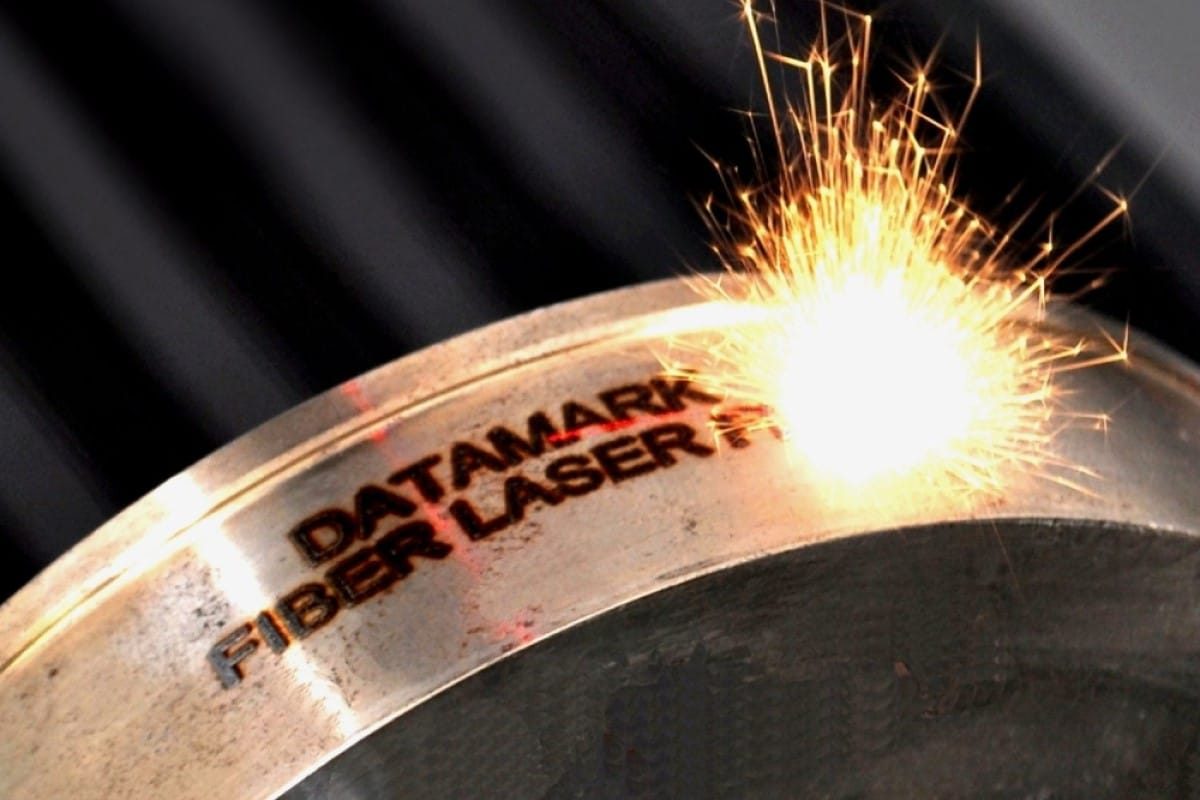
What is The Marking Speed of The Laser Marking Machine?
Laser marking machines have become indispensable tools in the ever-evolving modern manufacturing industry, providing unparalleled precision and versatility. The core of its operating efficiency lies in one key parameter: marking speed. Marking speed refers to how quickly a laser marking machine can create complex engravings, barcodes, and identifiers on various materials. Understanding this parameter helps optimize production, improve quality, and meet stringent industry demands.
In this comprehensive exploration, we delve into the complexities of laser marking speed, revealing what it means and the many factors that influence it. From material properties to laser parameters and system dynamics, we journey to decipher the complexities that impact marking speed. As we explore this space, manufacturers will gain insights into the art and science of balancing speed and precision, ultimately unlocking the full potential of laser marking technology in contemporary manufacturing.
Table of Contents
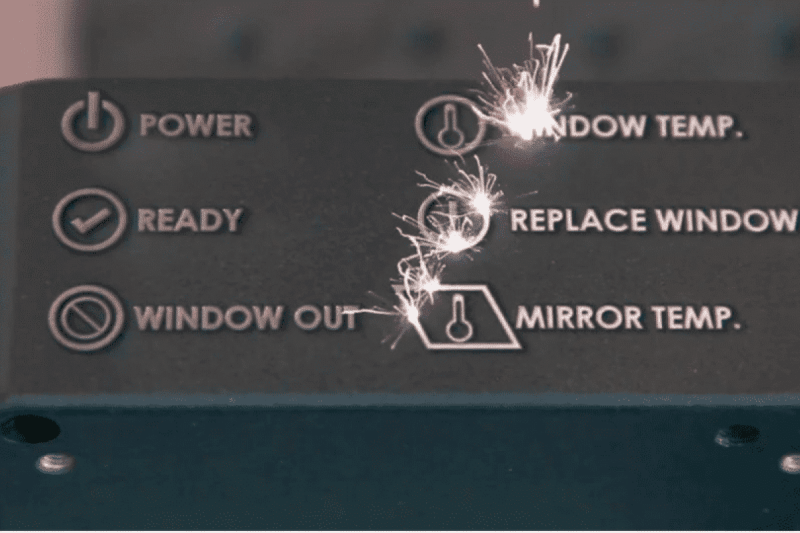
Marking speed definition
In the field of laser marking machines, marking speed is a key metric, which reflects the rate at which the laser beam interacts with the material surface to create complex and precise marks. This basic parameter is quantified in millimeters per second (mm/s) or inches per second (in/s) and represents the linear velocity of the laser beam through the material during the marking process.
In essence, marking speed is a dynamic factor that affects the efficiency and productivity of laser marking operations. It depicts the balance between performing markup quickly and maintaining optimal quality. Manufacturers strategically deploy marking speeds to achieve required throughput levels while ensuring durability and clarity of marks on different materials.
Marking speed is more than just a number, it reflects the fusion of technical prowess and materials science, embodying the ability of a laser marking machine to etch, engrave, or serialize a range of materials with unparalleled precision and speed. Understanding the nuances of marking speed can help realize the full potential of laser marking technology in a variety of industrial applications.
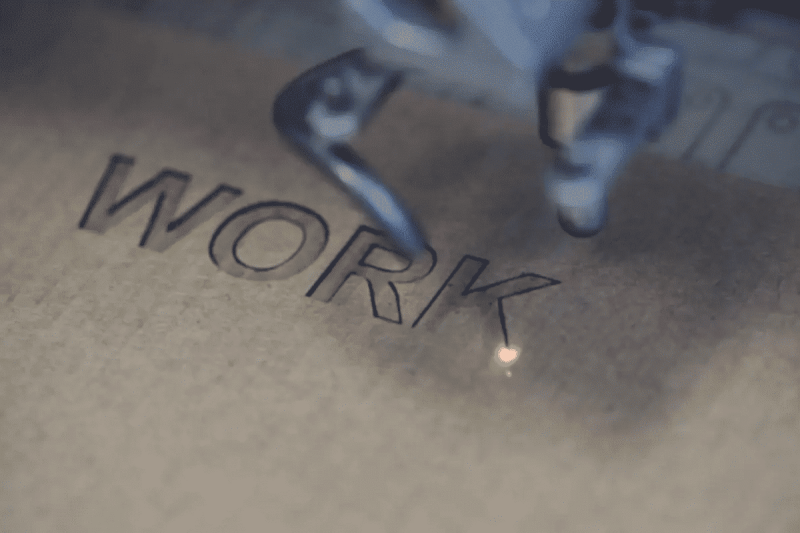
The importance of marking speed
The marking speed of laser marking machines goes beyond mere numerical indicators and is a key determinant that profoundly affects all aspects of manufacturing. Understanding the importance of marking speed is critical for manufacturers looking to optimize their production processes, ensure output quality, and remain competitive in a dynamic market.
- Throughput And Efficiency: Marking speed is directly related to throughput, which defines how quickly a product can be marked within a given time frame. Higher marking speeds mean greater productivity, giving manufacturers the flexibility to meet demand and reduce lead times.
- Cost-Effectiveness: Time is money in manufacturing. Faster marking speeds mean lower production costs per part because manufacturers can complete more work in a given amount of time. This cost efficiency is especially important in high-volume production environments, where even small improvements in marking speed can lead to significant savings.
- Adapt To Market Needs: In today’s fast-paced market, agility is crucial. Laser marking machines with adjustable marking speeds enable manufacturers to quickly adapt to changing market demands, changing production plans, and changing customer requirements. This flexibility ensures that businesses can remain responsive and competitive in dynamic market conditions.
- Quality Assurance: While speed is crucial, it cannot be at the expense of quality. Optimal marking speed ensures marks are accurate, clear, and consistent on a variety of materials and surface finishes. Maintaining high-quality standards helps meet regulatory requirements, ensure product traceability, and enhance brand reputation.
- Process Optimization: Marking speed is the benchmark for evaluating the efficiency of the laser marking process. By analyzing and optimizing marking speed, manufacturers can identify opportunities for process improvement, equipment optimization, and workflow simplification. This iterative approach fosters continuous improvement and drives operational excellence.
- Competitive Advantage: In a highly competitive market, every advantage is important. Laser marking machines have faster marking speeds, allowing manufacturers to surpass competitors, seize market opportunities, and provide customers with quality products. By leveraging cutting-edge technology and optimizing marking speed, businesses can stand out and gain a competitive advantage.
In essence, marking speed is not just a technical parameter, it is a strategic enabler that enables manufacturers to achieve higher productivity, lower costs, maintain quality standards, optimize processes, and operate in today’s fast-paced world. Gain a competitive advantage in manufacturing environments. By prioritizing and optimizing marking speed, companies can take their laser marking operations to new levels of efficiency, agility, and profitability.
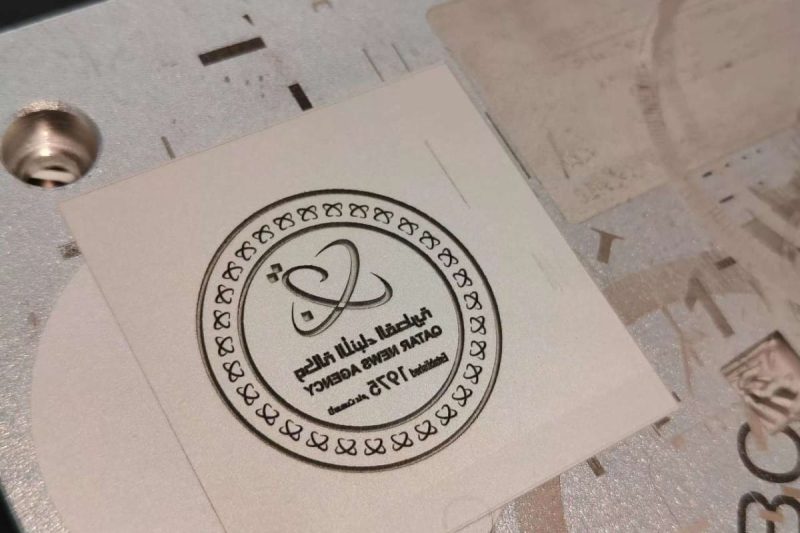
Factors affecting marking speed
The marking speed of a laser marking machine is affected by many factors, including material properties, laser parameters, optical system properties, environmental conditions, motion control, and system integration. Understanding these factors can help optimize marking speed and achieve desired results in laser marking applications.
Material type
- Impact: Different materials react differently to laser marking. Hard and dense materials may require slower marking speeds to ensure proper absorption of laser energy, while softer materials may be able to withstand higher speeds.
- Note: The composition, conductivity, and hardness of the material play a key role. Manufacturers must adjust marking speed based on the material to be marked to achieve the desired quality and depth.
Laser power
- Impact: The power of the laser generator directly affects the marking speed. Higher laser power generally results in faster marking speeds, but the relationship is not linear.
- Note: Balancing power with material type is critical. Manufacturers need to optimize power settings to achieve the desired marking results without compromising quality.
Focal length and spot size
- Impact: The focal length and spot size of the laser beam determine the energy concentration on the material surface. Smaller spot sizes and shorter focal lengths enable higher energy density, resulting in faster marking speeds.
- Note: Proper calibration of the optical system, including adjustments to spot size and focal length, helps optimize marking speed while maintaining accuracy.
Marking depth requirements
- Impact: Applications requiring deeper marks may require slower marking speeds to ensure adequate laser penetration and sufficient mark depth.
- Note: Manufacturers must align marking speed with the specific depth requirements of the application, striking a balance between speed and desired marking depth.
Laser wavelength
- Impact: Different wavelengths interact with materials in different ways, affecting absorbance. Selecting the appropriate laser wavelength can optimize marking speed.
- Note: Matching the laser wavelength to material properties can improve efficiency. Understanding how different wavelengths interact with specific materials allows you to make informed choices in optimizing marking speed.
Scan head speed and accuracy
- Impact: The speed and accuracy of the scan head responsible for guiding the laser beam are critical. The high-speed, precise scan head helps improve overall marking efficiency.
- Note: Regular calibration and maintenance of the scan head is necessary to ensure optimal performance. High accuracy of beam positioning enables faster and more reliable marking.
Environmental conditions
- Impact: Environmental factors such as temperature and humidity will affect the efficiency of the laser marking machine. Extreme conditions may require adjustment of marking speed.
- Note: It is vital to maintain stable environmental conditions in the workplace. Monitor and adjust marking speed based on environmental changes to ensure consistent and reliable performance.
Motion control and system integration
- Impact: Different wavelengths interact with materials in different ways, affecting absorbance. Selecting the appropriate laser wavelength can optimize marking speed.
- Note: Matching the laser wavelength to material properties can improve efficiency. Understanding how different wavelengths interact with specific materials allows you to make informed choices in optimizing marking speed.
Pre- and post-processing steps
- Impact: Activities before and after the actual marking, such as surface cleaning, coating removal, or post-marking processing, can affect marking speed.
- Note: Optimized pre-processing steps ensure a clean and suitable surface for marking, while efficient post-processing facilitates the overall workflow. Adjusting the marking speed to accommodate these steps helps achieve a seamless process.
To sum up, the marking speed of a laser marking machine is affected by many factors, including material characteristics, laser parameters, optical system characteristics, environmental conditions, motion control system integration, etc. By understanding and optimizing these factors, manufacturers can achieve efficient, precise laser marking in a variety of materials and applications, thereby increasing productivity, quality, and competitiveness in modern manufacturing environments.
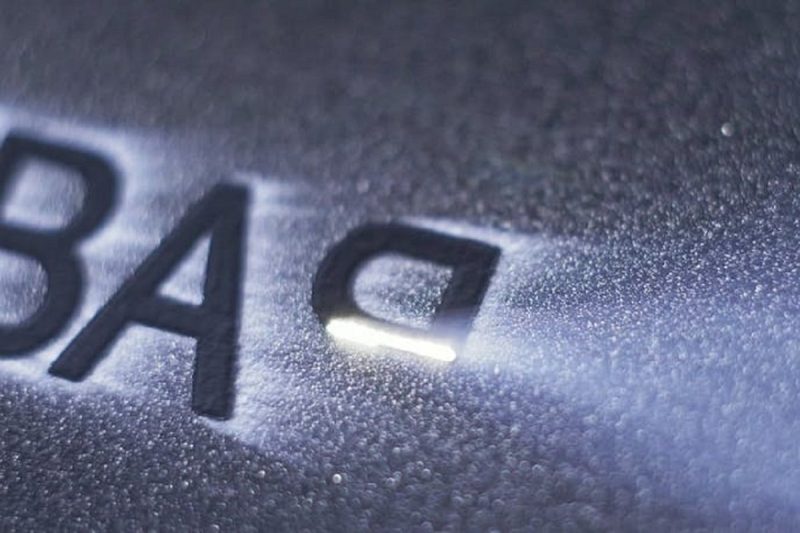
Marking speed optimization strategy
Optimizing marking speed is a multifaceted endeavor that requires careful consideration of a variety of factors, including material properties, laser parameters, system dynamics, and operating conditions. By implementing targeted optimization strategies, manufacturers can increase marking efficiency, productivity, and quality to maximize the capabilities of their laser marking machines. The following are key optimization strategies for achieving optimal marking speed:
Material selection and preparation
Choose materials that have properties that facilitate efficient laser marking, such as appropriate thermal conductivity, surface reflectivity, and absorptive properties. Prioritize materials that enable higher marking speeds without compromising quality. Additionally, ensure proper surface preparation, including cleaning, degreasing, and surface preparation, to optimize energy absorption and adhesion to promote faster marking speeds.
Laser parameter optimization
Conduct a comprehensive parameter optimization study to determine the best laser settings for specific materials and marking requirements. Adjust laser power, pulse frequency, pulse duration, and wavelength to achieve desired mark depth, contrast, and speed. Fine-tune parameters through experimentation and process trials to maximize marking efficiency while maintaining quality and consistency.
Optical system calibration
Regularly calibrate and maintain the optical components of your laser marking system, including lenses, mirrors, and beam delivery systems. Ensure precise beam positioning, focus, and alignment to minimize energy loss and aberrations to maximize marking efficiency. Regularly inspect and clean optics to prevent contamination and degradation, maintain beam quality, and control optimal marking speed.
Scan head optimization
Optimize scan head performance by calibrating speed, acceleration, and deceleration to minimize dwell time and maximize movement speed. Using a high-speed, high-precision scanning head, fast and accurate beam positioning can be achieved. Implement advanced motion control algorithms and feedback systems to enhance scan head performance and minimize system inertia, vibration, and mechanical errors.
Process integration and automation
Integrate laser marking systems with automated workflows and manufacturing processes to streamline operations and maximize efficiency. Automated material handling, part positioning, and laser parameter control reduce setup time and minimize manual intervention, resulting in faster marking and higher throughput. Implement a real-time monitoring and feedback system to adaptively control and optimize marking speed based on dynamic process conditions.
Adaptive control and dynamic optimization
Implement adaptive control algorithms and dynamic optimization strategies to adjust marking speed in real-time based on material properties, surface conditions, and environmental factors. Leverage sensor feedback, machine learning algorithms, and predictive analytics to optimize marking parameters and adapt to changing process conditions. Continuously monitor and analyze process data to identify improvement opportunities and refine optimization strategies accordingly.
Environmental control and stability
Maintain optimal environmental conditions within the marking environment to ensure the stability and reliability of laser marking operations. Control temperature, humidity, and air quality to minimize changes that can affect laser performance and material properties. Stable environmental conditions help maintain consistent marking speed and quality, improving overall process efficiency.
Training and skills development
A comprehensive training and skills development program is provided for operators and technicians to ensure proficient operation and maintenance of laser marking systems. Equip personnel with the knowledge and expertise to solve problems, perform routine maintenance tasks, and optimize marking parameters for maximum efficiency and quality. Continuous training and skills development enable employees to drive process improvements and innovation, thereby increasing overall productivity and competitiveness.
Process optimization and workflow management
Analyze and optimize the entire laser marking process, including material handling, part positioning, and data management, to eliminate bottlenecks and inefficiencies. Simplify workflow management with efficient scheduling, resource allocation, and production planning to maximize utilization and throughput. Implement lean manufacturing principles and continuous improvement practices to identify and eliminate waste to further optimize marking speed and efficiency.
In summary, optimizing the marking speed of a laser marking machine requires a comprehensive approach including material selection, parameter optimization, system calibration, process integration, and continuous improvement. By implementing targeted optimization strategies and leveraging cutting-edge technologies, manufacturers can unleash the full potential of laser marking technology to achieve unparalleled efficiency, productivity, and quality in industrial marking applications.
Summarize
In short, the marking speed of the laser marking machine is a key parameter that significantly affects the efficiency, quality, and productivity of marking operations in various industries. Marking speed, measured in millimeters per second (mm/s) or inches per second (in/s), determines the rate at which complex engravings, barcodes, and identifiers can be created on different materials. Several factors, including material type, laser power, focal length, marking depth requirements, laser wavelength, scan head speed, and environmental conditions, intricately affect marking speed. By understanding these factors and implementing optimization strategies such as material selection, laser parameter optimization, system calibration, and process integration, manufacturers can increase marking speed, throughput, and quality. Leveraging advanced technology and continuous improvement practices, manufacturers can unleash the full potential of laser marking machines and drive innovation and excellence in modern manufacturing processes while meeting the dynamic demands of the market.
Getting A Laser Marking Solution
Embarking on a journey to integrate laser marking solutions into your manufacturing processes? Unlock the potential of precision and efficiency by partnering with experts in laser technology. At AccTek Laser, we specialize in providing tailored laser marking solutions to meet your unique requirements.
Our team of seasoned professionals is ready to guide you through the process, ensuring a seamless integration of laser marking technology into your production line. Whether you are in the automotive, electronics, medical, or aerospace industry, we understand the specific demands of your sector.
To get started, simply reach out to us through [email protected] or give us a call at +8619963414011. Share your project details, material specifications, and production needs, and our experts will provide you with a comprehensive quote, outlining the optimal marking speed and customized solutions tailored to elevate your manufacturing capabilities. Let’s embark on a journey towards precision, efficiency, and innovation together.
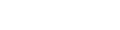
Contact information
- [email protected]
- [email protected]
- +86-19963414011
- No. 3 Zone A, Lunzhen Industrial Zone,Yucheng City , Shandong Province.
Get Laser Solutions