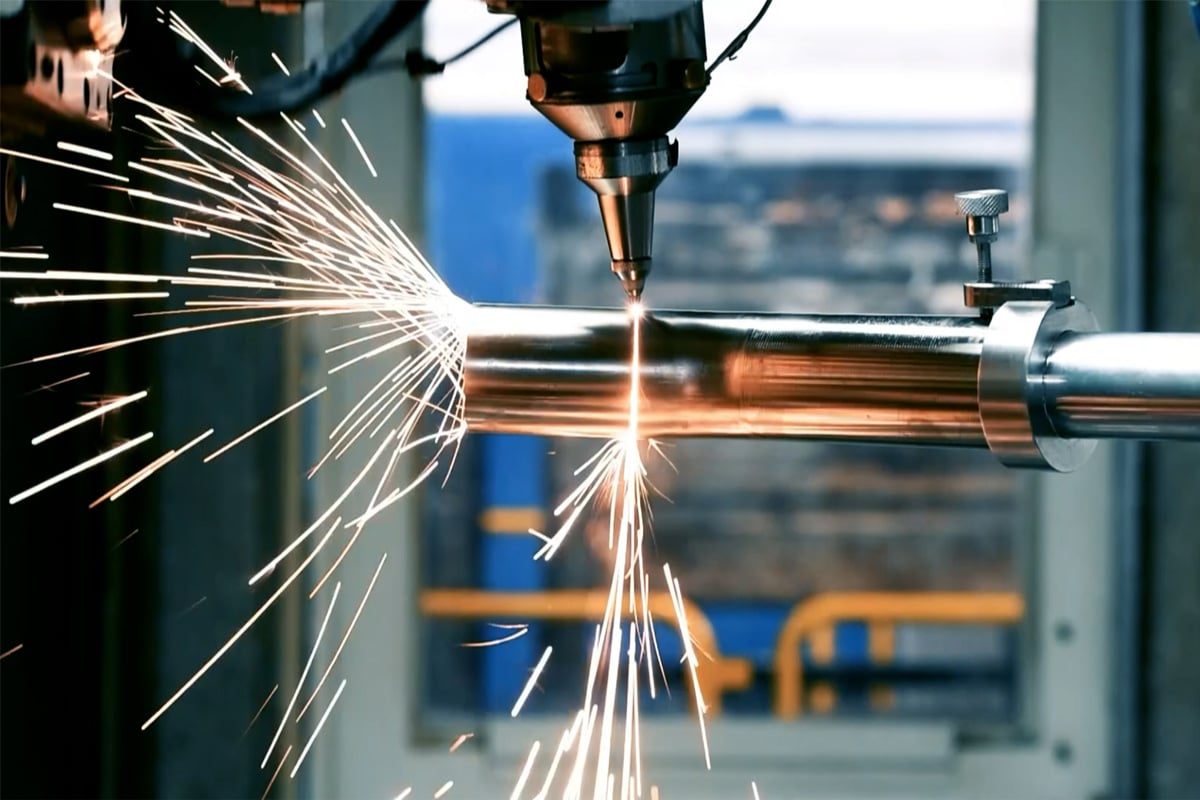
What Is the Difference Between CW and Pulsed Fiber Laser Generators?
The fiber laser generator was invented in 1963. By the end of the 1980s, the first batch of commercial fiber laser generators were available, after more than 20 years of development. Fiber laser generators are regarded as an amplifier for ultra-high-speed optical communications. Fiber laser generators have a simple structure, low cost, high electro-optical conversion efficiency, and good output effect, and their share in the industrial laser industry has increased year by year. There are two main types of fiber laser generators according to the output laser characteristics, namely continuous fiber laser generators and pulsed fiber laser generators. There are some differences in principles, technical characteristics, and applications between pulsed fiber laser generators and continuous fiber laser generators, and each is suitable for different occasions. This article mainly discusses the differences between the two fiber laser generators in various aspects, so as to determine which type of laser generator is suitable for different industries.
Table of Contents
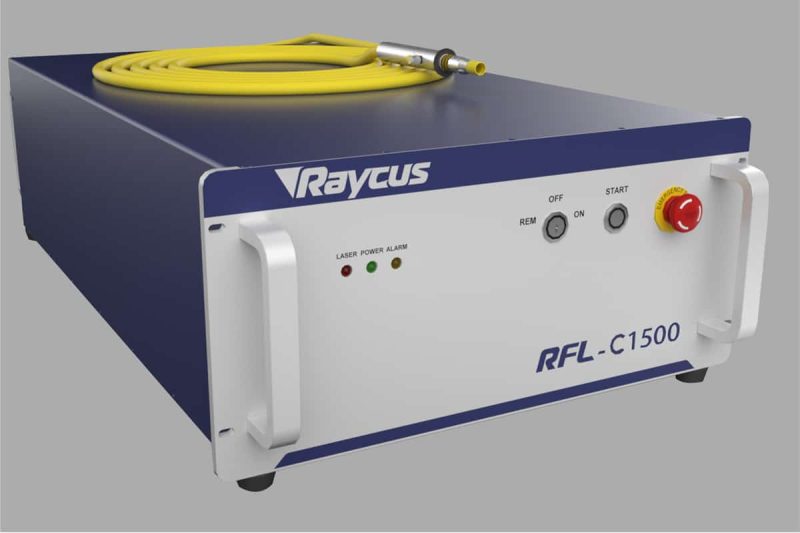
Fiber Laser Generator
To explore the difference between continuous fiber laser generators and pulsed fiber laser generators, we first need to roughly know the working principle of the fiber laser generator, what components a complete fiber laser generator includes, and what the function of each component is.
Working Principle of Fiber Laser Generator
The fiber laser generator uses glass fiber doped with rare earth elements as the gain medium. The pump source is coupled into the gain medium through an appropriate optical system. The pump light forms a high power density in the fiber core, causing a “population inversion” of the doped ion energy levels. When a positive feedback loop is properly introduced (forming a resonant cavity), laser oscillation output is generated.
Components of a Fiber Laser Generator
Like traditional solid-state and gas laser generators. Fiber laser generators are basically composed of three basic elements: pump source, gain medium, and resonant cavity, but the type of gain medium is different.
- Gain medium: The gain medium is an optical fiber doped with rare earth ions, which amplifies light through the process of population inversion and stimulated radiation. Acting as a medium for population inversion determines the performance of laser radiation.
- Pump source: The pump source provides energy to the gain medium to achieve population inversion (energy source for population inversion), thereby making laser operation possible.
- Resonant cavity: The resonant cavity consists of two mirrors to reflect light, increase the path length of light in the gain medium, and thus enhance light amplification. Provide feedback mechanism for laser amplification to select the spectral and spatial characteristics of light.
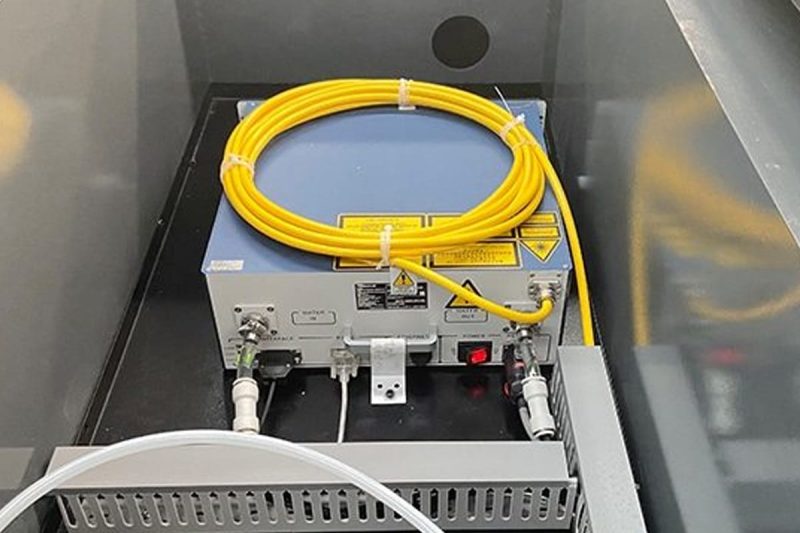
CW Fiber Laser Generator
Definition
The continuous fiber laser generator outputs a continuous laser beam, and the power is maintained at a relatively stable level. This feature makes the continuous fiber laser generator advantageous in situations where long-term, stable energy output is required.
Working Principle
The working principle of a continuous laser generator is based on the process of stimulated radiation. In the laser medium, some atoms or molecules are transitioned to a high energy level through the input of external energy. These high-energy atoms or molecules will be stimulated by the outside world and then transition to a higher energy level in the stimulated radiation field. In this process, the atoms or molecules generated by the laser medium will interact with the photons of the stimulated radiation field to generate radiated laser photons. These laser photons will be reflected in the resonant cavity, generating stimulated radiation to other atoms or molecules, thereby amplifying the laser signal and finally forming a continuous laser output.
Features and Benefits
- High stability: The continuous fiber laser generator can work stably for a long time, ensuring that the laser output during the production process is not disturbed. This stability makes it excel in applications that require long-term uninterrupted operation, such as large-scale manufacturing and automated production lines.
- High power density: The continuous fiber laser generator can provide a laser beam with high energy density, making it suitable for processing applications with high energy requirements. Its high power density is particularly suitable for processes such as cutting and welding of thick materials, which can effectively improve the processing effect and quality.
- Fast processing speed: The continuous fiber laser generator can quickly heat and melt materials due to the continuity and high power density of the laser beam. This high processing speed greatly improves production efficiency and is particularly suitable for high-volume production environments that require fast processing.
- High processing efficiency: The continuous fiber laser generator can maintain efficient processing performance during the production process, which is suitable for large-scale, high-efficiency production and processing tasks. Its high power output and stable laser quality help to improve overall production efficiency and processing accuracy and reduce production costs.
Application
- Large equipment processing, such as vehicle and ship machinery, cutting of large steel plates, and other processing occasions that are not sensitive to thermal effects but are more sensitive to cost.
- Widely used in optical fiber communication systems for signal transmission and amplification, with high stability and low phase noise.
- In the field of scientific research, it is used for applications such as spectral analysis, atomic physics experiments and laser radar, and can provide high-power and high-beam quality laser output.
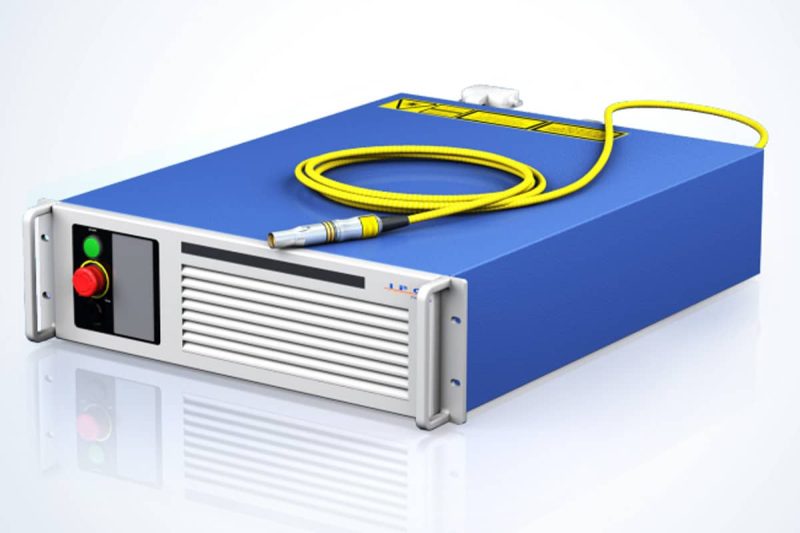
Pulsed Fiber Laser Generator
Definition
The laser of a pulsed laser generator is “intermittent”. Of course, the intermittent time is often very short, usually measured in milliseconds, microseconds, or even nanoseconds and picoseconds. Compared with continuous lasers, the intensity of pulsed lasers is constantly changing, so there are concepts of “peaks” and “troughs”.
Working Principle
The main components of a pulsed laser generator include a pump source, a fiber amplifier, and a modulator. First, the pump source injects strong laser light into the optical fiber. The rare earth atoms in the optical fiber absorb the energy of photons, causing the electrons to transition to high energy levels and return to the ground state under stimulated radiation, generating a primary radiation with the same frequency as the pump light. Then, after amplification of the fiber length, the light gradually becomes stronger. Finally, the modulator sends out a driving pulse, compressing the photons to a certain extent to form a short pulse. A pulsed laser generator compresses continuous laser light into a very short time to output it, obtaining a high-energy output. The cost of obtaining a high-energy output from a continuous laser would be very high, and pulsed lasers solve this problem very well.
Features and Benefits
- High peak power: Pulsed lasers have high peak power and can release a lot of energy in a short time. This makes pulsed lasers have important applications in fields such as material processing, laser drilling and laser cutting.
- Narrow spectral width: The spectral width of pulsed lasers is usually narrow, making them highly coherent. This gives pulsed lasers advantages in fields such as optical communications and optical storage, enabling high-speed and high-capacity data transmission.
- Phase stability: Pulsed lasers have good phase stability, which is very important for some applications that require coherence and precise time control, such as spectral analysis and interferometry.
- Short pulse width: The pulse width of pulsed lasers is usually very short, reaching picoseconds, femtoseconds or even attoseconds. Short pulse width makes pulsed lasers have important applications in fields such as ultrafast optics, bioimaging and precision measurement.
Application
- Pulsed laser plays an important role in scientific research, especially in the field of ultrafast optics. It can be used to study the dynamic process of matter, molecular vibration, electron motion and chemical reaction, etc.
- Pulsed laser is widely used in medical imaging and treatment. For example, femtosecond laser can be used in corneal correction surgery, while picosecond laser can be used for skin spot removal and tattoo removal, etc.
- Pulsed laser plays an important role in the field of optical communication and information technology. It can realize applications such as high-speed fiber-optic communication, optical storage and lidar.
- Pulsed laser is widely used in industrial manufacturing. Applications such as laser cutting, laser welding and laser marking require high peak power and precisely controlled laser pulses.
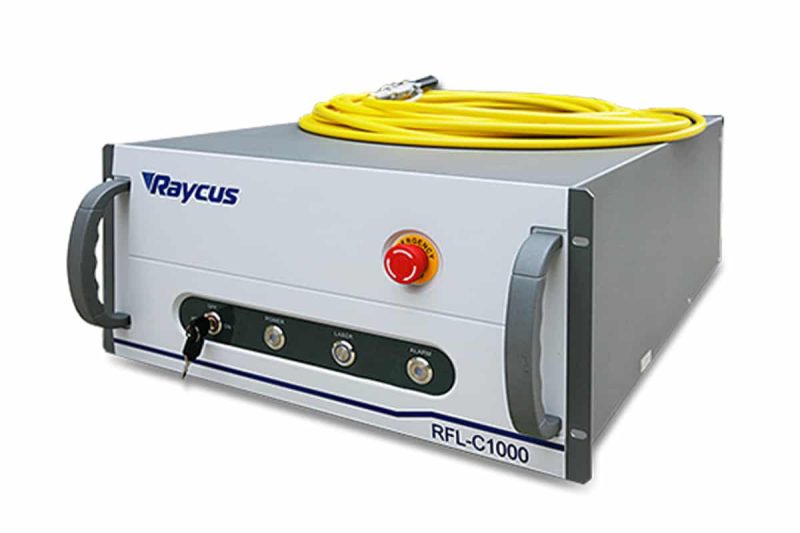
Comparison of CW and Pulsed Fiber Laser Generators
After discussing the essential differences between the two fiber laser generators, we continue to compare the differences between the two laser generators in real-world applications, discussing power output, cutting, welding and cleaning capabilities, heat-affected zones, material compatibility, cost considerations, and more.
Power Output
- The pump source of the continuous fiber laser generator continuously provides energy without interruption, and the output power remains unchanged. The output power of the continuous laser is generally low, which is suitable for occasions that require continuous laser operation.
- The pulsed fiber laser generator compresses the energy of the laser into a very narrow time for output, so it has a larger laser output power than the continuous laser, which is suitable for processing occasions that require high power and deep penetration in a short time.
Cutting, Welding and Cleaning Capabilities
- Cutting: Continuous fiber laser cutting machines suitable for fast and large-scale cutting; pulse laser is suitable for high-precision and small-size cutting.
- Welding: Both can be used for welding. Continuous fiber laser welding machineis more suitable for processing materials with higher thickness. The welding efficiency is better than that of pulse laser welding machine, but pulse laser has more advantages in precision welding and micro welding.
- Cleaning: Pulse laser cleaning machinehas high precision and needs to strictly control the temperature rise of the substrate. For application scenarios that require no damage to the substrate, such as molds, pulse lasers should be selected. For some large steel structures, pipelines, etc., due to their large size and fast heat dissipation, the requirements for substrate damage are not high, so continuous laser cleaning machine can be selected.
Heat Affected Zone
- Pulse laser has a small heat-affected zone on the material and small deformation, which is suitable for small precision equipment.
- Continuous laser outputs high power uninterruptedly and releases a large amount of heat energy in a short time. It is suitable for processing large equipment that is not sensitive to thermal effects, and the speed is faster than pulse laser.
Material Compatibility
Material Compatibility of CW Fiber Laser Generators
Continuous fiber laser generators are widely used in the processing of various materials due to their stable laser output and high power density. Its material compatibility mainly includes:
- Metallic materials: Continuous fiber laser generators can efficiently cut, weld and punch metals. This includes common metals such as steel, aluminum, copper, titanium, silver, etc. Its high power density enables the laser beam to quickly penetrate the metal surface for precise and efficient processing.
- Non-metallic materials: In addition to metal materials, continuous fiber laser generators are also suitable for processing some non-metallic materials such as plastics, ceramics and glass. Under the action of the laser beam, these materials can be processed into the desired shape and size by melting, evaporation or chemical reaction.
Material Compatibility of Pulsed Fiber Laser Generators
Pulse fiber laser generators are characterized by their short pulse width and high peak power, and they also perform well in the field of material processing. Their material compatibility is mainly reflected in the following aspects:
- Precision processing materials: Pulse fiber laser generators are particularly suitable for materials with high processing precision requirements. Their short pulse width enables the laser beam to reach extremely high energy density in a very short time, thereby achieving micro-processing and precision marking of materials.
- High reflectivity materials: For high reflectivity materials such as copper and aluminum, the processing effect of continuous fiber lasers may be limited to a certain extent. Pulse fiber laser generators can effectively overcome the reflection problem of materials through their high peak power and short pulse width, and achieve precise processing of these materials.
- Heat-sensitive materials: The short pulse action time of the pulse fiber laser generator makes the material less affected by heat during the processing process, so it is particularly suitable for heat-sensitive materials. These materials are prone to deformation or cracking during processing, and the low heat impact characteristics of the pulse fiber laser generator can effectively avoid these problems.
Both continuous fiber laser generators and pulsed fiber laser generators excel in material compatibility, but each has different advantages and scope of application. Continuous fiber laser generators are suitable for situations that require long-term stable processing and high power density, and can process a variety of metal and non-metal materials. Pulsed fiber laser generators are characterized by their short pulse width and high peak power, and are particularly suitable for situations that require high processing accuracy and thermal effects, such as precision processing, high reflectivity material processing, and heat-sensitive material processing. When selecting a fiber laser generator, it is necessary to comprehensively consider the specific processing requirements and material properties.
Cost Considerations
- Continuous laser generators are usually low-cost and have price advantages, suitable for processing in large-scale production sites.
- Pulse laser generators are relatively expensive due to their high technical complexity, and are suitable for high-precision, high-value-added processing.
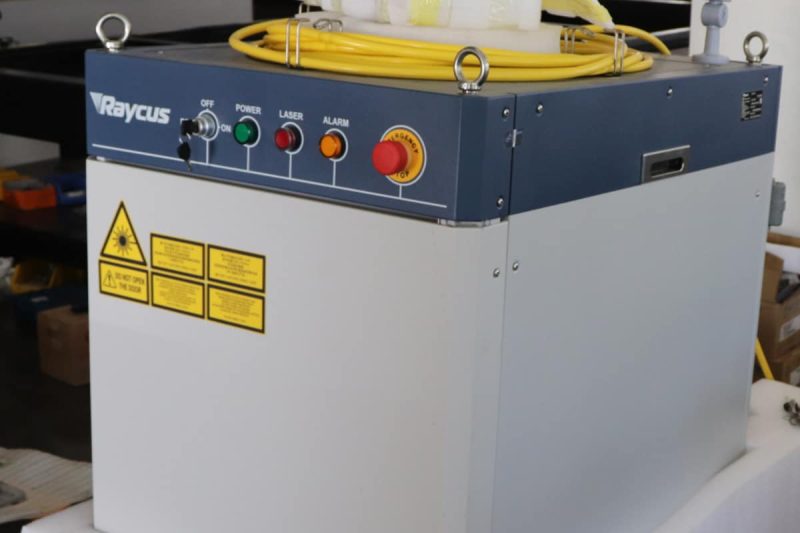
Factors That Influence Your Choice
Through the above comparison, we have a general understanding of what type of laser generator to choose. In addition, we should also consider factors that affect our choice, such as: application requirements; speed, accuracy and material compatibility; budget considerations; initial investment and operating costs; future scalability and versatility requirements.
Application Requirements
- Processing tasks: clarify the type of processing tasks to be performed, such as cutting, welding, marking, drilling, etc. Different tasks have different requirements for the type, power and performance of the laser generator.
- Processing materials: understand the type, thickness, hardness, thermal conductivity and other characteristics of the material to be processed, because these factors will directly affect the selection of the laser generator.
- Processing quality: whether there are special requirements for the smoothness of the processing edge, the size of the heat-affected zone, and the accuracy.
Speed, Precision and Material Compatibility
- Processing speed: Evaluate the required processing speed according to production needs to determine whether the laser generator can meet the requirements of efficient production.
- Processing accuracy: For applications that require high-precision processing, such as precision manufacturing, microelectronics processing, etc., a laser generator that can provide higher precision processing should be selected.
- Material compatibility: As mentioned earlier, different laser generators have different compatibility with materials. Make sure that the selected laser generator can handle the target material and consider the diversity of materials and possible future changes.
Budget Considerations
- Initial investment: Evaluate the budget for purchasing the laser generator, including the equipment cost, the cost of supporting equipment (such as cooling system, control system), etc.
- Operating cost: Consider the long-term operating costs of the laser generator, such as energy consumption, maintenance cost, and consumables cost.
- Return on investment: Analyze the expected benefits and cost recovery cycle after investing in the laser generator to evaluate the economic feasibility of the investment.
Initial Investment and Operating Costs
- Equipment cost: The prices of laser generators of different types, brands and configurations vary greatly, and the choice needs to be based on budget and performance requirements.
- Operating costs: including power consumption, cooling system costs, maintenance costs and possible consumable costs, etc. These costs can have a significant impact on overall economics over the long term.
Future Scalability and Versatility Requirements
- Technology upgrade: Consider whether the laser generator supports future technology upgrades and expansion functions to adapt to changing processing needs.
- Versatility: Selecting a laser generator with multiple processing modes and functions can improve the flexibility and utilization of the equipment and meet diverse production needs.
- Scalability: Evaluate whether the laser generator is easy to integrate with other equipment and systems, and whether it supports future expansion and upgrades of the production line.
In summary, when choosing a continuous fiber laser generator or a pulsed fiber laser generator, you need to fully consider application requirements, speed, accuracy and material compatibility, budget considerations, and future scalability and versatility requirements. By comprehensively weighing these factors, you can choose the laser generator device that best suits your needs.
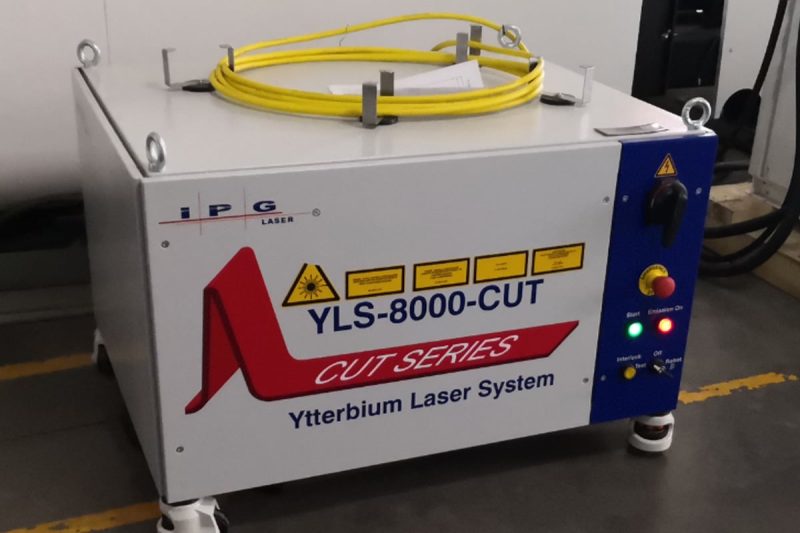
Summarize
When choosing a fiber laser generator, it is critical to understand the differences between continuous and pulsed fiber laser generators. Both have their own characteristics and advantages, and are suitable for different application scenarios and needs.
- With its stable laser output and high power density, the continuous fiber laser generator is suitable for occasions that require long-term continuous operation and large-scale processing. It can provide high-power, high-processing efficiency laser output and is suitable for metal cutting, welding and optical fiber communication systems. In addition, because its laser output is continuous, the cost is low, making it suitable for large equipment and economical production applications that are not sensitive to thermal effects.
- Pulsed fiber laser generators, with their high peak power and short pulse width, perform well in high-precision processing, micro-processing of materials and processing of heat-sensitive materials. It can release a large amount of energy in a very short time, giving it significant advantages in ultrafast optics, medical imaging, precision manufacturing and other fields. Although its technical complexity is high and its cost is relatively high, the high peak power and precise control it provides make it particularly important in high value-added applications.
In practical applications, the choice of fiber laser generator depends on many factors, including application requirements, processing speed, precision, material compatibility, and budget considerations. Continuous fiber laser generators are suitable for large-scale processing tasks that require continuous and stable laser output, and are cost-effective. Pulsed fiber laser generators are suitable for precision processing tasks that require high precision, short pulses, and high peak power, especially when processing high reflectivity and heat-sensitive materials. By comprehensively evaluating factors such as application requirements, speed, precision, material properties, and budget, flexible selection and comprehensive consideration of these factors will help optimize the production process, improve production efficiency, and achieve the best economic benefits.
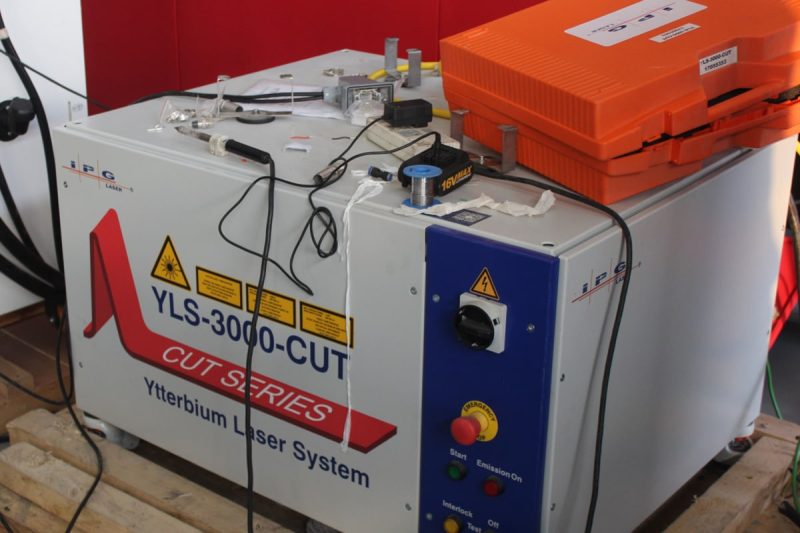
Get Laser Solutions
Choosing the right fiber laser generator can help optimize power consumption and achieve high operational efficiency. Working with a trusted supplier ensures access to advanced technology, tailored advice and ongoing support. At AccTek Laser, we offer a comprehensive range of laser machine equipment designed to meet a variety of industrial needs. Our experts can help you choose the most energy-efficient model and configuration, taking into account factors such as material type, thickness and production volume. We also offer cutting-edge features such as high-efficiency laser generators, intelligent cooling systems and energy management software to maximize performance and minimize energy use. In addition, our team provides regular maintenance services and technical support to keep your equipment at peak efficiency. By partnering with AccTek Laser, you can achieve significant energy savings, reduce operating costs and enhance your sustainability efforts. Contact us today to learn more about our innovative laser solutions and how they can benefit your business.
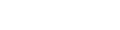
Contact information
- [email protected]
- [email protected]
- +86-19963414011
- No. 3 Zone A, Lunzhen Industrial Zone,Yucheng City , Shandong Province.
Get Laser Solutions