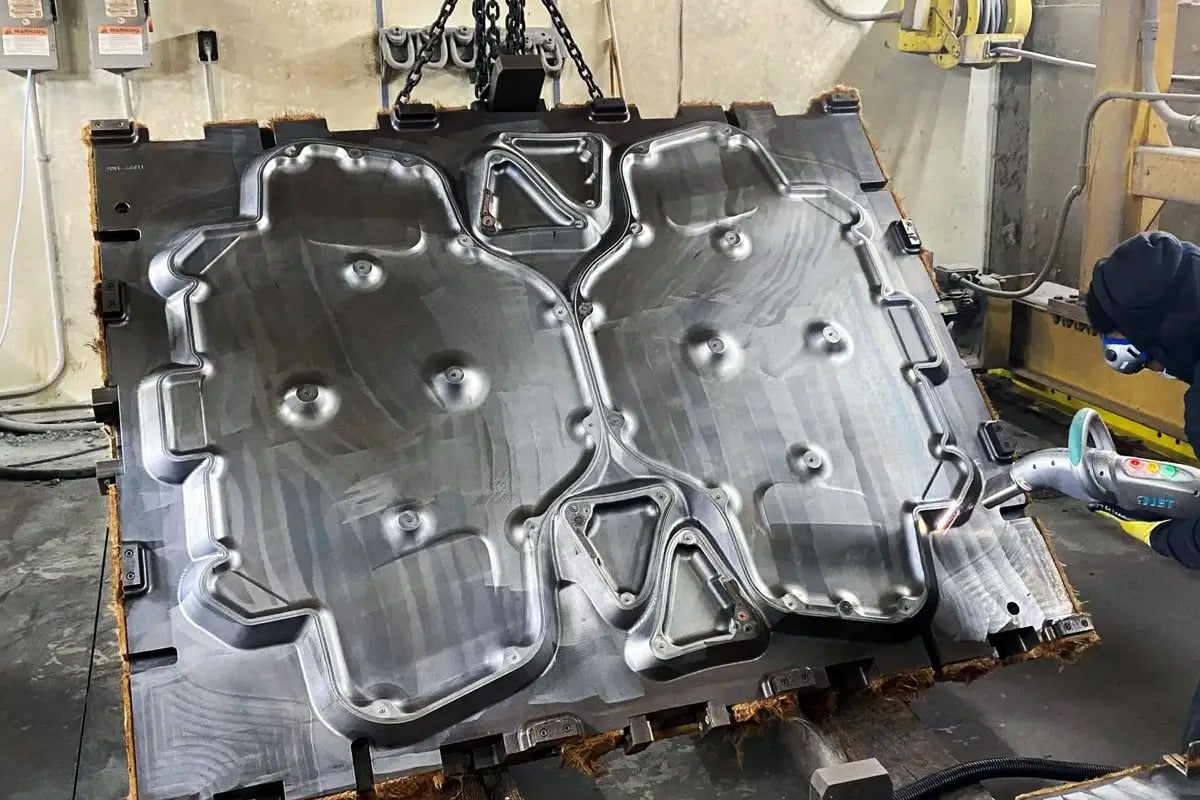
What Is Pulsed Laser Cleaning?
Pulse laser cleaning is an efficient surface cleaning method based on laser technology. It uses a short-pulse laser beam with high energy density to irradiate the target surface, so that pollutants, oxide layers, or coatings are evaporated or peeled off in a very short time. This process is achieved through the thermal effect of the laser, the photopressure effect, and the selective absorption of the laser by the material, thereby effectively removing dirt or unnecessary coatings on the target surface without causing mechanical wear or thermal damage to the substrate. Compared with traditional cleaning methods (such as chemical solvent cleaning and mechanical polishing), pulse laser cleaning has the advantages of non-contact and no consumables, and is particularly suitable for scenarios with high requirements for cleaning accuracy and material protection.
This technology has been widely used in many fields due to its versatility and environmental protection. For example, in industrial manufacturing, it can be used to remove residues on the surface of molds and oxide layers on welding parts; in the field of cultural relics protection, it can remove surface dirt without damaging cultural relics. With the continuous advancement of laser technology, pulse laser cleaning machines are gradually becoming a key solution in the cleaning industry, especially in the modern industrial and scientific research fields that pursue efficient, safe and green cleaning, showing great potential.
Table of Contents
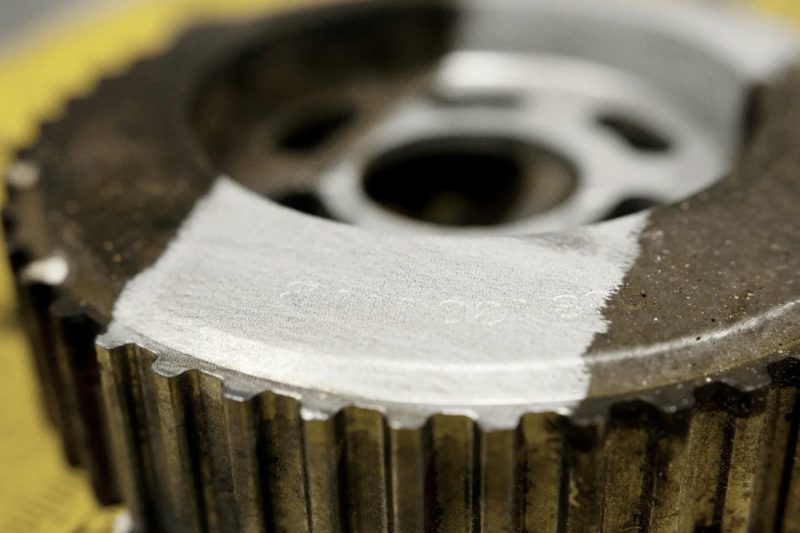
Advantages of Pulsed Laser Cleaning
Contactless Process
Pulsed laser cleaning uses a laser beam to transfer energy to the target surface without directly contacting the object being cleaned. This feature brings many benefits:
- Avoid mechanical damage: Traditional mechanical cleaning may wear or scratch the substrate, while laser cleaning completely avoids these problems.
- Suitable for complex geometries: The laser beam can penetrate deep into tiny areas such as micro-holes, slits, or curved surfaces, making it ideal for cleaning delicate workpieces.
- No consumables required: No consumables such as brushes and sandpaper are required, further reducing material loss during the cleaning process.
Precision and Control
Laser cleaning is known for its excellent accuracy and is especially suitable for scenes that require high substrate protection:
- Selective cleaning: Laser cleaning can be precisely positioned to remove only surface contaminants without damaging the underlying material. For example, when repairing artifacts, only the dirt or oxide layer on the surface is removed while retaining the original material.
- Micron-level control: Many high-end laser devices can achieve micron or even nanometer-level precision, which is used to clean precision parts in the aerospace industry, such as engine blades.
- Adjust power and frequency: Depending on the different materials and contaminants, the laser power and pulse frequency can be adjusted to achieve the best cleaning effect.
Environmental Friendly
As a green cleaning technology, pulsed laser cleaning has minimal impact on the environment:
- No chemicals: No chemical solvents are required, avoiding the pollution problems common in chemical cleaning processes, such as toxic waste liquids or corrosive chemical leaks.
- Low waste generation: Laser cleaning usually only produces a small amount of solid particles or gases, which are easy to collect and treat.
- Low energy consumption: The energy efficiency of modern laser equipment is gradually improving, which is suitable for low carbon emission requirements in large-scale industrial applications.
Versatility
The wide applicability of pulsed laser cleaning makes it the preferred cleaning method in many industries:
- Multiple material processing: It can clean a variety of substrates such as metals, ceramics, glass, composite materials, etc., which is suitable for the diverse needs of the manufacturing industry.
- Multiple types of pollutant removal: Including oxides, coatings, oil stains, rust and other surface attachments, especially suitable for large-area cleaning or removal of complex pollutant combinations.
- Flexible adaptability: The adjustability of laser parameters enables it to perform well in many fields from industrial production to cultural relics protection.
Efficiency and Speed
Pulse laser cleaning meets the high requirements of modern industrial production with its fast and efficient cleaning capabilities:
- Suitable for large-area processing: High-powerlaser cleaning equipment can clean large areas of rust or contaminants on metal surfaces in a few seconds, significantly improving production efficiency.
- Supports automation integration: Laser cleaning equipment can be easily integrated into existing automated production lines to achieve fully automatic cleaning without manual intervention.
- Reduce downtime: Compared with traditional cleaning methods, laser cleaning is fast and simple, which can minimize downtime for equipment maintenance and improve productivity.
Pulse laser cleaning has become one of the preferred technologies for modern industrial cleaning due to its advantages such as non-contact, high precision, environmental protection, and high efficiency. It not only performs well in removing complex pollutants but also meets cleaning tasks with high requirements for substrate protection. In the future, with the further development of technology, its application field and applicability will be more extensive.
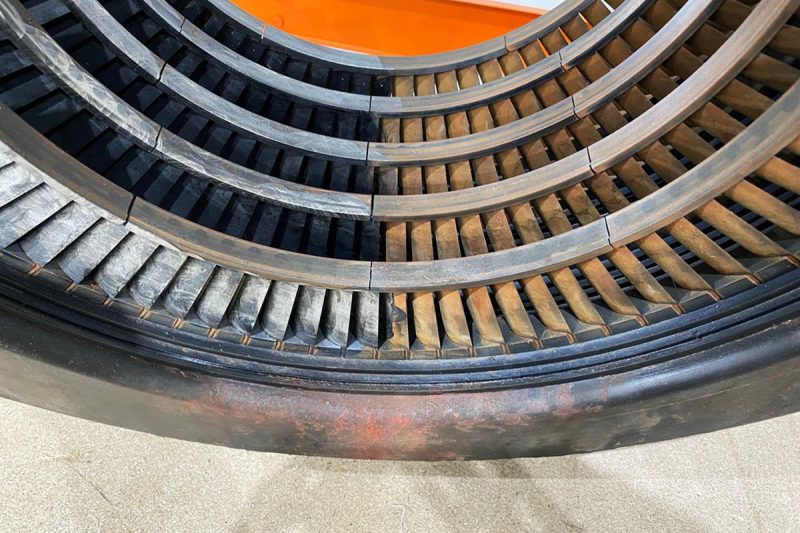
Challenges and Limitations of Pulsed Laser Cleaning
Although pulsed laser cleaning has won the favor of the industry with its excellent performance and wide applicability, it also faces some challenges and limitations in practical applications. The following is a detailed analysis:
High Initial Cost
The high cost of laser cleaning equipment is the primary obstacle faced by many companies, especially small and medium-sized enterprises:
- Equipment is expensive: The cost of laser cleaning equipment usually ranges from tens to hundreds of thousands of dollars, which is several times or more higher than traditional cleaning equipment (such as ultrasonic cleaning or chemical cleaning equipment).
- Additional costs: In addition to the equipment itself, maintenance costs, spare parts replacement and energy consumption are also factors to consider, which can put a strain on businesses with limited budgets.
- Long cost payback period: Although laser cleaning has significant advantages in terms of efficiency and environmental protection, the initial investment is high and it takes longer to recover the cost.
Training and Expertise
The high-end nature of pulse laser cleaning technology means that operators need certain professional skills:
- Professional training needs: Laser cleaning equipment requires operators to understand laser parameters (such as power, pulse frequency, scanning speed, etc.) and be able to optimize settings according to the cleaning task.
- Fault diagnosis ability: Once there is a problem with the equipment, the operator needs to have basic diagnosis and maintenance capabilities, otherwise it may cause prolonged equipment downtime.
- Technical support dependence: Many manufacturers of laser cleaning equipment are located in developed countries, and geographical restrictions on after-sales service and technical support may cause inconvenience.
Material Restrictions
Not all materials are suitable for pulsed laser cleaning:
- Materials with low thermal stability: For example, some plastics, rubbers or organic materials may melt, deform or crack due to thermal shock during laser cleaning.
- Coatings and composites: Some multi-layer coatings or composites may be difficult to control the cleaning depth during laser cleaning, resulting in damage to the base layer.
- Optical properties of the substrate: The light absorption rate of the material has a direct impact on the cleaning effect. For example, highly reflective metals (such as aluminum or copper) may require higher laser power to achieve the desired effect, thereby increasing costs.
Security Question
Pulse laser cleaning needs to be operated in a strict safety environment to avoid harm to the human body and the environment:
- Laser radiation risk: High-energy laser beams can cause irreversible damage to the eyes and skin, so professional laser protection equipment must be worn and a safe area must be set up.
- Fire hazard: When removing flammable materials (such as grease or organic contaminants), high-energy lasers may cause sparks or combustion, increasing the risk of fire.
- Waste disposal: Although pulsed laser cleaning produces less waste, the removed contaminants may form particles or smoke, which need to be managed through appropriate filtration and treatment devices.
Workaround
To address these challenges, many companies and research institutions are working to develop more economical, easy-to-use and safe laser cleaning solutions:
- Reduce equipment costs: Through technology optimization and production scale expansion, equipment manufacturing costs are gradually decreasing.
- Provide comprehensive training: Equipment suppliers usually provide operation and maintenance training to help companies quickly adapt to new technologies.
- Improve safety measures: Modern laser cleaning equipment is equipped with more safety features, such as automatic laser cut-off, real-time monitoring of the operating environment, etc., which further reduces operational risks.
The advantages of pulsed laser cleaning technology are obvious. Although there are some limitations, these problems are being gradually solved through the correct technology selection and appropriate measures, paving the way for its wider industrial application.
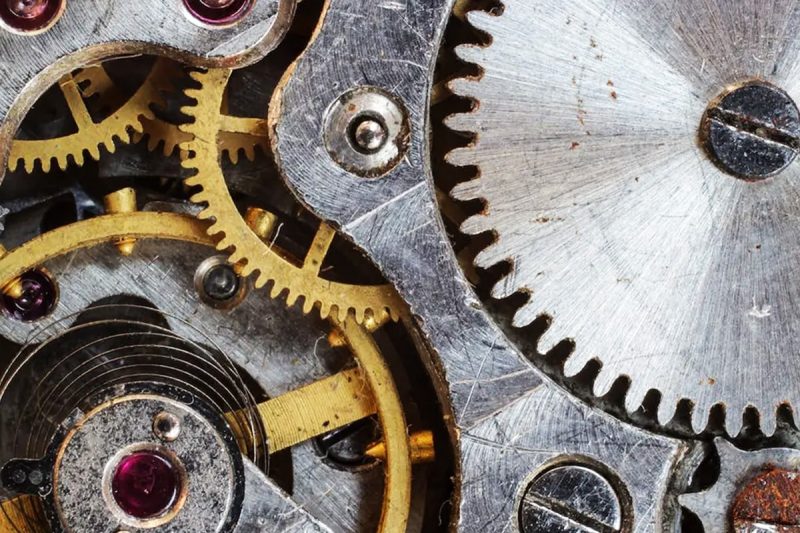
Applications of Pulsed Laser Cleaning
As an efficient, environmentally friendly and precise cleaning technology, pulse laser cleaning has been widely used in many industries. The following is an analysis of the specific applications and advantages of each industry:
Auto Industry
In automotive manufacturing, precise cleaning is critical to ensuring product performance, and pulsed laser cleaning technology provides an ideal solution for this:
- Pre-welding cleaning: used to remove oxides, coatings or contaminants from the welding area to ensure the strength and quality of the welded joint.
- Mold cleaning: Laser cleaning can effectively remove residues on the mold surface, such as oil, rubber residue or plastic components, extending the service life of the mold and maintaining surface accuracy.
- Parts cleaning: suitable for cleaning rust or dirt on engine parts, transmissions, and wheel assemblies.
Aerospace Industry
Aerospace has extremely strict requirements on material cleanliness and surface treatment. The high precision and non-contact characteristics of pulsed laser cleaning technology meet this demand:
- Cleaning of complex parts: such as turbine blades, composite parts, or aircraft structures, laser cleaning can deeply clean hard-to-reach surfaces without damaging the material.
- Surface preparation: Before spraying or coating parts, laser cleaning can effectively remove contaminants and improve the adhesion and durability of coatings.
- Oxide removal: Clean the oxide layer of aluminum alloy and titanium alloy parts to ensure that they meet the strict quality standards of the aviation industry.
Electronics Industry
The electronics industry requires high-precision and non-destructive cleaning methods. Pulsed laser cleaning technology excels in many aspects:
- Solder Residue Removal: Used to remove solder residue from circuit boards to ensure stable circuit performance.
- Microparticle Cleaning: Remove fine particles or contaminants in semiconductor manufacturing to prevent them from affecting chip performance and yield.
- Component Maintenance: Clean sensitive electronic components, such as fiber optic connectors or sensors, to ensure their efficient operation.
Cultural Heritage Protection
Laser cleaning has become an important tool in the field of cultural relics protection. Its non-contact and high selectivity are particularly prominent in protecting cultural relics:
- Dirt cleaning: remove dirt from stone sculptures, metal objects, or paintings to restore the original appearance of cultural relics.
- Corrosion layer removal: clean the rust layer on bronze or iron objects while retaining the original texture.
- Special surface treatment: used to clean the surface of fragile materials such as porcelain and glass without damaging their structure or pattern.
Power Generation Industry
The operational efficiency of power generation equipment relies on regular cleaning, and pulsed laser cleaning technology provides significant advantages in maintaining and extending equipment life:
- Turbine cleaning: Remove dirt and oxide layers from gas or water turbines to improve efficiency and reduce energy consumption.
- Heat exchanger cleaning: Efficiently remove scale deposits on the heat exchanger surface to ensure heat transfer efficiency.
- Pipeline maintenance: Clean corrosion or deposits inside the pipeline to avoid blockage or performance degradation.
Medical Device Manufacturing
The application of pulsed laser cleaning technology in medical device manufacturing and maintenance is mainly focused on precision cleaning and aseptic processing:
- Surface contamination cleaning: remove microorganisms, blood residues, or other contaminants on the instrument to ensure its sterility.
- High-precision instrument cleaning: suitable for cleaning surgical tools with complex geometries, such as endoscopes or minimally invasive instruments.
- Ensure surface integrity: maintain the surface finish and functional performance of medical devices during the cleaning process.
Food and Beverage Industry
The cleanliness of food processing equipment is directly related to food safety. Pulsed laser cleaning technology provides an environmentally friendly and efficient solution for this:
- Equipment cleaning: Remove grease, sugar stains, or processing residues from the surface of production equipment to ensure compliance with food hygiene standards.
- Mold maintenance: Clean residues on food-forming molds to extend mold life and ensure product quality.
- Pipeline cleaning: Remove sediments in storage and transportation pipelines to ensure a sterile environment.
Marine Industry
Corrosion and deposition in the marine environment have a significant impact on equipment performance. Pulsed laser cleaning provides an efficient means for cleaning and maintenance:
- Rust cleaning: Remove rust from ships and marine equipment to reduce maintenance costs.
- Biological fouling removal: Clean algae, shellfish, and other organisms attached to the bottom of the ship to reduce navigation resistance.
- Anti-corrosion preparation: Laser cleaning can effectively remove old coatings and dirt before repainting or anti-corrosion treatment.
Textile Industry
The textile industry has high requirements for the cleanliness of dyeing and processing equipment, and laser cleaning technology also shows unique advantages in this field:
- Removing dye residues: cleaning dye residues on fabrics or printing and dyeing equipment to improve product color fastness and quality.
- Cleaning processing pollution: removing grease, colloid, or other contaminants on the surface of fabric production equipment to ensure stable equipment operation.
- Non-destructive cleaning: cleaning high-end fabric materials to avoid damage that may be caused by traditional methods.
Pulse laser cleaning meets the complex cleaning needs in different fields with its versatility and high efficiency, and brings opportunities for sustainable development and technological upgrading to many industries.
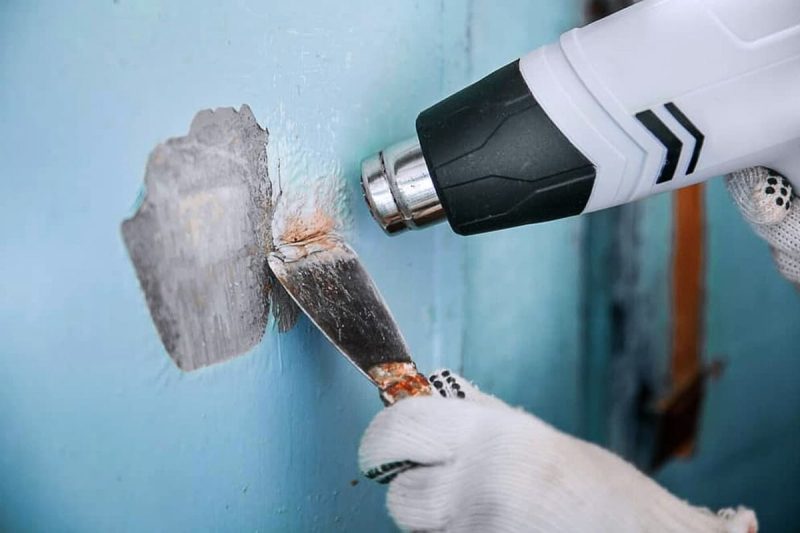
Pulsed Laser Cleaning Technology Considerations and Best Practices
To achieve the best cleaning effect in different application scenarios, pulsed laser cleaning technology needs to consider many factors and follow best practice guidelines. The following is a detailed analysis of the main considerations:
Choosing the Right Laser
Choosing the right laser type and wavelength is the basis of cleaning results. The absorption characteristics of different materials to the laser wavelength determine the cleaning efficiency and accuracy.
Laser Type Selection
- Ultraviolet laser (UV): Suitable for precision applications such as electronic components and semiconductor cleaning, because its low heat-affected zone and high absorption efficiency can effectively protect the substrate.
- Continuous laser and pulsed laser: More suitable for metal cleaning and large-area contaminant removal because of its strong penetration.
- Green laser: Used for transparent or translucent materials such as glass or ceramics, it has good adaptability.
The Importance of Wavelength Matching
- The optical properties of a material determine how efficiently it absorbs a particular wavelength. For example, metals absorb CW and pulsed lasers more strongly, while oxide layers respond better to UV wavelengths.
- By choosing a matching wavelength, thermal damage can be minimized and cleaning speeds can be increased.
Process Optimization
The success of pulsed laser cleaning relies on the optimization of the cleaning process parameters. It is crucial to adjust the settings according to the specific task.
Adjust Key Parameters
- Pulse frequency: High-frequency laser pulses are suitable for quickly removing thin layers of contamination, while low-frequency settings are better for removing thicker oxides or coatings.
- Power density: Too high a power density may damage the substrate, while too low a power density may make it difficult to completely remove contaminants. The optimal value is usually determined experimentally.
- Scan speed: Slower scan speeds can achieve more thorough cleaning, but too slow a speed may increase the risk of heat buildup.
- Focus position: Precisely adjust the focus position to ensure that the laser energy is concentrated in the target area and avoid energy dispersion.
Process Development and Validation
- Before actual cleaning, it is recommended to conduct small-scale experiments to verify the suitability of cleaning parameters for the target material and contaminants.
- Use simulation software to predict the interaction between the laser and the material and optimize parameter settings.
Maintenance and Quality Control
The reliability of laser equipment and the stability of cleaning quality directly affect operational efficiency. Regular maintenance and quality monitoring are the key to ensuring performance.
Laser Equipment Maintenance
- Optical component cleaning: The laser head and lens should be kept clean to prevent beam scattering or power loss.
- System calibration: Regularly calibrate the laser equipment to ensure that the laser output power and wavelength are accurate.
- Cooling system check: Keep the equipment cooling system running well to prevent the high-power laser generator from overheating and causing failure.
Quality Control of Cleaning Results
- Inspection tools: Use optical microscopy or scanning electron microscopy to check the cleaned surface to confirm that contaminants are completely removed.
- Standard testing: Use non-destructive testing (NDT) methods, such as optical reflectivity measurement, to evaluate the surface performance after cleaning.
- Consistency monitoring: In large-scale cleaning tasks, use automated quality monitoring systems to monitor cleaning results in real-time to avoid deviations.
The potential of pulsed laser cleaning technology can be maximized by properly selecting the laser type, optimizing process parameters, and implementing effective equipment maintenance and quality control. This not only ensures that the cleaning task is completed efficiently but also extends the equipment life and improves the overall economic benefits, providing reliable support for a wide range of industrial applications.
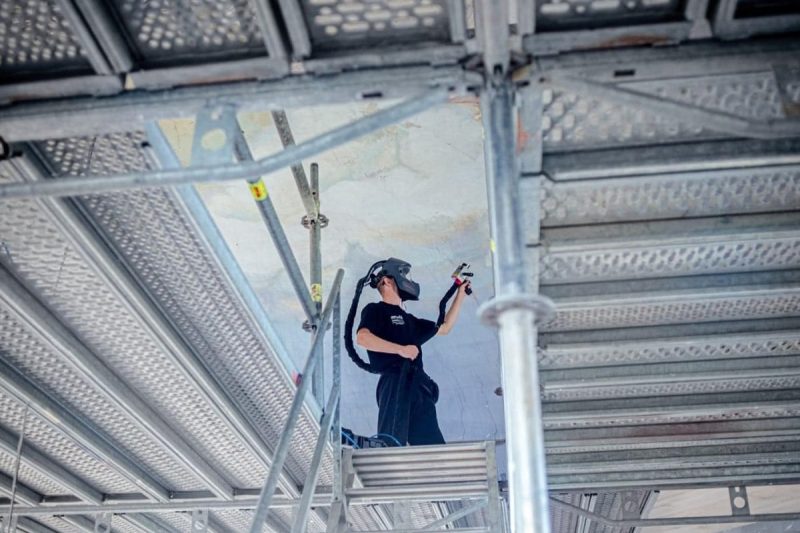
Summarize
Pulse laser cleaning technology is a revolutionary and innovative technology. With its non-contact operation, high-precision control capabilities, and environmental advantages, it has shown great application potential in many industries. From the automotive industry to aerospace, electronic manufacturing, and other fields, pulse laser cleaning has become an important means of removing pollutants, oxide layers, and coatings. Compared with traditional cleaning methods, it not only avoids mechanical damage and chemical pollution, but also can efficiently and accurately remove pollutants, reduce damage to the substrate, and show its unique value in high-demand fields. AccTek Laser has accumulated rich experience in the field of laser technology and is committed to providing high-performance laser cleaning equipment to help customers improve production efficiency and product quality.
However, pulsed laser cleaning also faces some challenges, especially the high initial investment in equipment and high operational complexity requirements, which may require some small and medium-sized enterprises to consider additional costs when adopting it. As laser technology continues to develop, we believe that the cost of pulsed laser cleaning will gradually decrease, making this technology acceptable to more industries. We will continue to promote technological innovation and improve equipment performance to meet the market demand for efficient and green cleaning solutions. In the future, pulsed laser cleaning is expected to be applied in a wider range of fields, providing a more efficient and environmentally friendly cleaning method for all walks of life.
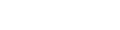
Contact information
- [email protected]
- [email protected]
- +86-19963414011
- No. 3 Zone A, Lunzhen Industrial Zone,Yucheng City , Shandong Province.
Get Laser Solutions