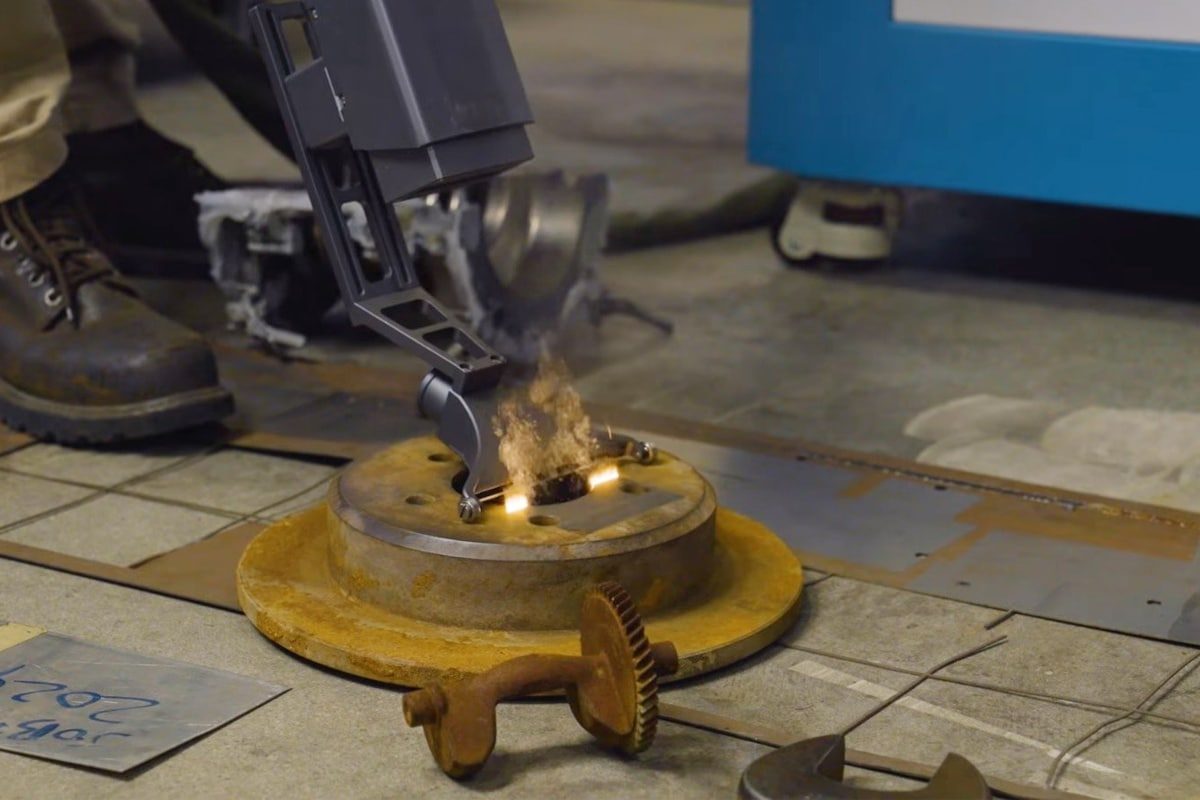
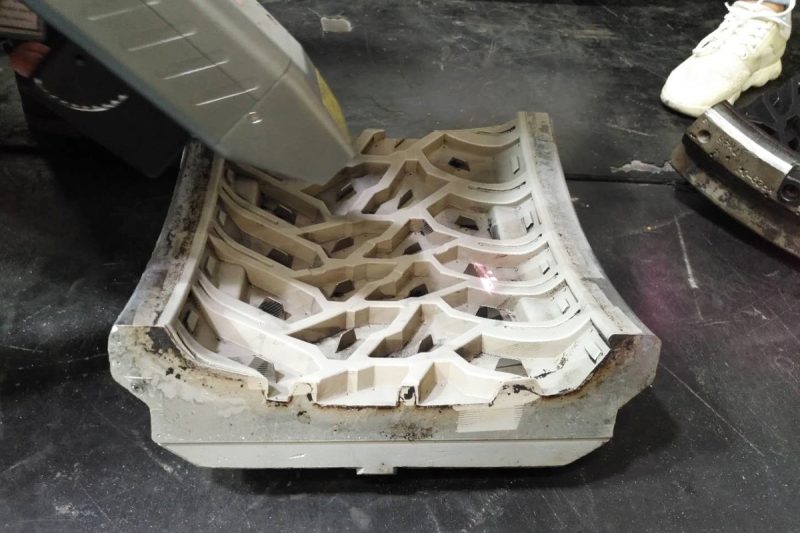
Introduction to Laser Cleaning Technology
Understanding Laser Technology
Laser technology, short for light amplification by stimulated emission of radiation, involves emitting a coherent beam of light that can be precisely controlled and directed. The basic principles of laser technology include:
- Coherence: The light waves produced by lasers are in phase, meaning there is a fixed relationship between their peaks and troughs, resulting in a highly focused and intense beam.
- Monochromaticity: Lasers are typically monochromatic, consisting of a single wavelength or color, which allows for precise aiming and minimal beam spread.
- Directivity: The directionality of lasers means that the beam can be directed with high precision, making them ideal for targeted cleaning applications.
- Energy Density: Lasers can concentrate a large amount of energy into a small area, enabling effective contaminant removal without damaging the underlying material.
Types of Laser Cleaning Machines
Continuous Wave (CW) Laser Cleaning Machines
Continuous wave laser cleaning machines emit a constant laser beam, providing a steady and uninterrupted stream of energy. This type of laser cleaning machine is particularly effective for applications that require uniform cleaning over larger areas. The main features and applications of CW laser cleaning machines include:
- Stable Output: The constant energy output allows for smooth and uniform cleaning, making it ideal for removing thin layers of contaminants or coatings.
- Heat Management: CW lasers generate a lot of heat, which needs to be carefully managed to avoid damaging the substrate. This makes them suitable for use with materials that can withstand higher temperatures.
- Applications: Common uses include cleaning metal surfaces, removing paint, and treating surfaces in the automotive and aerospace industries.
Pulsed Laser Cleaning Machines
Pulsed laser cleaning machines work by emitting short, high-intensity laser beams. This mode of operation allows for precise control of the energy delivered to the surface, making pulsed lasers ideal for delicate and highly controlled cleaning tasks. Key features and applications of pulsed laser cleaning machines include:
- High Peak Power: Short pulses deliver high peak power with minimal heat buildup, reducing the risk of thermal damage to the substrate.
- Precision: The ability to control pulse duration and frequency allows for precise removal of contaminants, making pulsed lasers suitable for delicate cleaning applications.
- Applications: Pulsed lasers are often used to clean sensitive materials such as historical artifacts, semiconductor components, and complex mechanical parts.
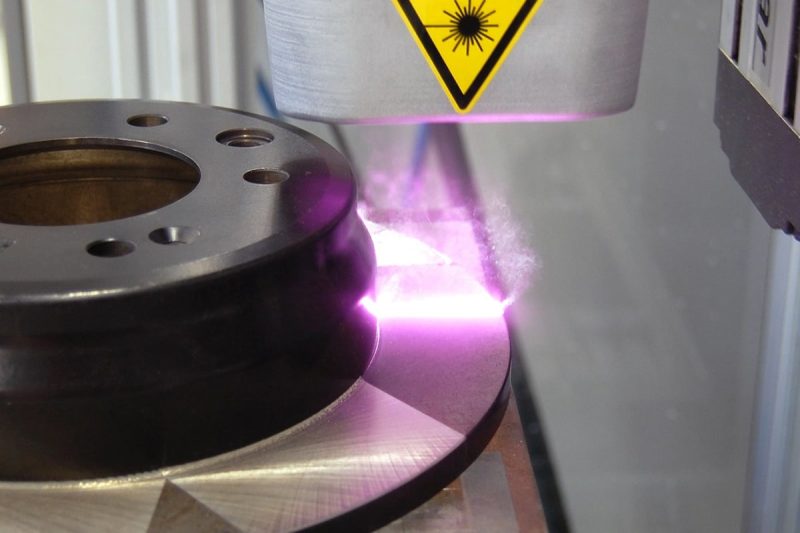
Theoretical Training
Understanding Laser Physics
Basic Principles of Laser Operation
- Stimulated Emission of Radiation: Lasers operate on the principle of stimulated emission of radiation, where an excited electron in an atom drops to a lower energy level, emitting a photon. This photon can then stimulate other excited electrons to emit more photons, resulting in a coherent beam of light.
- Coherence and Monochromaticity: Lasers are coherent, meaning the light waves are in phase, and monochromatic, meaning it has a single wavelength. These properties enable lasers to precisely focus their energy, making them very effective in cleaning applications.
- Amplification: Light is amplified in a gain medium, which can be a gas, liquid, or solid. The gain medium is excited by an energy source, such as an electrical discharge or another laser, creating a population inversion where there are more atoms in an excited state than in the ground state.
Laser-Material Interactions
- Absorption and Ablation: When a laser beam strikes a material, its energy is absorbed, causing rapid heating and subsequent ablation (removal) of the material. The efficiency of the process depends on the absorption characteristics of the material and the laser parameters.
- Threshold Fluence: This is the minimum laser energy per unit area required to begin ablating the material. Different materials have different threshold fluences, and the operator must understand these threshold fluences to adjust the laser settings appropriately.
- Thermal Effects: The laser generates a lot of heat, which can have a thermal effect on the material. The operator must understand how to control these effects to avoid damaging the substrate.
- Photochemical Effects: In some cases, the laser can initiate a photochemical reaction that changes the properties of the material or removes contaminants without significant heating.
Laser Parameters
- Wavelength: The wavelength of the laser determines how it interacts with different materials. For example, shorter wavelengths generally allow for more precise cleaning.
- Power Density: The amount of laser power per unit area affects the rate and depth of cleaning. Higher power densities can remove material faster but require careful control to prevent damage.
- Pulse Duration and Repetition Rate: These parameters control the duration and frequency of the laser pulses. Shorter pulses allow for more precise material removal, while the repetition rate affects the overall speed of the cleaning process.
Components of a Laser Cleaning Machine
Laser Source
- Type of Laser: Different applications may require different types of lasers (continuous and pulsed). Continuous lasers are popular for their efficiency and precision.
- Power Supply: The power supply unit provides the necessary electrical energy to the laser source. Proper handling and maintenance of the power supply ensures consistent laser performance.
Optical System
- Beam Delivery: The components that direct the laser beam from the source to the workpiece, including mirrors, lenses, and optical fibers. Operators must understand how to align and maintain these components to ensure efficient beam delivery.
- Focusing Mechanism: The system used to focus the laser beam onto the target surface, usually involving lenses or adjustable optical elements. Proper focusing allows the desired cleaning effect to be achieved without damaging the substrate.
- Protective Windows: Transparent barriers protect the optical components from contamination from debris and fumes generated during the cleaning process. Regular inspection and cleaning of these windows will maintain optical clarity.
Control System
- User Interface: A control panel or software interface that allows the operator to adjust laser parameters, monitor system status, and perform cleaning procedures. Familiarity with the interface helps achieve efficient operation.
- Safety Interlocks: Built-in safety mechanisms effectively prevent accidental exposure to laser radiation, for example, if the protective door is opened, the interlock device disables the laser.
- Diagnostic Tools: Integrated systems can be used to monitor the performance of the machine and alert the operator to potential problems, such as overheating or misalignment.
Cooling system
- Cooling Methods: Laser generators generate a lot of heat during operation and require an effective cooling system to maintain stable performance. These can include air cooling, water cooling, or refrigeration units.
- Maintenance: Regular maintenance of the cooling system is necessary to prevent overheating and ensure the life of the laser equipment.
Safety Features
- Enclosures: Protective enclosures that contain the laser beam and prevent accidental exposure. Operators should know how to use and maintain these enclosures properly.
- Emergency Stop Button: A conveniently accessible button that immediately shuts down the laser generator in an emergency. Operators must be familiar with its location and operation.
Ventilation and Filtration
- Fume Extraction: Laser cleaning produces fumes and particles that must be safely exhausted from the work area. A ventilation system with filters ensures a safe working environment.
- Filter Maintenance: Regular replacement and maintenance of filters are necessary to keep the ventilation system effective and in compliance with health and safety regulations.
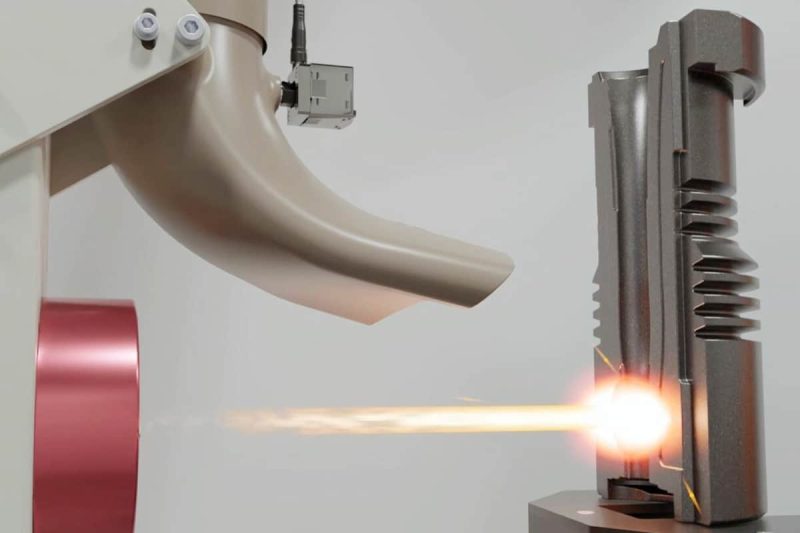
Safety Procedures for Laser Cleaning
Laser Safety Basics
Laser Classifications
- Class 1: Lasers that are safe under all normal conditions of use.
- Class 2: Low-power visible lasers that are safe for accidental exposure of less than 0.25 seconds.
- Class 3R: Medium-power lasers that can be hazardous if exposed directly to the eyes.
- Class 3B: Hazardous High-power lasers if exposed directly to the eyes.
- Class 4: High-power lasers that can cause eye and skin injuries and pose a fire hazard.
Laser Radiation Hazards
- Eye Hazard: The laser beam can cause serious eye damage, including permanent vision loss if viewed directly or reflected.
- Skin Hazard: Direct exposure to the laser beam can cause burns and other skin damage.
- Fire Hazard: High-power lasers can ignite flammable materials, creating a fire risk.
Non-Beam Hazards
- Electrical Hazards: Laser equipment operates at high voltages that may pose a risk of electric shock.
- Fume Hazards: Laser cleaning produces hazardous fumes and particulate matter, requiring proper ventilation.
- Mechanical Hazards: Moving parts in laser cleaning machines can cause personal injury if not handled properly.
Safety Equipment
Personal Protective Equipment (PPE)
- Laser Safety Goggles: Operators must wear laser safety goggles that are specifically designed to protect the operator from the wavelength and power of the lasers used. These goggles prevent eye damage from direct or reflected laser beams.
- Protective Clothing: Wearing flame-retardant and protective clothing minimizes the risk of skin injuries and reduces the impact of debris and particles generated during the cleaning process.
- Gloves: Proper gloves protect hands from burns, cuts, and other injuries.
- Face Masks and Respirators: Depending on the cleaning application, additional protection such as face masks and respirators may be required to protect against fumes and particulates.
Engineering Controls
- Interlock Systems: Safety interlocks prevent the laser from operating if certain conditions are not met, such as a safety door being open or a protective enclosure not in place. This prevents accidental exposure to the laser beam.
- Shielding: Shielding around the laser and cleaning area blocks laser radiation and debris, reducing the risk of accidental exposure and environmental contamination.
- Emergency Stop Button: In an emergency, a conveniently located emergency stop button immediately shuts down the laser, preventing further hazards.
Administrative Controls
- Warning Signs and Labels: Visible warning signs and labels around the laser cleaning area alert personnel to the presence of laser hazards. These signs should identify the laser class, the nature of the hazard, and the safety measures required.
- Access Control: Access to the laser cleaning area is restricted to trained and authorized personnel. This minimizes the risk of exposure to laser hazards for untrained personnel.
Environmental Controls
- Ventilation Systems: Proper ventilation removes hazardous fumes and particles generated during the cleaning process.
- Fume Extractors: Localized fume extractors capture and filter fumes directly at the source.
Safety Procedures
Operational Safety Procedures
- Pre-Operation Inspection: Perform a thorough pre-operation inspection to ensure that all safety systems are functioning properly. This includes verifying that safety interlocks are engaged, protective shields are secure, and that all PPE is available and in good condition.
- Setup and Calibration: Follow the manufacturer’s machine setup and calibration guidelines. This ensures that the laser is properly aligned and that parameters are set for safe operation.
- Operation: Operate the laser cleaning machine according to established protocols. This includes monitoring the machine’s status, keeping the work area clean and organized, and avoiding any actions that could compromise safety.
Maintenance and Inspection Procedures
- Regular Maintenance: Perform regular maintenance tasks as recommended by the manufacturer. This includes cleaning and inspecting the optical system, checking the cooling system, and replacing worn or damaged components.
- Inspection: Regularly inspect safety equipment such as laser safety goggles and protective shields to ensure they are in good condition and provide adequate protection.
Emergency Response Procedures
- Emergency Shutdown: Learn how to use the emergency stop button and other shutdown procedures to quickly and safely shut down the laser in an emergency.
- First Aid and Medical Assistance: Provide immediate first aid for laser-related injuries and know how to seek medical assistance when needed. This includes treating burns, eye injuries, and smoke inhalation.
- Incident Reporting: Report any incidents, near misses, or safety issues to appropriate personnel. This helps identify hazards, improve safety protocols, and prevent future incidents.
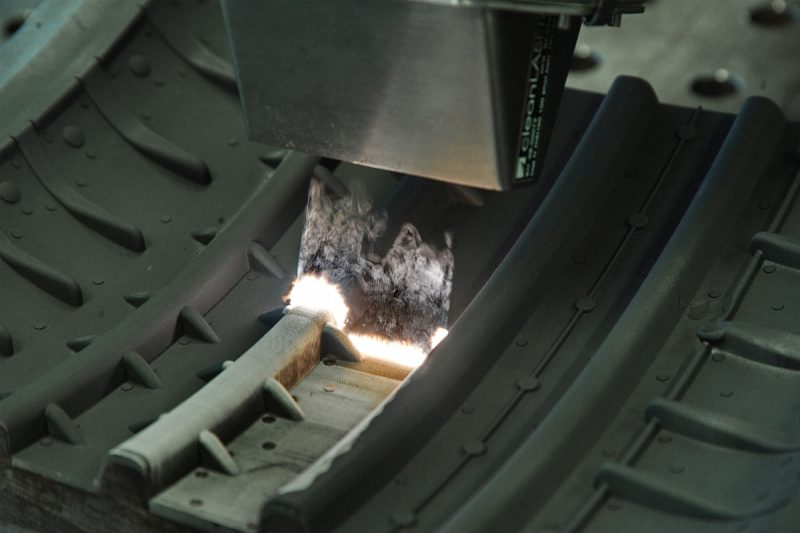
Machine Operating Techniques
Basic Operation
Initial Setup
- Machine Assembly: Learn how to properly assemble and set up the laser cleaning machine according to the manufacturer’s instructions. This includes connecting the power supply, assembling the optics, and setting up the control system.
- Calibration: Properly calibrate the machine to ensure accurate and consistent cleaning performance. Calibration includes adjusting the focus of the laser beam, setting the correct power level, and aligning the beam path.
Startup Procedure
- Power Up: Safely start the machine following the manufacturer’s instructions. This includes checking all connections, ensuring that safety interlocks are engaged, and verifying that the cooling system is operating properly.
- System Checks: Perform a series of system checks to ensure that the machine is operating properly. This includes checking the laser source, optics, control interfaces, and safety features.
Parameter Setup
- Laser Power: Set the laser power level appropriate for the material being cleaned. Lower power levels are suitable for delicate surfaces, while higher power levels are required for more stubborn contaminants.
- Pulse Duration and Frequency: Adjust the pulse duration and frequency based on the cleaning requirements. Shorter pulses and higher frequencies are suitable for precise cleaning, while longer pulses and lower frequencies are used for larger amounts of material removal.
- Focus Adjustment: Properly focus the laser beam on the target surface to maximize cleaning efficiency and minimize damage to the substrate.
Operation Controls
- Control Panel: Learn how to use the machine’s control panel or touchscreen interface. This includes navigating menus, setting parameters, and starting/stopping the cleaning process.
- Manual Operation: Learn how to manually operate the machine to perform specific cleaning tasks. This involves using a handheld laser head or manually directing the laser beam to clean intricate or hard-to-reach areas.
Monitoring and Adjustments
- Continuous Monitoring: Continuously monitor the cleaning process to ensure the laser is functioning properly and cleaning is proceeding as expected. Look for signs of overheating, laser misalignment, or poor cleaning performance.
- Real-Time Adjustments: Adjust laser parameters in real-time based on observed cleaning results. This may involve fine-tuning power levels, adjusting focus, or changing cleaning speeds.
Shutdown Procedures
- Safe Shutdown: Follow the manufacturer’s guidelines for safely shutting down the machine. This includes turning off the laser source, shutting down the cooling system, and securing the machine.
- Post-Operation Check: Perform a post-operation check to ensure the machine is in good condition for the next use. This includes inspecting the optics, checking for any signs of wear or damage, and performing routine maintenance tasks.
Advanced Operations
Advanced Calibration
- Precision Alignment: Use advanced alignment tools and techniques to ensure that the laser beam is precisely aligned with the target surface. This may involve the use of an alignment laser or specialized calibration software.
- Beam Quality Assessment: Regularly assess the quality of the laser beam using a beam profiler or other diagnostic tools to ensure it remains within specified parameters.
Advanced Parameter Optimization
- Material-Specific Settings: Gain insight into how different materials respond to laser cleaning. Adjust laser parameters (power, pulse duration, frequency) to optimize cleaning performance for specific materials such as metals, plastics, ceramics, and composites.
- Surface Characterization: Use advanced surface characterization techniques such as optical microscopy or surface profilometry to analyze cleaned surfaces and adjust parameters for better results.
Complex Cleaning Tasks
- Multi-layer Coatings: Learn how to handle complex cleaning tasks involving multiple layers of coatings or composites. This requires precise control of laser parameters to selectively remove specific layers without damaging the underlying materials.
- Complex Surfaces: Master techniques for cleaning complex or irregular surfaces, such as those found in aerospace components, medical devices, or historical artifacts. This may involve using specialized laser heads or adjusting the beam path for optimal coverage.
Automation and Programming
- Automated Cleaning Systems: Gain proficiency in using automated cleaning systems with integrated robotic arms or CNC controls. This involves programming the machine to follow precise cleaning paths and automatically adjust parameters based on real-time feedback.
- Software Integration: Learn how to integrate laser cleaning machines with other software systems, such as CAD/CAM software, to enable automated cleaning of complex geometries.
Troubleshooting and Maintenance
- Diagnostic Tools: Use advanced diagnostic tools and techniques to troubleshoot your laser cleaning machine. This includes identifying and resolving issues related to laser alignment, power stability, and optics integrity.
- Preventive Maintenance: Develop a preventive maintenance program to keep the machine in optimal condition. This includes regularly inspecting and cleaning optics, checking cooling systems, and updating control software.
Safety Enhancements
- Advanced Safety Protocols: Implement advanced safety protocols for handling high-power laser systems. This includes setting up additional safety barriers, using advanced interlock systems, and conducting regular safety audits.
- Emergency Response Training: Receive specialized training in emergency response procedures for laser-related incidents. This includes first aid for laser injuries, evacuation procedures, and coordination with emergency services.
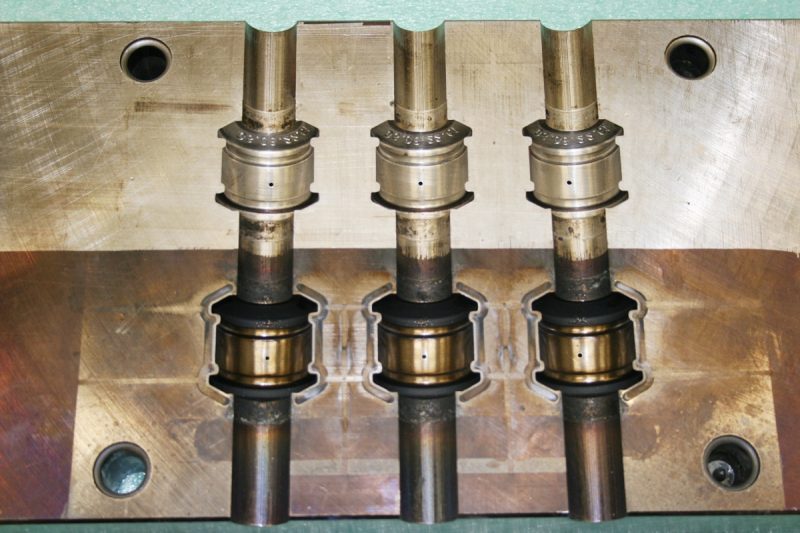
Maintenance Procedures
Regular Maintenance
Routine Maintenance
- Visual Inspection: Perform a visual inspection of the entire machine, looking for signs of wear, damage, or loose parts. Pay special attention to cables, connectors, and moving parts.
- Optics Inspection: Clean lenses, mirrors, and other optical components daily to remove dust and debris. Use appropriate cleaning solutions and materials to avoid scratching or damaging optics.
- Cooling System Inspection: Verify that the cooling system is operating properly. Check the coolant level and ensure there are no leaks or blockages in the system.
- Safety Features Test: Test all safety features, such as interlocks, emergency stop buttons, and protective covers to ensure they are functioning properly.
Weekly Maintenance
- Laser Source Inspection: Inspect the laser source for signs of wear or damage. Clean the laser head and check for proper alignment.
- Electrical Connections: Check all electrical connections for tightness and signs of corrosion or wear. Make sure all cables and connectors are secure.
- Ventilation System: Check and clean the ventilation system, including filters and exhaust fans, to ensure proper airflow and fume extraction.
- Software Updates: Check the manufacturer for any available software updates and install them to ensure the machine’s control system is up to date.
Monthly Maintenance
- Mechanical Components: Check mechanical components, such as motors, bearings, and linear guides, for wear and lubrication. Apply lubricant as needed to reduce friction and wear.
- Calibration: Perform a full calibration of the machine to ensure the laser beam is accurately aligned and focused. This includes checking the alignment of the mirrors and adjusting laser parameters.
- Power Supply Check: Check the power supply unit for signs of overheating or damage. Make sure it is providing the correct voltage and current to the laser source.
- Documentation: Keep detailed records of all maintenance activities, including dates, tasks performed, and any problems found. This helps track the condition of the machine and schedule future maintenance.
Troubleshooting
Laser Output Problems
- No Laser Output: If the laser source is not emitting any beam, check the power supply and make sure the machine is properly connected and powered on. Verify that all safety interlocks are engaged and the control system is properly configured.
- Inconsistent Beam Quality: If the intensity or quality of the laser beam fluctuates, check the optics for contamination or misalignment. Clean and realign the optics as needed. Inspect the laser source for signs of wear or damage.
Cooling System Problems
- Overheating: If the machine overheats, check the coolant level and make sure the cooling system is functioning properly. Check for any leaks or blockages in the coolant lines. Make sure the ventilation system is providing adequate airflow.
- Coolant Contamination: If the coolant appears dirty or contaminated, drain it and replace it with fresh coolant. Clean the coolant reservoir and lines to prevent future contamination.
Electrical Problems
- Power Fluctuations: If the machine experiences power fluctuations, check that the electrical connections are secure and for signs of corrosion. Make sure the power supply is stable and provides the correct voltage and current.
- Control System Error: If the control system displays an error message or malfunctions, consult the machine’s user manual for troubleshooting guides. Perform a software reset or update if necessary. Check for any loose or damaged cables.
Mechanical Problems
- Unusual Noise: If the machine makes unusual noises, check the mechanical parts for signs of wear or damage. Lubricate bearings and moving parts to reduce friction. Replace any worn or damaged parts.
- Motion Problems: If the machine’s scan head or other moving parts are not running smoothly, check the linear guides and motors for obstructions or wear. Clean and lubricate as needed, and replace any faulty parts.
Safety System Malfunctions
- Interlock Problems: If the safety interlocks are not working properly, check the sensors and switches for proper operation. Make sure all safety doors and covers are securely closed and engaged.
- Emergency Stop Malfunction: If the emergency stop button does not work, check the wiring and connections for faults. Replace the emergency stop button if necessary.
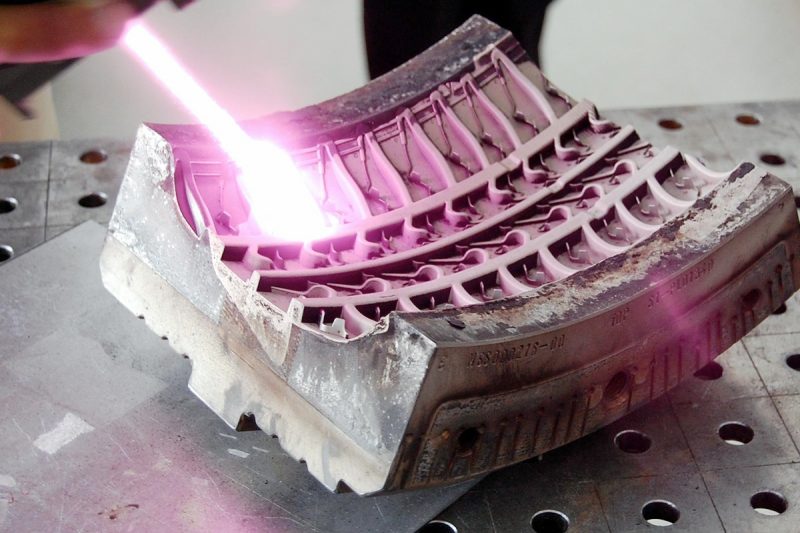
Summary
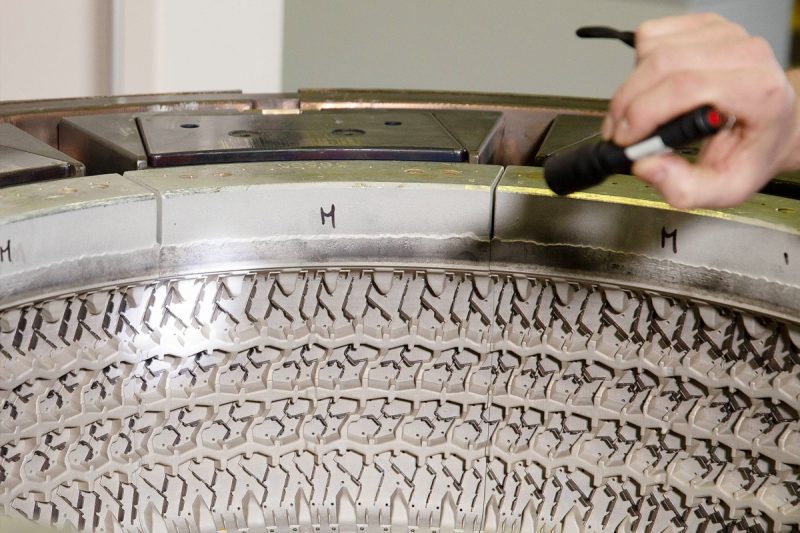
Get Laser Cleaning Solutions
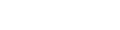
- [email protected]
- [email protected]
- +86-19963414011
- No. 3 Zone A, Lunzhen Industrial Zone,Yucheng City , Shandong Province.