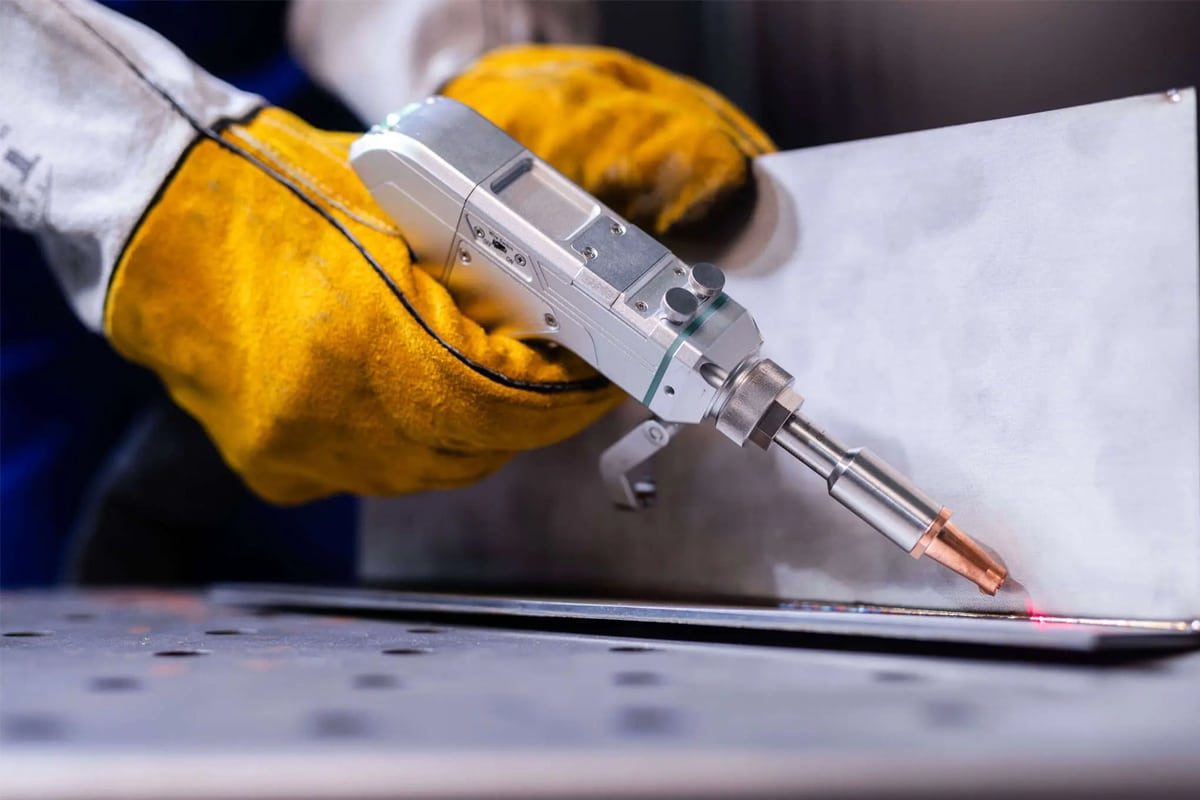
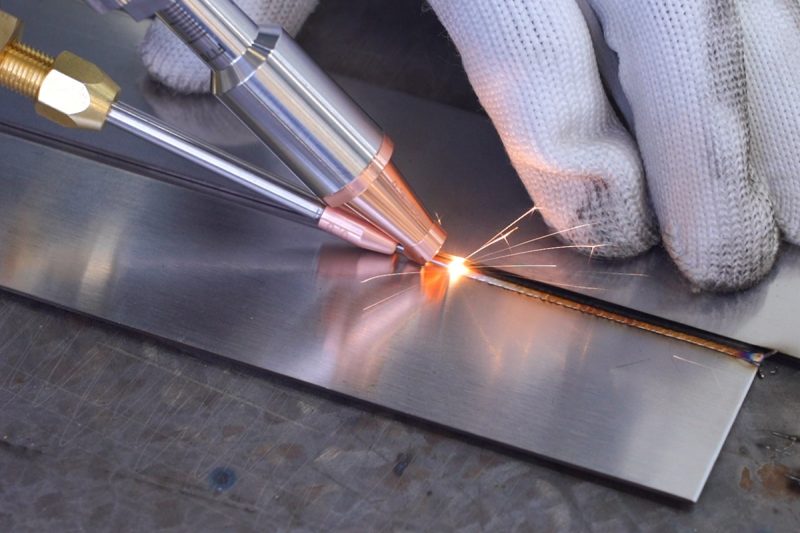
Overview of Laser Welding
What is Laser Welding?
Laser welding is a precise and efficient joining process that uses a highly focused laser beam to heat and fuse materials. The laser beam generates a concentrated heat source, allowing for narrow, deep welds with minimal heat-affected zones (HAZ). Laser welding operates in two main modes, depending on the power density and material properties:
- Keyhole Mode Welding: In this mode, a high-power-density laser beam vaporizes the material, creating a narrow, deep keyhole filled with molten metal and vapor. The keyhole acts as a conduit for the laser energy, enabling deep penetration and high aspect ratio welds. This mode is ideal for applications requiring deep and narrow welds, such as in the automotive and aerospace industries.
- Conduction Mode Welding: This mode occurs at lower power densities compared to keyhole welding, where the laser heats the material without vaporizing it. Heat conduction from the surface creates a shallow, wider weld pool. Conduction mode welding is suitable for thin materials or when minimal penetration and heat input are desired.
Advantages of Laser Welding
Laser welding offers several benefits that make it advantageous over traditional welding methods:
- Precision and Accuracy: The concentrated laser beam allows for precise control, producing accurate welds with minimal distortion.
- High-Speed Processing: The high energy density of the laser enables fast welding speeds, increasing productivity and reducing cycle times.
- Minimal Heat-Affected Zone: Reduced thermal spread minimizes distortion, making laser welding suitable for delicate or thin components.
- Automation Capability: Laser welding is easily integrated into automated systems and robotic arms, enhancing efficiency for high-volume production.
- Material Versatility: Capable of welding a wide range of metals and alloys, including difficult-to-weld materials, such as titanium and stainless steel.
- Non-Contact Process: No physical contact is required, reducing wear and tear on tools and eliminating the risk of electrode contamination.
Applications of Laser Welding
Laser welding is used in numerous industries due to its unique capabilities and precision:
- Automotive Industry: Used for welding car body panels, gears, transmission components, and exhaust systems, where high precision and speed are critical.
- Aerospace Industry: Suitable for welding lightweight, high-strength components such as turbine blades, structural parts, and engine components.
- Electronics Industry: Ideal for micro-welding delicate circuits, connectors, and enclosures in electronic devices.
- Medical Device Manufacturing: Used for welding intricate medical devices, surgical instruments, and implantable components where precision and cleanliness are paramount.
- Jewelry and Art: Enables intricate repairs and fabrication of complex jewelry designs and artistic metalwork.
- Industrial Manufacturing: Applied in the joining of metal sheets, piping, and heavy-duty structural components across various industrial sectors.
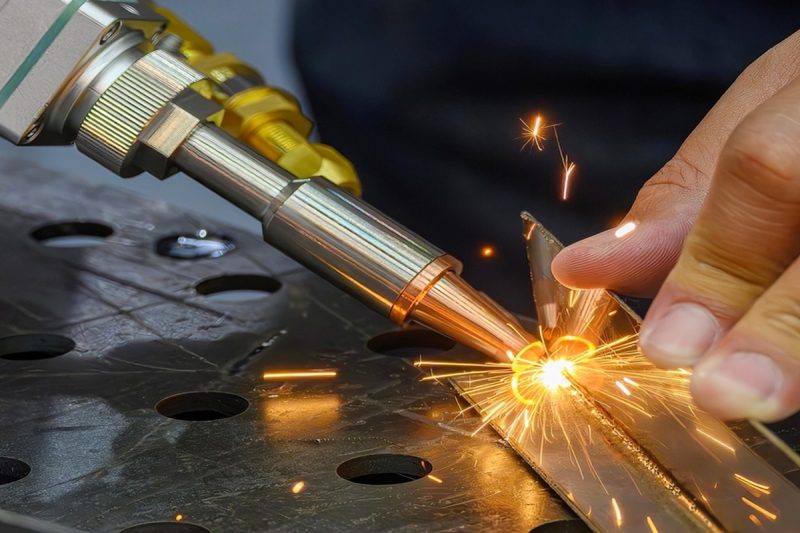
Common Welding Defects in Laser Welding
Porosity
Causes
- Surface Contamination: Oil, grease, moisture, and rust on the workpiece surface can generate gas when heated, leading to trapped bubbles within the weld.
- Shielding Gas Issues: Inadequate shielding gas coverage, low flow rates, or inappropriate gas type can result in atmospheric contamination, such as oxygen and nitrogen intrusion, which forms gas pockets.
- Material Composition: High concentrations of hydrogen, sulfur, carbon, or other impurities in the base metal can lead to gas evolution during welding.
- Rapid Cooling: Quick solidification of the molten pool can trap gas before it escapes.
Solutions
- Surface Cleaning: Thoroughly clean workpieces before welding, removing contaminants such as grease, oil, and rust.
- Optimized Shielding Gas Flow: Use appropriate shielding gases like argon or helium, ensuring the correct flow rate and coverage to protect the weld pool.
- Material Selection and Preparation: Choose materials with low impurity content and perform pre-weld treatments such as degassing.
- Parameter Tuning: Adjust laser parameters to allow controlled cooling, giving gases time to escape.
Cracking
Types of Cracking
- Hot Cracking: Occurs at high temperatures during solidification due to tensile stresses or impurity segregation (e.g., sulfur).
- Cold Cracking: Forms after cooling, often associated with hydrogen embrittlement, residual stresses, or improper material composition.
Causes
- High Thermal Gradients: Rapid heating and cooling cycles can introduce residual stresses that promote cracking.
- Material Composition: Certain alloys, particularly those high in sulfur or carbon, are more susceptible to cracking.
- Impurities: Elements like sulfur and phosphorus can segregate at grain boundaries, weakening the structure.
- Hydrogen Absorption: Hydrogen introduced through moisture, contaminated shielding gas, or base metal can lead to delayed cracking.
Solutions
- Preheating and Post-Weld Heat Treatment: Preheat the workpiece to reduce thermal gradients and perform post-weld heat treatments to relieve residual stresses.
- Material Control: Select materials with low impurity levels and optimize their chemical composition to reduce crack susceptibility.
- Hydrogen Control: Dry materials and use low-hydrogen processes, such as using dry shielding gases and avoiding moisture.
- Stress Relief Techniques: Use fixtures and proper joint designs to minimize stress concentration.
Undercut
Causes
- Excessive Heat Input: High laser power or slow travel speeds can cause localized melting and loss of material without sufficient filler metal.
- Incorrect Beam Angle: Misalignment of the laser beam relative to the joint can lead to material removal rather than fusion.
- Improper Focus: Inaccurate laser focus can concentrate energy unevenly.
Solutions
- Optimize Heat Input: Adjust laser power, travel speed, and beam diameter to control heat distribution.
- Beam Alignment: Properly align the laser beam with the joint to ensure even melting and filling.
- Welding Technique: Adjust the angle and positioning of the laser to reduce material loss.
Lack of Fusion
Causes
- Insufficient Heat Input: Low laser power or excessive travel speed can prevent full fusion of the base materials.
- Improper Joint Preparation: Poor fit-up, gaps, or misalignment between workpieces can inhibit full fusion.
- Contamination: Surface oxides, dirt, or other contaminants can act as barriers to fusion.
Solutions
- Increase Heat Input: Use sufficient laser power or reduce travel speed to achieve proper fusion.
- Improve Joint Fit-Up: Ensure proper alignment and fit between workpieces for consistent weld penetration.
- Surface Cleaning: Remove oxides, oils, and other contaminants from the welding surfaces.
Incomplete Penetration
Causes
- Low Laser Power: Insufficient energy input to fully melt through the material thickness.
- High Travel Speed: The laser moves too quickly to fully heat and melt the joint.
- Improper Beam Focus: Focusing the laser incorrectly can lead to shallow penetration.
Solutions
- Increase Laser Power: Adjust power settings to ensure full penetration through the joint.
- Reduce Travel Speed: Allow more time for the laser to heat and melt the material.
- Correct Beam Focus: Properly focus the laser to achieve consistent penetration depth.
Spatter
Causes
- Excessive Laser Power: High power settings can cause violent boiling of the molten pool.
- Contaminants: Surface impurities can react with the heat, creating rapid vaporization.
- Improper Shielding Gas: Inadequate shielding can allow oxidation, causing spattering.
Solutions
- Adjust Laser Parameters: Reduce laser power and optimize pulse settings to prevent excessive energy input.
- Surface Cleaning: Ensure surfaces are free from contaminants before welding.
- Shielding Gas Optimization: Use appropriate shielding gas and maintain proper flow rates.
Weld Bead Irregularities
Causes
- Inconsistent Travel Speed: Fluctuations in speed lead to uneven heat input.
- Laser Power Variability: Changes in power output can result in inconsistent melting.
- Incorrect Beam Focus: Misaligned focus leads to uneven energy distribution.
Solutions
- Maintain Consistent Travel Speed: Ensure uniform speed throughout the welding process.
- Stabilize Power Output: Use a stable power source to maintain consistent laser output.
- Adjust Beam Focus: Ensure correct beam alignment and focus for even energy delivery.
Burn-Through
Causes
- Excessive Heat Input: High laser power or slow travel speeds can lead to excessive melting.
- Thin Material: Thin sheets are more prone to burn-through.
- Incorrect Beam Focus: Concentrating energy in a small area can exacerbate melting.
Solutions
- Reduce Heat Input: Decrease laser power or increase travel speed.
- Broaden Beam Focus: Distribute laser energy more evenly.
- Use Appropriate Material Thickness: Match material thickness to welding requirements.
Deformation and Distortion
Causes
- Thermal Stresses: Rapid heating and cooling cycles cause expansion and contraction.
- Thin Materials: More susceptible to warping and bending.
- Excessive Heat Input: High energy input can lead to severe distortion.
Solutions
- Optimize Heat Input: Use controlled laser parameters to minimize excessive heat.
- Fixturing and Clamping: Hold workpieces in place with fixtures to reduce movement.
- Balanced Welding: Use techniques that balance heating and minimize stress.
Oxidation and Discoloration
Causes
- Inadequate Shielding Gas: Low gas flow or poor coverage can expose the weld pool to air.
- Improper Gas Composition: Incorrect choice of shielding gas may fail to prevent oxidation.
- Contaminants: Surface impurities can react and cause oxidation.
Solutions
- Ensure Proper Shielding: Use an adequate flow of shielding gas to protect the weld pool.
- Select Appropriate Gas Composition: Choose a shielding gas that effectively prevents oxidation (e.g., argon).
- Surface Cleaning: Clean workpiece surfaces thoroughly to minimize reactions during welding.
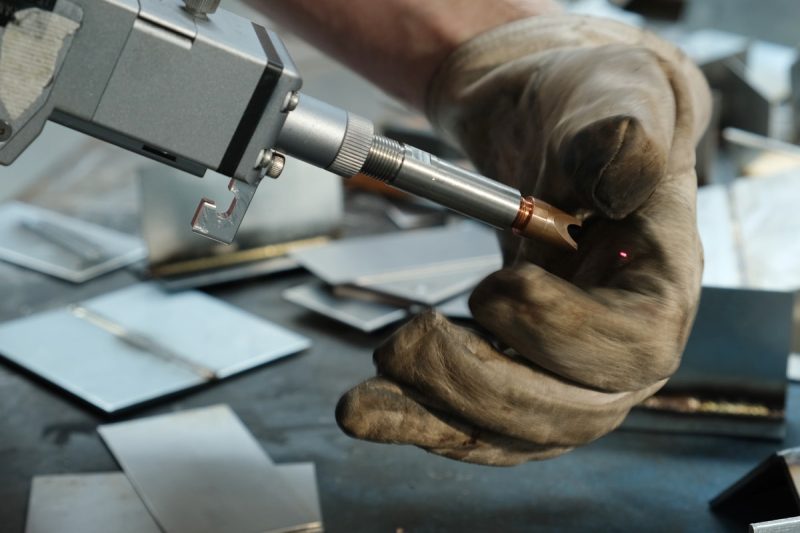
Factors Influencing Welding Defects
Material Properties
The properties of the materials being welded play a significant role in determining the quality of the weld and the likelihood of defects.
- Thermal Conductivity: Materials with high thermal conductivity, such as aluminum, tend to dissipate heat quickly, requiring higher laser power or slower travel speeds to achieve sufficient penetration and fusion. Insufficient control can lead to defects like lack of fusion or incomplete penetration.
- Melting Point: Materials with varying melting points require different laser parameters. For example, titanium has a high melting point and requires greater energy input, while low-melting-point materials like zinc may suffer from burn-through if not carefully managed.
- Reflectivity: Highly reflective materials, such as copper and certain aluminum alloys, can reflect a portion of the laser energy, reducing effective heat input. This may result in incomplete fusion, inconsistent penetration, or spatter, as reflected energy can affect surrounding areas.
- Material Composition and Impurities: Elements like sulfur, phosphorus, and hydrogen in the material can increase the likelihood of defects such as porosity and cracking. For instance, high hydrogen content can cause porosity, while sulfur and phosphorus increase the risk of hot cracking. Selecting materials with low impurity levels or conducting pre-weld treatments can help mitigate these issues.
Welding Parameters
Proper selection and control of laser welding parameters are crucial in preventing defects. Key parameters include:
- Laser Power: Adequate laser power is essential for achieving full penetration and fusion. Insufficient power can lead to a lack of fusion or incomplete penetration, while excessive power may cause burn-through, spatter, and deformation.
- Travel Speed: Travel speed affects the heat input per unit length of the weld. Too high a speed may prevent the material from heating adequately, resulting in defects like lack of fusion and incomplete penetration. Conversely, too slow a speed may cause excessive heat input, leading to burn-through and distortion.
- Beam Focus: Correct beam focus is essential for energy concentration. Misalignment or incorrect focal position can lead to insufficient penetration, irregular bead profiles, and weld porosity. For deep penetration, a focused beam with a small spot size is necessary, whereas a defocused beam may be suitable for wider, shallow welds.
- Pulse Duration (in pulsed laser welding): Pulse duration affects the amount of energy delivered in each pulse. Short pulses reduce heat input and minimize the risk of deformation, making them ideal for delicate or heat-sensitive materials. Longer pulses allow for greater penetration but may increase the risk of defects like spatter and porosity.
Joint Design
The design and preparation of the joint can significantly influence weld quality and the likelihood of defects.
- Fit-Up Tolerance: Proper joint fit-up is essential for achieving consistent weld quality. Gaps or misalignment between workpieces can result in a lack of fusion, porosity, or inconsistent penetration. Tight fit-ups allow for better control of the molten pool and minimize the risk of defects.
- Joint Type: Different joint types (e.g., butt, lap, fillet) require different laser welding techniques and parameters. For example, butt joints with poor alignment may lead to undercuts or lack of fusion, while lap joints with excessive overlap can cause spatter and insufficient fusion.
- Accessibility: In complex structures, limited access to the joint can restrict the laser beam’s reach, leading to incomplete fusion or irregular bead formation. Proper fixturing and laser alignment are necessary for joints with limited accessibility.
- Preparation and Cleaning: Proper preparation and cleaning of the joint area are critical, as surface contaminants can lead to porosity, cracking, and spatter. Cleaning removes oxides, oils, and other impurities that can interfere with fusion and introduce defects.
Environmental Factors
Environmental conditions in the welding area can directly affect weld quality and the occurrence of defects.
- Ambient Temperature: Welding in extreme temperatures, either too cold or too hot, can affect the cooling rate of the weld and lead to thermal stress and cracking. Cold environments, for example, can cause rapid cooling, leading to brittle welds and cracks.
- Humidity and Moisture: Moisture in the environment can introduce hydrogen into the weld pool, increasing the risk of porosity and hydrogen-induced cracking. Welding in a dry, controlled environment or taking precautions to prevent moisture exposure is essential for high-quality welds.
- Shielding Gas Quality and Flow: Shielding gas protects the molten weld pool from atmospheric contamination. Inadequate shielding gas flow or the use of low-purity gas can lead to oxidation, porosity, and discoloration. Additionally, shielding gases such as argon and helium should be used based on material requirements to prevent contamination.
- Vibration and Movement: Environmental vibrations or movement in the welding setup can lead to inconsistent weld beads and other defects. Stable fixturing and minimizing external movement are essential to ensure consistent results.
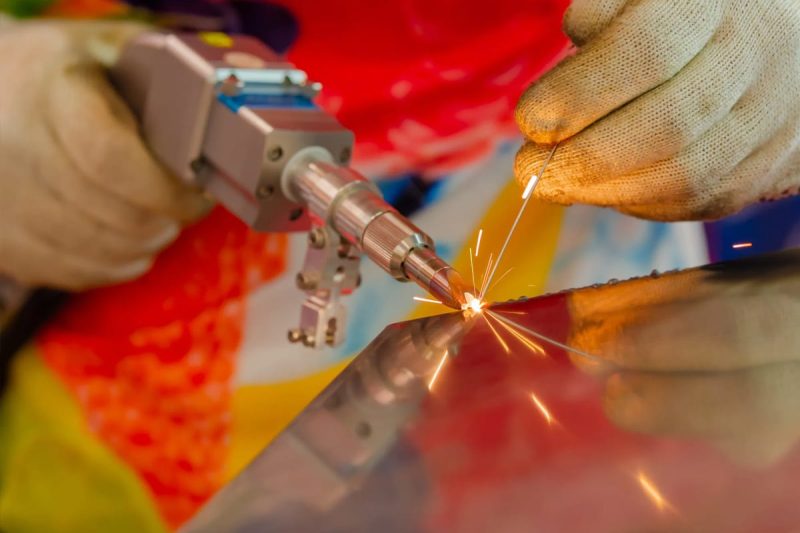
Additional Considerations and Best Practices
Proper Material Selection
Choosing the right materials for laser welding is essential for achieving high-quality welds and minimizing defects.
- Material Compatibility: Ensure that the base materials are compatible with laser welding. Different materials respond differently to laser energy due to variations in melting points, thermal conductivity, and reflectivity. For example, reflective materials like aluminum may require special measures to reduce reflection and optimize heat absorption.
- Material Purity: Use materials with low levels of impurities, such as sulfur and phosphorus, which can contribute to porosity, cracking, and other defects.
- Material Thickness: Consider the thickness of the materials to be welded, as it influences the required laser power and heat input.
Laser Type and Settings
Selecting the appropriate laser type and fine-tuning its settings are critical factors for successful laser welding.
- Laser Type: Choose between continuous-wave (CW) and pulsed lasers based on the application. CW lasers are ideal for high-speed welding, while pulsed lasers are suitable for delicate or heat-sensitive components.
- Power and Speed Settings: Optimize laser power, travel speed, and pulse duration to achieve desired penetration, minimize defects like spatter or porosity, and control heat input.
- Beam Focus and Positioning: Proper beam alignment and focus are essential for even energy distribution and consistent welds.
Joint Design and Fit-Up
Proper joint design and fit-up ensure consistent weld quality and reduce the likelihood of defects such as lack of fusion, porosity, and misalignment.
- Fit-Up Tolerances: Ensure that joints have tight and consistent fit-ups, minimizing gaps that could lead to uneven fusion or porosity.
- Joint Accessibility: Design joints to allow for easy access by the laser beam, minimizing the risk of incomplete fusion or irregular beads.
- Joint Preparation: Properly clean and prepare the joint surfaces to remove contaminants, such as oils, oxides, and other impurities.
Shielding Gas Selection
Shielding gas protects the molten weld pool from atmospheric contamination, preventing oxidation, porosity, and other defects.
- Gas Type: Select appropriate shielding gases, such as argon, helium, or mixtures, based on the base material and desired weld characteristics. For example, argon is often used for stainless steel, while helium can improve penetration for thicker materials.
- Flow Rate: Ensure that the shielding gas flow rate is sufficient to cover the weld pool without turbulence or inadequate coverage.
- Purity: Use high-purity shielding gas to avoid contamination.
Pre-Weld and Post-Weld Treatments
Pre-weld and post-weld treatments can significantly reduce the likelihood of defects and improve overall weld quality.
- Pre-Weld Cleaning: Thoroughly clean workpieces to remove contaminants, such as oils, rust, and moisture, which can lead to porosity, cracking, and other defects.
- Preheating: Preheating materials, particularly those prone to cracking, can reduce thermal gradients and minimize residual stresses.
- Post-Weld Heat Treatment: Perform post-weld heat treatments, such as annealing or stress relief, to reduce residual stresses and improve the mechanical properties of the weld.
Operator Training
Skilled operators play a critical role in ensuring consistent, high-quality laser welds.
- Technique Training: Train operators on the proper handling of laser welding equipment, including positioning, speed control, and parameter adjustments.
- Defect Identification: Educate operators to recognize common defects, their causes, and how to make necessary adjustments to prevent recurrence.
- Safety Protocols: Ensure operators are trained on laser safety procedures to protect themselves and the work environment.
Equipment Maintenance
Regular maintenance of laser welding equipment is essential to ensure consistent performance and prevent defects.
- Optics Cleaning: Clean lenses, mirrors, and other optical components regularly to maintain beam quality and accuracy.
- Calibration: Calibrate laser systems periodically to ensure accurate power output, beam alignment, and focus.
- Component Inspection: Inspect and replace worn or damaged components, such as nozzles and lenses, to maintain weld consistency.
Process Monitoring
Process monitoring and control are vital for achieving consistent, defect-free welds.
- Real-Time Monitoring: Use sensors and monitoring systems to detect and correct deviations in weld parameters, such as power fluctuations, travel speed, and beam focus, in real time.
- Data Logging: Record welding parameters and results to analyze trends, identify root causes of defects, and implement continuous improvement measures.
- Quality Inspections: Conduct regular inspections, including non-destructive testing (NDT) methods, to verify weld quality.
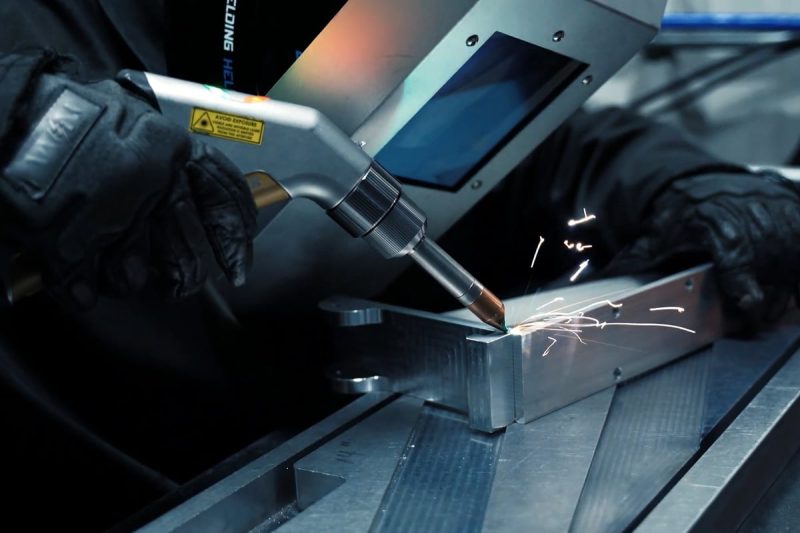
Summary
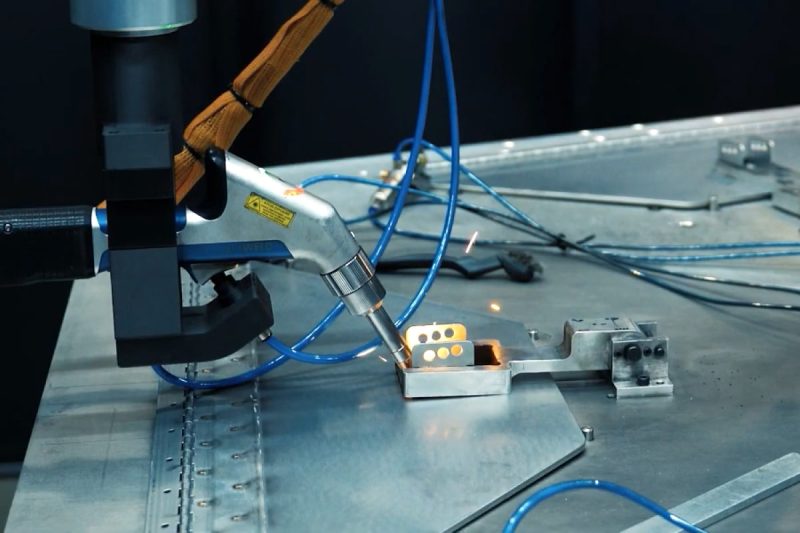
Get Laser Welding Solutions
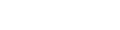
- [email protected]
- [email protected]
- +86-19963414011
- No. 3 Zone A, Lunzhen Industrial Zone,Yucheng City , Shandong Province.