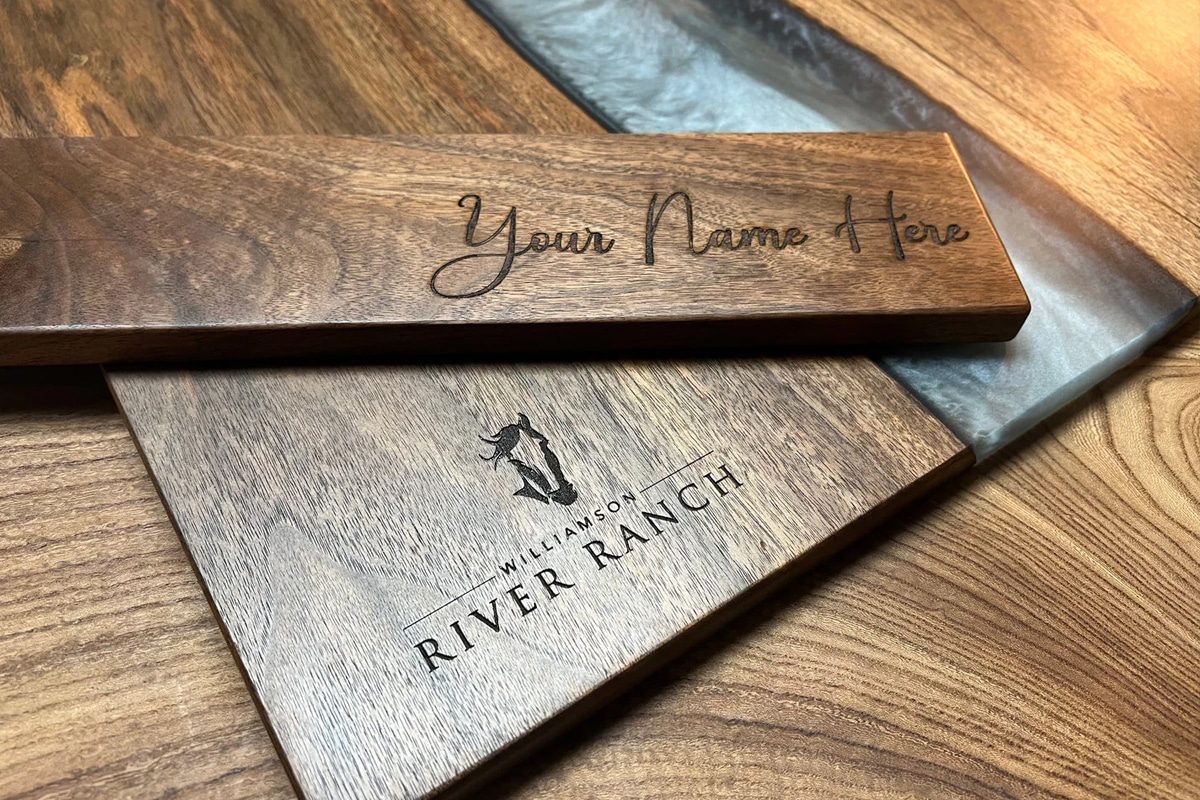
What Safety Precautions Should Be Taken When Laser Marking?
Laser marking is an indispensable technology in modern manufacturing and manufacturing, revolutionizing the way product surfaces are labeled and branded. Its versatility spans a variety of materials, including metals, plastics, ceramics, and glass, making it the first choice in a variety of industries including automotive, electronics, aerospace, and medical devices. Despite its widespread adoption and undeniable advantages, laser marking also presents some potential risks that require strict safety measures. Ensuring personnel safety, protecting equipment integrity, and preventing environmental hazards are top considerations in any laser marking operation.
In this comprehensive guide, every stage of the process, from initial setup to routine maintenance, requires meticulous attention to security details. For the safe and effective execution of laser marking tasks, we have conducted in-depth research on the importance of a series of safety precautions and measures to help companies better operate laser marking safely.
Table of Contents
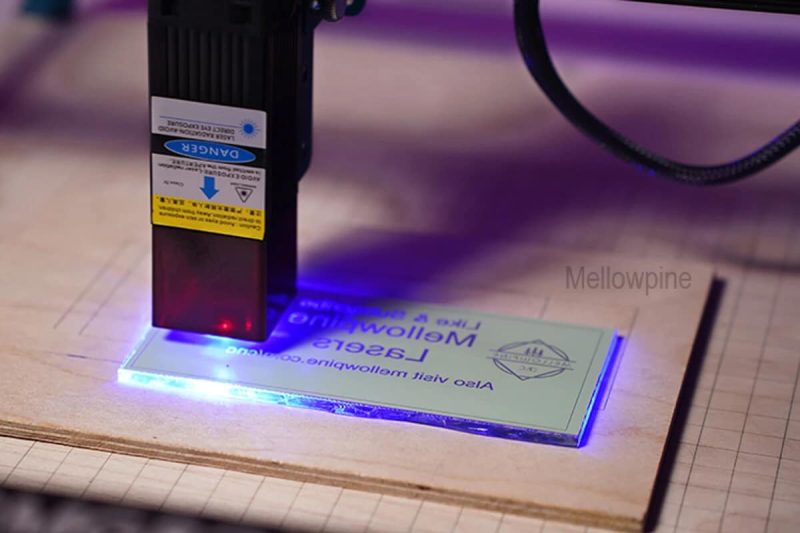
Basic Principles Of Laser Marking
Laser marking offers unparalleled capabilities in labeling, branding, and traceability. The core principle of laser marking is to use a highly focused laser beam to change the surface properties of a material, thereby creating permanent marks with superior clarity and durability. The process involves directing a laser beam onto the surface of the material, where it interacts with the substrate to produce the desired mark.
There are several types of laser marking methods, each suited for specific materials, applications, and desired outcomes.
- Engraving: Engraving involves removing material from the surface to create a mark. This method is particularly useful for metals and harder materials, where the laser beam vaporizes the surface layer to leave a deep, permanent mark.
- Ablation: Ablation, also known as surface removal marking, entails vaporizing a thin layer of material from the surface, leaving a contrasting mark. It is commonly used for plastics, ceramics, and certain metals, offering precise and high-contrast marking without affecting the material’s integrity.
- Annealing: Annealing relies on localized heating to alter the material’s properties, often resulting in color changes without surface damage. This method is well-suited for metals and alloys, allowing for subtle, aesthetically pleasing marks while preserving the material’s structural integrity.
- Foaming: Foaming involves creating a frosted or raised mark by inducing controlled heat to expand and foam the material’s surface. This method is ideal for plastics, providing a tactile and visually distinct mark without compromising the material’s integrity.
- Coloration: Coloration utilizes chemical additives or surface treatments to induce color changes in the material upon exposure to the laser beam. This method is commonly employed for plastics and certain metals, offering customizable and durable color markings for branding and identification purposes.
Each of these laser marking methods offers unique advantages in terms of mark quality, speed, and compatibility with different materials. By understanding the principles and applications of these methods, manufacturers can leverage laser marking technology to enhance product identification, traceability, and aesthetic appeal across various industries.
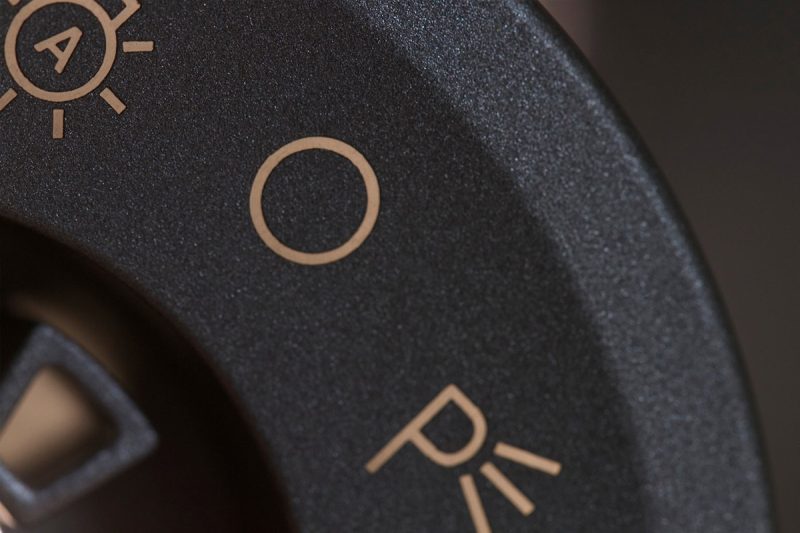
Potential Hazards Associated With Laser Marking
While laser marking offers numerous advantages in terms of accuracy and efficiency, it also presents potential hazards that must be carefully managed to ensure the safety of people, equipment, and the environment. Understanding these hazards enables effective implementation of appropriate safety measures and risk reduction.
Understand The Hazards Associated With Laser Marking Operations
- Laser radiation exposure risk: One of the most significant dangers associated with laser marking is the risk of exposure to laser radiation. Direct or indirect exposure to high-intensity laser beams can cause eye injuries ranging from temporary vision impairment to permanent blindness. Additionally, skin exposure to laser radiation may result in burns or tissue damage. Engineering controls such as interlocks, enclosures, and beam shields must be implemented to minimize the risk of personnel exposure to laser radiation.
- Fire and Ignition Hazards: The laser marking process generates heat, which may create fire and ignition hazards, especially when working with flammable materials or in environments with combustible dust or vapors. Proper ventilation and fire suppression systems are required to manage these hazards. Additionally, conducting regular inspections and implementing safe work practices, such as removing flammable materials near laser equipment, can help prevent fire incidents.
- Material and chemical hazards posed by marking substrates: Some marking substrates may emit harmful fumes, particulates, or chemicals when laser marked. For example, some plastics can release toxic gases when heated, causing respiratory hazards to people. It is critical to assess the potential hazards of marked substrates and implement appropriate ventilation systems and personal protective equipment (PPE) to mitigate exposure risks.
Risks To People, Equipment And The Environment
Insufficient safety measures during laser marking operations pose risks not only to personnel, but also to equipment and the environment. For example, improper handling of laser equipment or failure to follow safety protocols can result in damage or malfunction of the equipment. Additionally, the release of hazardous substances into the environment due to improper ventilation or containment measures may have adverse effects on environmental health. Implementing a sound safety management system and regular inspections can help minimize these risks.
In summary, laser marking operations present a variety of hazards that require careful consideration and proactive risk management strategies. By understanding the potential risks associated with laser radiation exposure, fire hazards, material hazards, and other operational hazards, organizations can implement appropriate safety measures to protect personnel, equipment, and the environment from harm.
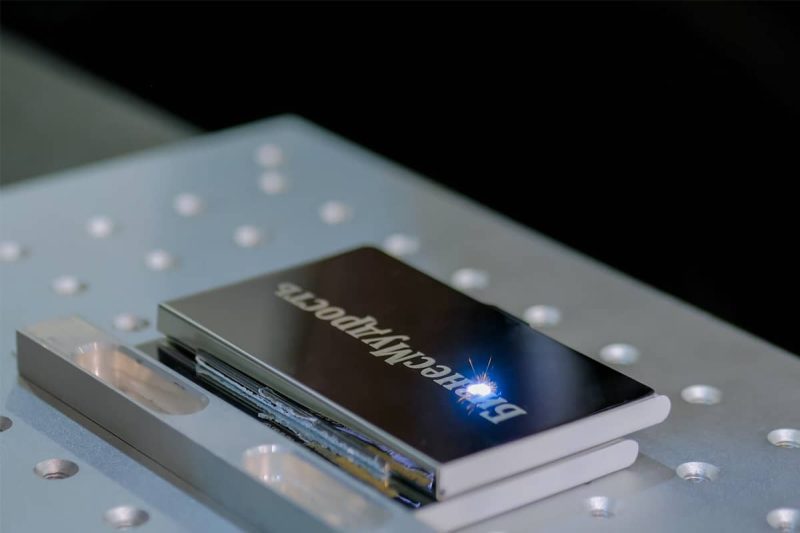
What Safety Precautions Should Be Taken When Laser Marking?
Safety precautions related to laser operation are critical to protecting personnel and ensuring a safe working environment. Implementing comprehensive safety measures can minimize the risks associated with laser radiation exposure, fire hazards, and material hazards. Here are some basic safety precautions:
Personal Protective Equipment (PPE)
- Laser Safety Glasses: Proper laser safety glasses or goggles are available that are designed to block the specific wavelengths of the laser being used. Ensure that all personnel working in laser operating areas wear appropriate eyewear.
- Protective Clothing: Personnel are required to wear appropriate clothing to protect against potential burns or skin exposure to laser radiation. This may include long-sleeved shirts, pants, and closed-toed shoes made of non-flammable materials.
- Gloves: Use heat-resistant gloves when handling hot materials or operating laser equipment to prevent burns.
Laser Safety Training
- Provide comprehensive laser safety training to all personnel involved in laser marking operations. Training should cover topics such as laser hazards, safe operating procedures, emergency protocols, and the proper use of personal protective equipment.
- Ensure personnel understand the specific hazards associated with the type of laser being used and understand how to safely operate and maintain laser equipment.
Control Measures
- Implement engineering controls such as interlocking, beam containment, and beam shielding to prevent unauthorized access to the laser beam and minimize the risk of laser radiation exposure.
- Use administrative controls such as establishing laser safety protocols, conducting regular safety inspections, and maintaining clear signage to communicate hazards and safe operating procedures.
- Hire a laser safety officer or designee who is responsible for overseeing laser safety practices, conducting hazard assessments, and ensuring compliance with safety regulations.
Ventilation And Smoke Extraction
- Install appropriate ventilation systems and fume extraction equipment to remove airborne contaminants, smoke, and particulate matter generated during laser marking operations.
- Make sure the ventilation system is properly maintained and adequate to meet the specific requirements of the laser marking process and the material being marked.
- Regularly inspect ventilation systems and smoke extraction equipment to verify their effectiveness and resolve any issues promptly.
By incorporating these safety precautions into laser marking operations, organizations can create a safer work environment and minimize the risks associated with laser radiation exposure, fire hazards, and material hazards. Regular training, hazard assessments, and ongoing safety monitoring are important components of a comprehensive laser safety program.
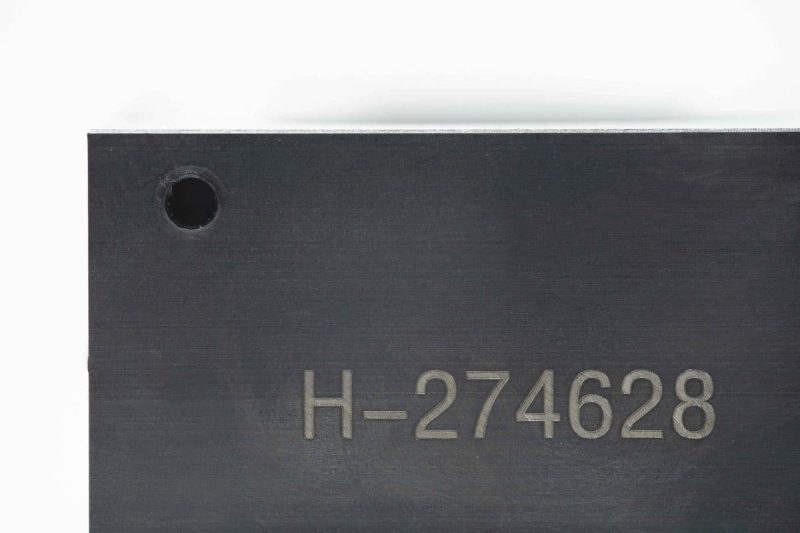
Safe Handling And Storage Of Marking Materials
Safe handling and storage of marking materials, including substrates and chemicals, is an important prerequisite to preventing accidents, minimizing hazards and maintaining a safe work environment.The following are guidelines for responsible handling of tagged materials:
Handling Marking Substrates And Chemicals
- Follow Manufacturer’s Instructions: Follow the manufacturer’s guidelines for handling and storage of marking substrates and chemicals. This includes information on proper storage conditions, handling precautions, and recommended personal protective equipment (PPE).
- Avoid direct contact: Wear appropriate personal protective equipment (such as gloves, safety glasses, and protective clothing) to minimize direct skin contact with the marking substrate and chemicals.
- Use in a well-ventilated area: Perform marking operations in a well-ventilated area to minimize exposure to harmful fumes or vapors. If ventilation is insufficient, use local exhaust ventilation or respiratory protection if necessary.
- Labeling: Clearly label labeled substrates and chemicals with appropriate hazard warnings, operating instructions, and storage requirements to ensure safe identification and use.
Dangerous Goods Storage Requirements
- Segregation: Store marking substrates and chemicals separately from incompatible materials to prevent cross-contamination or chemical reactions. Follow segregation guidelines based on compatibility charts or Material Safety Data Sheets (MSDS).
- Appropriate Containers: Use appropriate containers and packaging to store marking substrates and chemicals. Make sure containers are sealed and labeled with relevant hazard information.
- Storage conditions: Store marking materials in designated storage areas that comply with environmental and safety regulations. When determining storage conditions, consider factors such as temperature, humidity, and sunlight exposure.
- Emergency Response: Maintain emergency response procedures and equipment, such as spill kits, chemical neutralizers, and fire extinguishers, in areas where marked materials are stored.
Proper Disposal Of Waste
- Hazardous waste classification: Identifies and labels waste materials that qualify as hazardous waste based on regulatory classification and disposal requirements. Common hazardous waste categories include flammable, corrosive, toxic, and reactive materials.
- Segregation: Separating hazardous waste from non-hazardous waste and ensuring proper labeling and sealing to prevent leaks or spills during storage and transportation.
- Disposal methods: Dispose of hazardous waste through an authorized waste disposal facility or a licensed hazardous waste contractor by local, state, and federal regulations. Pack, label, and transport hazardous waste to disposal sites by prescribed procedures.
By following these guidelines for safely handling and storing marked materials, organizations can minimize risks, protect people and the environment, and comply with regulatory requirements governing the handling, storage, and disposal of hazardous materials. Regular training, hazard assessment and compliance with best practices are among the best measures to ensure safe handling throughout the life cycle of marked materials.
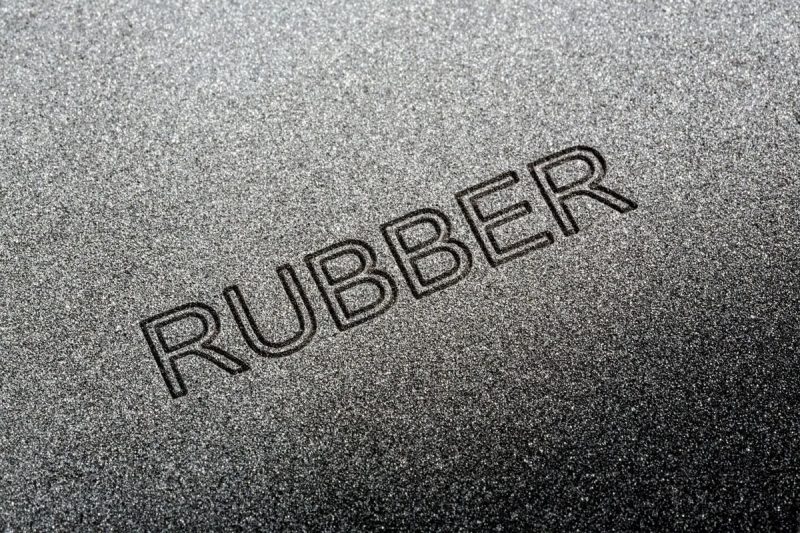
Emergency Procedures To Prevent Hazardous Operations In Laser Marking
Implementing effective emergency procedures is essential to prevent hazardous situations during laser marking operations and ensure a prompt and appropriate response in the event of an accident or injury. The following is a comprehensive overview of laser marking emergency procedures:
Protocol For Laser Related Accidents Or Injuries
- Conduct regular safety inspections and maintenance inspections on laser equipment to detect and deal with potential hazards promptly.
- Ensure all personnel are trained in laser safety protocols, emergency procedures, and first aid techniques.
- Establish clear lines of communication to report hazards, incidents, or safety issues to designated personnel or supervisors.
- Maintain an emergency contact list with relevant contact information for local emergency services, medical facilities, and designated laser safety officials.
Response To Laser-Related Accidents Or Injuries
- Relatively low cutting accuracy for metal materials: Compared with fiber laser cutting machines, CO2 laser cutting machines may be slightly less precise when cutting metal materials. Especially when cutting thin plates and cutting complex structures, its accuracy may not be as good as that of fiber laser cutting machines.
- Higher energy consumption: CO2 laser cutting machines have higher energy consumption, which increases operating costs. Especially when working continuously for a long time, energy consumption may become an issue that cannot be ignored.
First Aid Procedures For Laser Burns Or Eye Injuries
Laser Burns
- If burns are caused by fire, move the affected person away from the laser beam source and extinguish any flames.
- Cool the burn with warm water for at least 10-20 minutes to relieve pain and minimize tissue damage.
- Cover the burn with a clean, dry dressing or sterile bandage to protect the area and prevent infection.
- Seek immediate medical attention for further evaluation and treatment of burn injuries.
Eye Injury
- If an individual suffers an eye injury from laser exposure, immediately flush the affected eye with clean water or a sterile saline solution for at least 15 minutes.
- Do not rub or put pressure on the injured eye as this may worsen damage to the eye tissue.
- Cover the injured eye with a clean, dry dressing or a sterile eye patch to protect the area and prevent further injury.
- Seek emergency medical attention from an eye specialist or emergency medical services for thorough evaluation and treatment of eye injuries.
Contact Information For Emergency Services And Medical Assistance
- Ensure all personnel have access to emergency contact information for local emergency services, including ambulance services, fire departments, and medical facilities.
- Display emergency contact numbers prominently in designated areas within the facility, such as near laser equipment or in common work areas.
- Provide additional contact information for a designated laser safety officer or supervisor who can coordinate emergency response efforts and provide assistance as needed.
By implementing these emergency procedures and providing comprehensive training to personnel, organizations can effectively prevent hazardous operations in laser marking and ensure a timely, coordinated response to laser-related accidents or injuries that minimizes potential harm and Promote workplace safety.
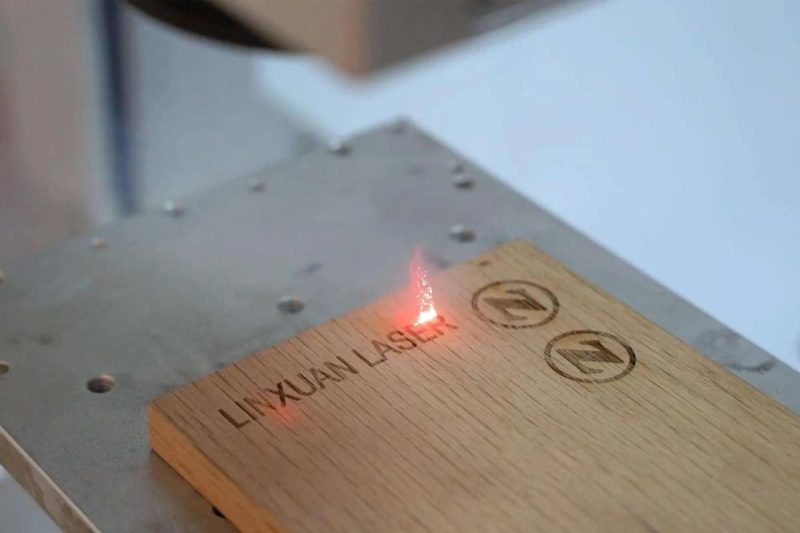
Perform Regular Maintenance Inspections On Laser Marking Machines
Regular maintenance inspections of your laser marking machine help ensure optimal performance, extend equipment life, and maintain a safe working environment. Routine machine inspections and maintenance measures can help us detect potential problems early, prevent costly failures, and reduce safety risks. The following introduces the measures for regular maintenance and inspection:
Routine Machine Inspection And Maintenance
- Routine inspections include visual inspection of the laser marking machine and its components for signs of damage, wear, or abnormalities.
- Check for loose or damaged parts, such as belts, mirrors, lenses, and protective guards, and tighten or replace them as necessary.
- Clean the machine and its components regularly to remove dust, debris, or contaminants that may affect performance or safety.
- Lubricate moving parts according to the manufacturer’s recommendations to ensure smooth operation and prevent premature wear.
Check Laser Alignment, Beam Quality And Safety Features
- Regularly check the alignment of the laser beam to ensure it accurately hits the desired marking area and maintains consistent quality.
- Adjust laser beam alignment as needed using the manufacturer’s recommended alignment tools and techniques.
- Monitor beam quality parameters such as beam profile, power stability, and focus size to ensure optimal marking performance.
- Test safety features such as interlocks, emergency stop buttons, and safety enclosures to verify that they operate properly and provide adequate protection against laser hazards.
Calibration Of Safety Systems And Emergency Shutdowns
- Calibrate safety systems, including laser power meters, beam occluders, and beam shutters, to ensure they accurately detect and respond to laser emissions.
- Regularly inspect emergency shutdown procedures and equipment to verify that they can effectively stop laser operations during an emergency.
- Train personnel on proper emergency shutdown procedures and ensure they understand how to safely shut down laser equipment in the event of an emergency or malfunction.
By implementing the above routine inspections and maintenance measures for machines, companies can minimize downtime, reduce the risk of accidents, and extend the service life of laser marking equipment. It is important to follow the manufacturer’s recommendations and maintenance procedure guidelines and seek professional help for complex repairs or problems beyond routine maintenance.
Summarize
From intricate designs on metal surfaces to clear identification codes on plastic parts, laser marking has become a key technology for precision marking and branding across industries. However, behind the benefits there are also potential dangers, and in this article we explore the safety precautions needed to conduct a safe and responsible laser marking operation. By adhering to strict safety precautions, including training, use of personal protective equipment, risk assessments, maintenance inspections, and emergency preparedness, you can create an environment conducive to an efficient and reliable laser marking work environment while ensuring the safety of personnel and efficient operation of equipment.
At AccTek Laser, we specialize in providing customized laser marking solutions to meet your unique requirements. Our team of experienced professionals is ready to guide you through the entire process, ensuring laser marking technology is seamlessly integrated into your production line. Share your project details, material specifications and production needs and our experts will provide you with a comprehensive quote outlining optimal marking speeds and custom solutions.
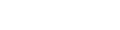
Contact information
- [email protected]
- [email protected]
- +86-19963414011
- No. 3 Zone A, Lunzhen Industrial Zone,Yucheng City , Shandong Province.
Get Laser Solutions