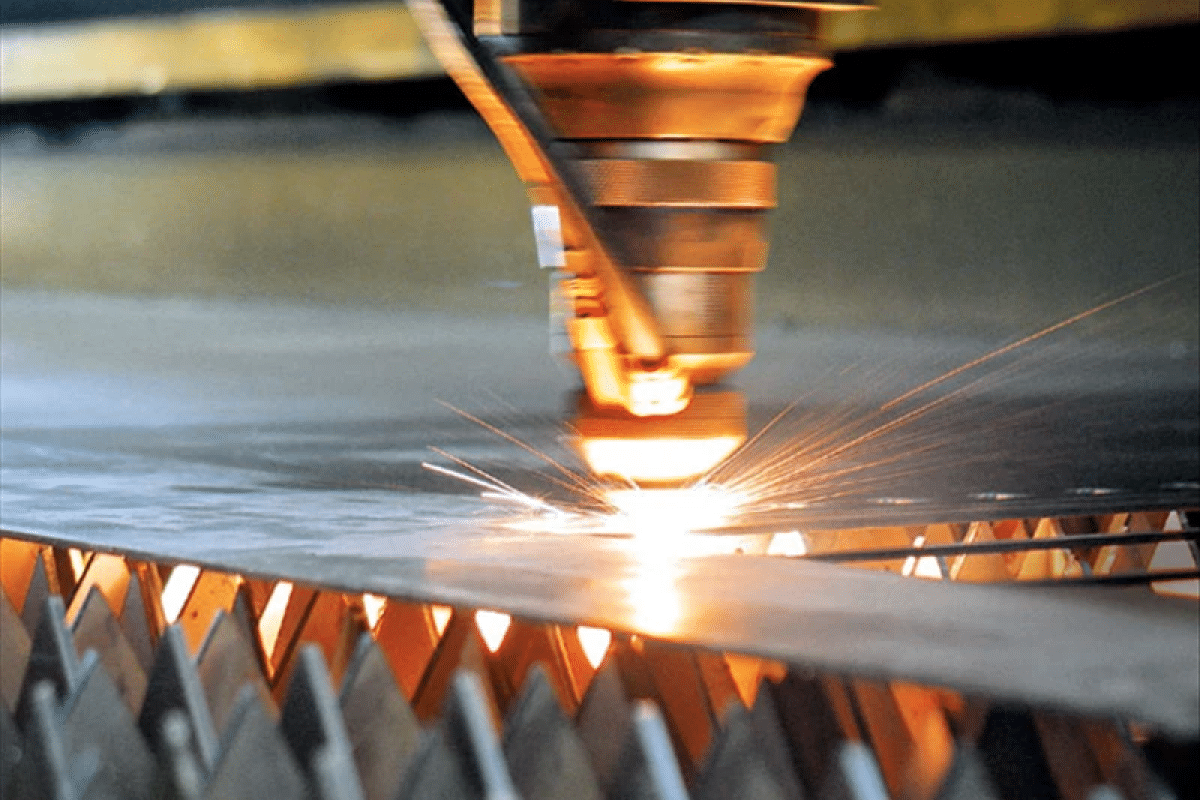
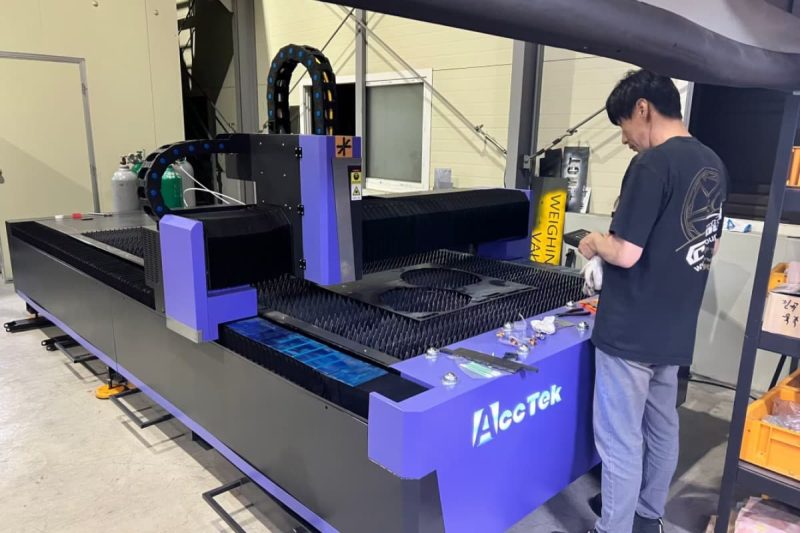
What materials cannot be cut by laser cutting machines?
Highly reflective material
The laser cutting machine will produce a high-energy laser beam when working, and highly reflective materials such as copper, silver, aluminum, etc. will reflect most of the laser energy, resulting in poor cutting results or even damage to the cutting machine itself. This is because the absorption rate of laser energy by highly reflective materials is very low and cannot be cut in a short time. Instead, it will cause reflection and scattering on the surface of the material, further weakening the cutting effect. There are some ways we can overcome these problems:
- Auxiliary gas purge: Introducing auxiliary gas, such as nitrogen or oxygen, during cutting can move the reflected laser energy away from the cutting area and improve cutting efficiency.
- Change the wavelength: Selecting a laser light source with an appropriate wavelength can reduce the reflectivity of the laser on highly reflective materials. For example, infrared lasers absorb copper and aluminum better than visible light lasers, thereby improving cutting results.
- Coating treatment: Coating high-reflective materials can reduce their reflectivity and increase the absorption rate of laser energy on the material. This method can improve cutting results in some cases.
- Choose appropriate power and parameters: According to different highly reflective materials, adjust parameters such as laser power, pulse frequency, and scanning speed to obtain the best cutting effect.
Transparent material
Toxic materials
Certain toxic materials such as fluoride and cyanide may produce toxic gases or harmful dust during the laser cutting process, causing serious harm to operators and the environment. Therefore, to protect the health and safety of workers, laser-cutting machines should not be used to cut such toxic materials. Here are some common coping strategies:
- Ventilation facilities: Set up an effective ventilation system in the cutting area to quickly discharge the generated harmful gases outdoors and carry out environmental protection treatment.
- Use absorbent: Place absorbent in the cutting area to absorb toxic gases and reduce gas diffusion.
- Cryogenic cutting: Reduce the temperature during cutting and reduce the amount of organic matter released by gasification.
- Choose alternative materials: Choose materials that do not contain organic solvents to reduce the generation of toxic gases during laser cutting.
Stone
Although laser cutting machines are widely used on metal and non-metallic materials, the effect of laser cutting machines is not ideal for hard and high mineral content materials, such as marble, granite, sandstone, and other stones. This is because stone has a high thermal conductivity and it is difficult for the laser energy to concentrate on the cutting area in a short time, making cutting difficult and prone to cracks and uneven cutting surfaces. Here are some possible solutions:
- Cutting parameter optimization: For different stone materials, the parameters of the laser cutting machine can be adjusted, such as power, speed, focus depth, etc., to achieve better cutting results. By continuously optimizing parameters, the difficulty of cutting stones can be overcome to a certain extent.
- Auxiliary processing methods: For stones that are difficult to cut with a laser, other processing methods can be considered, such as mechanical cutting, water jet cutting, etc. These methods can better cope with the special properties of stone and achieve precise cutting.
- Material pretreatment: Before laser cutting, the stone can be pretreated, such as preheating, pre-segmentation, etc., to reduce energy loss during cutting and improve cutting efficiency and quality.
- Material selection: During the project planning stage, appropriate materials can be selected based on the characteristics of the stone to avoid using stones that are not suitable for laser cutting, thereby reducing the occurrence of cutting problems.
High-density polyethylene
High-density polyethylene easily produces adhesive gas during laser cutting, which causes an increase in attachments on the cutting surface and affects the cutting quality. In addition, HDPE also produces toxic gases during the cutting process, posing a threat to the environment and operators. Here’s an explanation of how to resolve these issues.
To reduce the production of sticky gas:
- Optimize cutting parameters: Adjust parameters such as laser power, scanning speed, and focal length to reduce heat accumulation in the cutting area, thereby reducing the generation of adhesive gas.
- Auxiliary gas purge: During the cutting process, the introduction of auxiliary gas (such as nitrogen) can help to quickly blow away the generated gas and reduce its retention in the cutting area.
To avoid the release of toxic gases:
- Ventilation facilities: Set up forced ventilation equipment in the cutting area to discharge the toxic gases generated promptly. Use a gas treatment system to filter and process the discharged gases to reduce the gas concentration.
- Personal protective measures: Operators should wear appropriate protective equipment, such as respirators, protective glasses, etc., to reduce exposure to toxic gases.
Reactive Materials
Multilayer composites
Multilayer composite materials are usually made of layers of different materials, such as carbon fiber-reinforced composites. Due to the different thermal conductivity and optical properties of different materials, the laser is prone to produce unstable cutting effects during the cutting process, which may lead to peeling, cracks, and other problems. But there are still ways to deal with these limitations:
- Cutting parameter optimization: Adjust the parameters of the laser cutting machine, such as laser power, scanning speed, etc., to adapt to the characteristics of different material layers. Through reasonable parameter settings, the cutting effect can be improved to a certain extent.
- Use of auxiliary gas: Using appropriate auxiliary gas, such as nitrogen, oxygen, etc., can play a role in cooling and purging during the cutting process, reducing heat conduction between material layers, and thereby improving the cutting effect.
- Laser source selection: For multi-layer composite materials, a laser source of a specific wavelength can be selected to enhance the absorption capacity of a certain material for better cutting.
- Pretreatment process: Before cutting, other methods can be used for pretreatment, such as mechanical processing, heat treatment, etc., to reduce the difference between material layers and thereby improve the effect of laser cutting.
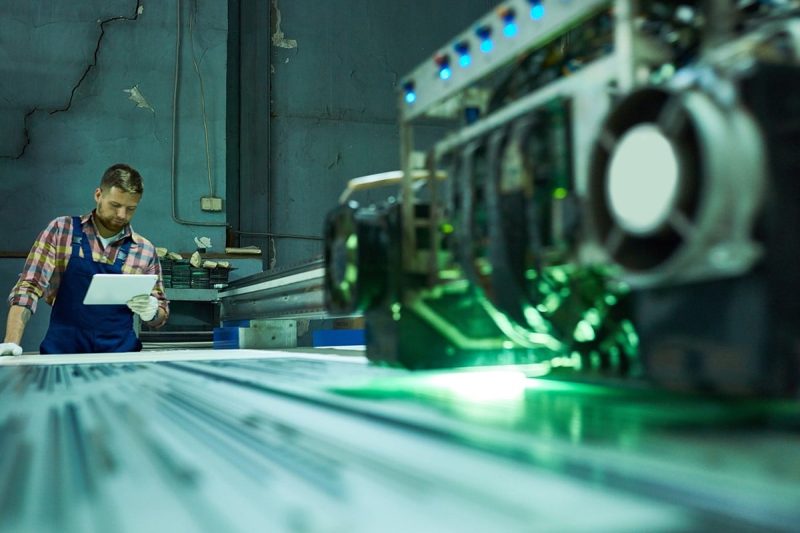
Safety precautions with laser cutting
Material Compatibility
- verify whether the material being cut is compatible with the laser cutting process. Some materials can emit toxic fumes or react unpredictably when laser cut, so be aware of the specific hazards associated with the materials you use.
- understand the limitations of laser cutting machines in terms of material thickness and type.
Personal Protective Equipment (PPE)
- Always wear laser safety glasses designed for the specific wavelength of the laser being used. These glasses effectively protect the eyes from potential laser beam exposure.
- Avoid wearing loose or flammable clothing to avoid fire hazards. Consider wearing appropriate protective clothing (including long sleeves and pants) to protect skin from potential laser reflections or sparks.
- wearing closed-toed shoes can protect your feet from falling objects or potential hazards.
Training and Certification
- Ensure that operators using laser cutting machines are adequately trained and certified to operate the equipment safely. Training should cover not only the operation of the machine but also safety protocols and emergency procedures.
Ventilation and smoke extraction
- The workplace should maintain adequate ventilation to eliminate smoke and gas generated during the laser-cutting process. Use an exhaust system to direct smoke away from the work area. Follow local ventilation and emission control regulations and guidelines.
- ensure regular maintenance of exhaust systems and filters to prevent the build-up of potentially harmful particles.
Maintenance and inspection
- regularly inspect the laser cutting machine for any signs of wear, damage, or malfunction. Address any maintenance or repair issues promptly to prevent accidents.
- Keep the laser cutting machine clean and remove any debris or material that may have accumulated in the work area.
Machine safety features
- I understand where the emergency stop button is on the machine and how to use it. Ensure all operators are trained for emergency use.
- The mark laser cutting areas and machines with warning signs and labels to indicate potential hazards and required safety measures.
Emergency procedures
- Establish clear emergency procedures and ensure all operators are familiar with them. This should include measures to be taken in the event of a fire, machine failure, or personal injury.
- Establish clear emergency procedures and escape routes.
- lPost emergency contact information and procedures in a prominent location.
Summarize
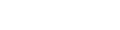
- [email protected]
- [email protected]
- +86-19963414011
- No. 3 Zone A, Lunzhen Industrial Zone,Yucheng City , Shandong Province.