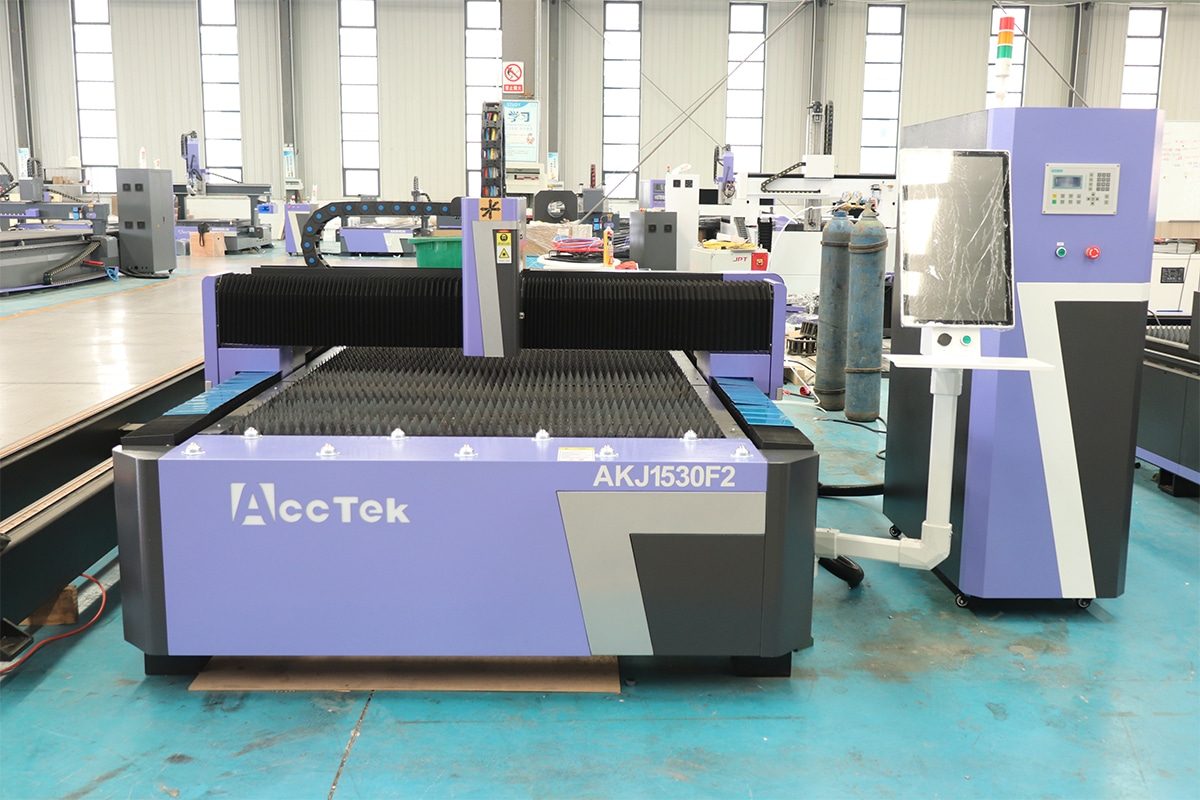
What to Consider Before Buying a Laser Cutting Machine
Laser-cutting machines have become an indispensable tool for a wide range of industries, including manufacturing, automotive, textiles, and electronics. With unparalleled precision, efficiency, and versatility, these machines are a vital investment for businesses looking to increase their production capabilities. However, purchasing a laser cutting machine is a big decision that requires a significant financial investment and thorough research. Understanding the key factors to consider can go a long way in selecting the right machine for your specific needs and operational requirements.
This article explores the essential aspects to evaluate before purchasing a laser cutting machine, guiding you through the intricacies of this technology to ensure you make a smart, strategic investment. Whether you are looking to upgrade your existing equipment or venture into laser cutting for the first time, this comprehensive guide will help you navigate the decision-making process with confidence.
Table of Contents
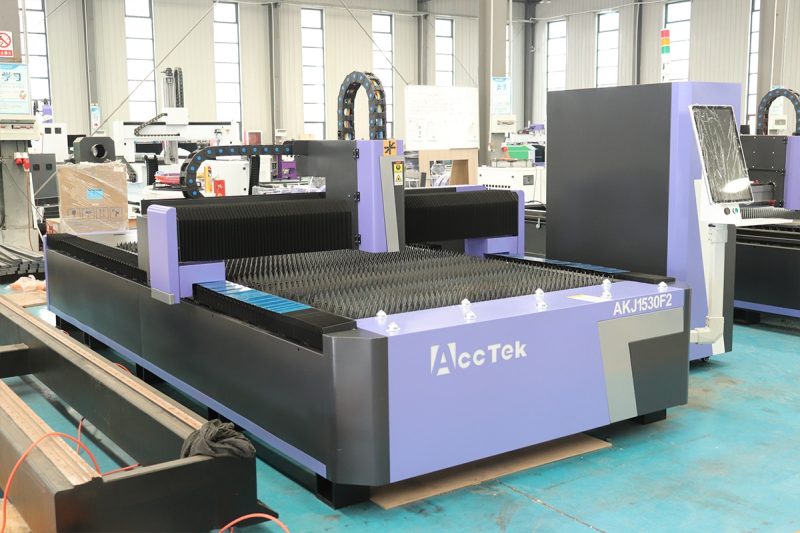
Understanding Laser Cutting Machine
When considering buying a laser cutting machine, you need to understand the different types available and their specific applications ahead of time. The two most commonly used laser cutting machines are fiber laser cutting machines and CO2 laser cutting machines. Each has different features, advantages, disadvantages, and ideal applications.
Fiber Laser Cutting Machine
Description
Fiber laser cutting machines use a solid-state laser source, where the laser beam is generated by a set of diodes and then guided and amplified by a fiber optic cable. The technology is known for its high efficiency and ability to produce a small spot of concentrated beam, resulting in precise and clean cuts. Fiber laser generators are particularly suitable for cutting metal materials.
Advantages
- High Efficiency: Fiber lasers have a higher electro-optical conversion efficiency than CO2 laser generators, which reduces energy consumption and operating costs.
- Precision: The small spot and high power density enable extremely precise cutting, making them ideal for complex designs and fine details.
- Speed: Fiber laser generators can cut materials, especially thin metals, at higher speeds, increasing productivity.
- Low Maintenance: These machines have fewer moving parts and the laser source has a longer life, which reduces maintenance requirements.
- Versatility: Able to cut a variety of metals, including carbon steel, stainless steel, aluminum, brass, and copper.
Disadvantages
- Cost: The initial investment is higher compared to CO2 laser cutting machines, but the operating savings can offset this cost over time.
- Material limitations: While fiber lasers are well suited for metals, they are less effective on non-metallic materials such as wood, acrylic, and some plastics.
- Complexity: The technology can be more complex to operate and requires specialized training for operators.
Applications
- Metal Fabrication: Cutting and shaping metals for the automotive, aerospace, and construction industries.
- Electronics: Precision cutting of components and housings.
- Jewelry: Fine engraving and cutting of metals used in jewelry making.
- Medical Devices: Manufacturing of precise and complex medical instruments.
CO2 Laser Cutting Machine
Description
CO2 laser cutting machines use a mixture of gases (usually CO2, nitrogen, and helium) excited by an electrical discharge to produce a laser beam. This beam is then directed and focused to cut or engrave materials. CO2 laser cutting machines are highly versatile and can cut a wide range of non-metallic and metallic materials.
Advantage
- Versatility: It can cut both metallic and non-metallic materials, including wood, acrylic, glass, leather, and textiles.
- Smooth Cuts: It provides smooth, clean cuts, especially on non-metallic materials.
- Lower Initial Cost: Typically cheaper than fiber laser cutters, making it more accessible to small businesses and startups.
- Ease of Use: CO2 laser cutting machines are generally considered easier to use and set up, especially for non-metallic applications.
Disadvantage
- Less Efficiency: CO2 laser generators are less energy efficient than fiber laser generators, resulting in higher operating costs over time.
- Slower Speeds: Cutting speeds are slower compared to fiber laser cutters, especially for metals.
- Maintenance: CO2 laser tubes require more maintenance due to the presence of more moving parts and the need to replace them regularly.
- Thickness Limitation: Cuts thick metals less efficiently than fiber laser cutting machines.
Applications
- Signage and Advertising: Cuts and engraves acrylic, wood, and other materials to create signs and displays.
- Textiles and Fashion: Cuts fabrics and materials for apparel and accessories.
- Packaging: Creates custom packaging and prototypes from cardboard, paper, and plastic.
- Crafts: Engraves and cuts materials for art and decorative projects.
Both fiber laser cutting machines and CO2 laser cutting machines have their unique advantages and disadvantages. Fiber laser cutting machines excel at cutting metals with high precision and speed, making them ideal for industries such as automotive, aerospace, and metal fabrication. On the other hand, CO2 laser cutting machines offer greater flexibility in cutting a variety of non-metallic materials, making them suitable for industries such as signage, textiles, and woodworking. Understanding these differences will help you choose the right laser-cutting machine for your specific needs and applications, ensuring a worthwhile investment for your business.
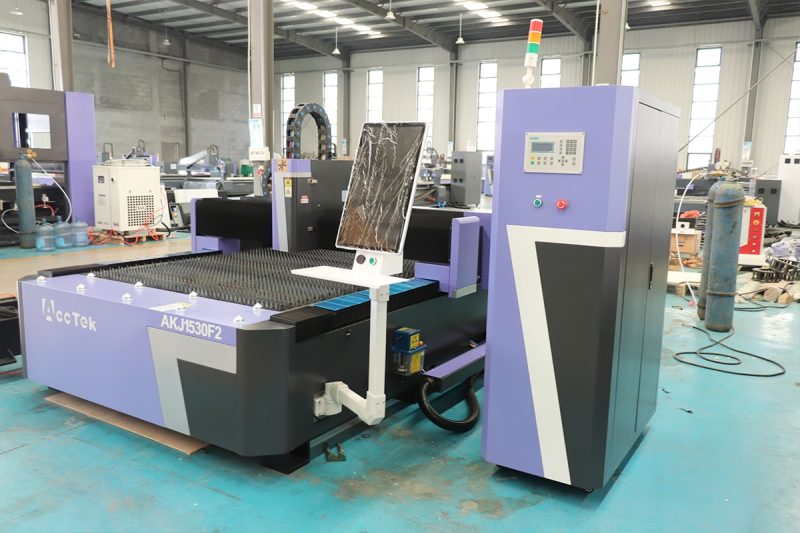
Factors to Consider Before Purchasing a Laser Cutting Machine
When purchasing a laser cutting machine, you need to carefully evaluate various factors to ensure that the equipment you choose meets your business needs and maximizes your return on investment. Here are the key considerations to keep in mind:
Budget Considerations
- Initial Cost: The initial purchase price of a laser cutting machine can vary widely depending on its type, power, and features. Determine your budget range and look for a machine that offers the best value within that range. Keep in mind that higher-end models may cost more upfront but offer better performance and longevity.
- Operating Costs: Consider ongoing expenses such as energy consumption, maintenance, replacement parts, and consumables such as lenses and gases. Choosing a more energy-efficient machine can reduce long-term operating costs.
- Return on Investment (ROI): Evaluate how the machine will affect your production capabilities and profitability. More expensive machines may offer faster speeds and better precision, resulting in increased productivity and higher-quality output, which can improve your ROI.
Material Compatibility
- Material Type: Determine the materials you plan to cut (e.g., metal, plastic, wood, textile) and make sure the laser cutter is compatible with them.
- Specific Material Requirements: Different materials require specific laser types (e.g., fiber laser for metals, and CO2 laser for non-metals). Make sure the machine can handle the material properties and thickness.
Cutting Thickness
- Maximum Cutting Thickness: Make sure the machine can cut the thickest material you are using. The power and type of laser will affect its ability to cut different thicknesses. Consider the maximum thickness of different materials the machine can handle.
- Consistency: Evaluate the machine’s ability to cut consistently across different thicknesses. Some machines may have difficulty handling thicker materials, resulting in inconsistent cuts or requiring multiple passes.
Cutting Speed
- Production Speed: Higher cutting speeds can significantly increase your productivity. Evaluate how fast the machine can cut the materials you use, balancing speed with your need for precision and quality.
- Efficiency: Consider how efficiently the machine can handle multiple cuts and different materials. Advanced software and control systems can optimize cutting paths, reducing cutting time and material waste.
Precision and Accuracy
- Tolerance Level: Different applications require different levels of precision. Make sure the machine can meet the tolerance levels required for your project, especially for intricate designs and detailed work.
- Beam Quality: The quality of the laser beam affects the precision of the cut. Machines with superior beam quality produce finer, more accurate cuts.
Understand Power Requirements
- Laser Power: Laser power, measured in watts, determines the machine’s cutting capabilities. Thicker materials and faster cutting speeds require higher power. Match the laser power to your specific cutting needs.
- Electrical Requirements: Make sure your facility can support the electrical needs of the laser cutter. Some high-power laser generators require special electrical setups.
Machine Size
- Workspace Size: Consider the space available in your facility for the laser cutter, including space for material handling and storage.
- Footprint: Consider the physical space available in your facility. Laser cutters come in a variety of sizes, and you need to make sure there is enough room for the machine, material handling, and operator access.
Ease of Use and Software Compatibility
- User Interface: The user-friendly interface shortens the learning curve and increases productivity. Look for machines with intuitive controls and clear displays.
- Software Integration: Make sure the machine’s software is compatible with your existing design and production tools. Advanced software features such as nesting, autofocus, and real-time monitoring can improve efficiency and accuracy.
Control System
- Precision Control: The high-quality control system precisely manipulates the laser and material, resulting in improved cut quality. Consider systems with advanced motion control and feedback mechanisms.
- Automation Features: Features such as autofocus, material loading/unloading, and real-time monitoring can improve efficiency and reduce operator workload.
Maintenance and Service Requirements
- Routine Maintenance: Understand the regular maintenance tasks required to keep the machine running smoothly. Machines with fewer maintenance requirements can reduce downtime and operating costs.
- Service Support: Choose a manufacturer known for reliable customer support and easy access to spare parts. A good warranty and responsive technical support can minimize downtime and resolve issues quickly.
Safety Features and Regulatory Compliance
- Safety Enclosure: Ensure the machine has an appropriate safety enclosure to protect the operator from laser exposure.
- Fume Extraction: An effective fume extraction system can help remove hazardous fumes and particles generated during the cutting process.
- Emergency Stop: An easily accessible emergency stop button allows the operator to quickly shut down the machine in an emergency.
- Regulatory Compliance: Verify that the machine complies with relevant safety standards and regulations in your region to ensure a safe working environment.
Additional Features and Accessories
- Customization Options: Consider machines that offer customizable features to meet specific operational needs.
- Accessories: Evaluate the availability and cost of additional accessories, such as rotary attachments, advanced lenses, and specialized cutting heads.
- Future Upgradeability: Choose a machine that can be upgraded with new features or higher-powered lasers to keep up with future technological advances.
Choosing the right laser-cutting machine requires a thorough understanding of your specific needs and careful evaluation of a variety of factors. By considering your budget, material compatibility, cutting thickness, speed, accuracy, power requirements, machine size, ease of use, control systems, maintenance, safety, and additional features, you can make an informed decision that will improve your operational efficiency and ensure a successful investment. This comprehensive approach will help you select a laser-cutting machine that not only meets your current needs but also supports your future growth and productivity.
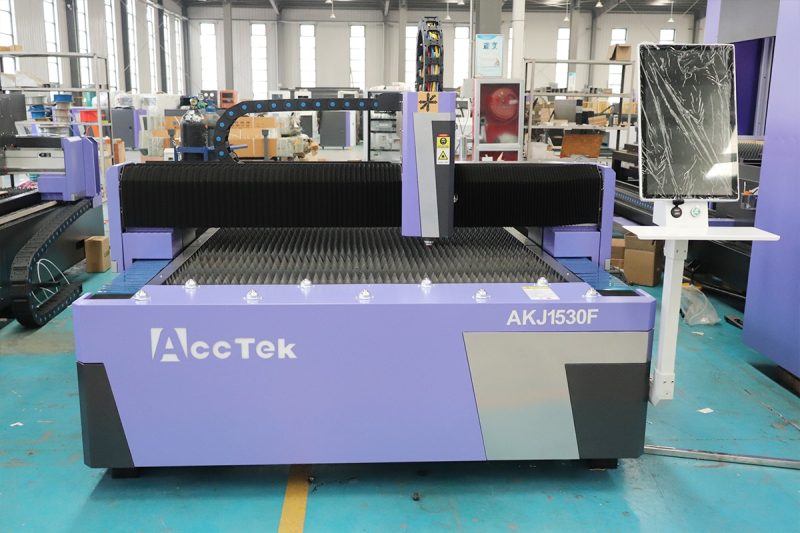
Research and Compare Options
When considering purchasing a laser cutting machine, thoroughly researching and comparing available options is a critical step to ensure you make an informed decision. Here are key steps to guide you through this process:
Gather Information from Reputable Sources
- Manufacturer Websites: Start by browsing the official websites of laser cutting machine manufacturers. These websites offer detailed specifications, features, and capabilities of their machines. Look for technical data sheets, product catalogs, and case studies that can give you a comprehensive understanding of each machine’s capabilities.
- Industry Publications: Subscribe to industry magazines, journals, and online publications that cover advancements in laser cutting technology. Articles, reports, and white papers can provide insight into the latest trends, technological innovations, and best practices.
- Trade Shows: Attend industry trade shows and conferences. These events are great opportunities to see machines in action, speak directly with manufacturers, and attend demonstrations and demos. Trade shows also allow you to compare different models side-by-side and network with industry professionals.
- Online Forums and Communities: Join online forums, discussion groups, and social media communities that focus on laser-cutting technology. Participating in these platforms can help you gain practical insights from other users’ experiences, ask questions, and get advice.
Read Reviews and Testimonials
- Customer Reviews: Look for customer reviews on manufacturer websites, third-party review sites, and online marketplaces. Reviews provide a user’s first-hand experience with the machine, highlighting both positive and negative aspects.
- Case Studies and Success Stories: Many manufacturers publish case studies and success stories on their websites. These documents detail the use of their machines in real-world applications, demonstrating benefits and performance across a variety of industries.
- Testimonials: Look for testimonials from well-known companies and industry leaders. These endorsements can increase confidence in the machine’s capabilities and reliability.
- Comparative Reviews: Look for comparative reviews and articles that evaluate multiple laser-cutting machines. These reviews often provide side-by-side comparisons of features, performance, and value, helping you understand the pros and cons of different models.
Consult Industry Experts or Peers
- Industry Experts: Contact industry experts, consultants, and technical advisors who specialize in laser cutting technology. Their expertise can provide valuable insights into technical aspects, recent advances, and best practices for selecting a machine.
- Peers and Colleagues: Consult peers and colleagues in your industry who have experience with laser-cutting machines. Their practical experience and advice can help you avoid common pitfalls and make informed decisions based on real-world applications.
- Professional Associations: Join professional associations and organizations related to laser cutting and manufacturing. These groups often have resources, forums, and networking opportunities that connect you with knowledgeable professionals and experts.
Request Quotes and Demos from Multiple Suppliers
- Request Quotes: Contact multiple suppliers and request detailed quotes for the laser cutting machine you are considering. Make sure the quotes include all costs, such as shipping, installation, training, and maintenance. Comparing quotes will help you understand the price range and determine the product that best fits your budget.
- Schedule Demo: Schedule a live or virtual demo with different suppliers. By watching the machine in action, you can evaluate its performance, speed, precision, and ease of use. Ask the supplier to demonstrate how to cut specific materials and designs to understand how the machine can meet your requirements.
- Ask Questions: During the demo, ask in detail about the machine’s features, capabilities, and limitations. Ask about the training provided, software compatibility, maintenance requirements, and after-sales support. A thorough understanding of these areas will help you evaluate the machine’s overall value and suitability.
Researching and comparing options is a critical stage in the process of purchasing a laser-cutting machine. By gathering information from reputable sources, reading reviews and testimonials, consulting industry experts or peers, and requesting quotes and demonstrations from multiple suppliers, you can make an informed decision. This comprehensive approach ensures that you select a laser-cutting machine that meets your operational needs, budget, and long-term goals, ultimately increasing your productivity and profitability.
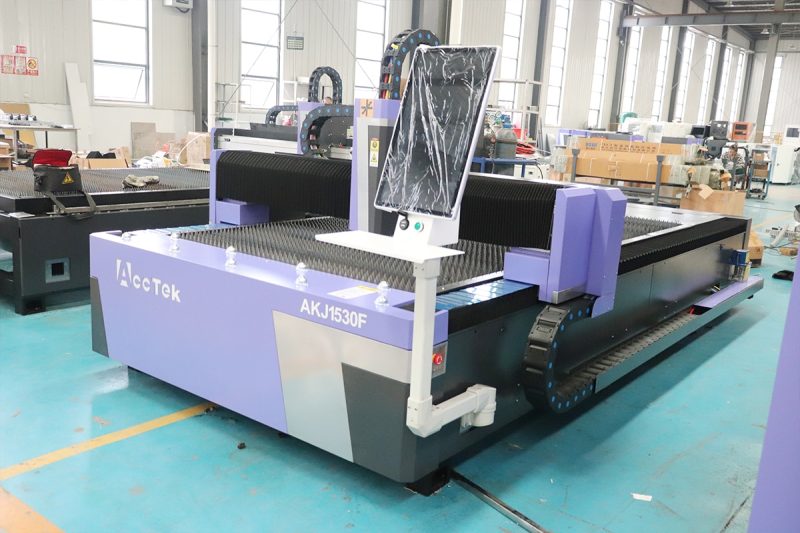
Evaluating Suppliers and Brands
When purchasing a laser cutting machine, evaluating suppliers and brands on the market is a crucial step. The reputation and reliability of a manufacturer can significantly impact your long-term satisfaction with the machine. Here are the key factors to consider when evaluating suppliers and brands:
Manufacturer Reputation and Experience
- Track Record: Research the manufacturer’s history and track record. Companies that have been in the industry for a long time may have more experience and a proven track record of producing reliable and high-quality machines.
- Customer Reviews and Testimonials: Look for customer reviews and testimonials that highlight the manufacturer’s reputation. Positive feedback from existing users can be a strong indication of a manufacturer’s reliability and product quality.
- Awards and Recognitions: Consider manufacturers that have received industry awards and recognitions. These accolades can be a testament to their innovation, quality, and commitment to excellence.
- Global Presence: Manufacturers with a global presence often have more resources and a strong supply chain, ensuring better support and service no matter where you are located.
Warranty and After-Sales Support
- Warranty Terms: Check the warranty terms offered by the manufacturer. A comprehensive parts and labor warranty can provide peace of mind and protect your investment.
- Duration and Coverage: Check the warranty duration and what it covers. Some manufacturers offer extended warranties or service contracts that can be beneficial to you.
- After-Sales Support: Evaluate the after-sales support provided by the manufacturer. Reliable support helps minimize downtime and resolve any issues that may arise during the operation of the machine.
- Service Network: Consider the manufacturer’s service network and whether they have authorized service centers or technicians in your area. A well-established service network ensures fast and efficient support.
Customer Service Responsiveness
- Response Time: Evaluate the manufacturer’s responsiveness to customer inquiries and support requests. Fast response times can maintain productivity and minimize disruptions.
- Technical Assistance: Ensure that the manufacturer offers technical assistance, including troubleshooting guides, online resources, and access to skilled technicians.
- Training and Resources: Look for manufacturers that offer comprehensive training programs and resources. Proper training ensures your team can operate the machine efficiently and safely.
- Communication Channels: Consider the availability of multiple communication channels, such as phone, email, and live chat, to contact customer support. This flexibility can improve the overall customer service experience.
Availability of Spare Parts and Consumables
- Spare Parts Inventory: Check the availability of spare parts for your laser cutting machine. A readily available spare parts inventory reduces downtime and ensures smooth operation.
- Consumables: Evaluate the availability and cost of consumables such as laser tubes, lenses, and filters. Affordable and easily accessible consumables contribute to cost-effective long-term operations.
- Local Dealers: Determine if the manufacturer has local dealers or partners who can quickly supply spare parts and consumables. This can significantly reduce waiting time for critical parts.
- Supply Chain Reliability: Consider the reliability of the manufacturer’s supply chain. Supply chain disruptions can cause delays in receiving important parts and consumables.
Upgradeability and Future-Proof Options
- Modular Design: Look for machines with a modular design that can be easily upgraded and modified. This flexibility ensures that the machine can adapt to changing needs and technological advances.
- Software Updates: Make sure the manufacturer provides regular software updates that enhance the machine’s performance and functionality. Up-to-date software is essential to maintain compatibility with new technologies and improved functionality.
- Scalability: Consider the machine’s scalability and whether it can be expanded to meet future production needs. Scalable machines can grow with your business and accommodate increased workloads.
- Innovation and R&D: Evaluate the manufacturer’s commitment to innovation and research and development (R&D). Companies that invest in R&D are likely to introduce new features and improvements that keep their machines at the forefront of technology.
Evaluating suppliers and brands is a critical step in purchasing a laser-cutting machine. You can make an informed decision by considering factors such as the manufacturer’s reputation and experience, warranty and after-sales support, customer service responsiveness, availability of spare parts and consumables, and upgradeability and future-proofing options. This comprehensive evaluation ensures that you choose a reliable, high-quality machine that meets your current needs and supports your business growth and changing needs, ensuring a successful and long-lasting investment.
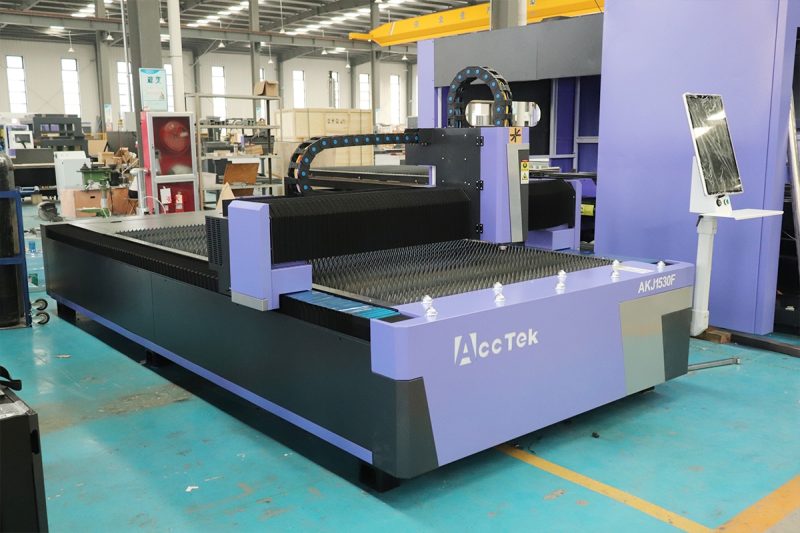
Make a Decision
After thoroughly researching and evaluating the various laser-cutting machine options, it’s time to make an informed decision. This process involves weighing the pros and cons of the different options, considering the long-term costs and benefits, narrowing down the choices based on your priorities and requirements, and finally making a final purchase decision. Here is a detailed guide to help you through this critical stage:
Weigh the Pros and Cons of Different Options
- Gather Information: Gather all the information you can about the different laser-cutting machines you are considering. This includes technical specifications, features, costs, and feedback from reviews and recommendations.
- Create Comparison Matrix: Develop a comparison matrix that lists the key factors for each machine, such as material compatibility, cutting speed, accuracy, power requirements, and ease of use. This visual tool will help you see the pros and cons of each option side by side.
- Evaluate Strengths and Weaknesses: Evaluate the pros and cons of each machine based on your specific needs. For example, one machine may cut quickly but cost more to run, while another may be highly accurate but more complicated to operate.
Consider Long-Term Costs and Benefits
- Total Cost of Ownership (TCO): Calculate the total cost of ownership for each machine, including initial purchase price, maintenance, energy consumption, consumables, and potential downtime. This comprehensive view helps you understand the long-term financial impact.
- Operational Efficiency: Consider how each machine’s features and performance will affect your operational efficiency. A higher initial cost may be justified if the machine significantly increases productivity and reduces material waste.
- Scalability: Consider the future growth of your business. Choose a machine that can scale with your business, whether through upgrades or by handling increased production volumes.
- Return on Investment (ROI): Estimate the ROI by considering the expected increase in production capacity, quality improvements, and potential new business opportunities the machine will bring. Machines with a higher ROI are more reasonable investments.
Narrow Selection Based on Priorities and Requirements
- Match Requirements: Match each machine’s features to your specific requirements. Focus on how each machine meets your priority needs. For example, if you primarily cut metals, a fiber laser might be a better fit than a CO2 laser.
- Prioritize: Determine the factors that are most important to your business. These factors might include cutting speed, material compatibility, precision, ease of use, or after-sales support. Rank these priorities to guide your decision-making process.
- Consult with Stakeholders: Involve key stakeholders in the decision-making process, including operators, production managers, and financial officers. Their input can provide valuable perspective and help ensure that the final selection meets the needs of all departments.
- Supplier Interaction: Further engage with shortlisted suppliers. Request a detailed demonstration, clarify any doubts, and request more information if needed. This interaction provides a deeper understanding of each machine’s suitability.
Make the Final Purchase Decision
- Review Final Options: Review a shortlist of machines that meet your criteria. Make sure all stakeholders are aligned and that any remaining questions or concerns have been addressed.
- Negotiate Terms: Negotiate the best terms with your preferred vendor. This includes price, warranty, maintenance contracts, training, and delivery schedules.
- Check References: Before making a final commitment, check references provided by the vendor. Talking to current users of the machine can provide further assurance of its performance and reliability.
- Purchase: Once you are confident in your choice, proceed with the purchase. Make sure all terms and conditions are clear and well-documented, including warranty, after-sales support, and training terms.
- Implementation Plan: Develop a detailed plan to install, train, and integrate the new machine into your operations. The plan should include timelines, responsibilities, and contingencies to ensure a smooth transition.
Deciding which laser-cutting machine to purchase requires careful consideration of a variety of factors, from technical specifications and long-term costs to supplier reliability and operational requirements. By weighing the pros and cons, considering long-term costs and benefits, narrowing down your choices based on your priorities, and making an informed final decision, you can select the right laser-cutting machine that meets your business goals. This methodical approach will help ensure that your investment will increase your production capabilities, provide a significant return on investment, and support the growth and success of your business. By following these steps, you will be well prepared to make a confident and informed decision, ensuring that the laser-cutting machine you choose is the best fit for your operational needs, budget, and future ambitions.
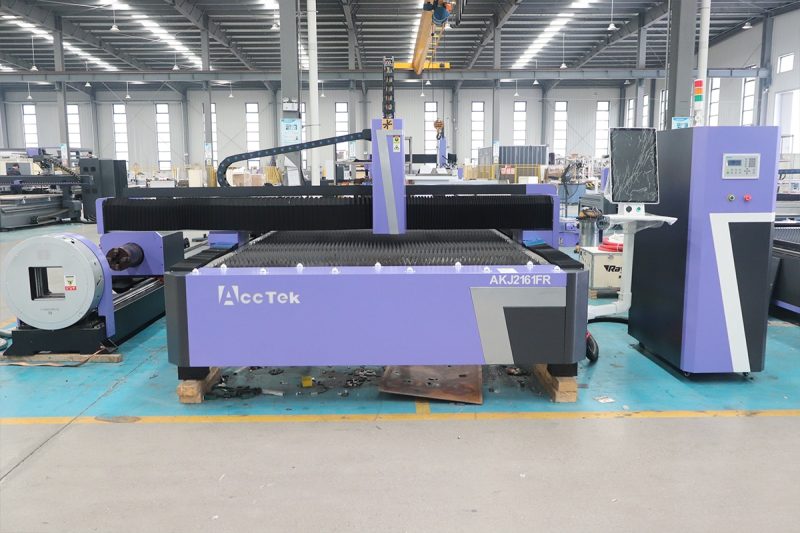
Summary
Choosing the right laser-cutting machine is a complex and critical decision that can significantly impact your business efficiency and growth. Start by understanding the different types of laser cutting machines, such as fiber and CO2 lasers, and their respective benefits and applications. Thoroughly research and compare options by gathering information from reputable sources, reading reviews, consulting industry experts, and requesting quotes and demos.
Evaluate vendors based on their reputation, warranty and support, customer service, spare parts availability, and future-proofing. Carefully weigh the pros and cons, consider long-term costs and benefits, and narrow down your choices based on your specific needs and priorities. Finally, make an informed decision that fits your operational requirements and budget. By following these comprehensive steps, you can select a laser-cutting machine that not only meets your current needs but also supports your future growth and success.
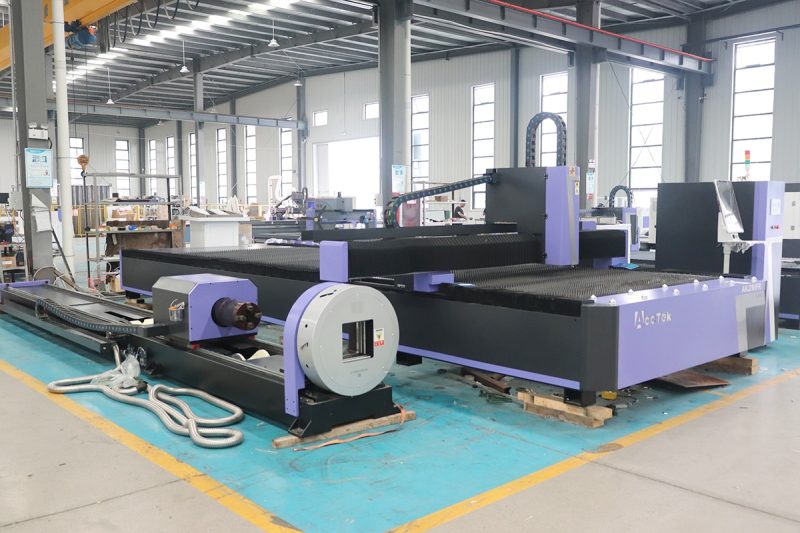
Get Laser Cutting Solutions
When looking for the ideal laser cutting solution, AccTek Laser is a leading supplier with a reputation for providing high-quality machines that meet a variety of industrial needs. We offer a comprehensive range of laser cutting machines, including fiber and CO2 lasers, designed to meet the needs of a wide range of applications. By working with AccTek Laser, you will benefit from our extensive experience, innovative technology, and excellent customer support. Our machines are known for their precision, efficiency, and reliability, ensuring optimal performance in cutting different materials.
In addition, AccTek Laser provides detailed consultation to understand your specific requirements and help you choose the right machine. We also provide comprehensive after-sales support, including training, maintenance, and technical assistance. Investing in an AccTek laser-cutting machine ensures that you get a solution that will enhance your production capabilities and drive your business forward.
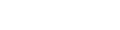
Contact information
- [email protected]
- [email protected]
- +86-19963414011
- No. 3 Zone A, Lunzhen Industrial Zone,Yucheng City , Shandong Province.
Get Laser Solutions